From Motown to Silicon Valley: Digital technologies and the future of the CV industry
By Bradley Osborne - 7th February 2023
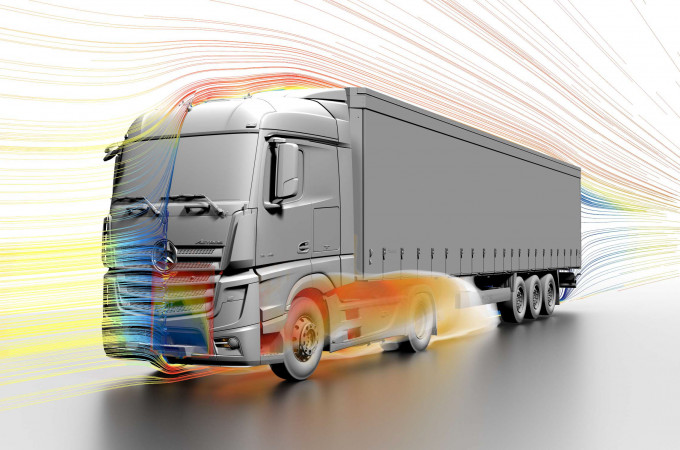
Aerodynamic vehicle simulation using Siemens' Simcenter STAR CCM+
The first in an open-ended series of features on the tech industry's involvement in the commercial vehicle space, this article takes a glance at how the technology, business model, and culture of 'Silicon Valley-type' start-ups have already changed the way the CV industry works.
In a posting dated 21 June 2022, Renault Group opened with the following statement: