Pioneers in the Wild West of EVs: an interview with John Kimes of Sigma Powertrain
By Bradley Osborne - 22nd August 2023
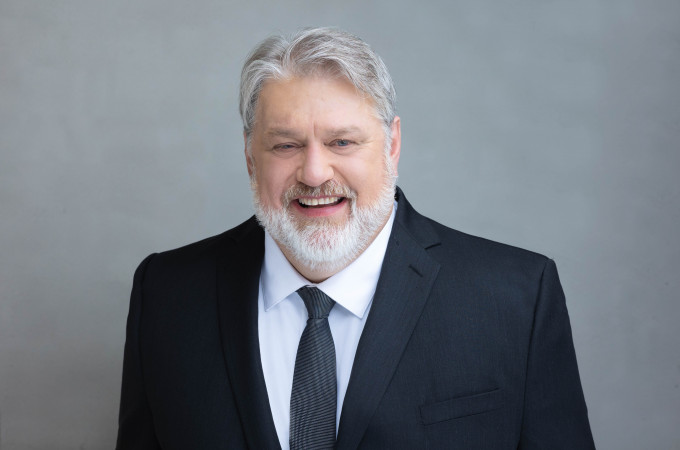
John Kimes, founder, CEO and President of Sigma Powertrain
USA – Investors are enamoured with the startup company. Some of the shine is starting to wear off, however, in the automotive industry, where the practice of new firms merging with SPACs (special-purpose acquisition companies) in order to raise money on the stock exchange has led to mixed results. The view of John Kimes is that SPACs have “soured” the market. The underperformance of some SPACs post-merger, often down significantly from their initial public offerings, is making investors more and more cautious about putting their money behind other startups, he argues.
For Kimes, it’s personal. As founder, and now CEO and President, of a startup company himself, Kimes is naturally concerned about investors balking from handovers of significant funds because of the irresponsible actions of others. On the other hand, his company has already raised USD10m following seed round funding in 2019, and Kimes told me multiple times that he is unsure how long he can continue to call his firm a startup.