FR8 Technologies, the new kid on the block, looking to revolutionise goods distribution transport with a new axle design for electric trucks
By Luke Willetts - 23rd May 2023
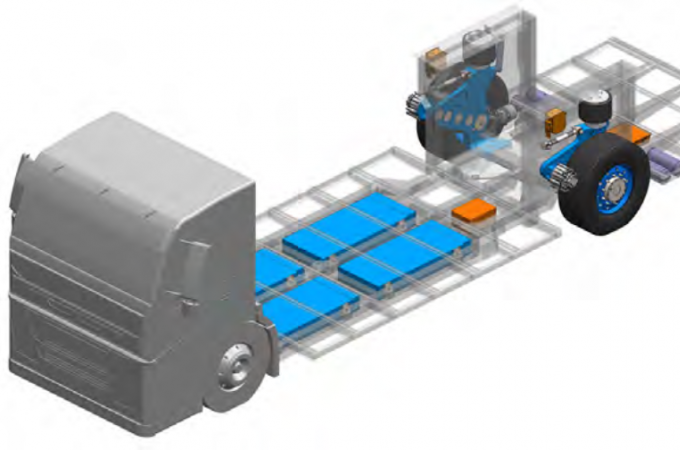
FR8 e-DRIVE Vehicle Package Layout
UK – Founded in 2022, with offices in Birmingham, UK, the new kid on the block is new electric axle design company, start-up FR8 Technology Ltd. Led by seasoned experienced transportation industry personnel - Richard Welford, CEO, Anu Kabra, CTO and Tom Hughes, CSM - the new company aims to supply the goods transportation and distribution industry with a revolutionary electric axle design (the patented FR8-eDRIVE) that will not only increase the payload and load volume in distribution trucks, but also increase operational performance by up to 30%.
The three founders come from strong engineering backgrounds having all earnt master’s degrees in the subject. Furthermore, all three come with experience of working in the commercial vehicle sector, Tom Hughes has worked at Meritor and BAE Systems, Anu Kabra at Volta Trucks and Richard Welford at Tata Motors. FR8 is solely owned and operated by these three directors.
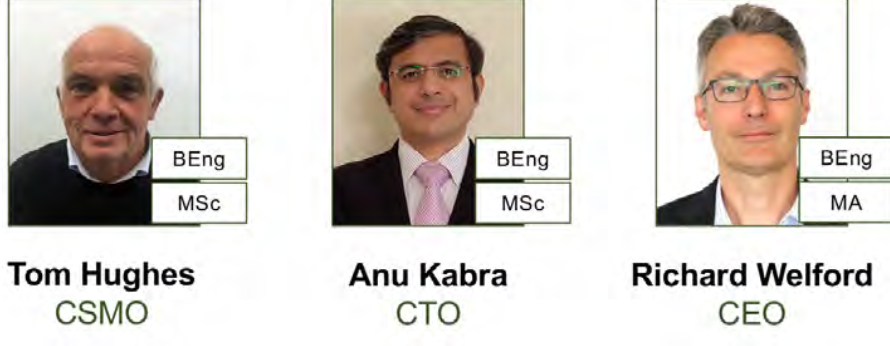
Leadership Team
Background: The market conditions for electric commercial vehicles
To shift transport operations to zero-emission vehicles (ZEVs), the European Commission has pledged the phasing out of all fossil-fuelled trucks by 2040 and is proposing new CO2 emissions targets for new heavy-duty vehicles (HDVs) in the form of Euro VII. This means that new commercial vehicles manufactured by OEMs must meet certain emissions criteria if they are to be sold and operated in Europe in the coming years. Slated to come into law from 2025 onwards (although legislation may be delayed until 2027/28), many operators and OEMs alike, are recognising that the days of trucks and buses powered by the traditional diesel internal combustion engine (ICE) are numbered, and that this is resulting in considerable resources being allocated to the development of electric vehicle technology in Europe. Despite the proposed new EC legislation and EU incentives to develop electric trucks, there is no doubt currently that without considerable buying-support in the form of subsidies there remains no business case for adopting electric trucks. The issue, therefore facing operators, relates to two facts, the hefty expense of transitioning their vehicles to electric and enduring a compromised operating performance when compared with the traditional ICE trucks that have served the industry so well for so many years.
The rise of the e-axle?
As a highly efficient power source for propelling electric vehicles, truck e-axles are designed to go beyond providing just torque and power, they are also used to balance performance, durability and reliability to allow maximum time on the road per charge. Current electric drive suppliers, like Allison, Meritor (now Cummins), ZF and Dana (to name but a few) continue to slowly advance e-axles in all kinds of categories making them simpler and more power-dense reducing packaging size and weight, lowering noise emissions and increasing system efficiency.
Improvement in design
Lately, improved design flexibility for battery placement and truck body positioning has also been a big development focus for these companies and this has spurred the market to design higher-performing and more efficient electric vehicles. The combination of improved packaging and lower weight also supports OEMs which need to employ large battery packs without compromising on cargo space or load capacity. Newer e-axles can utilise fully integrated electric motors improving performance efficiency and cooling, all while reducing the impact on packaging flexibility.
Maintenance considerations of the e-Axle
Looking beyond e-axle capability it's important to be aware of maintenance needs too, primarily high voltage safety, which includes architecture, charging pre-operation inspections and EV maintenance schedules. The majority of heavy-duty EVs operate at 650 volts with peaks up to 800 volts so certain precautions need to be taken to safely service the vehicle. However, much of the e-axle is going to be familiar to technicians because brakes, suspensions and wheel ends are all still common with conventional axles. Technicians will need to understand high voltage systems and safety protocols, which will require time-consuming training sessions to be undertaken by staff. A positive for the industry is that overall maintenance requirements are inherently lower for electric drive systems when compared with diesel powertrains since there is a considerable reduction in overall number of components and moving parts.
Inherent challenges faced by electrification of the truck transportation industry
Whilst there are significant benefits of e-axle technology, many of the major OEMs are weighed down by processes that ultimately result in a slow transition to electric drive technologies. While there are a whole host of issues continuing to halter the shift to ZEVs in the commercial trucking industry, one perhaps of most significance is design and that the majority of the current electric commercial vehicles on offer today retain the same vehicle architecture as their fossil-fuelled counterparts. A major issue arising out of this includes the decreased range and payload of EV CVs! This, added to the shortage of charging infrastructure and long charging times, results in lower levels of operating efficiency and reduced uptime compared with diesel vehicles. These detriments are compounded by the need to train/retrain maintenance professionals on EV servicing processes.
Understandably, the cost-benefit analysis doesn’t add up, and ultimately the transition has been hindered by a combination of both the technology and the economics, in an industry where many companies are already running on single-digit margins. Fleet operators are waiting until either the technology/price efficiency catches up with one another or their hands are forced by legislation, before going all in on the transition to ZEVs.
FR8 Technology’s proposed solution to the problem
In response to this, FR8 believes that OEMs may have missed an opportunity to optimise CV formats when transitioning to electric drive. This opportunity comes in altering the existing e-Axle design and chassis architecture resulting in the payload floor remaining too high above the wheels, equating to a floor height of over one metre and prolonging the need for powered tail lifts that are heavy, costly, dangerous and energy-consuming.
Setting out to resolve this problem, FR8 technology has invented a completely new design of e-Axle, enabling a low floor option specifically for the commercial vehicle sector. By dropping the height of the payload floor to just 300mm, Tom Hughes explained, this significantly speeds up delivery/offloading times. Asked how significant the low floor design is Hughes said up to 30%, a figure he can back with an earlier study by French truck builder, Renault Trucks! The low floor design also eliminates the need for a tail-lift, which offers aa potential saving of some 400kg, Hughes added.
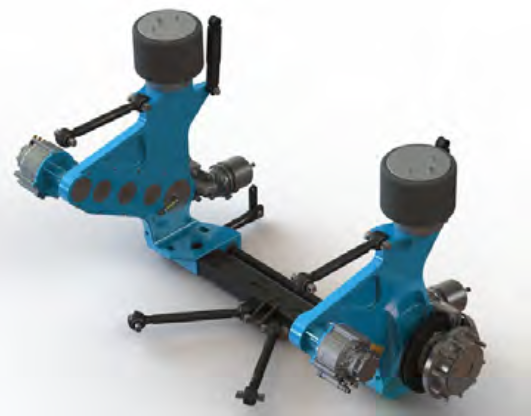
FR8 e-DRIVE
Subsequently, the advantage for operators is the additional payload weight and volume capacity created by the low floor and removal of the taillift, said Hughes. The increased payload and volume enable an operator to deliver goods using fewer trips, and, over greater distances, so bringing down costs and generating more revenue per vehicle. Another important potential gain, Hughes was keen to point out, is that fewer vehicles are needed to do the same amount of work. “To summarise, these vehicles can do more, by carrying more, in order to earn more.”
Speaking of the FR8 axle design, Hughes said that initially the concept was designed for vehicles of between 5.5t and 19t gross vehicle weight, but the FR8 e-DRIVE, he claims, is perfectly scalable up and down the gross weight range depending on the vehicle and the operator’s needs. Through the various stages of development, FR8 has been refining the engineering of the product and engaging the market for feedback.
Environmental benefit of the FR8 eDRIVE
Hughes explained that within the context of impending Euro VII regulation, the ability of the FR8 eDrive to help reduce emissions is enormous. In terms of emissions reductions estimates, Hughes said: “Our calculations suggest that avoiding just one 5-year refresh cycle (i.e. bringing forward transition from ICE to BEV from 2040 to 2035), for the smallest potential market we have identified of some 70,000 commercial vehicles in Europe, the new e-axle design could save around 75Mn tonnes of CO2 if the electricity is from sustainable sources, or around 33Mn tonnes of CO2, if it was still generated by fossil fuel. Importantly, a vehicle equipped with the patented FR8-eDRIVE would save an additional 8Mn tonnes of CO2 versus a traditional high-floor electric commercial vehicle.”
The company is currently in the process of refining the prototype through various stages of testing and validating performances, which will then lead to a period of further development where the technology is either then sold or licensed to a suitable Tier 1 supplier. Hughes explained that FR8 is currently meeting with, and courting, potential partners.
Different Stages of Development / Funding
Initially, the project started three years ago, with the help of a grant from Britain’s Advanced Propulsion Centre (APC), which helped the company take its idea and make it viable, through various research and development steps taking it from an idea to a design. This was done primarily in-house with a third party verifying the gear design. At the end of ‘Phase 1’, the company had a viable test module.
FR8 then completed the second phase of assessing its viability in the market place and calculating that the potential size of the global e-axle market for the FR8 e-DRIVE is worth a conservative USD 1.4bn.
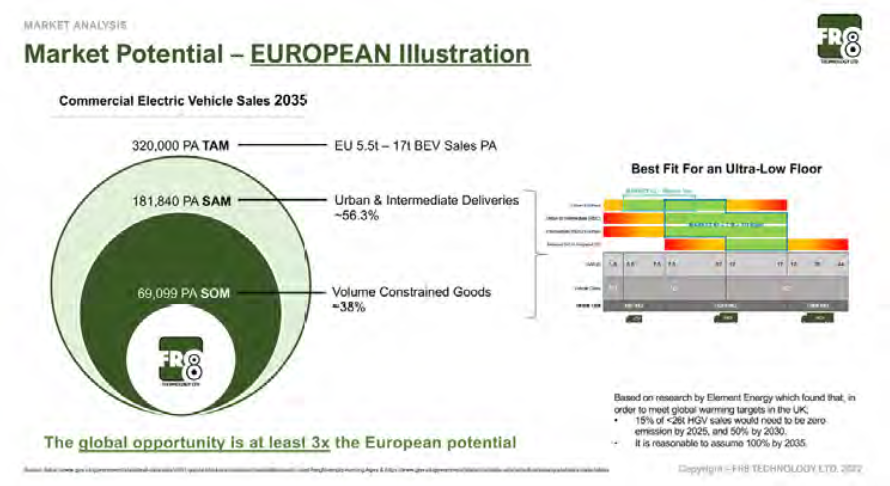
Estimated Size of the Global E-Axle Market
In a third development phase, FR8 has now tested all the gearing systems, making sure they work, and verifying the speed and torque of the gears as well as efficiency and noise. Innovate UK (IUK), another government funding body, has helped facilitate this phase with grant funding.
The next step, which the company is currently undertaking, is building a fully-fledged prototype.
It remains to be seen the UK’s role in the global transition to electric vehicles. FR8 may prove to be an interesting case study in answering this question. Be sure to stay tuned, as we bring you more developments from FR8 in the near future.