ZF Global Technology Day 2023: A T&BB report
By Bradley Osborne - 18th July 2023
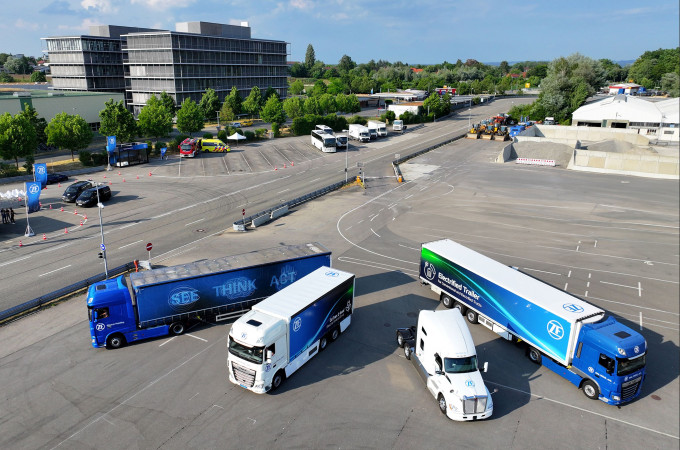
Demonstration vehicles on the track at Friedrichshafen
Germany – Friedrichshafen is well on its way to becoming the core plant for ZF Group’s portfolio of products for commercial electric vehicles. That was the main takeaway from a press trip to the German town to attend the annual ‘Global Technology Day’, featuring factory tours, vehicle demonstrations, and a keynote by CEO Dr Holger Klein.
The town’s manufacturing roots go deep. For over a hundred years, ZF has made transmissions at Friedrichshafen, initially for zeppelins before quickly shifting to applications in every type of road vehicle. We were taken round a production hall where gearwheels are still being made with cutting and grinding machines. However, we were informed that gear production is “shrinking” at the plant to make room for electric drive production.
In the centre of this plant, a space has been demarcated for a future “eMobility Campus”. Here, ZF will carry out assembly of its future electric drive systems, ‘CeTrax 2’ and AxTrax 2’. The plant’s head of gear production, who is now also head of e-drive production, told the press that clearing the required space will take up to 2025. 2,000-square-metres have already been freed up. The company has had to reduce its work-in-progress on the transmission side by 30% in order to allow for these changes.
That is not to say that transmission production will be eventually phased out. On the contrary, ZF’s electric drive systems for commercial vehicles will have integrated transmissions – albeit these will be smaller and limited to three speeds only. Far from being a hindrance, ZF’s legacy production and expertise is part of what Dr Peter Laier, the head of Commercial Vehicle Solutions at the company, calls its “systems competence”.
Naturally, we tend to think of products as discrete units or commodities, with individual names and functions. But ZF’s growing portfolio for commercial electric vehicles – covering air management, fuel cells, steering, driveline, braking, and electronics – are increasingly designed to work best together. The idea is that electric vehicle manufacturers will turn to ZF for everything they need to build a new EV platform, thus reducing the time it takes to bring a new vehicle to market. Moreover, ZF’s drive systems are energy-agnostic, suitable for both battery and fuel cell electric drivelines.
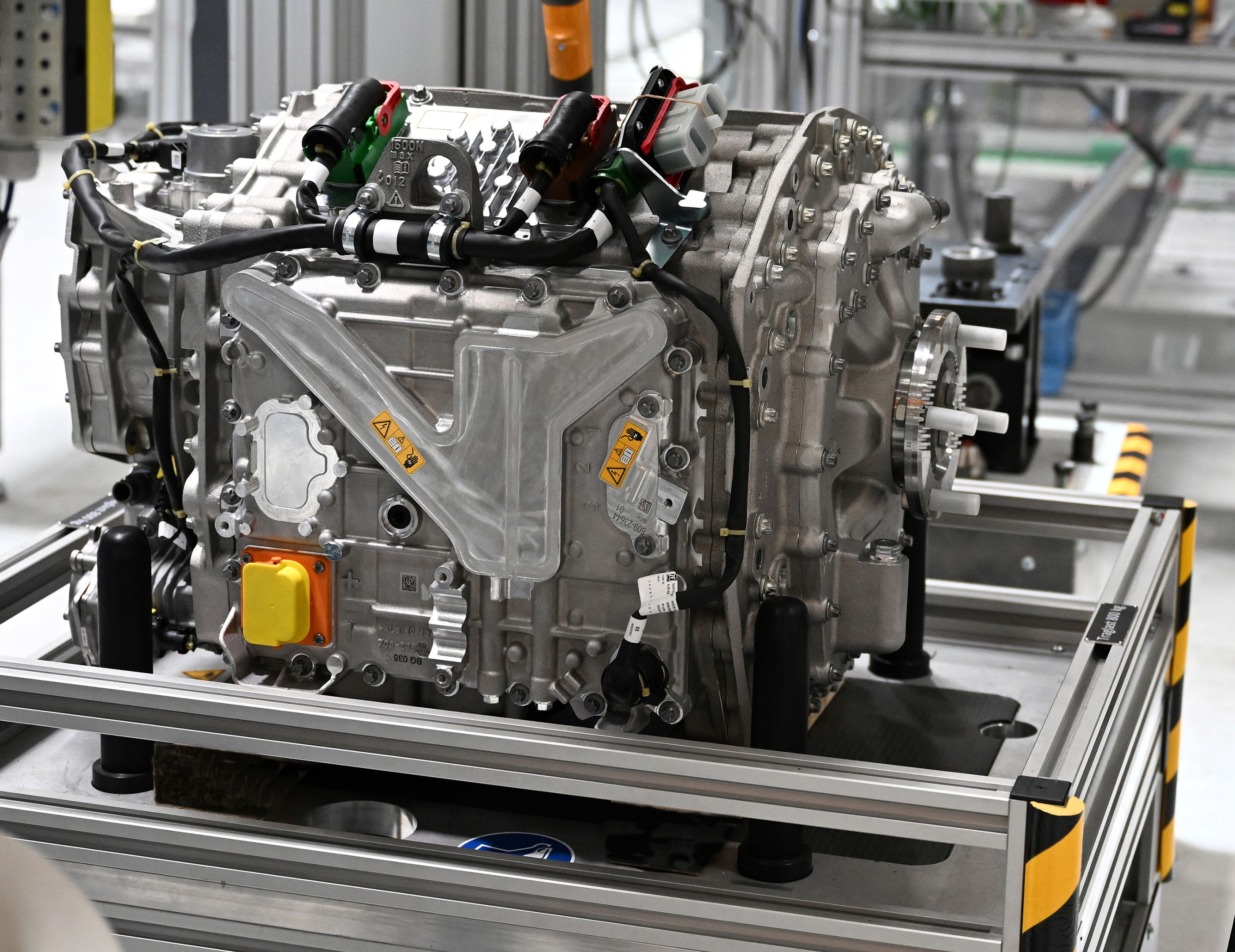
The CeTrax 2
Keynote by Dr Holger Klein
The group’s new CEO addressed audiences online and in-person at the Global Technology Day, announcing that ZF’s aim is to “make mobility more sustainable and safer”. He said that the group is embracing “the new normal of the automotive industry”, referring to shortening development cycles and quicker time-to-market for new products.
In Ensdorf, Saarland, ZF has agreed to invest in a new semiconductor fabrication facility which American firm Wolfspeed plans to build. Here, 200mm silicon carbide wafers, developed through joint research between the two companies, will be made for automotive applications. Dr Klein announced that “chips are the new gears”: an oblique reference, perhaps, to the shrinking volume of gear production at Friedrichshafen.
Dr Klein told press that two group divisions, one for car chassis technology and the other for active safety systems, would be merged into a single division for “chassis solutions” next year. ZF’s portfolio of products for steering, braking, and damping, together with their respective safety systems, will be rolled into one division, serving every vehicle segment. The R&D focus of this division will be x-by-wire technologies that replace mechanical connections with electrical ones – an area in which ZF is a world leader, according to Dr Klein.
Moving on to software, the CEO announced a planned joint venture with KPIT Technologies of Pune, Maharashtra, India. Called ‘Qorix’, the JV will be focused on producing middleware for automotives – software serving as an intermediary between the vehicle control unit and embedded applications used by the customer. There are middleware solutions such as QNX which are already available, but Dr Klein emphasised the need to “define a standard for middleware” for the whole automotive industry.
Software is becoming more and more central to what traditional manufacturers do. But Dr Klein suggested that the automotive industry should take notes on aspects of the tech industry’s culture. Tech firms are less hierarchical than automotive firms, and this makes them more “agile” and “innovative”, Dr Klein said. How this might translate to the (very different) context of the automotive industry remains to be seen.