Official opening of VDL Bus Roeselare: a T&BB feature
By Bradley Osborne - 7th May 2024
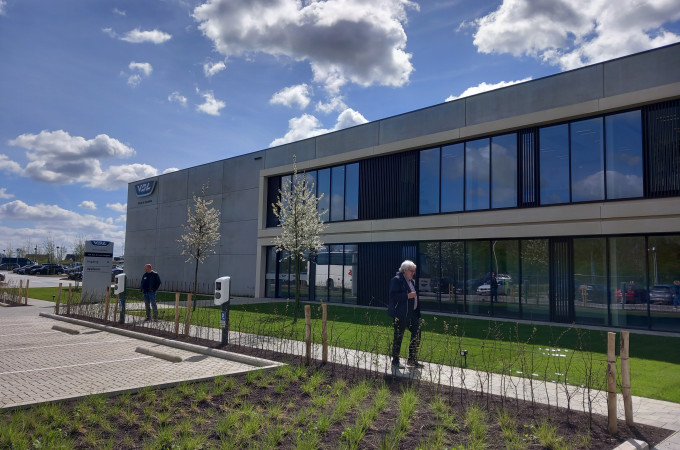
Exterior of the VDL facility in Roeselare
Belgium – On 10 April, members of the press descended on the Flemish city of Roeselare to visit a new bus factory operated by Dutch company VDL Bus & Coach. Ostensibly, they were there to report on the factory itself and the ribbon cutting ceremony which marked its official opening, but I suspect that the local media were hunting for information on an entirely different topic. Indeed, the CV trade journalists hardly spoke of anything else: the bankruptcy of commercial vehicle manufacturer Van Hool and the prospect of a rescue by VDL. Van Hool has since confirmed that the parent company of VDL Bus & Coach, VDL Groep, together with South African firm GRW Tankers & Trailers, will be taking over the business – though which parts of it will be saved remains to be seen. Willem van der Leegte, CEO of VDL Groep and a member of the third generation of the Van der Leegte family which owns the group, told the press that he was very concerned about the developments at Van Hool, and admitted that VDL has also gone through a difficult period.
The fate of Van Hool threatened to completely overshadow the factory opening. In fact, the bad news from outside was easily forgotten once we were inside the factory, with its immaculately clean and modern assembly line. It is dedicated to building the next-generation ‘Citea’ with battery electric drive and a new design done completely from scratch. Across two lines, the factory boasts an annual production capacity of 800 buses; this is supplemented by extra capacity at the factory in Valkenswaard, Netherlands, which also assembles the electric Citea alongside other models. Nevertheless, I was impressed by the concentration of effort and efficiency on display at Roeselare, where the principles of lean or “just-in-time” manufacturing are followed assiduously across the whole span of the 27,000-square-metre plant. Most of all, I was struck by how quiet it was. The factory floor felt light and spacious, not crammed and grey like so many other plants. Later, I was told that the noise had been kept to a minimum while the press tour was in progress, which altered my impression somewhat. Nevertheless, I cannot imagine that it ever gets very loud on the assembly lines. We were informed that no welding takes place at the plant; instead, the parts of the bus are bolted together, making for a much cleaner and quieter assembly process.
The new plant at Roeselare is meant to replace an older site in the same city, which VDL has said will eventually be decommissioned. The old factory was once home to ‘Jonckheere’, a veteran bus and coach builder which became a subsidiary of VDL in 1998. Jonckheere vehicles continued to be made until 2010, when the name was retired and its operations at Roeselare were absorbed by the VDL Bus & Coach business. It was sobering to think, while touring the factory which will replace the former Jonckheere site, that the name of Van Hool might also disappear before the end of the year. The Belgian manufacturer’s fate is still uncertain: in the interval, one feels the relief of some attendees that, whatever matter may happen in Koningshooikt, bus manufacturing will continue in Flanders.
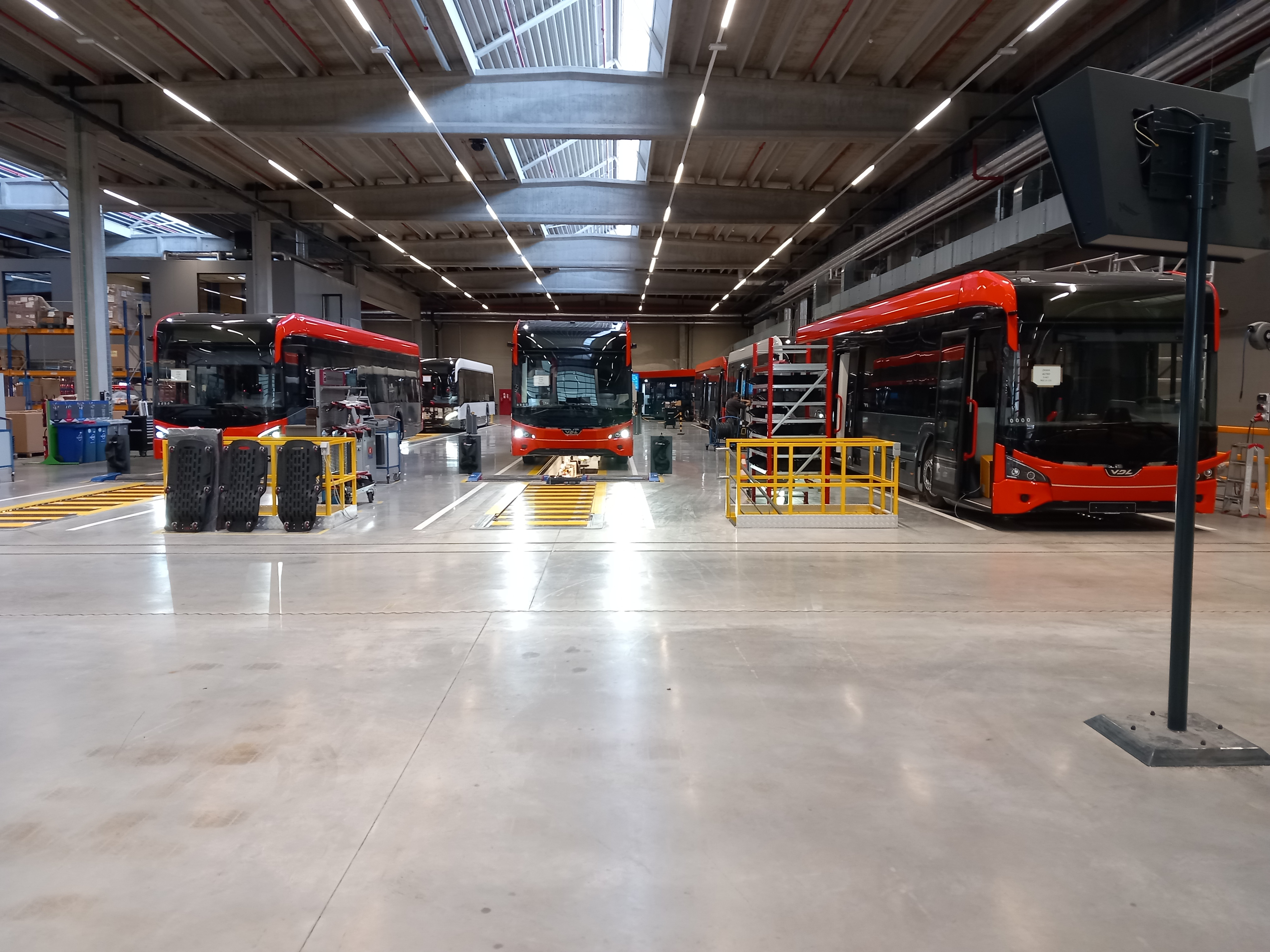
Finished vehicles at the end of the assembly line
Details of the factory
The new assembly plant in Roeselare can be split into two sections which differ in shape and size. Running along two sides of the rectangular building, forming an ‘L-shape’ across its length and width, is the assembly area, where the buses are built. In the remaining area of the building, pre-assembly of certain parts of the bus is carried out. There is also a smaller section of the floor which is a closed warehouse with a tool maintenance bay; however, the parts stored here are reportedly for customers and not for the assembly line. All parts destined for the bus assembly are delivered “just in time” and are queued up, waiting to be brought onto the line. We were given a brief glimpse of ‘StreamLine’, the system employed by the company to log procurements and track incoming orders to the factory.
The assembly line is divided into twelve sections, or twelve “steps” in the assembly process. Firstly, the chassis is brought in from outside of the factory (all VDL chassis are supplied by the parent group). The second step in the process is the first part of the assembly – the installation of the floor and wheel arches. Then, the back wall of the bus is attached to the chassis. Next come the side walls (across two steps), followed by the roof. Now that the shell is assembled, the interior can be fitted, followed by standard and customer-specific components (in two steps). In the final steps, commissioning and inspections are carried out: first, the bus is driven across a section of the assembly line in an initial assessment; then comes quality control. Finally, the under-body coating is applied, and the bus can leave the factory for further testing before it is delivered to the customer.
Before they are assembled on the chassis, the various parts of the bus body are put together across six lines which run perpendicularly to the assembly line in the pre-assembly area. The floor, the back wall, the side walls, the roof, and some interior parts (as well as the cabin) are all built separately and are queued up for assembly on the chassis. During pre-assembly, the battery packs are installed in the floor of the bus. By attaching the floor and back wall first, a gap is allowed for the quick installation of certain interior furnishings (for instance, the seats) before assembly of the side walls. It is a very efficient and – as mentioned earlier – quiet process.
At the beginning of the tour, we were informed of VDL’s three manufacturing values during a presentation. I’ve recorded the original words in Dutch – betrouwbaarheid, innovatie, and duurzaamheid – which Google tells me translate to ‘reliability’, ‘innovation’, and ‘sustainability’. On the sustainability note, we were informed that the factory is largely self-sufficient in meeting its energy needs, thanks to an array of over 2,000 solar panels on its roof. But the value which was most in evidence on the factory floor was ‘efficiency’, which in Dutch is efficiëntie (according to Google). Had it been nominated as one of VDL’s manufacturing values, it would hardly need translating; and the evidences of it inside the factory – the clear layout of the floor, the elegant assembly process, and the quiet concentration of the workers – require no translation whatsoever.
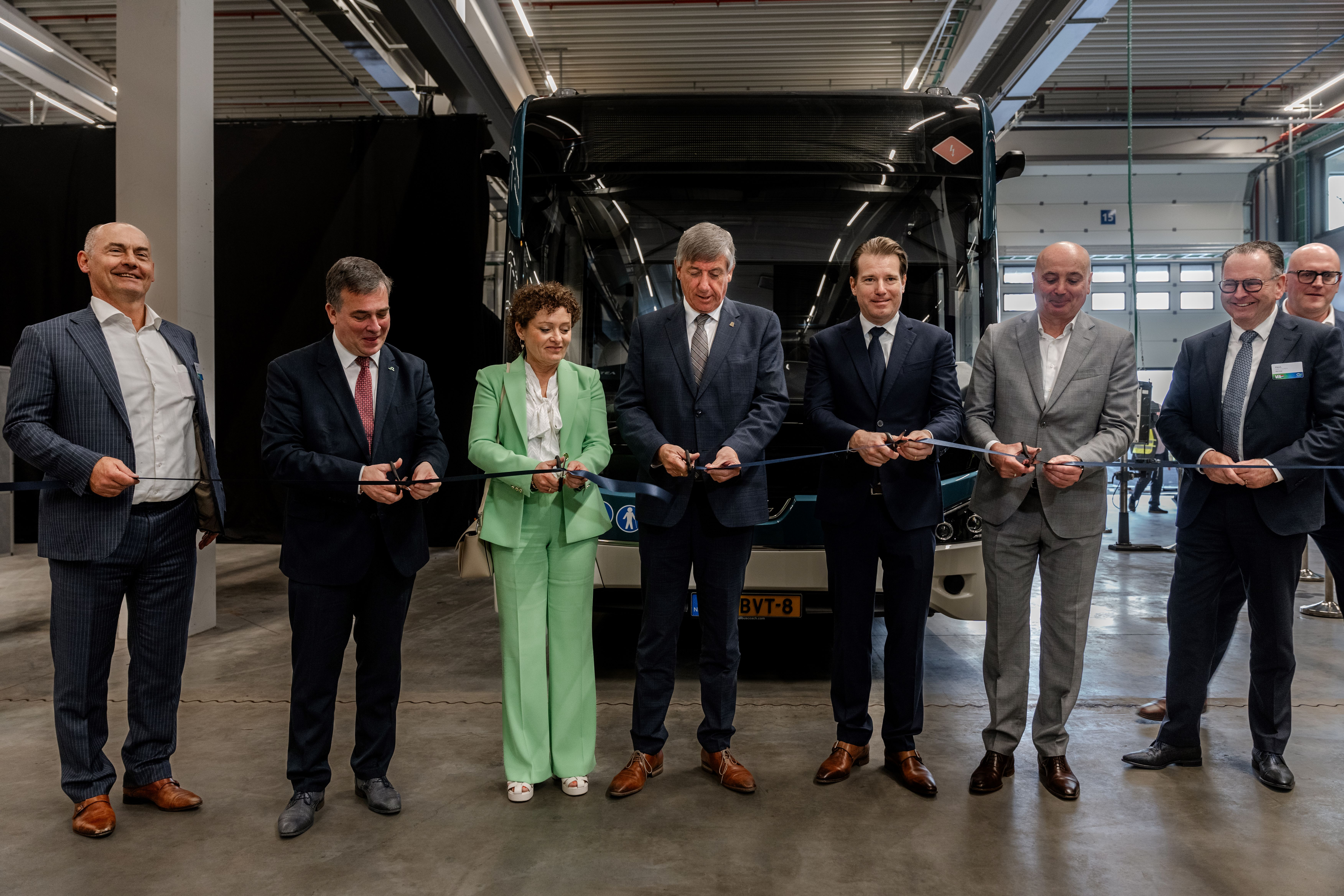
Ribbon cutting ceremony at the new VDL bus plant in Roeselare, Belgium
Press conference and panel discussion
The official opening ceremony was preceded by a press conference, during which executive members of VDL and local government officials addressed the audience. Willem van der Leegte, who was the first to speak, said that he considered the VDL Groep to be a “Dutch-Belgian” or “Dutch-Flemish” company. In reference to the situation at Van Hool, he admitted that the whole coach industry has undergone financial struggles since the COVID-19 pandemic. Nevertheless, VDL has made major investments in the business and is preparing to launch its new touring coach, the ‘Futura’, in the first quarter of 2025.
Van der Leegte complained that Europe’s automotive industry is competing on an unfair playing field, as high export duties to other markets (for example, the USA) are not matched by equivalent import duties to the European market. This was the first of many references, explicit as well as implicit, to China. The next came from Minister-President of Flanders Jan Jambon, who gave an equivocal vote of confidence in European industry when he said that Europe would stop buying Chinese goods only as soon as its manufacturers “step up to the mark”. He added that the news from Van Hool had been a “terrible blow”. While he accepted that the family business would not survive, Jambon assured the audience that the government would support the restart of production in Koningshooikt.
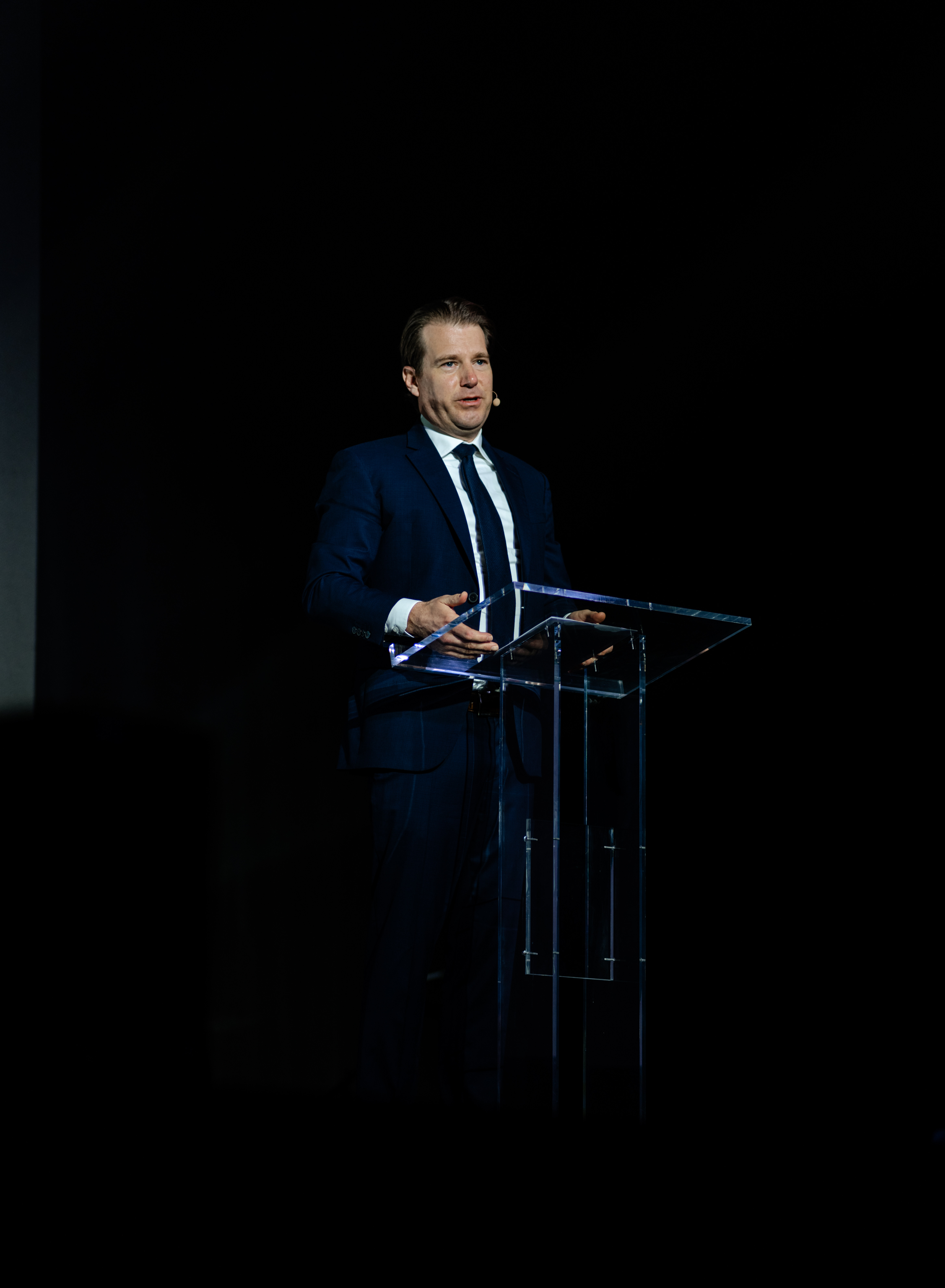
Willem van der Leegte, CEO of VDL Groep
During a panel discussion following immediately after the press conference, Lydia Peeters, who is the Flemish Minister for Mobility and Public Works, admitted that Europe had become economically overdependent on China. She stressed that the European Union needs an industrial strategy to become less dependent, and she advocated for a reduction in the rules for gaining permits to build new industrial sites. Alain Doucet, Director of the Roeselare site, said it had taken a lot of energy and persuasion to get the new factory built. It had been designed entirely around the new generation Citea, and was inspired by the VDL Nedcar facility in Born, Netherlands, where BMW and Mini cars are assembled by contract. Rounding off the discussion, Rolf-Jan Zweep, CEO of VDL Bus & Coach, noted that the situation at Van Hool was not unique to that company; rather, it is symptomatic of problems across the entire bus and coach industry.