Fitting for its purpose: Voith Electrical Drive System for heavy trucks
By Bradley Osborne - 10th January 2023
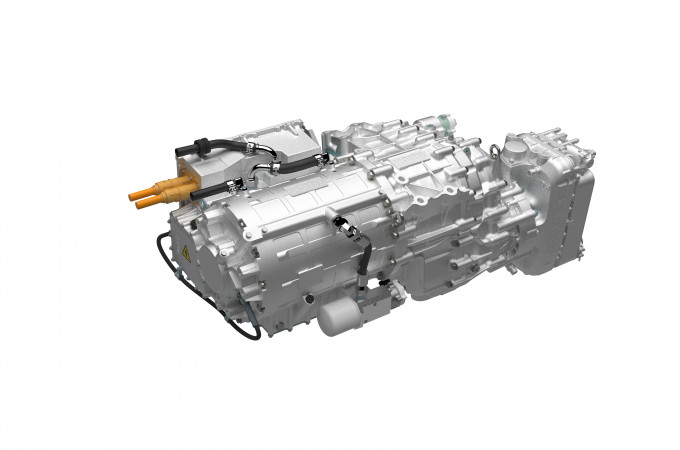
The Voith Electrical Drive System HD+
Germany – Electric motors are not entirely fit for purpose – that is to say, they are not fit for all the purposes which commercial vehicle operators would like them to fulfil. According to Alexander Denk at Voith, “the bus segment will be electrified (battery or fuel cell power) first, followed by the truck segment and lastly the off-highway mining and construction vehicles.” It has been much easier to transition urban buses to electric drives, as the performance requirements and the use cases of the city bus are more favourable to the needs and affordances of e-powertrains. As such, Voith was able, in the space of just two and a half years, to bring two drive systems – under the ‘Voith Electrical Drive System’ (VEDS) name – to market, specifically targeting the bus segment. It has taken longer to produce a similar drive system which can adequately perform in heavier duty applications due to the higher complexity and challenges to design drive train for heavy duty trucks. Nevertheless, Denk is confident that Voith has come up with a product that can push the electric motor into applications with much more challenging performance requirements.
The HD+ hardly looks like it is related to the heavy duty (HD) and medium duty (MD) applications preceding it. Yet there is in fact a connection between them – if not a family resemblance. Voith began developing its electric drive platform in 2017, and in 2018 it produced its first prototype of the HD. Customer deliveries began at the end of 2019 for the HD, and six months later the MD followed. However, the company has continued to develop the technology, and the results are not only a drive system that will be capable of handling tougher applications, but innovations which can be applied across the platform and will inform the development of the next generation of HD and MD systems.
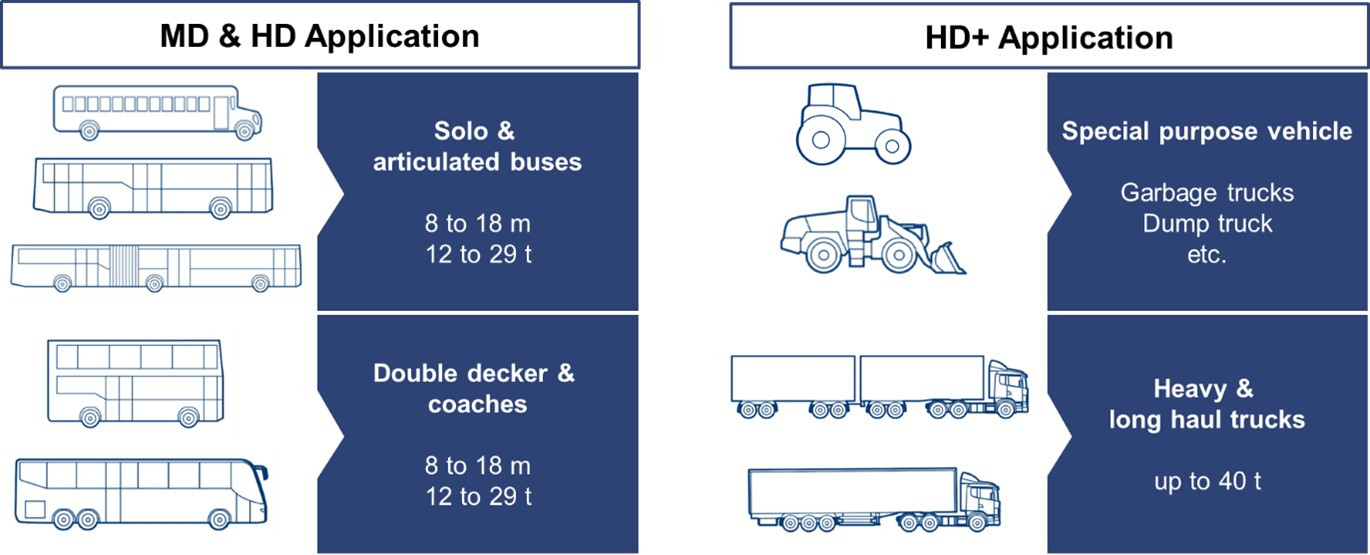
Applications of the HD/MD and HD+ by segment
The MD drive system is designed for city bus applications, on routes that are relatively undemanding and with easy access to charging points. The HD is better suited to more difficult transport applications – larger articulated buses and to coaches which require better performance and greater range. The HD+ takes a significant leap forward to a very different set of applications: dump trucks, concrete mixer trucks, and other trucks for urban construction purposes, as well as long haul trucks for goods distribution.
Specifications and design of the HD+
How has Voith achieved this? The answer, for the most part, is greater torque. While the maximum torque available on the HD is 3,100 Nm, in the higher spec HD+ (the EVO 390), the maximum torque is 12,840 Nm – more than four times greater. This is provided by the addition of an automatic manual transmission (AMT) with four gears which Denk says was designed from the ground up for the purpose of serving the HD+ electric motor. The alternative option, he says, would have been to considerably expand the size of the electric motor; but this would entail extending the diameter of the motor to an unwieldy 80 centimetres. In fact, the new e-motor for the HD+ is smaller and lighter than the motor in the HD/MD, meaning that the additional weight of the transmission does not make the whole system much heavier than the HD/MD system. The HD+ motor is also much faster, with an RPM of 10,500 (compared to 2,500 and 3,800 in the MD and HD). The transmission converts the motor power to torque, allowing for the extra push to haul heavy loads that trucks need.
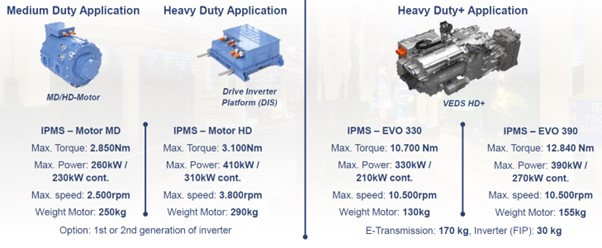
Specifications of the HD+ compared with the HD and MD
The greater torque does not provide everything that heavier demands require, though. Some customers will need considerable braking energy too, which were fulfilled in the conventional truck by the engine brake and the retarder. As a result, Voith will offer the option of a retarder with the HD+ that will connect directly to the transmission. According to Denk, the additional retarder will provide braking energy up to 650kW – vital for stopping a fast-moving and heavily-laden vehicle. Again, as with the transmission, the alternative option is unappealing: it would mean adding a secondary electric motor designed only to provide the required braking power. The solution of offering an optional retarder is, in Voith’s view, a more elegant one and unique in the market. In this respect, Voith has benefited from its many years of experience in the retarder business.
Savings in space and weight have also been made in the design of the new inverter, which is improved over the first inverter generation offered with the HD and MD. The inverter now incorporates the control unit, which is a discrete component in the HD/MD VEDS scope. The entire component – inverter plus control unit – in the HD+ provides greater power density and offers improved cybersecurity, according to Denk. As such, future generations of the HD and MD will also use the new inverter, with the separate inverter and control unit currently in use gradually being phased out.
The control unit is the master of the entire system, including the transmission. The parts which determine when to shift gears – the actuator and the oil pump – are “smart”, precisely calculating the optimum gear ratio for each situation. Denk claims that the shifting speed of the transmission is swift – that is, between 0.6 and 0.8 seconds – even without powershift or excessive cabling.
For the HD+, Voith has developed a range of different components that have obvious applications outside of the product in which they have been packaged. But Denk stresses that Voith is not in the business of merely supplying parts: it is a systems developer, and the VEDS HD+ (as well as the VEDS HD and MD) works best as a system of complementary parts designed to work together, and not apart from one another. The Voith Electrical Drive System is offered to customers as a complete unit, designed to be easily integrated (“plug and play”) into any electric powertrain. This does not preclude the customer from customising the system to meet their needs: indeed, Denk says that Voith is prepared to offer 40 variations for trucks and 700 variations for buses based on the fundamental product package, a dizzying number which accounts for the inclusion of other optional parts, including converters, charge control units, and cable harnessing. The balance Voith is attempting to strike – the balance which systems manufacturers so often seek – is between offering consistency in reliability and performance which is best provided by a coherent and integrated system of parts, and the flexibility to customise, add to, and subtract from that system to accommodate the user.
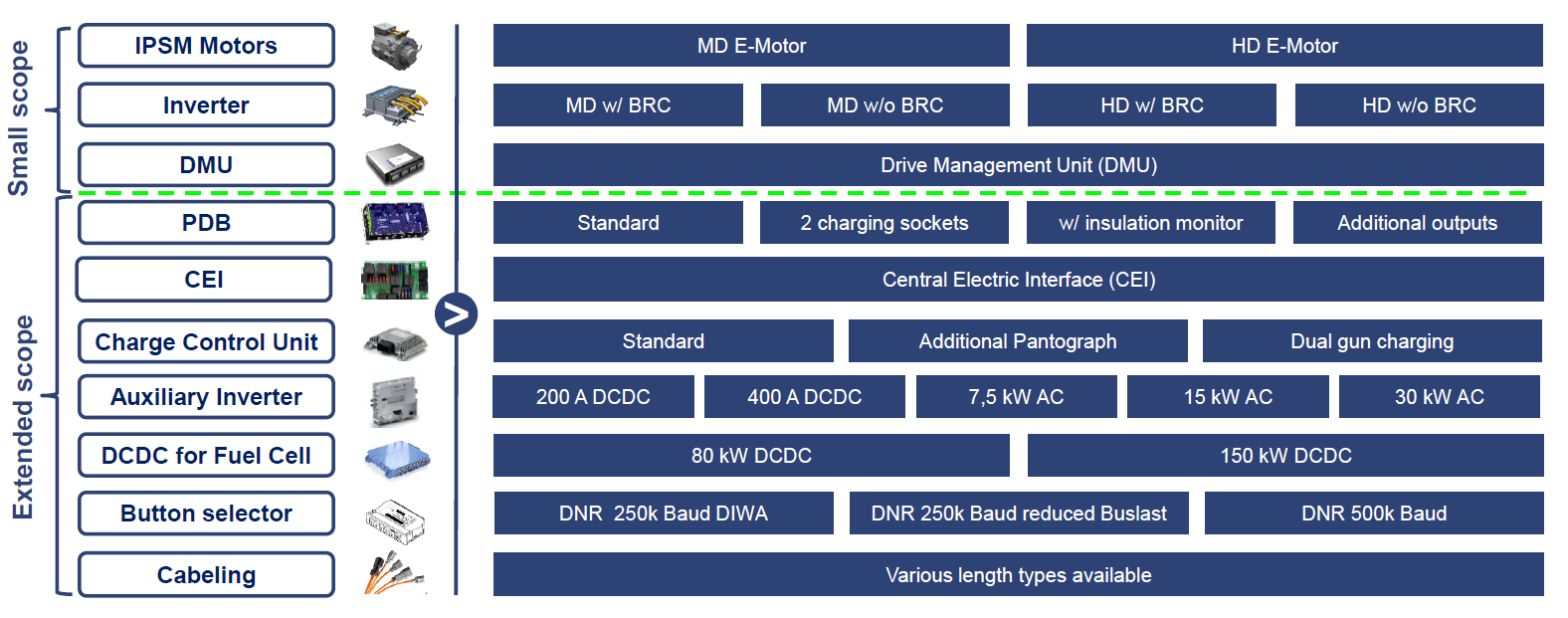
List of VEDS modular options available
The future of the VEDS
Development of the electric drive platform has drawn on the varied resources the Voith Group has under its command. While production of electronics and e-drive components takes place across the border at Sankt Pölten in Austria, the developers of the HD+ have also drawn on the mechanical expertise at Garching, near Munich, to produce the transmission. Research and development responsibilities were shared between Sankt Pölten and the group headquarters at Heidenheim an der Brenz in Baden-Württemberg.
The HD and MD can already be found in the vehicles of multiple bus manufacturers: Alexander Dennis, Wrightbus, Otokar and Iveco Bus can all be counted as VEDS customers. Retrofit bus and truck companies such as Orten, CCW and pepper motion have also made use of Voith’s system in electrifying diesel vehicles. Denk says that Voith is already in talks with truck OEMs regarding the HD+, as customer tests of the system are set to begin imminently, in advance of a slated late 2023 or early 2024 commercial launch.
Voith is keen not to alienate the truck manufacturers with its new offering. This partly motivated the decision, Denk claims, to opt for a central traction motor instead of a e-axle or wheel-hub motor. The truck OEMs are already coming out with their own electric axles, which Denk points out was shown by the most recent IAA. Instead of directly competing with them, Voith has chosen to go instead with options that will provide a “complementary portfolio” to the other products on the market. The HD+ will address needs that are harder to meet with e-axles: construction vehicles, distribution vehicles, and vehicles with super low frames and special axles.
Denk vouches for Voith’s central motor for other reasons too. An electric axle certainly takes up less space overall, but it is restrictive in other ways that Denk believes leads to compromises in reliability and efficiency. According to Voith’s conversations with its customers, operators want buses with high range and reliability and low running costs – and these needs, in Denk’s view, are best met by the centrally-placed (albeit bulkier) motor which Voith is offering.
When asked what Voith’s priorities are for future research and development into electric drive systems, Denk listed three “pain points”. Keeping the motor sufficiently cool remains an ongoing concern. The EVO 390 option in the HD+ is the first motor, Denk says, that Voith has produced which incorporates an active cooling system, with fluid moving through the rotor and bringing down the temperature of the magnets and the winding heads. Further improvements, however, will be required to improve the system’s performance. Future electric drive systems will also need to be compatible with the latest tech. Silicon carbide semiconductors, which are already standard in passenger cars, will require that electric motors are sufficiently insulated from spikes in voltage.
Perhaps the biggest step forward that manufacturers of electric drives will need to take is to remove the magnets. Most electric motors produce mechanical power with the use of permanent magnets made from scarce and expensive minerals. It is possible to make motors that are “excited” by a direct current alone, without the need for any magnets; but making such motors capable of reliably performing as well as a permanent-magnet motor will take more time. But it is a prize well worth aiming for, in Denk’s view. It would mean that electric drive manufacturers such as Voith would no longer be beholden to the volatile prices of rare magnet materials such as neodymium. Nothing else will drive the cost of production down quite as much as removing the magnets, according to Denk. Once the cost sinks, companies such as Voith will have more to spend on developing even more ingenious electric drive systems – systems that will be fit to carry out tougher jobs.
Alexander Denk is Vice President Product Line at Voith Turbo, a division of Voith Group focused on road and rail. After studying automotive engineering, Denk joined the company in 2007, starting out as a test engineer for transmissions and clutches for trucks. In 2016, he was promoted to Product Manager and Technical Expert, Retarder and Clutch Systems. He entered his current post in 2018.