Michelin celebrates 100 years of tyre retreading
By Bradley Osborne - 17th October 2023
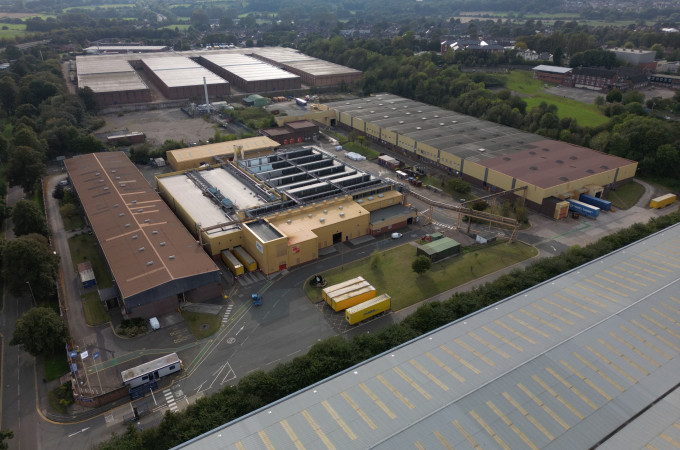
Aerial view of the Michelin Remix factory in Stoke-on-Trent
UK – This year, the Michelin Group is celebrating an important milestone in its long history of motor tyre manufacturing. In 1923, the French company developed a method for applying a new tread to old tyres, thus extending their useful life. One hundred years later, Michelin Tyre Plc commemorated the anniversary at the ‘Michelin Remix’ factory in Stoke-on-Trent, UK, where the company has been retreading truck and bus tyres since 1968.
The technology behind the retreading of tyres may be old, but Michelin’s promotion of the method is based on new values. By retreading used tyres instead of replacing them with new ones, Michelin claims it can reduce the consumption of raw material per tyre by 70%. The practice of retreading old tyres is therefore less wasteful and more sustainable. Getting the most out of a truck or bus tyre is an important environmental consideration for Michelin, given that natural rubber remains the primary material in its new tyres. The industry’s reliance on natural rubber is likely to persist for a long time: Michelin’s target for producing only tyres made entirely from recycled materials is 2050.
The original argument in favour of retreading was economical, and Michelin makes the total cost of ownership case for retreading even today. The method gives the old tyre a second life, while costing about 30% less than replacing it with a new one. Supposing the operator also has it regrooved twice (before and after retreading), the mileage of a tyre can be extended by 150% beyond its first life. This is what Michelin calls its “four lives philosophy” – though really it is a two lives philosophy with two half-lives (from regrooving) added on.
The Stoke factory is one of several places in Europe where tyre retreading takes place. According to Michelin, there are 32,000 people employed in the European retreading industry. It takes six months to train up a new hire to retread tyres. In Stoke, 180 people are involved in the retreading process. Nevertheless, there were signs of trouble only last year, when the BBC reported that the Unite worker’s union was seeking “cast-iron guarantees” from Michelin that it would keep the site open in the long term, after temporary pauses in production caused by an unfavourable market. Some workers will no doubt remember the termination of new tyre production at Stoke in 2000, removing approximately 950 jobs and ending a manufacturing lineage dating back to 1927.1
However, Michelin is firmly optimistic about the future of its retreading business. The growing adoption of sustainability commitments by hauliers and transport operators is bound to favour the reuse of old tyres over replacement with new ones. Moreover, the company is continually investing in the site. In 2015, the company announced a GBP12m investment, some of which went towards new retreading machinery; since then, it has invested some one million pounds per year. Though the company faces competition from newer and cheaper competitors, Andrew French, B2B Sales Director for the UK, told press that Michelin tyres represent the best value for money, being higher quality, longer lasting, and more sustainable.
Details of the retreading facility in Stoke-on-Trent
The Remix Factory in Stoke is geared towards a single retreading method, the “hot cure” or “mould cure” method. Although Michelin carries out “cold cure” retreading in other places, it favours hot cure in Stoke because the UK market prefers it. (Only a quarter of the UK retread market is based on the cold cure method.) Vincent Gridel, the factory manager, showed T&BB and other members of the press round the retread facilities.
The first stop on the tour was the ‘Casing Acceptance Workshop’, where incoming tyres are assessed for damage and marked either for repair or disposal. Some one in ten of tyres which come in for retreading are judged to be beyond repair. Gridel told us that tyre casings are typically rejected because the sidewall has sustained too much damage. Operators who look after their tyres well, by practicing good tyre inflation management, using the right tyre for the job, and servicing them periodically, are more likely to avoid irreparable damage of this kind, according to Gridel.
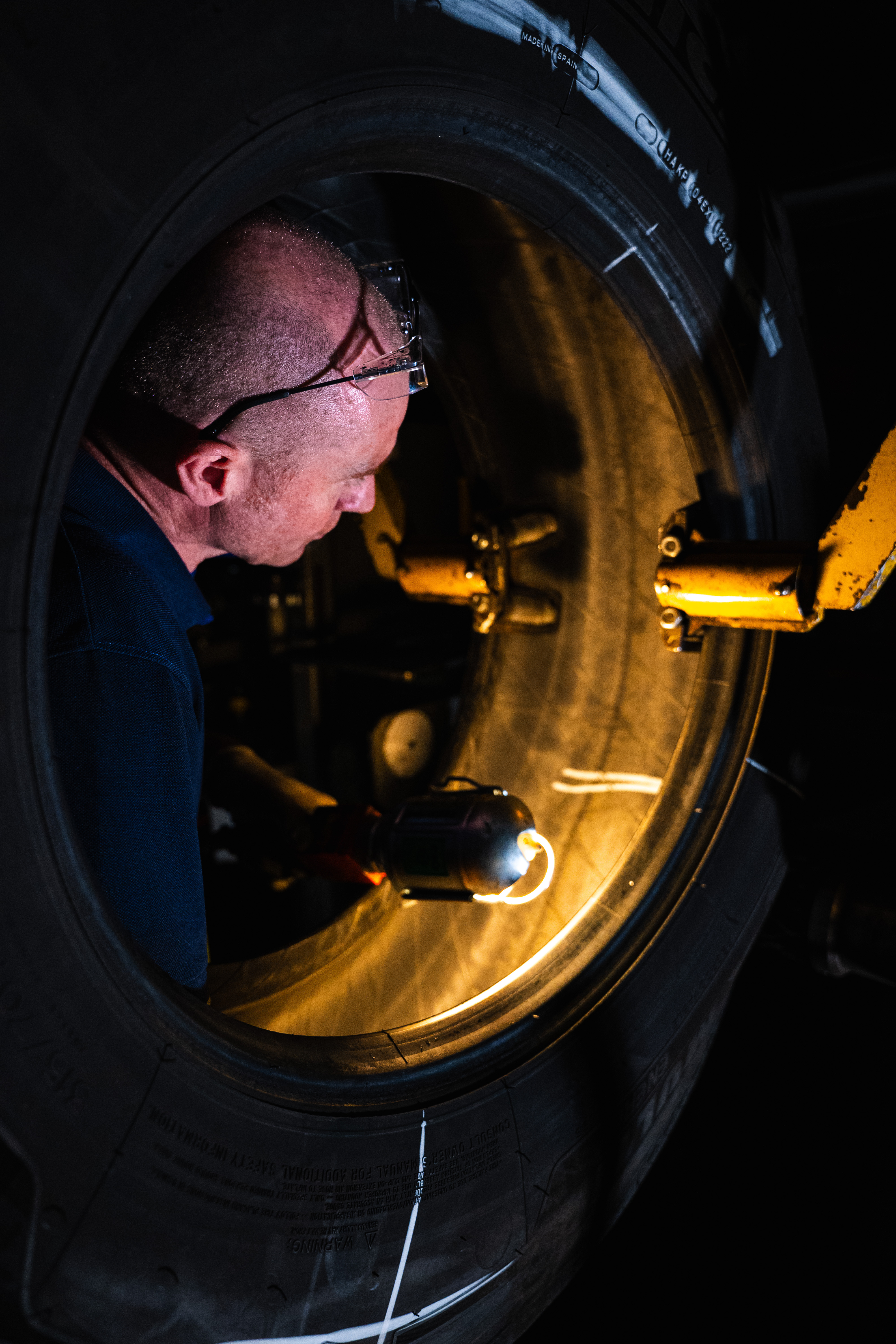
Tyre undergoing initial inspection
The vast majority of tyres which come in for inspection are cleaned first with a hot jet wash. Every tyre is then assessed in a test cell, in which a single technician examines the tyre and identifies flaws with the help of a metal probe. There are nine cells in the workshop, and each one can process 92 tyres in a single day. Of all the tyres, 60% are sent to the shearograph and 25% to the X-ray machine for more thorough inspection.
The vacuum shearograph produces images of the tyre that show up flaws invisible to the naked eye. It can find evidence of rubber separation and air bubbles in the fabric of the tyre; it can find localised damage caused by a sudden impact; and it can find embedded debris and nails. X-ray imaging is used to identify flaws, often caused by rust, in the metal wiring that forms the skeleton of the tyre. Some tyres go to the shearograph and some to the X-ray machine; some go to both, and some to neither. However, all bus tyres are X-rayed, regardless of their apparent wear and tear, due to the heavy beating they sustain during operation (for instance, damage from regularly mounting the curb).
We were shown a tyre that had just been assessed as irredeemable following an X-ray, which showed that the metal wiring was considerably damaged. Every tyre which Michelin rejects for retreading is slashed clean through so that it cannot be reused by an unscrupulous operator. Rejected tyres can be recycled for a variety of purposes: for example, shredded tyres can be used to make rubber mulch for landscaping in playgrounds.
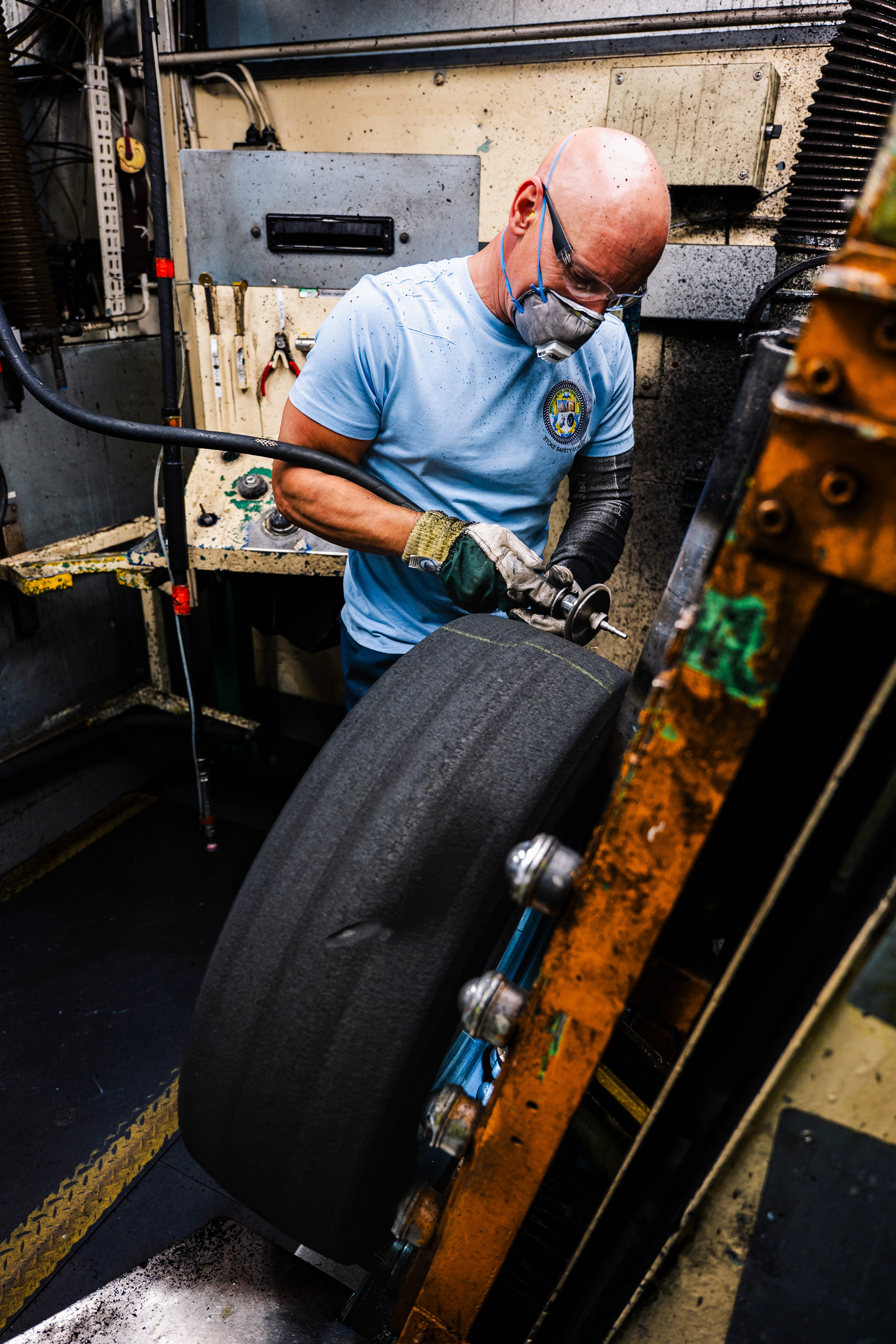
Operative preparing the tyre for retreading
We moved on to the retreading facility, which is in an adjacent building. Every tyre which makes it to this building has its old tread stripped off by a buffing machine prior to yet another inspection. During the second assessment, any damage is cut away to expose particular flaws due to, for instance, nails or rust. Large holes are filled in with compound and patched up.
After any flaws in the casing are addressed, the tyre finally reaches the retread part of the process. In the Michelin Remix factory, there are two lines operating in parallel for retreading all tyres which make it through the various assessment and patching stages. A new tread is applied to the tyre casing; afterwards, the tyre’s unique ID/barcode is fixed back onto the case. This, we were told, was a tedious manual job up until 18 months ago, when Michelin invested in robots to stick the barcode on automatically.
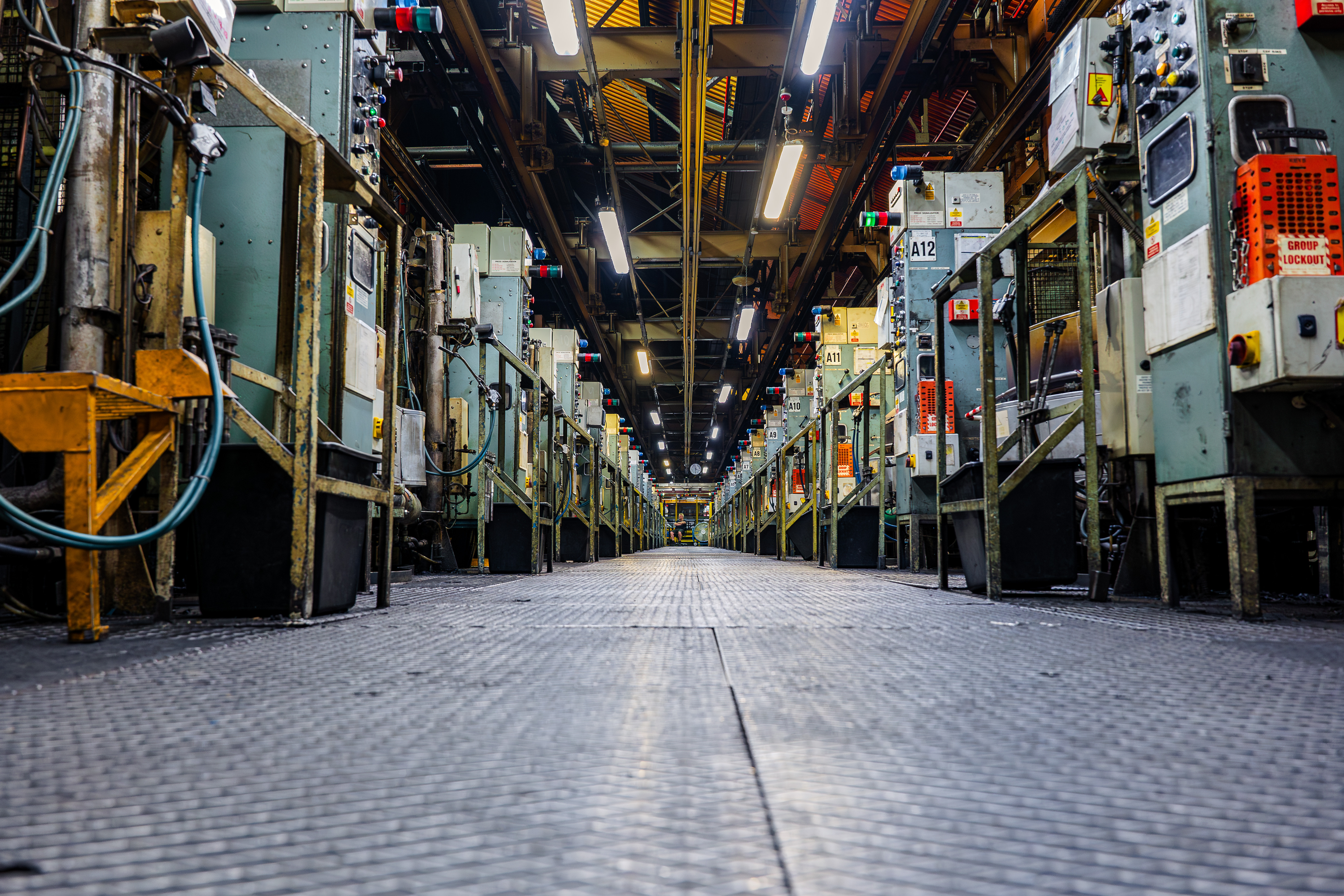
Hot cure presses inside the retread facility
As mentioned earlier, Michelin favours the hot cure method of retreading at the Stoke factory. This involves placing the tyre and the new tread in a curing press for up to an hour; a mould imprints the desired pattern onto the new tread and the tyre comes out looking like new. The hot cure line we saw had 26 curing presses. When the process finishes, the tyre is taken out and left to cool for one hour.
The post-curing process involves testing the finished tyre in a “Hawkinson machine”, before inflating it to 10 bar pressure. An operative told us between 230 and 240 tyres come through the final testing and inflation room per day.
1 From The Guardian, 18 October 2000.