EV charging “Testival” at Ekoenergetyka: a T&BB feature
By Bradley Osborne - 23rd July 2024
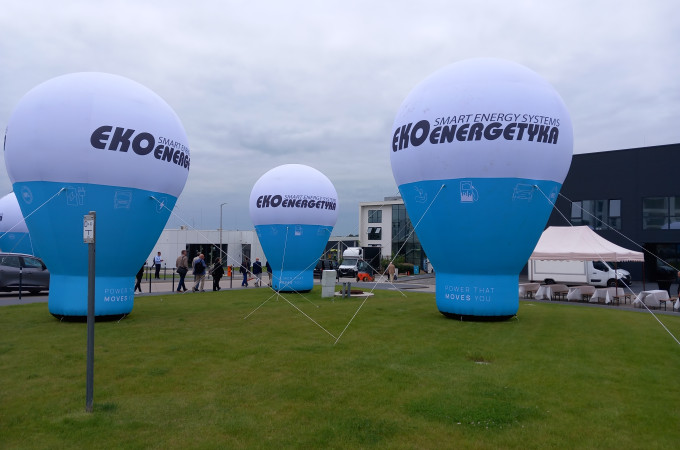
CharIN Testival and Conference at the Ekoenergetyka site
Poland – Somewhere in the industrial estate of a small city in western Poland, there is a charging station which was installed by me. I had some help, of course: there were the people who prepared the ground for the installation; there was the truck driver who delivered the station and operated the small crane which lifted it and placed it down in the right spot; and there were the electricians who secured the station in place and oversaw the whole operation. But I hooked up one of the wires that connects the station to the grid, and without this essential contribution, the unit simply wouldn’t work! Once the unit was in place, it was switched on and plugged into a car, and almost immediately the charging began. Even with my (inexpert) participation, the installation – excepting the preparation of the spot prior to the station’s arrival – took no longer than thirty minutes; undoubtedly, it would have taken even less time had the technicians not had to explain and demonstrate every step to a large audience of journalists and representatives from the charging industry.
An explanation of the context is in order. We were on the outskirts of Zielona Góra, a city which is probably little known to most readers, but which is only a couple of hours away from Berlin. The site of the installation was near the headquarters of Ekoenergetyka, the manufacturer of the charging station in question, and the hosts of a conference which brought together several hundred guests involved or interested in the development of Europe’s charging infrastructure. The event, organised by an industry association called CharIn, was the third such conference and “testival” to have taken place in Europe since 2023.
On the first day of the four-day event, multiple speeches and panel discussions were held on topics such as sustainability, finance, and interoperability. As a member of the press, however, I got to attend only a couple of these; for most of the day, we were taken round the company’s production lines and research and development facilities, many of which are brand new. On the second day – the day I left – we attended several workshops before watching (and participating in!) the installation of the charging station.
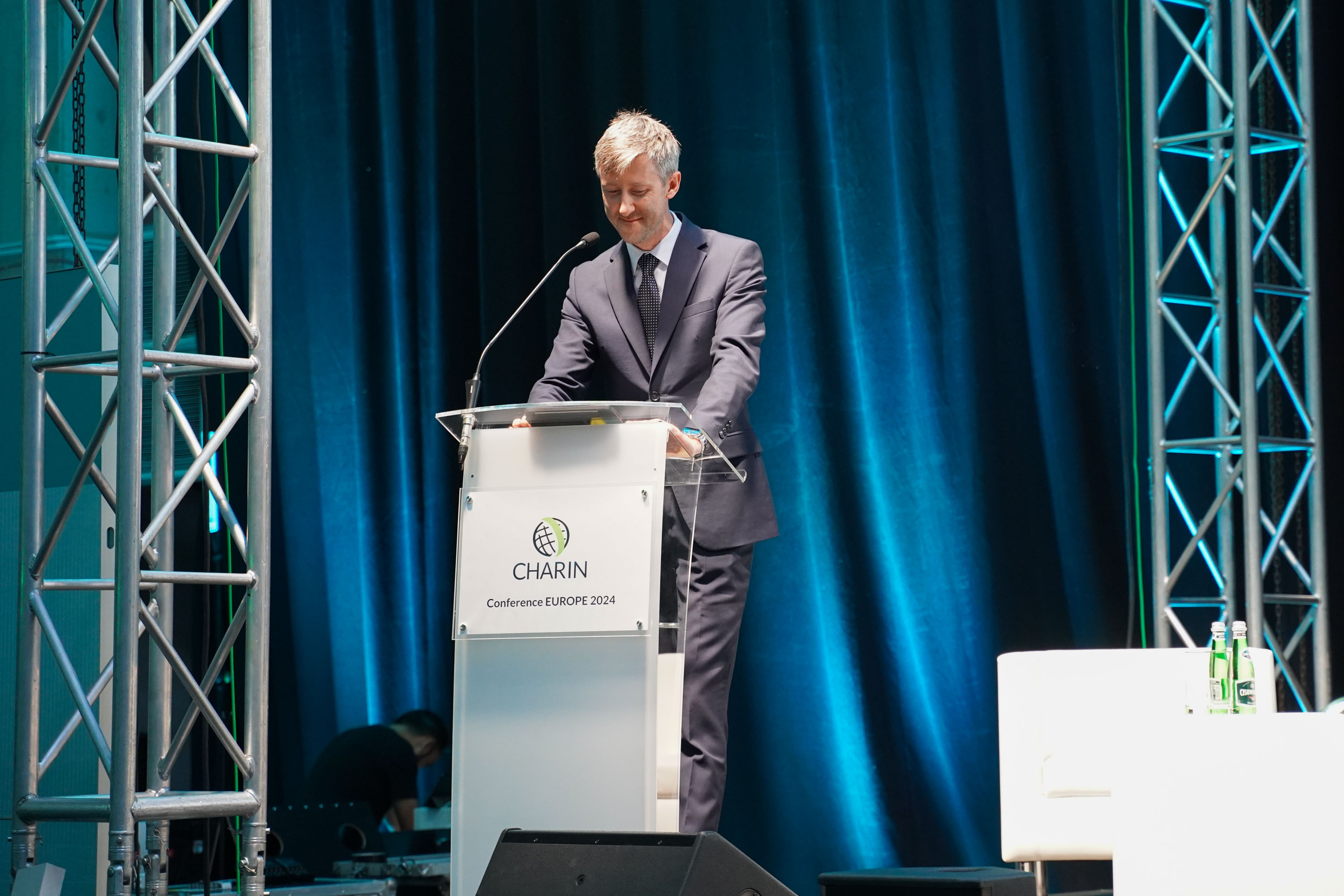
Maciej Wojenski speaking at the conference
Ekoenergetyka was founded in 2009, starting out as a university spin-off before becoming the 1,000-strong company which it is today. Co-founder Maciej Wojenski gave the press an outline of the company, which has worked with OEMs such as Volvo, Daimler Truck, and Scania to ensure that its chargers will work with commercial vehicles as well as cars. The company specialises in the development and production of DC fast chargers: in 2020, its 1,000th charger was installed, and as of today, it claims to have over 6,800 charging stations operating in Europe and Turkey. In Europe, it claims a 20% share of the market for municipal bus charging stations. Though it started to welcome outside investors in 2022, Ekoenergetyka remains a private company, which produces chargers according to its own design and develops the software in-house.
The ostensible reasons for our visit to the company headquarters were these: to see the latest innovations in charger design and to learn about the company’s newly opened production line. Naturally, however, we learned about a great deal more than that, including EU funding into e-mobility and the science behind megawatt charging. It was not easy to discover how much is being invested in Ekoenergetyka’s new facilities or how much of it is coming from public money; at the very least, I found out that the investments into the research and development labs were over EUR50m, and I imagine that just as much, if not more, is being invested in production. Enterprise Investors, one of Poland’s largest equity funds and a backer of Ekoenergetyka since 2022, is reportedly committing more than EUR45m towards e-mobility projects. And the “E-mobility Innovation Hub”, where the conference mainly took place, was supported by over PLN8.8m (or over EUR2m) in EU grant money. The rest of what I was able to discover is laid out below.
Production and R&D at Ekoenergetyka
The Ekoenergetyka site, comprising several buildings, covers approximately eight hectares on an industrial estate (“Nowy Kisielin”) located to the east of Zielona Góra. Wojenski told the press that when the company began manufacturing charging stations in the early 2010s, it started with small-scale production of highly customised units. Later on, the first production line for a standardised output was established, and today the company’s production capacity is 10,000 stations per annum. With the introduction of a new line and planned investments in automation, the company aims to double its capacity over the next several years.
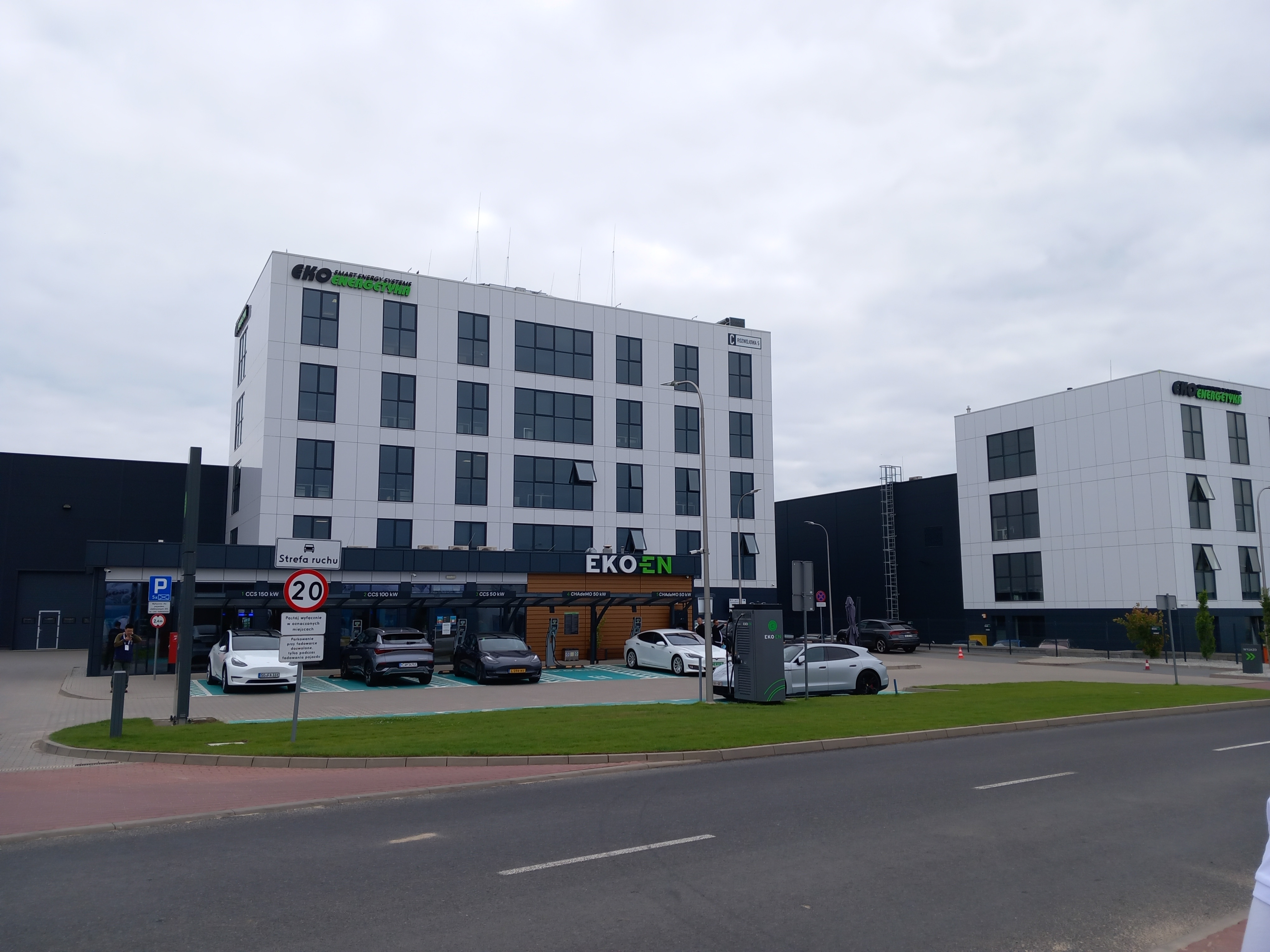
Ekoenergetyka headquarters
Ekoenergetyka produces several types of charging station. Its ‘Plug Charger Go’ range is designed to be highly mobile, using an onboard battery pack to deliver between 30 and 80 kW of power. However, its core products are the ‘Axon’ and ‘Satellite’ ranges, stationary units intended for installation in a charging park or at a vehicle depot. The Axon is a power unit which connects to a Satellite charging station to provide DC charging: in a typical setup, the Axon unit connects to each Satellite charger via underground cabling and can (depending on the power rating) deliver power to up to three charging stations. Depending on the unit, the Axon delivers a total output of 180-400 kW, which is split between each Satellite charger.
There is one product range – the ‘Axon Easy’ – which combines the power unit and chargers all in one, and this is what we saw being installed during the product demonstration. Depending on the specification, the Axon Easy provides 60, 120, or 180 kW at a charging current of up to 500 A. The power is split between two chargers, which hook up to a car, a van, a bus, or a truck. This product features one of Ekoenergetyka’s most recent innovations: an “ergonomic cable management system”, a fancy way of saying that the plug cabling is attached to an extendable mounting on the top of the unit. When the plug is not in use, the cable is rigged up to the unit; when the plug is in use, the cable will extend up to four and a half metres to the vehicle and remain suspended in the air, making sure that it does not trail along the ground.
Another innovation featured by the Axon Easy is a dynamic load balancing system or, in other words, an integrated piece of software which will automatically redistribute power between the two connections. If two vehicles are charging simultaneously, the power is usually distributed evenly: however, depending on the vehicles’ respective states of charge, the charging station can automatically redistribute the power so that one vehicle is receiving more power than the other. In a case where one vehicle has finished charging first, the other vehicle will then receive full power (instead of half).
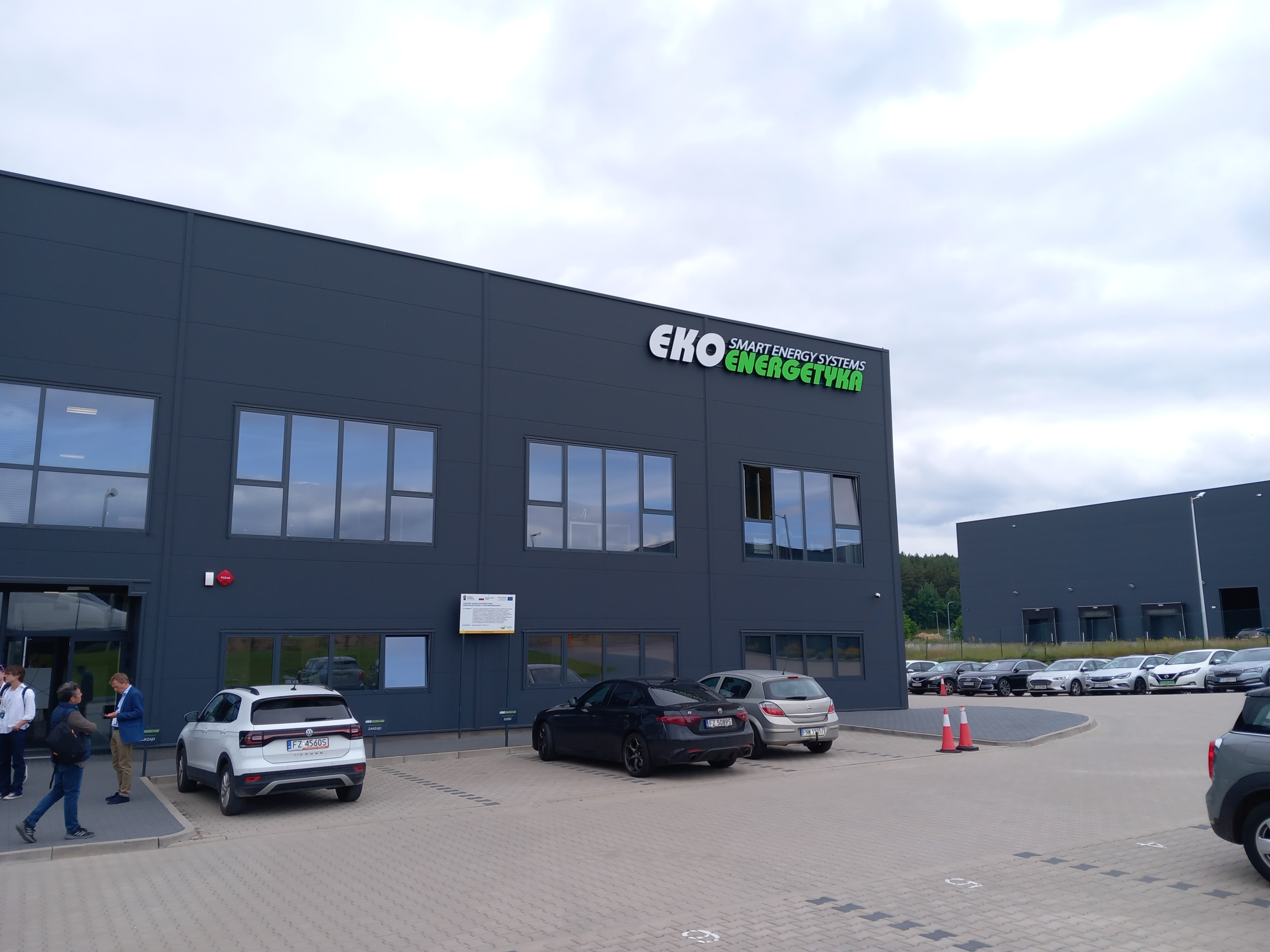
Ekoenergetyka production and R&D facility
The entire range of Ekoenergetyka’s power units and charging stations is assembled in its factory across several lines. The production lines we were shown were not automated; instead, workers were based at individual workstations and would assemble entire component assemblies or exterior casings on their own. On a typical eight-hour shift, these workers can produce up to fifty charging stations. However, with the introduction of the new line, Ekoenergetyka intends to expand this figure to ninety units per shift by 2025. Moreover, the company plans to switch from its current process to an automated production line, with industrial robots incorporated into certain elements of the process.
On a separate floor, we viewed the subcomponent assembly, which combines industrial machines with individual workstations for soldering electronic parts. Next to this, wire harnesses are produced and subcomponents are tested in cells. What we saw was a single shift pattern: the subcomponent assembly floor is not currently operating at its full capacity. Around forty-four workers were split evenly between electronics and wire harness production.
In the R&D labs, we were shown two “rooms” which Ekoenergetyka uses to test its charging technology. The first was an acoustic anechoic chamber for precisely measuring the level of noise produced by the charger. Four microphones are set up around the charging station, picking up the noise which is generated while energy flows in and out of the charger to/from the mains. The second was a radio-frequency anechoic chamber which measures radiation patterns. Though the chamber was empty when we viewed it, when in use, a charging station is placed inside to assess its vulnerability to electromagnetic interference.
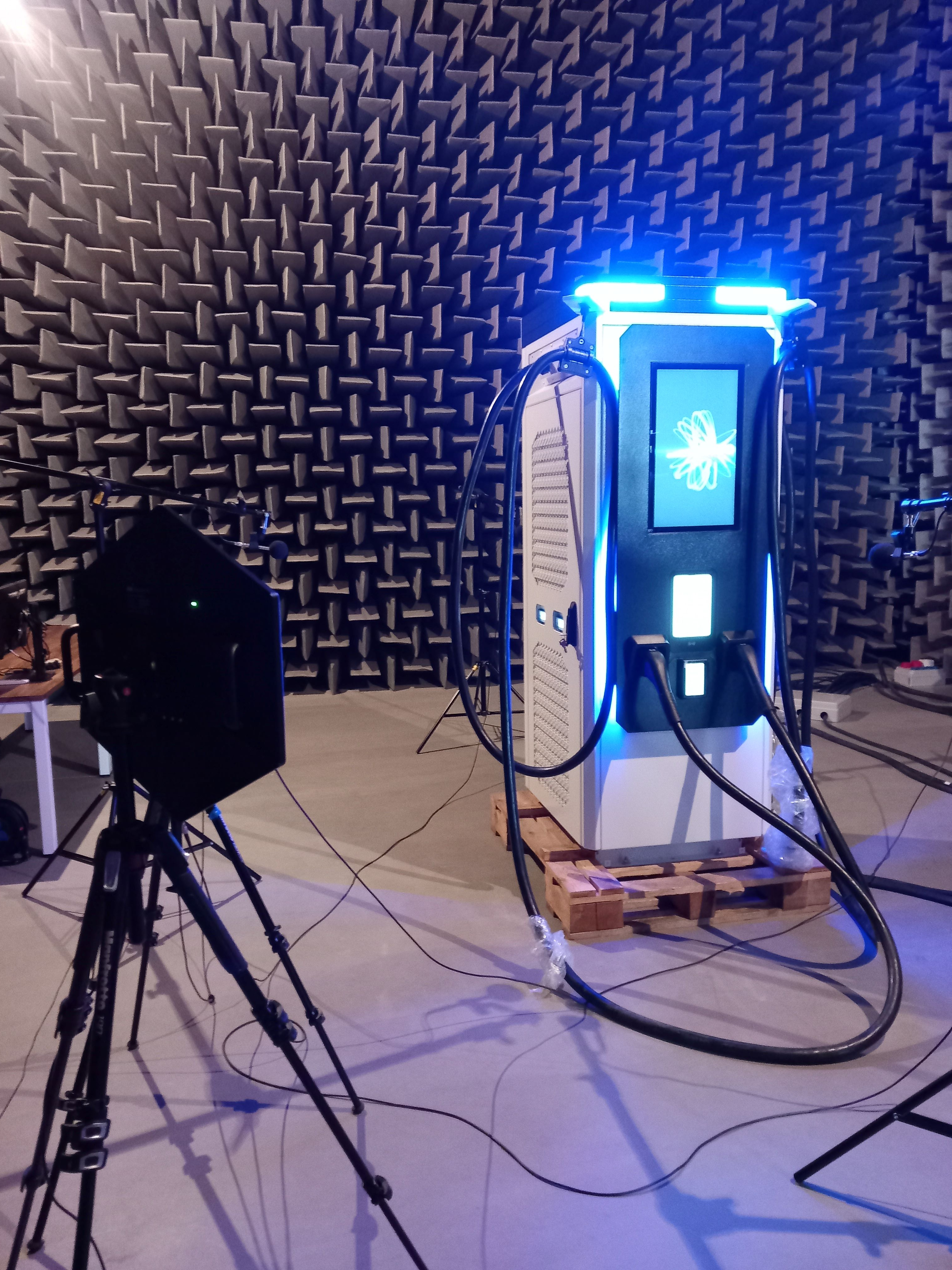
Inside the acoustic anechoic chamber
Finally, we were shown an office where Ekoenergetyka remotely monitors every one of its charging stations which are currently in use out in the world. Across multiple screens, one can see at a glance which charging stations are in use, and which are not working properly.
Megawatt charging
On the second day of the event, a useful presentation on the forthcoming “Megawatt Charging System” (MCS) was given. I present below the salient points.
MCS is an upgrade to the current CCS or “Combined Charging Standard”, defined as “an extension of the Type 2 standard with two large contacts for DC charging”. The design of a plug which follows the combined charging standard allows for either AC or DC charging, depending on what the vehicle can take and whether or not the operator is recharging his vehicle during a quick stop (DC fast) or overnight (AC slow). With the CCS charger, it is possible to deliver as much as 850 kW, though in reality, most CCS chargers have a much lower power rating than that.
With MCS – defined as “a development of the Type 4 standard developed for charging electric vehicles equipped with large batteries” – the 1,000 kW or 1 MW barrier can be breached, allowing for even faster recharging of the heaviest vehicles on the road.
The presentation outlined two possible scenarios. At 1,000 V, an MCS charger with a current of 1,000 A and a rating of 1,000 kW could recharge an electric truck (with 500 kWh energy capacity) from 10-80% in just twenty-one minutes. If that does not sound fast enough, the second scenario, involving an MCS charger at 1,000 V with a current of 3,000 A and a rating of 3,750 kW, suggested that the same truck could be recharged from 10-80% in only five minutes! These figures would mean that, with a 1,000-kW charger, 9 minutes of charging time would be required per 100 km; with a 3,750-kW charger, just 2.5 minutes of charging time would be required per 100 km. With megawatt infrastructure installed in the right places, a battery electric truck could cover thousands of kilometres while only needing to pause a couple of times for a less-than-ten-minute recharge per stop.
There are drawbacks, however. Multiple 3,750-kW chargers would place a significant burden on the grid; and MCS chargers require sophisticated cooling methods in order to avoid overheating while in use.
Moreover, in many scenarios, it is unlikely that a single truck would receive the full output of a megawatt charger. One 1,500 kW power unit would likely be connected to multiple charging stations, splitting the power between two to three vehicles at a time. In addition, it would be possible to configure a unit so that one plug would provide MCS charging while the other would provide CCS – a so-called “split charging system”. In any case, while many drivers won’t see their charging times shaved down to five minutes anytime soon, megawatt charging could considerably reduce the time taken by each vehicle during its pause, thus extending duty cycles and increasing the number of vehicles which can be served daily by a charging station.