On the move: Slovakian start-up battery manufacturer InoBat set for a bumper 2023
By Luke Willetts - 9th February 2023
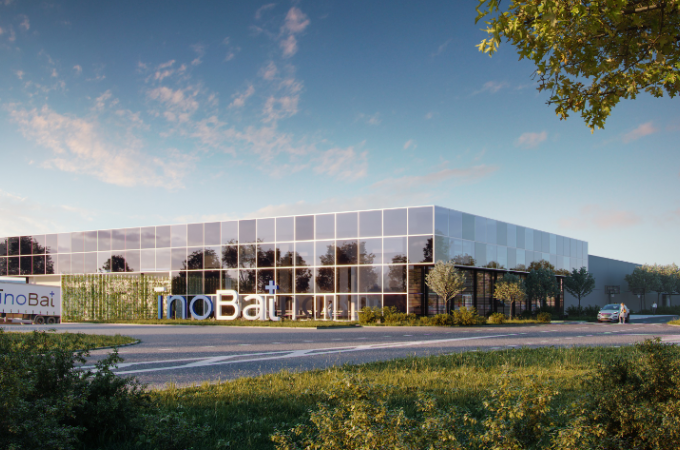
InoBat headquarters in Slovakia
The Genesis of Inobat
Slovakia - 2019 was the year R&D and battery cell production company, InoBat, headquartered in Bratislava, Slovakia, was established by founder and CEO, Marian Bocek. Bocek began his career as an investment banker on Wall Street and in 2014, co-founded the IPM Group, an asset and wealth management company with more than USD1 billion in assets under management, specialising in infrastructure and infrastructure technology companies. Based in London, today it has offices in Bratislava, Seoul, San Francisco and Hong Kong.
In January this year, T&BB had the opportunity to interview Nicola Rimmington (Director of Strategy Development at InoBat) and Iain Wight (InoBat’s Chief Commercial Officer) to get a sense of the past, present and future of this exciting new entity.
Wight explained that the start-up is aiming to take on the established competition, but not at their own game. Instead, InoBat is positioning itself as a producer of customised battery cells that are tweaked for a variety of duty cycles and applications that operators require, with plans to consistently produce those battery cells for their clients in the future. He emphasised that the standard battery chemistries that are readily available from mainstream manufacturers are largely tuned for the use cycle of passenger vehicles, and for vehicles that do not fit the duty cycle of a passenger car, i.e. specialist batteries with specialist chemistries, are much more attractive to Inobat.
Importantly, the company is predominately using Lithium-Nickel-Manganese-Cobalt-Oxide (NMC) battery chemistry, mainly in pouch cell* and prismatic formats. Wight said the company would continue to work with these and several other cell formats as well as a variety of chemistries, as, he said, …. “having the right chemistry in the right format for the right market sector, which can be modified and customised very quickly and effectively, is very important to us.”
This matches the founding philosphy and vision of Bocek, which is producing bespoke products that match exactly the range, use cycle, energy density and charging time requirements of the battery’s application. By offering highly customisable batteries has meant that the company has already built up interest from a broad base of sectors with an increasingly growing customer base.
As Wight mentioned, ultimately the genesis behind the company is that InoBat spotted the under-supply of consistently high-quality batteries. Battery demand, he said, in general has now subsequently overtaken manufacturing capability, with the large volume cell suppliers taking up long-term contracts with the big automotive players in the industry. Subsequently, his task and focus is building customer relationships with the ‘smaller volume’ battery suppliers and OE specialty manufacturers, which include, for instance, commercial vehicles as well as segments of the aerospace industry, high-performance automotive and off-highway vehicles. His team works hand in hand with the Inobat R&D team, led by Doug McAndrew (CTO), which develop the chemistries for lithium-ion cells in these underserved markets.
Iain Wight, InoBat’s Chief Commercial Officer
Investments
With its strongly focus target market and vision, the company hasn’t been short of capital investment from both public and private entities. The first backer was of course the founder, Marian Bocek, and his IPM Group asset management company. Following this, one of the earliest stakeholders was the mining giant, Rio Tinto, which in July 2021 committed USD2.4 billion to multiple projects including the development of InoBat’s 290,000ft² battery R&D centre and pilot line in Voderady, Slovakia, where it is currently integrating research and development activities together with a pilot line for battery cell manufacturing. Chinese battery component manufacturer, Wuxi Lead Intelligent Equipment Co. Ltd, is responsible for the design, manufacturing, and assembly of the pilot production line in Voderady. It is currently being shipped from China, Wight said, and that Inobat is aiming to produce its first battery cells in late March / April, 2023.
The next phase of the company’s plan, once the pilot production line in Voderady is successfully in operation, is to scale up manufacturing capacities through the rollout of several planned battery cell gigafactories in different world regions, the proposed locations of which are reported later in this article.
Also in 2021, electrification technology company, Ideanomics Inc** of New York City, USA, invested an unspecified amount of capital to continue the development of InoBat’s R&D centre and pilot battery plant in Slovakia. One of the battery cell gigafactories is planned in the USA with Ideanomics being a primary partner and customer - see below.
Another 2021 investor was India's largest automotive battery manufacturer, The Amara Raja Group of Tirupati, which announced a EUR10 million investment in InoBat.
Gigafactories require not only large amounts of capital but also permits, licenses and business support thus government assistance is paramount. The European Union (EU) is providing some of this support to Inobat, classifying InoBat as being a company contributing to Important Projects of Common European Interest (“IPCEI”). Furthermore, a Joint Development Agreement (JDA) was signed with the International Finance Corporation (IFC), part of the World Bank Group, forming part of its development programme to expand the world’s transition to zero-emission transportation. By using these public funds as well as the private investments from Ideanomics, Rio Tinto and Amara Raja and leveraging the company’s relationships in Europe and Asia, these investors believe that InoBat will consistently produce high-end batteries at scale by 2025.
Infrastructure Projects
InoBat’s Slovakian battery cell plant will form the centre of its operations and at full capacity will employ about 150 staff. It will become the focal point of a global network of gigafactories based on its “cradle-to-cradle” value chain, which integrates chemistry research, cell development, battery production and material recycling. During the interview, Rimmington stated that the pilot factory would boast an initial 45-megawatt annual capacity, focusing on customer development work, sample cells and cell design, which all form part of the industrialisation project.
Having already established a Serbian subsidiary in 2022, the company announced it has signed a declaration of intent with the Serbian government to build a gigafactory for manufacturing and recycling of battery cells in Serbia. At present, while there are no concrete plans in place, aside from financial support, the agreement with the Serbian government includes assistance in finding land to build the facility and securing the necessary permits/licenses required for construction and operation. Since January 2023, the aforementioned International Finance Corporation has been supporting early-stage project development there, as part of its green energy fund.
Later in 2022, InoBat announced plans to build another battery cell R&D and production facility in Indiana, USA. The plan is supported by one of InoBat’s investors, Ideanomics, as well as the State of Indiana itself. The three-phase plan in Indiana will begin with the opening of an R&D and production facility boasting an initial annual production capacity of 100MWh. Once this project is tried and tested, the next step is to build a full commercial-scale battery assembly plant with an initial production capacity of 2-3GWh. Thereafter it plans to construct a major tailor-made battery cell production plant with a capacity of 4GWh, once the necessary financing is in place. Rimmington concluded that Ideanomics would play a role in this project, potentially developing the module and pack capability in the future. Currently, the project is still in the development stage having received capital from investors. Rimmington indicated that the production facilities in Indiana and Serbia are therefore in development, with another gigafactory planned in Western Europe (UK or Spain), giving it a presence in Eastern and Western Europe as well as North America.
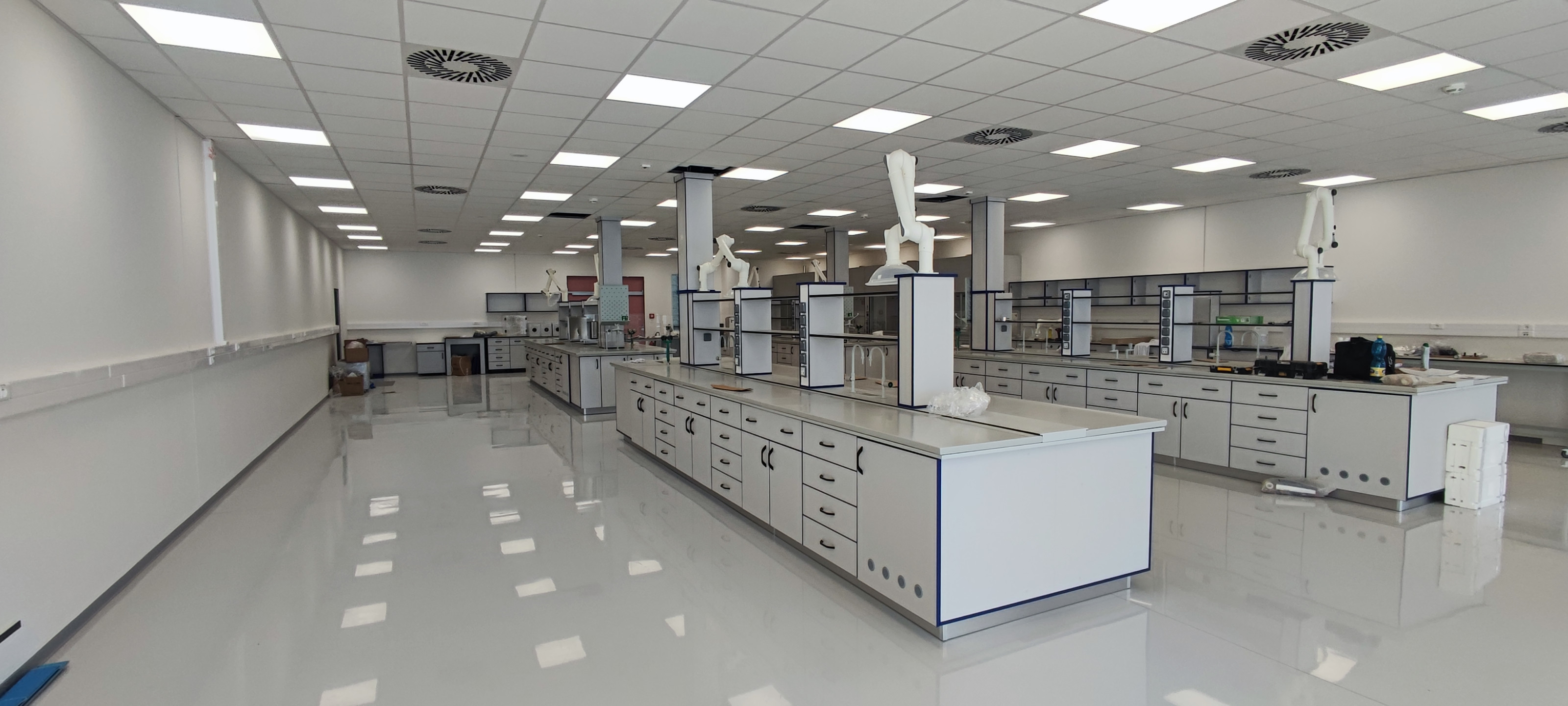
Inside InoBat’s Voderady Plant
Strategic Partnerships
Throughout the last few years, Rimmington spoke of the importance of building up an ecosystem of energy suppliers, investors, recycling and manufacturing capability in order to develop a sustainable value chain capable of producing products at scale. This was signified through a collaboration with London-based lithium refiner and battery recycling company, Green Lithium Refining Ltd in 2022. The partnership will see Green Lithium supply InoBat with battery-grade lithium chemicals, allowing the company to produce battery cells. The partnership has also seen the companies work together with the relevant government authorities in the UK and EU to achieve their respective strategic business goals, by developing a network of gigafactories across Western Europe in the coming years. Green energy will be used to power these manufacturing plants, supplied by UK energy supplier, Scottish Power, a subsidiary of Spanish energy giant, Iberdrola.
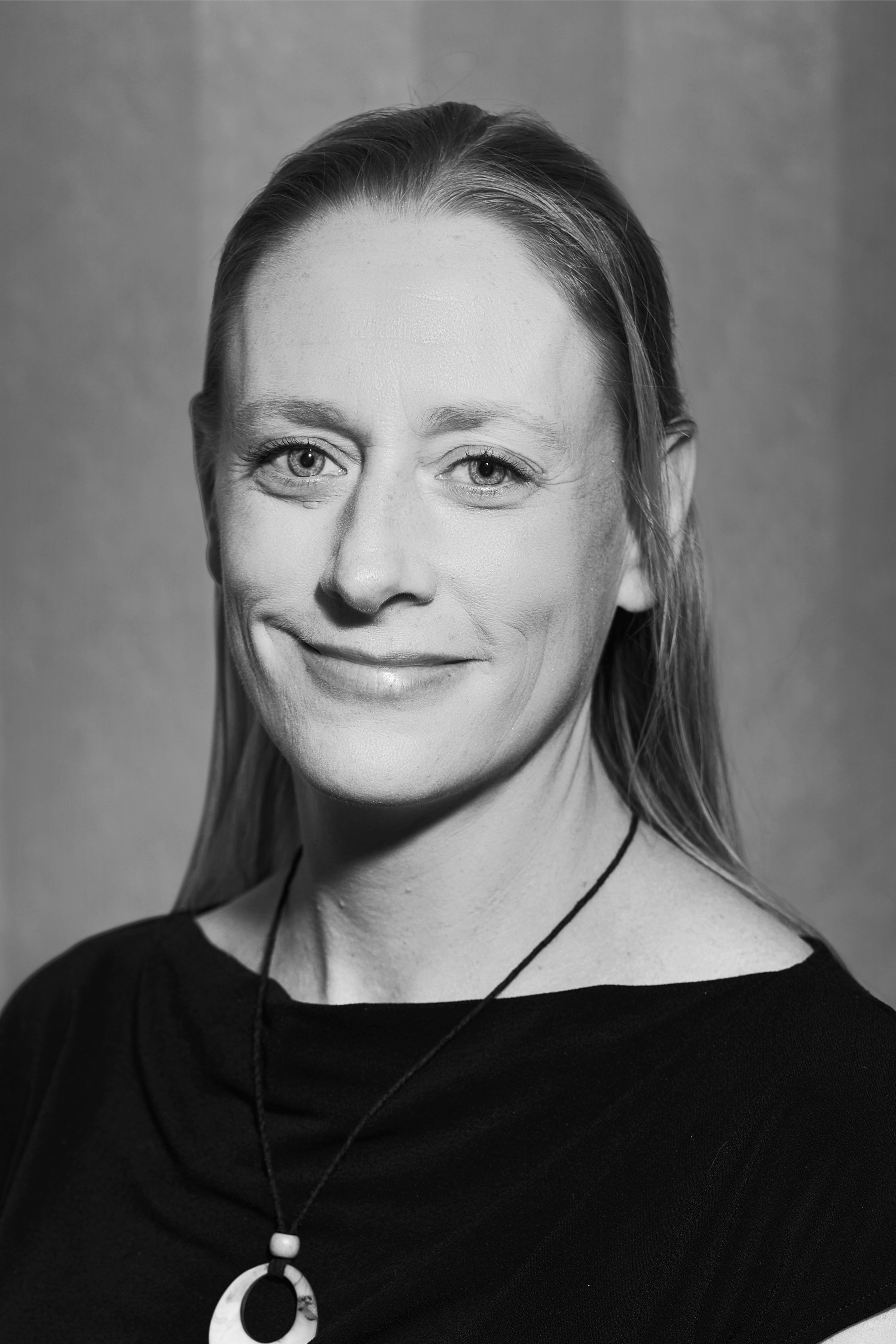
Nicola Rimmington, Director of Strategy Development at InoBat
Supply Agreements
As the company’s immediate focus is on producing battery cells, supply agreements with battery manufacturers are essential for business development. While it is not named many business partners, one company it is working in partnership with is Polish battery manufacturer, Impact Clean Power Technology SA of Warsaw. The two companies are working closely together to provide an unnamed European bus manufacturer with battery systems. InoBat will supply Impact with the cells needed to build battery packs for its customer. The high-voltage battery systems will be manufactured at Impact’s gigafactory in Poland.
Wight spoke of the necessity of using contract manufacturers such as GUS Technology LLP, which will produce battery packs at GUS’s headquarters in Taiwan, to fulfil the demand for InoBat battery orders ahead of reaching full capacity at its own production facility in Voderady. This agreement also supports InoBat’s ambitious growth strategy in the Asian battery market. Commencing in Q1 2023, InoBat is planning to welcome GUS staff to its production facility in Slovakia as part of a knowledge-sharing programme.
Battery Recycling and Sustainability
During the interview, Rimmington spoke of the importance of modern-day ESG*** ratings in setting up a company of this size. This encompasses environmental, sustainability, carbon footprints and lifelong assessments with the European battery directive requiring by law a minimum threshold of battery recycling. Rimmington affirmed that the company has reached a key milestone in battery recycling, with help from its recycling partners, including Gigamine Ltd. InoBat has used cell optimisation and design mechanisms to prove that recovered active cathode material from end-of-life batteries can be used in the production of new ones. She added that the batteries produced from recycled materials perform in line with new products made from virgin material. Reducing environmental impact through the re-utilisation of critical materials in the manufacturing and operating processes is therefore a key component of the cradle-to-cradle approach.
2023 and beyond
The future looks bright for this start-up as Wight said by the end of 2023, “we aim to produce cells out of our pilot line {in Voderady, Slovakia}, continue to develop our chemistry out of that and continue to utilise our pilot line. We need to maximise every opportunity we have with contract manufacturers. Finally, we have to break ground on the gigafactory which is directly beside the pilot line.” Through these multiple strategic investments, supply agreements, strategic partnerships and the development of the gigafactories, we could slowly see InoBat rival the major industry players in the near future.
After only three years, the company has developed its intellectual property behind the battery chemistry, developed battery cells, tested them and had them manufactured. The first factory in Slovakia has been built, with the pilot line being commissioned from March this year, which will then see, over the coming months, InoBat start producing their own battery cells with the possibility of supplying a battery module in the future. In the meantime, they are working with the integrators who design the battery and supply it to OEMs who will subsequently build it into their vehicles.
Commenting on the company’s progress, Marian Bocek, said:
At the heart of our success is InoBat’s truly differentiated approach to produce tailor-made EV battery solutions, understanding that no two customer’s needs are alike. We develop our products first before scaling up our manufacturing capability. With tailor-made products for key customers under our belt, supported by an excellent R&D and operational team, we have all we need to succeed and will continue to drive forward on our journey to become a leading player in green mobility.
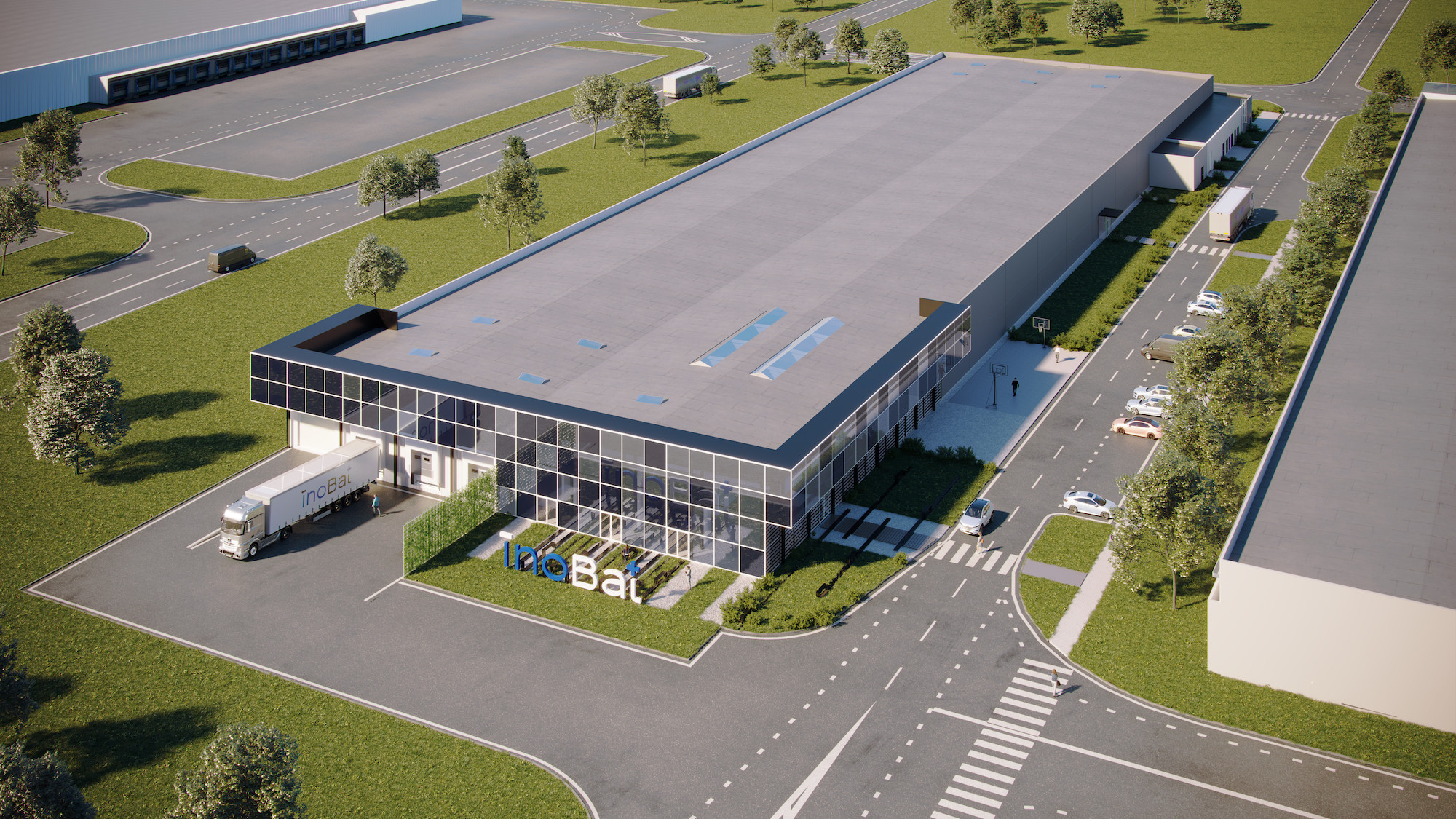
A rendering of what the finished Voderady plant will look like
* A pouch cell is a soft battery design where most of the cell components are enclosed in an aluminium-coated plastic film
** Ideanomics Inc is a global provider of electric mobility solutions, with subsidiaries across vehicle manufacturing, component production, and zero-emission infrastructure. These include: Energica - manufacturing electric motorcycles, Silk EV - producing luxury electric vehicles, Solectrac - manufacturing zero-emission agricultural tractors - Treeletrik, providing electric scooters, US Hybrid - developing powertrain components for electric, hybrid, and fuel cell, WAVE - offering charging infrastructure for mass transit, ports, and warehouses.
***An ESG rating measures a company's resilience to long-term environmental, social, and governance risks. Issues such as energy efficiency, worker safety, and board independence certainly have financial implications, but they are often underrated during traditional financial reviews.