Three of a kind: an interview with electric compressor manufacturer TCCI
By Bradley Osborne - 18th April 2023
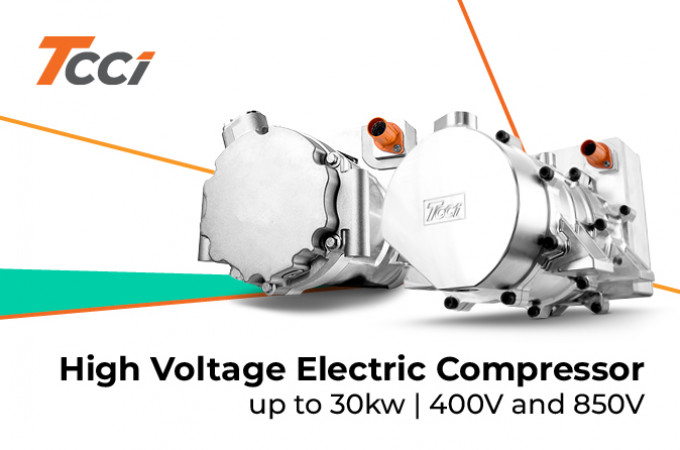
This month, T&BB spoke to Richard and Kara Demirjian of TCCI – a manufacturer of commercial vehicle compressors based in Decatur, Illinois – about its EV Innovation Hub: a veritable “triple threat” with an EV components production line, a climatic testing centre, and a training academy rolled into one facility, which it is developing as part of a public-private partnership with the state and local schools.
USA – In the latter part of the twentieth century and the early part of the twenty-first, the USA was not a good place to open a new factory. Rising costs at home and competition from abroad decimated American industry, and those manufacturers who managed to survive through multiple economic downturns decided to invest elsewhere, where labour and other expenses were cheaper. Nowhere was hit harder, perhaps, than the “Rust Belt”, an unflattering name for the northeast and midwestern states which straddle the Great Lakes. The region has acquired the name because it is dotted with the skeletal remains of factories which were once the motors of the American industrial machine but which have now fallen into disuse and decay.
TCCI Manufacturing, a company which has managed to keep its manufacturing facility in the city of Decatur, Illinois running for the past 35 years through various economic crises, was no exception to the general trend. The company took the decision in 2006 to expand into China, where labour costs were lower; and in 2018, it opened another factory in India. But when the COVID-19 pandemic exposed to the world just how overextended and volatile global supply chains have become, TCCI decided to take a closer look at the cost-benefit of regional localized manufacturing in addition to expanding its facilities abroad. With rising logistics and supply chain costs, “it just made sense,” according to Kara Demirjian, to seriously consider if it would be better to invest at home rather than abroad “for our market”. Conditions were ripe to “localise globalisation” – a straight reversal of the trend which has obtained since the 1980s.
Indeed, the past few years have seen the U.S. government engage in a strident campaign to bring heavy manufacturing back to the states. For the commercial vehicle industry in particular, this has meant a USD7.5bn cash injection between 2023 and 2028 into existing Federal Transit Administration programmes which seek to incentivise electric vehicle production and sales in the USA. The money will support state-level initiatives to replace diesel buses with electric ones, and other funds have been provided by state governments to pay for research and development of zero-emission trucks as well as buses.
As a supplier of electric compressors for new zero-emission vehicles, TCCI stands to benefit greatly from the industry’s shift to electric drivelines. It is also a beneficiary of a partnership with City of Decatur and Richland Community College who received state funding, announced last September, to create a public – private partnership with TCCI Manufacturing which included a new EV Component Manufacturing Facility to produce Made-In-America products. But TCCI’s ambitions for an EV Innovation Hub in Decatur are much bigger than that. What it plans is a cutting-edge centre for electric vehicle research, a testing lab for commercial vehicles and agricultural and construction machinery, as well as a training academy to teach local students in electric automotive engineering. It would be a factory, test centre and school rolled into one.
Within a matter of a few months, TCCI will break ground on an expanded manufacturing facility and a space which it calls the ‘Climatic Center for Innovation and Research’ (CCIR). Production is slated to begin in the second or third quarter of next year, and the academy’s first class is set to come through in the autumn of the same year.
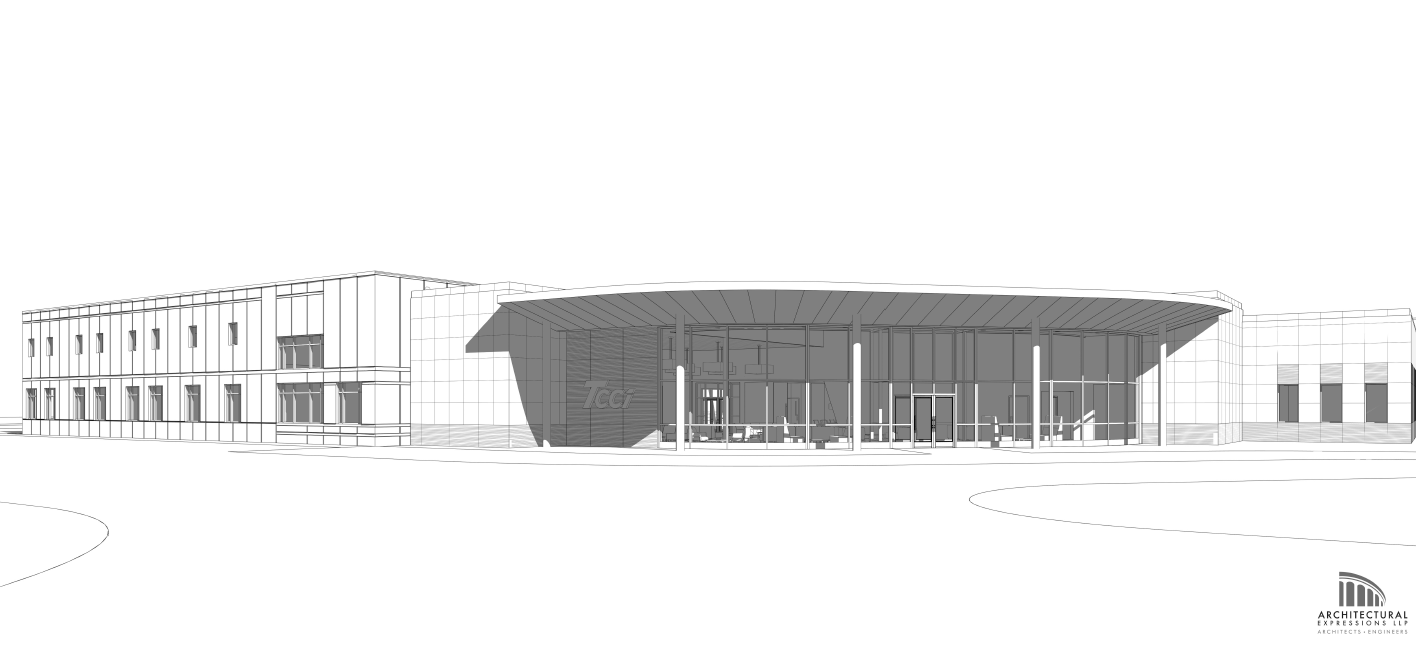
Render of TCCI EV Innovation Hub
Background to TCCI and its product range
The letters ‘TCCI’, which stand for ‘Tillotson Climate Control Inc’, tell the story of how the company came to be in the late 1980s. The business started as, and remains, a family company, going back to Gerald Demirjian, who was an executive at the former ‘BorgWarner Corporation’. BorgWarner Corp underwent a series of upheavals and transactions which eventually gave birth to the BorgWarner Inc which is active today. In that time, Demirjian bought out Tillotson, a maker of carburettors and a wholly owned subsidiary of BorgWarner Corp, and he acquired BorgWarner’s compressor business, which supplied to automotive firms such as Ford. Tillotson, which now makes carburettors for high-end racing karts, is still run by another Demirjian out in Tralee, Ireland, whereas TCCI took over the compressors and began supplying to commercial vehicle makers such as Freightliner, Navistar and Kenworth in the 1990s. These belt-driven, two-cylinder compressors are still made in Decatur and can be found powering air-conditioning in trucks by Volvo/Mack and Freightliner/Western Star and refrigeration units by Thermo King.
When TCCI got started, compressors on the market from Sanden, Valeo, Mahle, and Denso were made primarily for passenger cars. These were being installed in commercial vehicles as well – not taking account of the fact that CV applications bring tougher demands and therefore require more robust components. According to Richard Demirjian, TCCI has carved out a share of the global market for compressors because it chose to specialise in high-quality products that can withstand the demanding conditions of heavy-duty transportation. For the same reason, TCCI has become a major supplier to agricultural and construction vehicle manufacturers such as Caterpillar and CNH Industrial, whose need for robust components is even greater.
TCCI has tended to thrive in conditions which have proven deadly to other manufacturers. The company was born out of BorgWarner Corp’s crisis in the 1980s, and in 2008, it found that its business picked up even while it rapidly tailed off for others. “When things are going gangbusters, and the commercial [vehicle] industry is booming,” Richard explained, “nobody has any time other than to put those vehicles out.” However, when business slows down, the OEMs look to make cuts wherever they can, including warranty costs, and that’s when TCCI really “[gets to] shine and show the benefits of our product and pick up market share.” Automotive compressors from TCCI’s competitors, while perfectly serviceable, had become less and less durable due to cost-cutting design measures over the years. As a result, they couldn’t hack the demands of CV applications quite as well, and TCCI found that OEMs turned to its more robust compressors because they were less likely to fail and to cost them further down the line.
In the 2000s, TCCI decided to open a manufacturing facility in the city of Ningbo in Zhejiang, China, and it diversified its range with products such as wobble plate compressors for low horsepower applications and swash plate compressors for the toughest conditions. Moreover, it hired key personnel from competitors Sanden and Denso and tasked them with expanding TCCI’s portfolio and developing new products and technologies to improve compressor performance and durability. With these moves, TCCI was able to cut costs, improve its products, and grow its market share in spite of the economic recession. Between 2006 and 2015, the company reportedly went from “almost zero market share” to “the dominant player in almost every category.”
The lean times for vehicle manufacturing, however, are over, and the current boom in electric vehicles could very well upset TCCI’s market standing. As such, the company has been working quickly to adapt to the new order of things. Its presence in Europe – where the industry is “way ahead of the U.S.” – gave TCCI the foresight over two years ago to start developing 850-volt compressors, anticipating the switch in EVs from 400 volts to bring down charging times. Nevertheless, making the transition to fully electric compressors has been a “huge learning curve”, Richard claimed. In 2018, TCCI enlisted the aid of a technical expert from General Motors, specializing in compressors, A/C, and heat pumps for ICE and battery electric vehicles. He now heads advanced engineering for TCCI globally and has built up a team for the design and development of TCCI’s new compressors, which Kara claims is “paving the way for the industry providing the largest range of electric compressors in the market”.
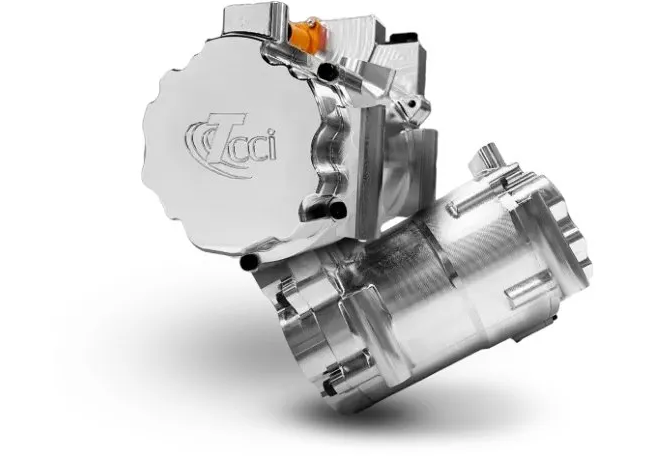
Electric compressors by TCCI
The old compressor is “a pretty straightforward product”. It is belt-driven and has a clutch which draws on the engine for the power. An electric compressor, on the other hand, is more complex and has a greater role to play in an electric vehicle. In addition to the conventional pumping mechanism, the new compressor has its own motor, inverter, and control unit inside of it as well. And along with the previous HVAC functions served by the old type of compressor, the new compressor must also maintain an optimum temperature for the electric powertrain, and especially the batteries.
TCCI showed its latest electric compressors at IAA Transportation in Hanover last September. The models shown were the 850-volt, 34cc, 46cc, 60cc, and 120cc compressors, with power ratings up to 29 kW. The product specs for the 60cc and 120cc mean that only a single unit would be required to cool both the driver cabin and the battery packs, eliminating the need to run several compressors in parallel. When asked about which companies were working with TCCI to test out and fine tune the product, Richard named Navistar and the Traton Group and alluded to “lots of start-up companies” who have recently entered the EV space.
The Climatic Center for Innovation and Research
Making a durable and powerful compressor is all well and good, but it is not guaranteed to be a good fit for an electric vehicle. The Climatic Center will enable TCCI to bring testing of the new compressors “back to the whole vehicle”.
When it is built, the CCIR will have a climatic chamber with a full vehicle mount capable of accommodating a vehicle over 60 feet, or roughly 20 metres, in length, and with a width of around 25 feet (between 7 and 8 metres). It will be more than big enough to comfortably fit a tractor unit or a large coach or bus in it. Richard couldn’t say what the maximum floor weight will be: it will depend on whether TCCI installs a roller dyno, or another type of chassis dynamometer. The tunnel will also feature a solar array and ambient temperatures as low as minus 40 degrees and as high as 55 degrees Celsius. A DC charger in the chamber will enable TCCI to test the effects of fast charging on the vehicle as well. Using these facilities, TCCI and its customers will be able to test the HVAC and refrigeration systems in prototype electric vehicles and assess their affect on battery health in highly-controlled conditions.
The Climatic Centre will replace a facility located in another part of Decatur which TCCI decommissioned five or six years ago. When it closed the old centre, TCCI moved its system benches and shakers to its main site and expanded its testing capabilities. Reviving the Climatic Centre, however, is a much bigger task. It will involve redeveloping a large portion of the existing building that was originally built in the 1940s to make parts for Sherman tanks serving in the Second World War. The old structure has an unstable roof and wooden trusses dating back 80 years. TCCI will tear the old fabric down and rebuild a new structure to house the new facility.
The choice to redevelop the Decatur site was not an inevitable one. “We could have chosen anywhere,” Kara said, pointing to the company’s facility in China, where TCCI was already making electric compressors, and the India location, which was also “well positioned” to duplicate production lines and expand operations. But when the COVID-19 pandemic overturned the former ways of doing business, she and Richard sat down and discussed the possibility of building the entire EV Innovation Hub in the U.S. instead. The high cost of doing so, however, would potentially sink any such plan. The two decided to look at what incentives were on offer in Illinois as well as in other states which might provide some financial assistance in bringing the facility to the states. In the end, looking “holistically… at infrastructure” and “business partnerships” as well as tax breaks available in the state, TCCI chose Illinois.
Kara worked with Governor JB Pritzker for financial support and was awarded as the first company in Illinois to receive REV Incentive program for the Company’s capital investment and commitment to job retention and creation. She also forged partnerships with the City of Decatur and the local community college, Richland Community College, which led to a partnership grant through Rebuild Illinois. The partnership also creates research and stem pathway programs with several public higher education institutions throughout the State of Illinois. The University of Illinois Urbana-Champaign, the state’s flagship institution for higher education, is ranked as a world leader in engineering. Other schools which TCCI is now partnered with include Northern Illinois University and the University of Illinois Springfield. The new facility at TCCI will include an EV Workforce Training Academy to train students in electric automotive engineering. The EV Training Academy, which will open alongside the new production line and the CCIR next year, will effectively be new model for workforce development with a community college onsite at TCCI. Kara elaborated:
It’ll be an immersive opportunity for students from all over the state to come to the EV training academy to get trained across advanced manufacturing, computer science engineering, which we know there’s a gap globally in our software development technology and the workforce in green jobs related to that.
Although the proposition to establish a new production line for EV components in Illinois was appealing enough on its own, Kara stressed that it was the combination of this, the CCIR and the Academy which firmly sold the idea of a public-private partnership. As a result, TCCI received the state’s first ‘Reimagining Electric Vehicles in Illinois’ tax incentive award last September with their capital investment of USD20m. Additionally, the state granted USD15.3m to Richland Community College and USD6m to the City of Decatur, who will work side-by-side with TCCI to develop the site. Once completed, the “three-tiered” facility will be open to industry, students, and higher education institutions to deliver “research, degree-based programs, certifications, stackable credentials and industry partner apprenticeships”.
The future of CV manufacturing in the Midwest
The past couple of years have been unusual for both Richard and Kara. “Who knew I’d be building curriculum?” Kara said, in reference to the company’s partnerships with academia. EV tech is imposing new demands on manufacturers, and apprentice and veteran engineers alike will need to adapt. “Our electrical guys used to work by themselves and so did the mechanical guys”, Richard commented,
and now you’ve got the whole team working together on how do we improve the efficiency and use less power to achieve the same output […] I think you’re going to see a closer working together of [mechanical, electrical and software engineers], especially the software and the hardware.
It is therefore crucial that engineers being trained up today receive an education that incorporates all aspects of electric vehicle design. No longer merely a pumping mechanism, the new compressor is an electrical system with computational power. Richard stressed the growing importance of cybersecurity, a wholly new domain for the company: the compressor is “on the main CAN-BUS line of the vehicle, so we have to be able to not have our software hacked into.”
Big changes are afoot at TCCI, then; but Richard and Kara pointed to other developments in the Midwest, too. Collaborations are happening across the region’s top engineering schools, which include the University of Illinois, University of Michigan, and Purdue University. Vehicle manufacturers are starting to come back to the Midwest to make investments, and naturally the Tier-1 suppliers are following suit. It is a far cry from fifteen years ago when, as Richard recalled, you could drive down the centre of Detroit and find only shuttered businesses and workers laid off by the big automotive firms.
You go there now, and there’s exciting things happening there – parts of Detroit are booming.
Crises come in two forms. They can be negative, such as an economic recession, or they can be positive. The rise of electric vehicle manufacturing is a kind of “positive crisis”, a period of economic growth which is nonetheless dangerous for those companies who are slow to respond. So far, TCCI has proven it can outlast the negative crises; with the redevelopment of its Illinois facility, it aims to show that it can survive the positive ones, too.
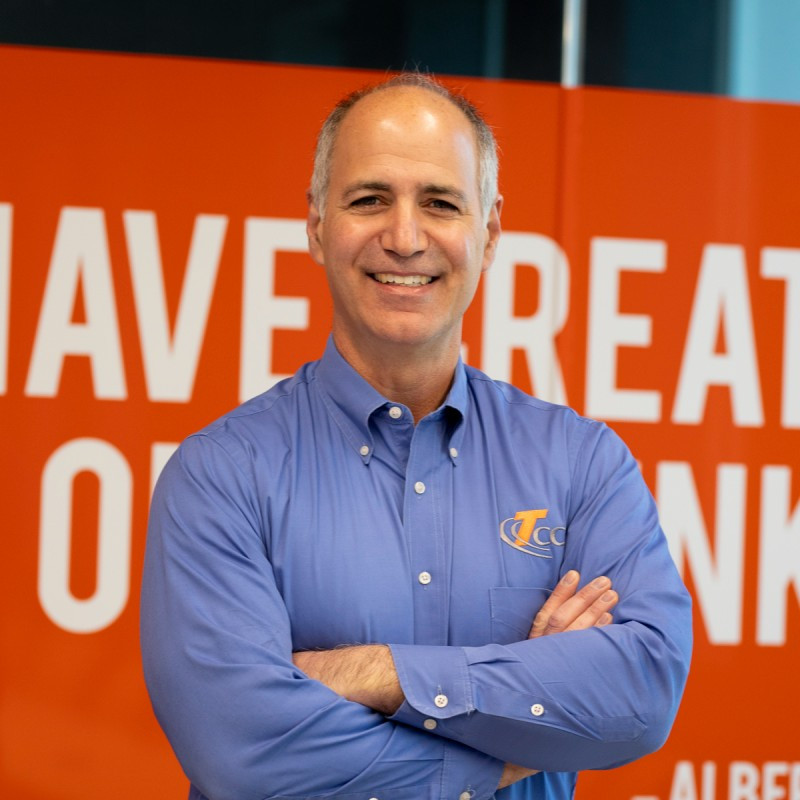
Richard Demirjian, President of TCCI, has served the company for over 35 years. He oversaw the transformation of the business in the past two decades, which saw a 300%+ growth in sales, following the expansion of manufacturing to six countries and the launch of 20 new products and technologies in the past 5 years. He is a graduate of the University of Illinois, Urbana-Champaign.
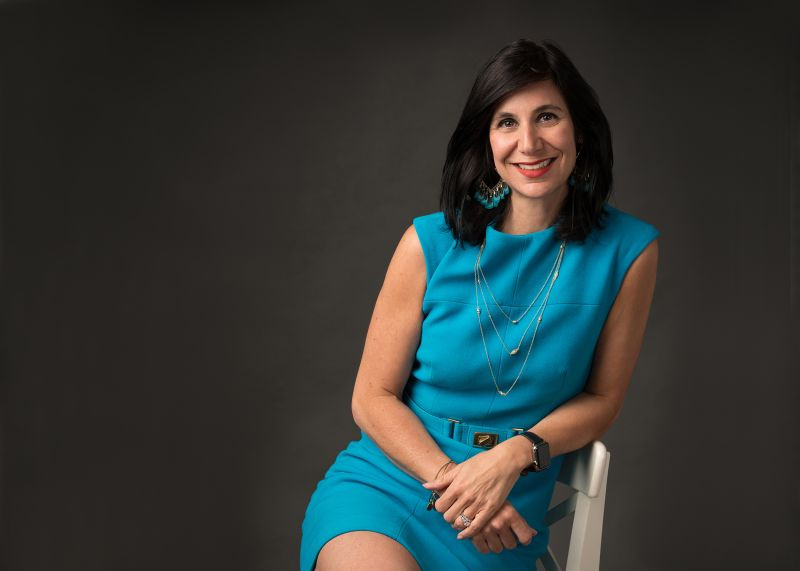
Kara Demirjian Huss is Vice President of TCCI and is also President of DCC Marketing, an agency which she founded in 2000. She is responsible for the major strategic and communications for TCCI, having led the effort to receive the State of Illinois’ Reimagine Electric Vehicle Incentive. She is a graduate of the University of Illinois, Urbana-Champaign.