Use of 3-level topology inverter to boost electric motor efficiency in buses, says ABB
By Jim Gibbins - 8th January 2024
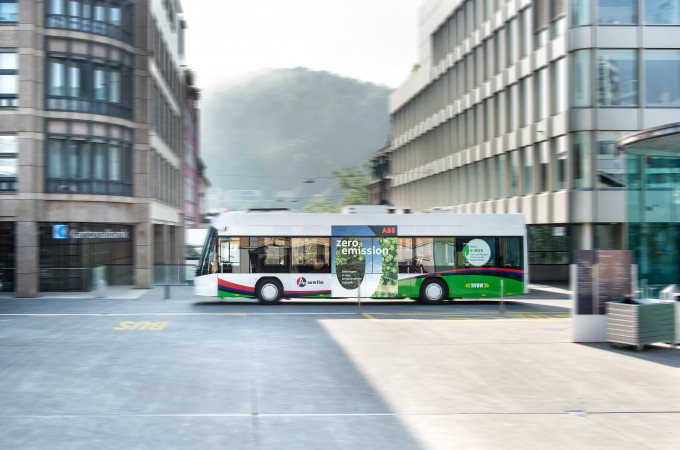
A bus in operation with ABB drive system
Switzerland – With the new 3-level topology inverter (HES580) set to come to market in mid-2024, David Segbers, eMobility Traction Product Manager at ABB in Turgi, Switzerland, provides T&BB with an explanation about what is a 3-level inverter and the benefits to come for the transit bus markets in Europe and elsewhere.
The power inverter (also known as a converter) is a key component in allowing bus operators to adopt electric vehicles to cut emissions and achieve net zero targets, writes Segbers.
It takes the direct current (DC) power from the battery and converts it to the alternating current (AC) that is required to drive the traction motors. It does this by using power electronics to switch between fixed voltage levels to create a sinusoidal output voltage
______________________________________________________
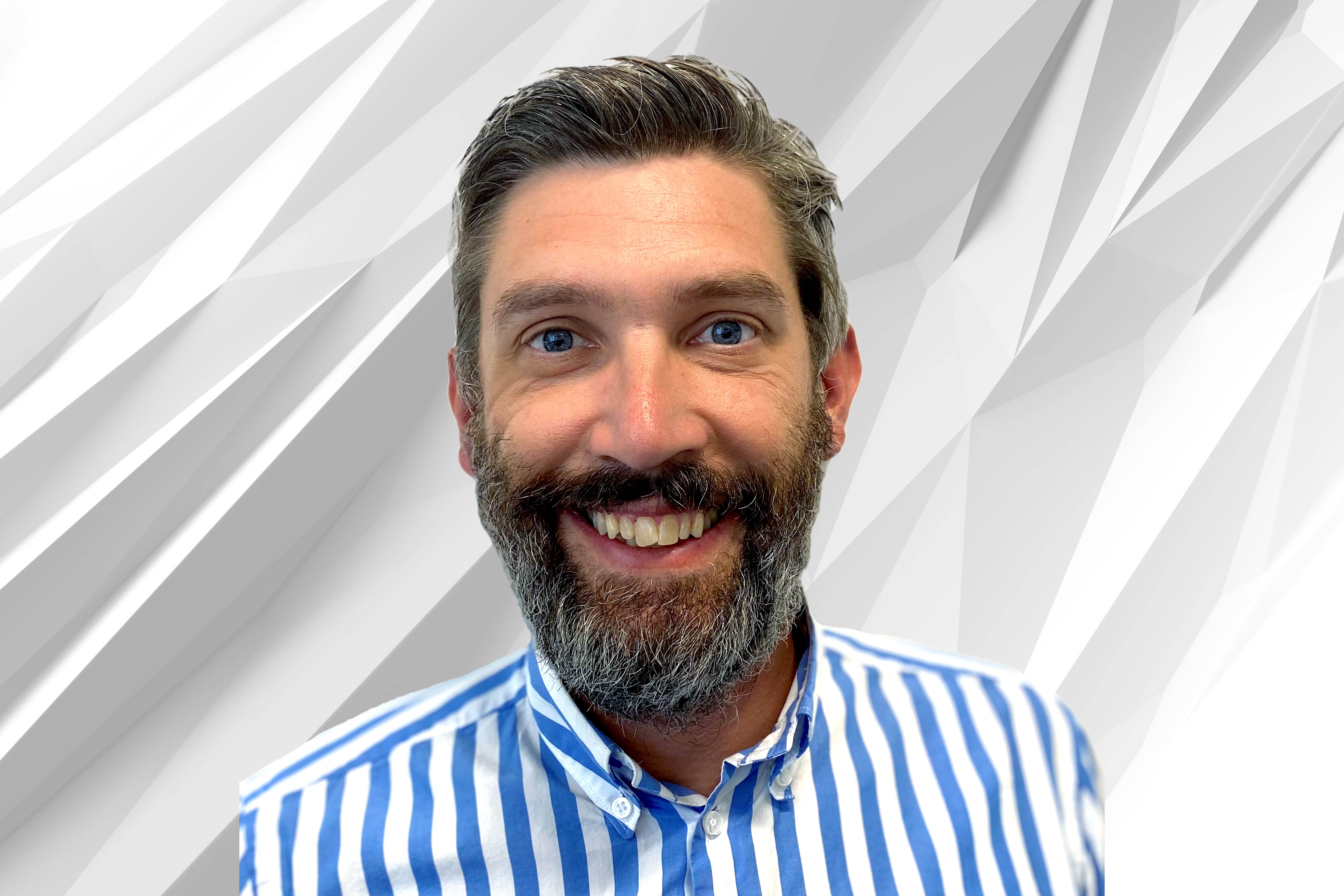
David Segbers is a Global Product Manager in ABB traction division and leads the Product Management team for Mobile ePower. In this role, David is responsible for the complete Mobile ePower Portfolio development such as Motors, Drives, Line Filters and Power Batteries. Furthermore, he leads the technical sales for key OEMS or complex system solutions.
Before joining ABB traction in 2015, he worked in sales and product management at an TIER1 automotive supplier and diesel engine manufacturer.
Segbers holds a Bachelor of Engineering (B.Eng.) in automotive Engineering of the DHBW Ravensburg and a Master of Engineering (M.Eng) in Product Management and International Sales Management of the Hochschule Konstanz.
Segbers was born 1981 and is a German citizen.
______________________________________________________
From 2-level to 3-level inverters
Using the diagram below, Segbers explains the difference between 2-level and 3-level inverters.
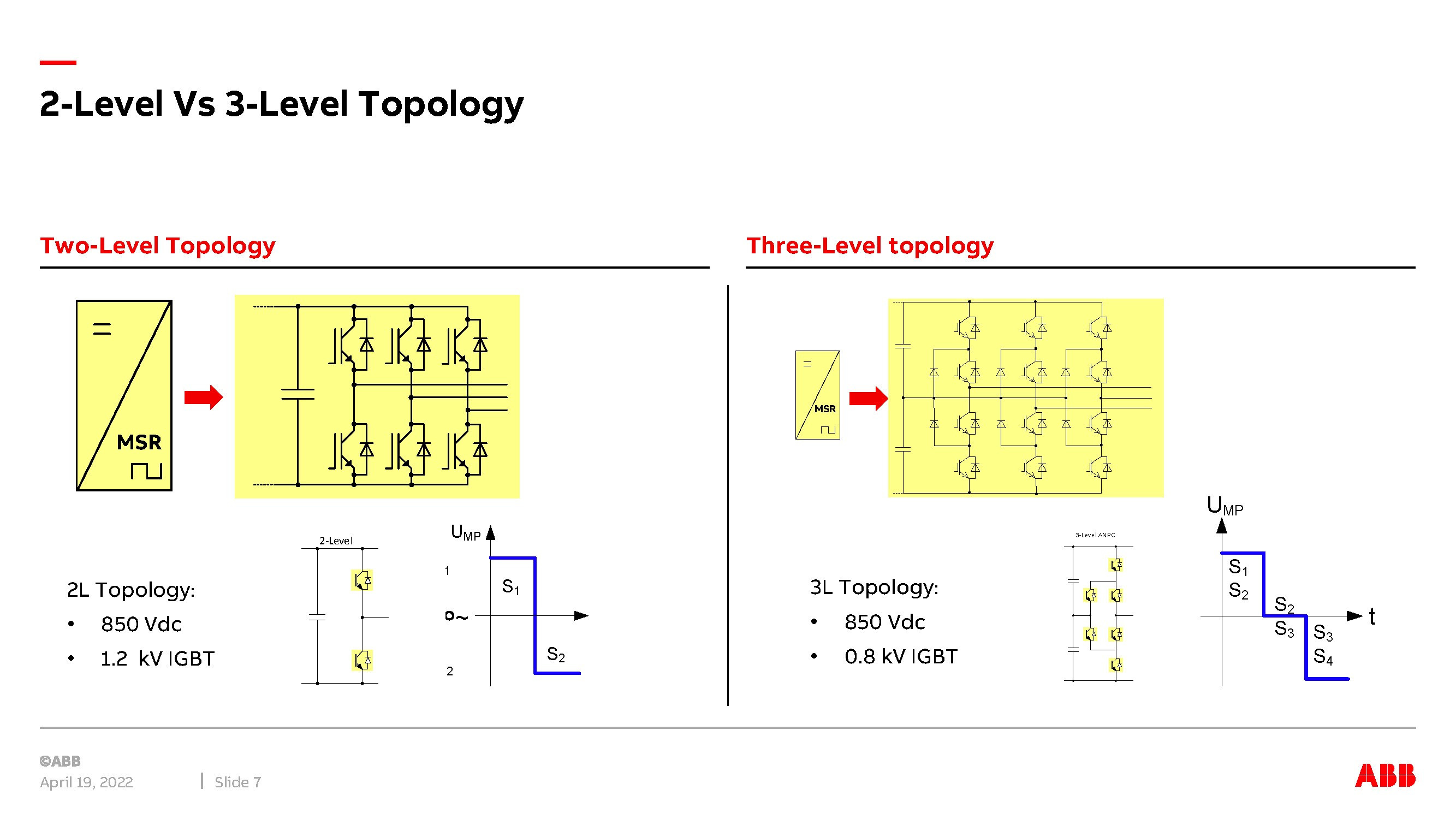
Caption: 2-Level v 3-Level Topology
A 2-level topology consists of IGBT (Insulated Gate Bipolar Transistors) semi-conductors in the invertor, which are made from different materials, the latest being silicon carbide, for example. With a 2-level (inverter) topology, the battery voltage switches between two levels, plus (+) and minus (-) at 850 Volt DC, which is the maximum battery voltage and for this, semi-conductors (IGBTs) of 1.2 Kilovolt (KV) class are needed.
In 3-level topology,” continued Segbers, “there are some more switches so that we can introduce a new level; it's an artificial neutral in between the two levels, enabling us to switch between plus (+) zero (0) and minus (-). This is why it has three levels, and this is why it is called three level topology.
Today, most electric buses, cars and heavy vehicles operate with 2-level inverters. These switch between positive and negative DC voltages to create an AC waveform. A side effect is that every time the inverter switches, it creates a voltage ripple. These ripples lead to harmonic effects that impact the efficiency, power output and reliability of motors, and the bigger the switching step, the larger the ripple and resulting harmonics.
When it comes to efficiency, electric motors experience losses from fundamental issues related to mechanics, resistance and magnetic effects. Motors on board buses and other vehicles are fed by inverters and experience losses due to harmonics.
Upgrading to a 3-level inverter will significantly reduce harmonic effects. These switch between positive, neutral and negative DC voltages. This halves the size of the switching steps and reduces the resulting current ripple.

Caption: 3-level advantages
In the case of a 2-level inverter, harmonic losses typically account for around 15-35 percent of the fundamental losses and therefore have a significant impact on overall efficiency. Using a 3-level inverter will decrease harmonic losses by up to 75 percent as it reduces the amount of energy that is lost to heat.
The 3-level inverter is more motor-friendly and saves energy and improves performance. It gives bus manufacturers the option to increase the power output from their existing motors for faster acceleration. Alternatively, they could use the conserved energy to extend the operational distance buses can travel, or they could downsize the battery system to cut capital costs.
One example is the HES580 drive that we introduced at Busworld as the most motor-friendly inverter. It provides a cleaner power supply for traction motors to give bus operators more control over reliability and running costs.
There are further benefits as harmonics also create stress in the windings of motors – so by reducing the harmonics, 3-level inverters also improve the lifetime and reliability of motors. The cool running also reduces the cooling requirements.
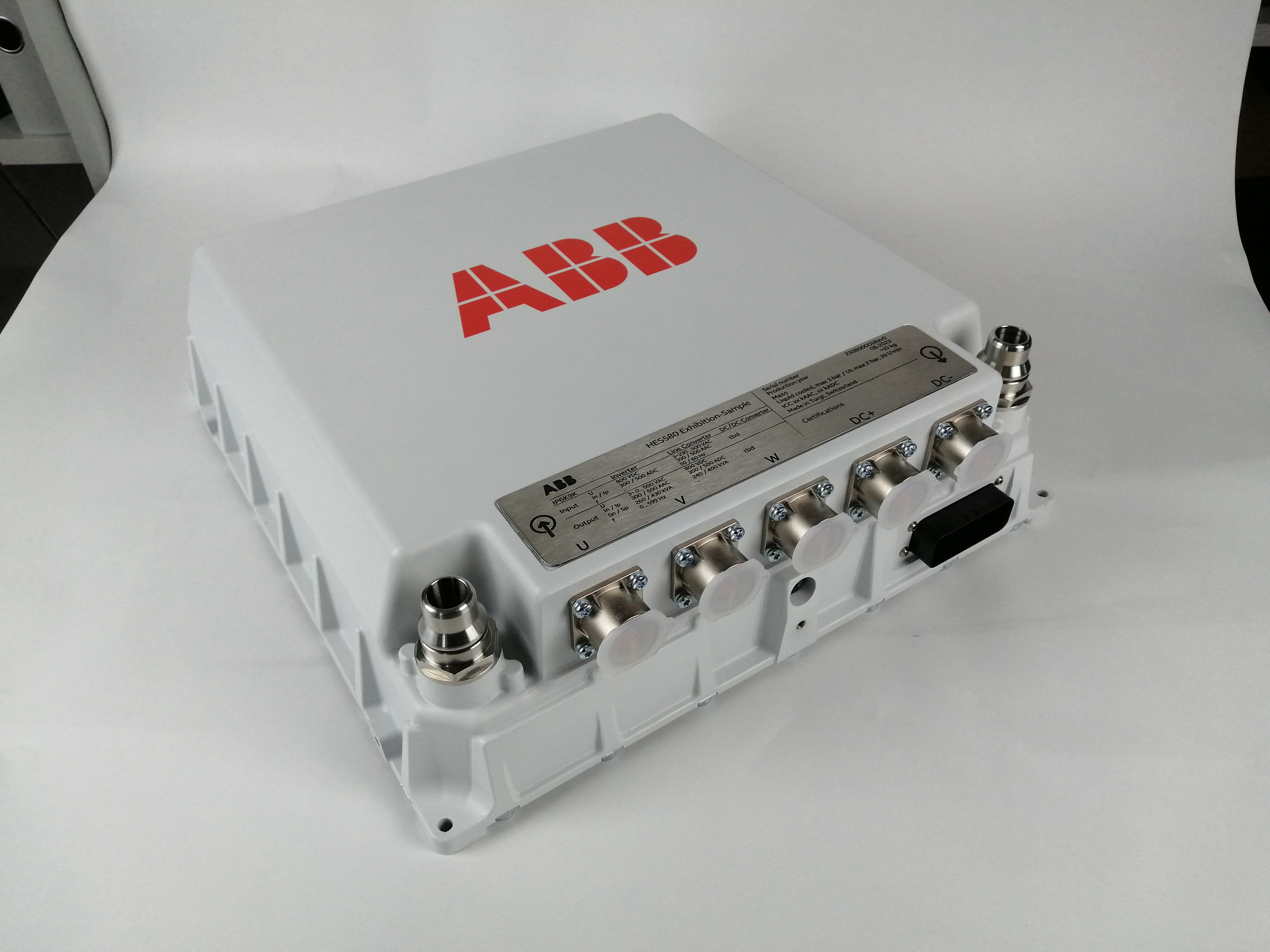
Caption: ABB HES580 3-Level inverter
Influence of inverter type on power output
The output torque illustrates the impact of inverter type on a motor. Datasheets typically show torque in relation to an ideal sinusoidal AC power supply. However, the harmonic effects will reduce the usable torque when supplying the same motor from an inverter.
In the example of a 45 kilowatt (kW) permanent magnet motor working at 3000 rpm, an AC power will result in the motor delivering torque of 180 Newton-metres (Nm). When a 2-level inverter is used, harmonic effects reduce the motor’s output to 80 Nm, a 65 percent reduction compared to the ideal AC feed. In comparison, a 3-level inverter reduces only reduces output to 130 Nm, a 28 percent drop. This shows how 3-level technology can significantly improve the output from a motor.
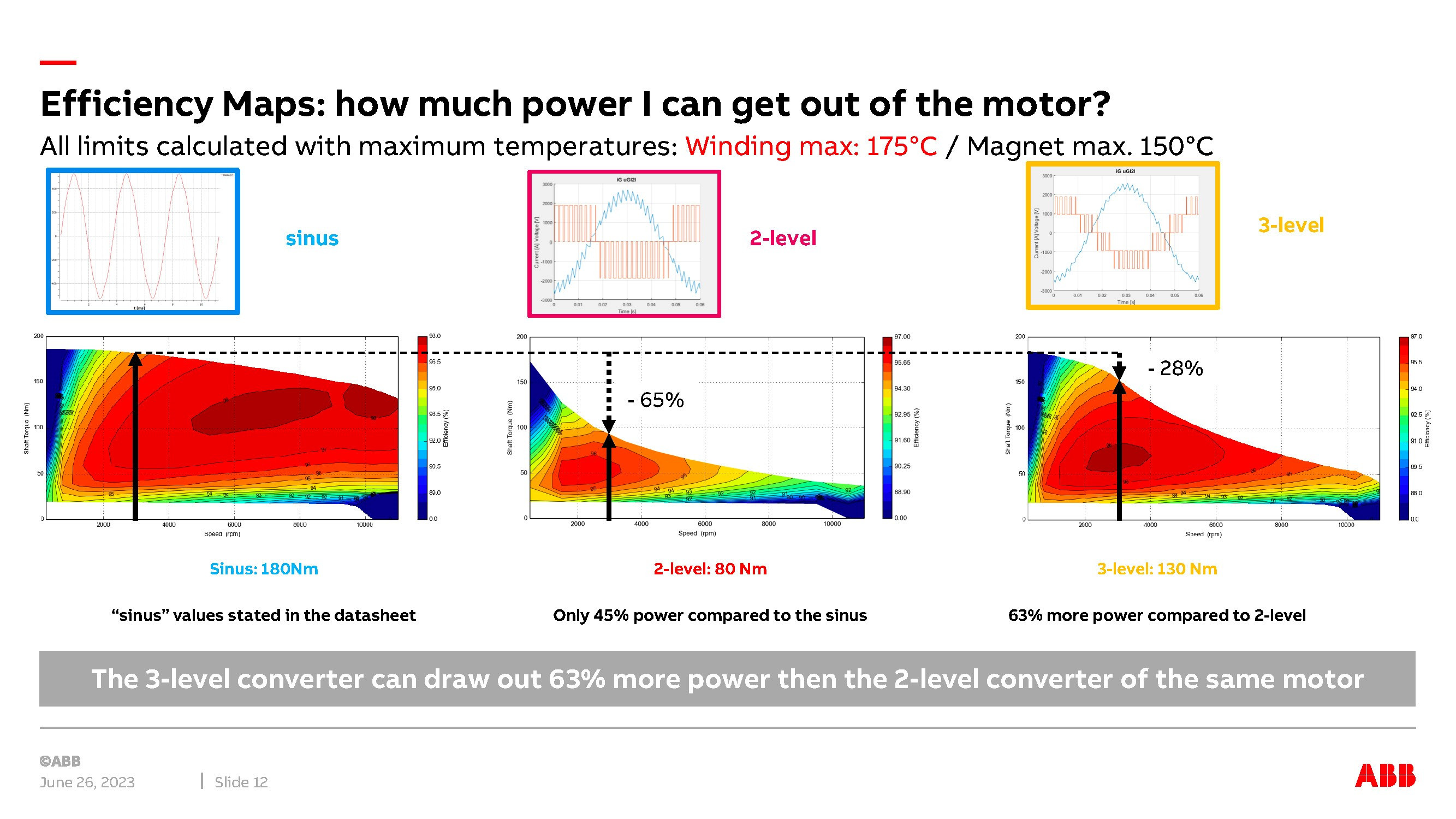
Caption: Influence of inverter type on motor efficiency
The effect is similar at every speed on a motor’s performance curve, making the 3-level inverter more efficient overall. However, it’s particularly pronounced at partial load conditions, where buses operate most frequently.
Design considerations when using 3-level inverters
Three-level inverters are larger and more complex than their 2-level counterparts, as they feature additional switching components that require more space. However, the efficiency gains allow for a strategic downsizing of other critical components, including motors and filters.
Moreover, the energy savings offered by 3-level inverters enable bus manufacturers to downsize their batteries or extend battery life. This can reduce charging times and achieve cost savings.
Considering silicon carbide semiconductors
An alternative to 3-level technology is to use inverters based on silicon carbide (SiC) semiconductors. These are capable of higher switching speeds and can emulate an AC sinusoidal waveform more closely than a silicon-based inverter to cut harmonic losses and improve efficiency. Another advantage of SiC inverters is that they are smaller compared with silicon invertors.
It may be worth considering using 2-level inverters based on SiC technology. However, the fast switching increases the stress on motor insulation. As a result, design engineers need to pay greater attention to cable length (distance of the inverter to electric motor) and electromagnetic compatibility.
On balance, 3-level silicon inverters are probably the best option today. They strike a good balance between energy efficiency, cost, and flexibility in terms of installation and motor selection.
Proven technology in rail
Three-level inverters are already used widely in electric rail, where they have demonstrated operational advantages. One example is on a line between the towns of Rhäzüns and Schiers in Switzerland, where two comparable trains operate – one with a 2-level inverter and the other with a 3-level inverter.
Both trains have a similar speed and profile along the line, but ABB found that one of the vehicles consumed 30 percent less energy. This was partly because of the 3-level inverter improving the energy efficiency of the drivetrain, and partly due to the train’s regenerative braking system.
Taking bus converters to the next level
In conclusion, 3-level inverters hold a lot of promise for buses. They offer potential to boost power from electric motors, improve energy efficiency at every operating point and reduce stress on motors so that bus operators can control budgets as well as emissions.
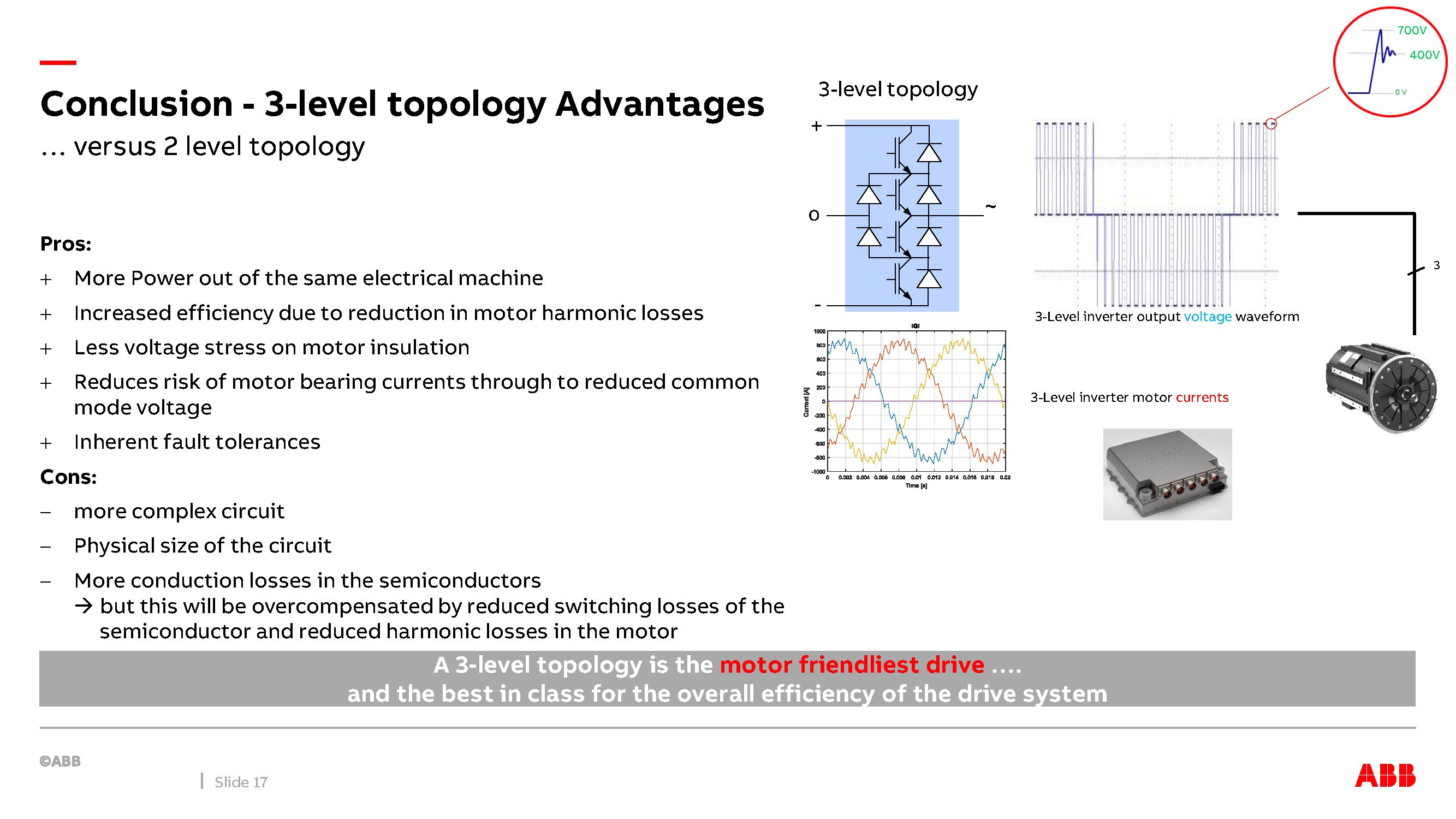
Caption: 3-level topology advantages versus 2-level topology
Outlook
ABB Traction is a supplier of traction motors and inverters primarily to the bus and rail OEM industry, and to date has supplied traction systems for installation in some 400 buses and trolleybuses. Batteries are also offered, but these tend to be offered when supplying trolleybuses. However, it does supply bus builders too: In Barden, Switzerland, for example, there is a bus line in operation with Hess-made buses that have flash fast charging using ABB batteries; at both ends of the line there are ABB pantograph-down fast charging stations, where the buses can be charged with 450kW.
Production of the new 3-level topology inverter starts in mid-2024, with the first application being in construction machines, but Segbers expects, next year the industry will also see a bus in operation with the new inverter technology. Segbers says ABB is in discussions with several European OEMs to realise this.
Direct drive applications will remain ABB’s focus for its traction drive systems. Bus and trolleybus OEMs in Europe remain its primary target market, as well as Turkey for the Turkish market but also for exporting to the markets of the Middle East and North Africa. In Europe we have a rather fragmented bus market with many local specialist OEMs in Italy and Spain, particularly, that are looking for flexible suppliers like ABB. At present, it has no business yet with the specialty truck segment, refuse collection vehicles or container tractor units, but it is involved with several tenders. Segbers, for the time being at least, rules out the USA because of the Buy America rules and in South America, the market tends to be a handful of big international chassis OEMs with few local independent producers, as well as the strong presence of the Chinese OEMs in the region.