Is fuel cell architecture the next step in the zero emissions road map for transit buses in North America? BAE Systems’ Greg Marx seems to think so
By Jim Gibbins - 30th January 2024
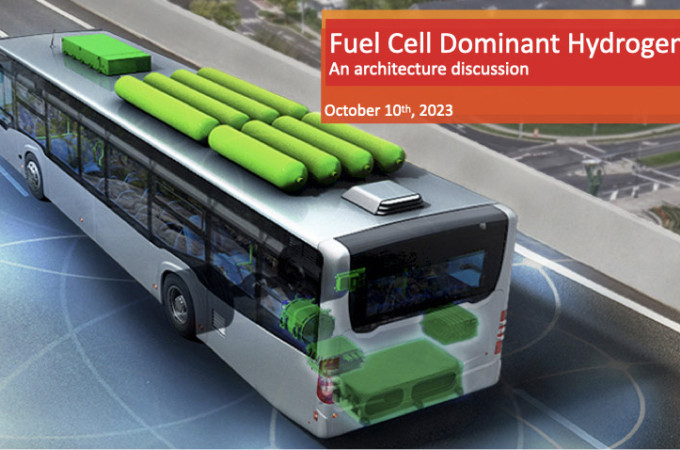
Schematic of an electric city bus with BAE Systems’ key components in dark green
USA - There are two standard hydrogen fuel cell (HFC) architectures for fuel cell vehicles that can be seen in the North American transit bus market today: One being a battery dominant fuel cell or in effect a battery electric bus with a range extender on board in the form of a fuel cell and some hydrogen storage to power the bus; the other architecture, which BAE Systems has implemented in the past and is also implementing now, is fuel cell dominant architecture; otherwise known as a fuel cell hybrid. A hybrid bus, where the fuel cell replaces the diesel engine, typically with more on-board hydrogen storage capacity and a much smaller battery.
These were the opening remarks of Greg Marx, Applications Engineer, Power & Propulsion Solutions at BAE Systems, in a presentation at APTA Expo 2023 held in early October in Orlando, Florida, when giving a brief overview of the transit bus market in North America and suggesting that the next step on the zero emissions road map was increased use of hydrogen fuel cell hybrid architecture.
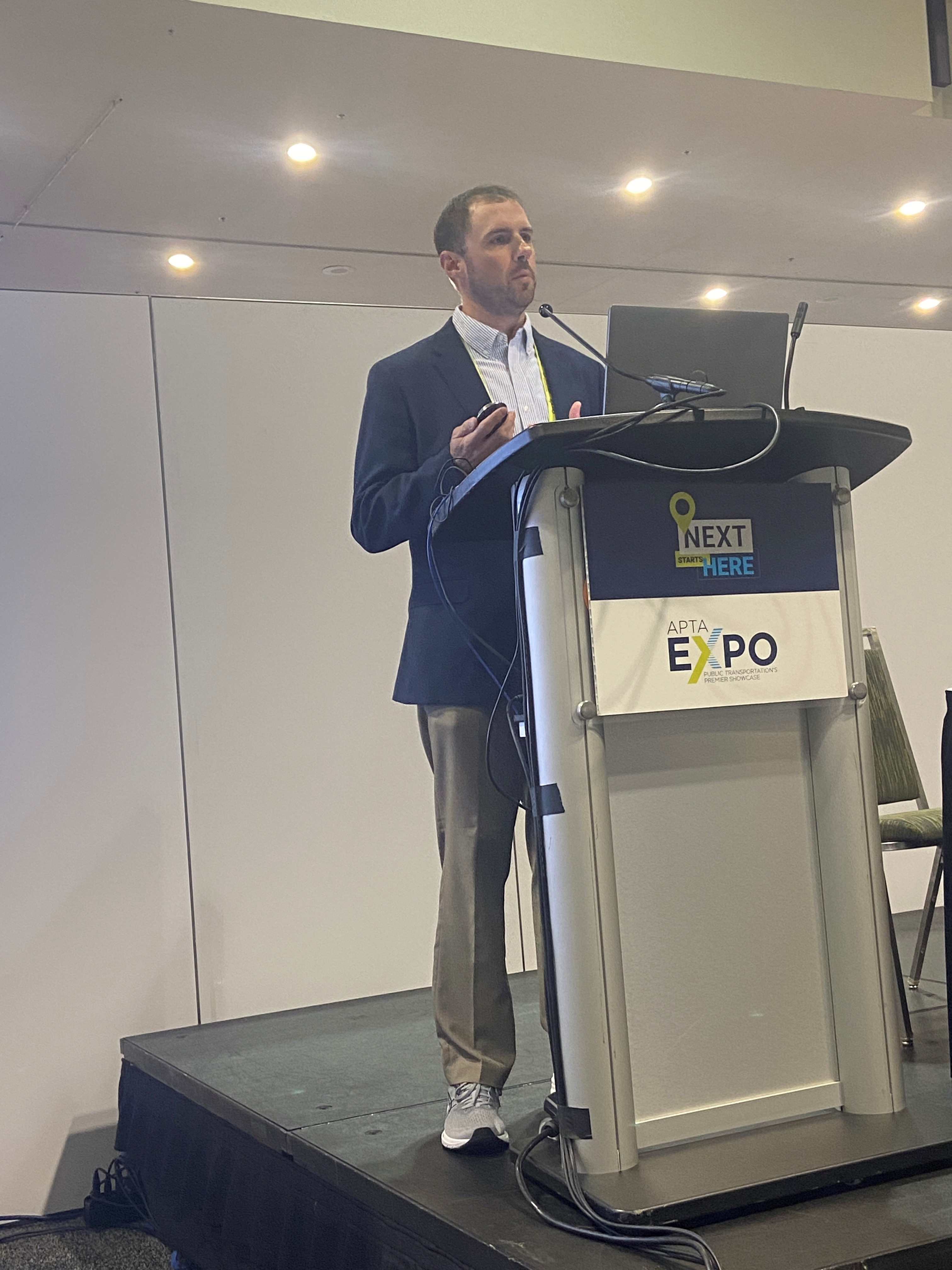
Greg Marx – Senior Principal Systems Engineer, Power & Propulsion Solutions at BAE Systems based in Endicott, New York, United States. Greg Marx is a vehicle applications engineer for diesel electric, fuel cell electric, and electric transit bus programmes, supporting design, integration, and testing phases for all vehicles. Marx has experience with electrified accessory suites, electric vehicle drive modes including GPS-enabled electric drive, control law and software development, and vehicle level troubleshooting and diagnostics. He has served as systems lead for several vehicle integration efforts, including a remote effort in 2009 and 2010. He is a member of the BAE Systems Hydrogen Safety Committee. Marx holds a Bachelor of Science degree in Computer Engineering from the University of Scranton, PA. |
---|
Battery v fuel cell dominant architectures
Marx went on to say that there are several other key differences between these two fuel cell architectures and that one of them is the size of the Energy Storage System (ESS) or battery.
On a battery dominant fuel cell architecture, there is notably more battery on board, stated Marx, typically more than 100 kilowatt hours (kWh). This generally consists of multiple battery packs consisting typically of NMC (lithium nickel manganese cobalt oxide) chemistry.
On a fuel cell dominant architecture, a smaller battery is used in the range of 20 to 40 kWh and a chemistry that is more suitable at handling a greater depth of regular discharge, such as LTO (lithium titanium oxide).
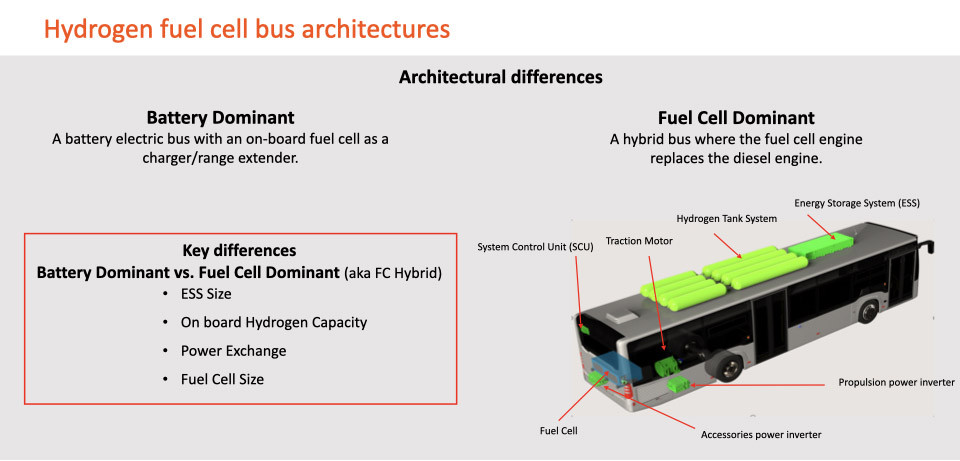
Battery dominant v Fuel Cell domninant elctric drive systems
Another key difference between the two architectures, is the amount of hydrogen on-board, Marx stated. The on-board hydrogen capacity for a battery dominant FC bus tends to be some four, possibly five tanks or the equivalent of 30 to 50 kgs of hydrogen. Whereas with a fuel cell dominant architecture, the aim is to maximise the amount of hydrogen gas on board, to maximise the fuel cell’s range; the number of tanks range from six to eight or the equivalent of 40 to 60 kg of hydrogen. The use of the battery in the FC dominant architecture functions in the same way as in a diesel hybrid for short distance zero emissions.
A further difference is power exchange. On the battery dominant architecture, the HFC is used as a range extender; so, the HFC tends to be smaller and initiates when the battery’s state of charge is depleted to a nominal amount to recharge the battery to help propel the vehicle. A HFC dominant architecture sends power to where it is most needed; either into the traction motor directly or into battery, depending on the battery’s state of charge. The battery, said Marx, tends to be used to offset high power demand during accelerations and to account for the delay in the fuel cell as it ramps up to meet the demand.
Lastly, the key main difference is fuel cell size; in the fuel cell hybrid architecture, “the fuel cell size should be as big as possible as it needs to replace the engine with the same amount of power.”
Fuel cell market trends
BAE Systems has been involved in fuel cell transit bus projects since the late 1990s and start of the millennium with trials of some demonstrator buses with different architectures evolving over the past two plus decades. Marx picked several projects that perhaps shows the evolution of fuel cell development in transit bus at BAE Systems.
Below is a short-list of BAE Systems’ key projects in date order from 2010 to today and going into operation next year, which essentially shows how the market has flip-flopped between battery dominant (BD) and fuel-cell dominant (FD) architectures.
…………………………………………………………………………………………………
BAE Systems involvement in fuel cell bus development
1998-2010: Various research projects
2010: A compound fuel cell hybrid Orion bus – a diesel hybrid with 2 x12kW fuel cells on-board.
2012: ENC Axess 40’ fuel cell hybrid with a 125kW fuel cell. (FD)
2013-17: A battery dominant ENC Axess 40’ with a smaller 85kW FC. (BD)
2024: ENC Axess EVO-FC 125kW fuel cell. (FD)
…………………………………………………………………………………………………
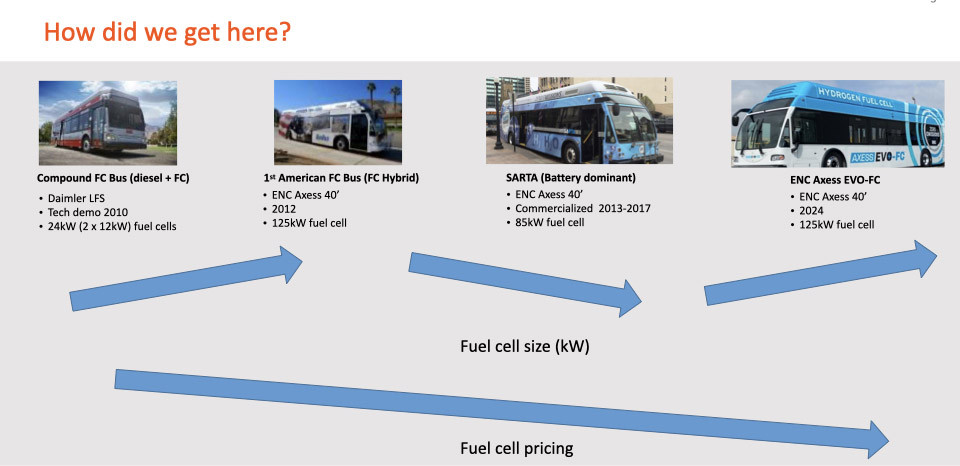
BAE Systems - Evolution of the HFC architecture in transit buses
In the 2020s, Marx said that BAE Systems has been seeing the market transition back to larger fuel cells and as such BAE Systems is now also transitioning back to the fuel cell hybrid architecture, where it is using a 125kW next gen fuel cell from its partner, Plug Power and 26kWh LTO battery.
The price of fuel cells, which were and still are a significant proportion of the bus, has been falling since 2010, said Marx, making the fuel cell hybrid architecture more economical. Consequently, this has pushed up the demand for fuel cells and most recently, demand for more efficient larger fuel cells with higher energy and power levels; Marx said he has seen examples of 150kW output fuel cells being used.
Challenges of fuel cell hybrid architecture
Marx said that BAE Systems has undertaken several design iterations to make the FC hybrid architecture work as well as possible to maximise the efficiency of the vehicle. One of the challenges is blending the FC power and ESS (battery) power together, Marx said, and that BAE Systems has a laboratory in Endicott, New York where this is undertaken.
Also, in the lab, it undertakes to manage the fuel cell for maximum hydrogen efficiency. A fuel cell, however, does not respond at the same speed as a diesel engine – it is not as fast – and this is where the ability to blend the power with the ESS is so important to performance and energy efficiency, but also, to prevent degradation to the battery.
The other main challenge is the amount of hydrogen that is required on-board each vehicle. If 60kg per bus is required this needs a significant capacity in H2 storage at the bus depot, which comes with different challenges of delivery / on-site production, storage and refuelling infrastructure, Marx pointed out.
Advantages of fuel cell hybrid architecture
“What we think it comes down to is this – ‘the more fuel on-board equals more range’,” stated Marx. “The market is showing us some range anxiety with BEVs, we believe the fuel cell hybrid architecture with the maximum amount of hydrogen fuel on board will offset this concern.” Marx, however, does not see the FC dominant architecture displacing the BEV in the market, but that both technologies will co-exist, with the FC dominant architecture being more suitable for longer range and longer periods of operation.
The other advantage is cost, said Marx. By having a smaller battery, this tends to result in the vehicle having a lower cost, said Marx. Why? First the initial price of the bus is lower because usually only a single battery is required and second, the lower cost at mid-life ESS replacement. Furthermore, BAE Systems believes the LTO chemistry can potentially last 10-12 years - -the life of the average bus today - without mid-life replacement. The battery overall and maintenance issues are also likely to be fewer too, Marx pointed out. It also reduces the volume of batteries required and the need for holding high stocks of batteries for backup.
Marx also suggested that the fuel cell dominant architecture is more efficient than battery dominant architecture. Why, because all the energy from the fuel cell can go direct to the e-motor when on the move and then switched, when stationary, directly to the battery, whereas in the battery dominant architecture, the fuel cell always charges the battery and then the energy must be converted to power the motor.
Another benefit of the FC hybrid is that it continues to provide power to the traction motor even if the battery state of charge falls to zero. “So, a 125kW fuel cell can power a bus up a low grade or back to a depot.”
Concluding remarks
The advantage of the larger fuel cells that are now coming to market is that in future it may be possible to use a fuel cell that can directly replace the 280 hp (200kW) diesel engine on a 40 foot hybrid vehicle. Whilst the FC industry is not there yet in offering fuel cells that can operate in that 200kW range, it could be almost a direct replacement for the diesel engine.