Green transformation: Oliver Schwank talks to T&BB about sustainability at Maxion Wheels
By Bradley Osborne - 20th February 2024
.jpg?w=680&h=450&fit=crop-45-36)
Maxion Wheels plant in Limeira, Brazil
Brazil / Germany – In the opening pages of its very first sustainability report, published in 2019, Iochpe-Maxion proclaimed its interest in “establishing a position of transparency for the market and society”. The Brazilian company – originally a logging firm and now one of the largest manufacturers of wheels and structural components for automotives and commercial vehicles – had pursued certain sustainability objectives prior to 2019, but these had been managed individually by its numerous subsidiaries. According to Oliver Schwank, who is Director of Global Safety, Sustainability, and Risk Management at Iochpe-Maxion’s division Maxion Wheels, the 2019 report represented the beginning of Iochpe-Maxion’s global approach to sustainability. The content of the report is confirmation of the company’s commitment to transparency, laying out in detail its energy consumption, greenhouse gas emissions, water usage, and raw material inputs; and this commitment is carried through three more reports from 2020, 2021, and 2022. But transparency should not begin and end within the pages of a sustainability report: and so, Oliver Schwank kindly submitted to our questioning; the answers to which form the basis for this article.
As 2019 was the year in which Iochpe-Maxion put together its corporate approach to sustainability, it was naturally taken as the baseline against which its future performance will be measured. While the absolute goal of carbon neutrality is set firmly in place for 2040, the company has committed to meeting relative targets in the interim. These include reducing its greenhouse gas emissions intensity (measured in tonnes of CO2 or equivalent per kilogram) by at least 30% in 2025, and 70% by the end of 2030. For the 2025 and 2030 targets, Iochpe-Maxion is counting scope 1 and 2 emissions only: that is to say, emissions derived from its business activities and from its energy consumption. Scope 3 emissions coming from the company’s value chain are covered by the 2040 target only.
In 2019, Iochpe-Maxion produced 186,467 tCO2e in scope 1 and 166,615 in scope 2. In 2020, scope 1 emissions fell dramatically to 145,302 tCO2e, rising back to 175,073 in 2021 before falling again, only slightly this time, to 171,034. The proximate cause of the anomaly in 2020 was the pandemic, and the resultant effects of supply chain disruption and market slowdown on production. By contrast, Iochpe-Maxion’s scope 2 emissions have trended steadily downwards: from 228,234 tCO2e in 2020 to 212,719 and 166,615 in 2021 and 2022. While such figures are an important measure of the company’s progress towards its sustainability targets, the key performance indicator is the trend in its emissions intensity. Here, the figures show a slight increase in 2020 and a reliable downward trend since then. Against the 2019 baseline of 0.000390 tCO2e/kg, Iochpe-Maxion records 0.000398 in 2020, 0.000371 in 2021, and 0.000313 in 2022. The 2022 number demonstrates a 19.7% decrease in emissions intensity since 2019, a significant advance towards the preliminary 2025 target of 30%.
Schwank joined the company in 2018, and in his view, the company’s success in meeting its sustainability targets thus far is reflective of its focus on innovation and competitiveness. The reduction in emissions intensity was achieved not only by purchasing more renewable electricity – though the company’s use of renewable energy has indeed grown considerably, jumping from 13% in 2021 to 37% in 2022. It was also achieved by new production methods that are boosting efficiency in the wheel plants and therefore lowering the energy consumed for every wheel made. Future reductions will be made by consuming less raw material per wheel and by using increasing amounts of sustainable steel and aluminium.
Like many other corporate documents of its type, Iochpe-Maxion’s sustainability report also publishes targets and commitments related to its workforce, its corporate culture, and its philanthropy. When asked about the emergence of environmental, social, and corporate governance (ESG) requirements, Schwank told T&BB that he thought it a positive development that spurs companies on to take actions which would be hard to justify on a purely material basis. As a result of ESG, there is considerable pressure to take on sustainability commitments from investors and customers, and this is driving change across multiple industries. Without the investor push, Schwank said, “it would be way harder [to become more sustainable], especially during less favourable business cycles”. In 2021, Iochpe-Maxion issued its first sustainability-linked bonds, a financial instrument intended to incentivise sustainable business activities; in this case, the key performance indicator is Iochpe-Maxion’s reduction in emissions intensity.1
.png)
Solar farm at Maxion Wheels Saraburi plant in Thailand
Sustainable production: achievements and challenges
Maxion Wheels operates 24 facilities across the world, making aluminium and steel wheels for both light and commercial vehicles. At six locations in Brazil, Mexico, Germany, Turkey, India, and China, Maxion produces steel wheels for trucks and other heavy-duty vehicles. While our conversation was focused on commercial vehicle wheels, many of Maxion’s plants cover multiple product lines and, as such, the following relates to its light vehicle wheel production as well.
There are two ways in which Maxion can significantly reduce greenhouse gas emissions from its industrial processes: one way is to use more energy from renewable sources; the other is to improve the efficiency, and thus lower the energy consumption, of its production methods. The latter pathway has required greater ingenuity. One example which Schwank gave was the heat treatment process. The company found that, simply by lowering the temperature by 5 to 6 degrees Celsius, it could reduce the plant’s emissions by 2%. As a result, the company is now working to implement this on a plant-by-plant basis. It is an innovation which depends on digitisation in order to work: through remote live monitoring of temperatures, for example, the heat treatment process can be managed to a much finer degree than was possible before, allowing for energy savings as great as 20%. The same tools used for finetuning heat treatment can also be used to monitor and optimise energy consumption, measuring electricity demand and shutting down idle systems in real-time. Just by digitising the plant, Schwank claims, it is possible to reduce overall emissions by 20-25%. As such, Maxion is aiming to implement digital monitoring and controls across every plant by 2027.
Of the two primary ways of reducing a company’s emissions, substituting renewables for energy derived from fossil fuels would appear to be far simpler and more immediately effective than investing in cutting edge technologies to improve efficiency. On the contrary, Schwank’s experience thus far has shown that switching to renewables is often complicated and can vary greatly from country to country. At its hot and sunny locations – in Thailand, India, Turkey, South Africa, and Mexico – Maxion has taken the decision to provide for its own energy needs with solar. For the most advanced of these projects, at the aluminium wheel plant in Saraburi, Thailand, Maxion installed solar panels on the roof of the plant and in an adjacent “solar park”. These contribute 24% of the plant’s total energy needs. At its wheel plants in Pune, Maharashtra, India, Maxion intends to generate over half of its energy with solar.
In locations where onsite electricity generation is not feasible for one reason or another, Maxion is buying in more energy from renewable sources instead. For instance, there are wind farms close to the company’s plant in Königswinter, Germany, as well as several other national renewable energy projects which allow the plant to replace its fossil-derived electricity. Such arrangements with the power supplier, which permit customers to increase their renewable energy mix, are not available in every country. In a country such as Thailand, where two or three government-owned power companies are in control, there are fewer options available. And in a country such as Mexico, the government may actively obstruct the efforts of companies to increase their use of renewables, according to Schwank. It is especially bad news when the nationalised energy sector is based on fossil fuels: in such cases, the government has an incentive to suppress renewable alternatives. This is consequently one of the main reasons why Maxion has decided to try and generate its own energy in these countries. In Thailand and India, it aims to expand its renewable energy generation to cover 40% and 100% of its needs, respectively.
At Maxion’s Brazilian plants in Limeira and Cruzeiro, the need to decarbonise electricity supply is far less urgent. According to Schwank, 88% of electricity from the Brazilian grid already comes from renewables, and so the company has chosen to focus its attention instead on replacing its supply of natural gas. The fuel is necessary for its industrial processes, which means the only feasible alternative is to switch to renewable natural gas (“biogas”) and/or “green” hydrogen. Brazil is pursuing both, but the biogas option is currently more advanced, and it has therefore been the focus of Maxion’s work on replacing natural gas. Schwank told T&BB that substituting renewable gas for fossil-derived gas would be easy, requiring very little change to the existing plant equipment and infrastructure. However, at this stage of feasibility testing, the Brazilian plants need to have their renewable gas delivered by truck, as transport through pipes is currently unavailable.
At the passenger car wheel plant in Ostrava, Czech Republic, Maxion is trialling green hydrogen instead of natural gas. The safety and effectiveness of the gas as a replacement is currently under assessment; the company is also looking into generating its own hydrogen onsite. In the short term, making its own hydrogen would be necessary for the Ostrava plant, as green hydrogen is expensive and available in only small quantities.
.jpg)
Arrival of raw steel at Maxion Wheels' Königswinter plant
Sustainable products: achievements and challenges
Maxion produces aluminium wheels for light vehicles such as passenger cars and vans. Not only is aluminium production more carbon intensive than steel production, it is – paradoxically – easier to decarbonise. Consequently, more effort has been put into making aluminium more sustainable. By contrast, steel has received less attention, putting it five years behind aluminium, according to Schwank.
“Green” steel options are limited. Schwank told T&BB that the carbon intensity of this low-carbon steel is about 1.75 tons of CO2 per ton steel, compared to the average range of between 2 and 3 tons. Maxion’s research and development into producing wheels with “green” steel has found that, together with the efficiency measures detailed above, a carbon emissions reduction of 62-66% is possible. However, the low-carbon option comes with a significant cost, according to Schwank. While customers have shown interest in low-carbon steel wheels, so far there have been no major commitments. The sustainability requirements which Maxion sees now from almost every aluminium car wheel customer in Europe are yet to be replicated by its customers for its steel truck wheels.
The obstructive expense of sustainable steel, and customers’ reluctance to absorb the additional expense, will become “a stoppage in the sustainability journey for a lot of suppliers”, including Maxion. This might only be overcome, certainly in the short term, by government intervention to incentivise the purchase of low-carbon steel products, or disincentivising conventional steel products. On the other hand, there has been a recent positive development, especially within the light vehicle segment, as customers are increasingly realizing that steel represents the lowest carbon option. This heightened awareness among consumers sparks optimism for a shift in the industry dynamics, where a greater adoption of steel wheels becomes a strategic choice for reducing a vehicle's overall carbon footprint.
However, there are more obstacles on the horizon for companies such as Maxion Wheels. Two “green” steel projects came to the attention of the commercial vehicle industry in the past year: one by established firm SSAB, and the other by startup H2 Green Steel. Both are in Sweden, both aim to replace coking coal with hydrogen in the steelmaking process, and both have agreed to supply vehicle manufacturer Scania beginning in the latter part of this decade. The projected timeline for green steel production is a sobering reminder that, even when the steel becomes available, it will be in relatively small quantities and at high demand from customers who will all be looking to decarbonise their businesses. “The volume will be very low, and if as a company, you want to secure your volume to [2026], you need to enter agreements with the suppliers now,” Schwank told T&BB. Again, the situation will vary between markets: Schwank expects green steel will become more widely available in Europe and Brazil by the end of the decade, whereas in India, customers may be waiting for five additional years. In China, “the problem remains unclear”: while volumes of green steel could potentially be very high, Schwank believes most or all of it will only be available to Chinese companies.
Even by 2030, the quantities of green steel that will become available will be restrictive to more ambitious sustainability goals. “If you want to go 100% fossil free steel, that will not work,” Schwank warned. In quantity as well as in technology, sustainable steel is likely to lag far behind aluminium, and it is not entirely clear what can be done to change this, or whether there will be any willingness from governments as well as from companies to do so. When one considers that the material inputs are responsible for as much as 80% of the carbon footprint of a steel wheel, the issue of availability threatens to become a “blocking point” for the industry’s sustainability ambitions.
In sum, a company which sets out with the best intentions and makes all the right moves might still find itself unable to meet its own sustainability targets due to external factors outside of its control. This is a challenge which Maxion faces alongside its rivals as well as its customers. Nevertheless, Schwank emphasises the transformation of mindset which has occurred at the company since the first sustainability report was published in 2019. As mentioned in the beginning, the divisions of Iochpe-Maxion were already following their own sustainability goals prior to 2019: what’s new is “the holistic approach in the company”:
Our products are getting better from a sustainability point of view, they’re getting lighter. Our processes get better. Raw materials are getting better, our production is getting more efficient, and we are using more green electricity. So it’s really a transformation of the whole company.
Ending the interview, Schwank pointed to lifecycle assessment as a crucial innovation for the industry, allowing for more rigorous measurement of the carbon footprint of a product which takes the whole of its life into account. Similarly, the innovation of Iochpe-Maxion’s corporate approach to sustainability lies in its holism; its ambition, to do everything more sustainably, “in all steps of the process.”
1 See its latest sustainability-linked financing framework, published in July 2023: https://api.mziq.com/mzfilemanager/v2/d/aa331a3b-0a4a-4acc-a70e-512ff88e3c02/e1969a96-5690-9d87-fc6d-ac25ef7349c2?origin=1
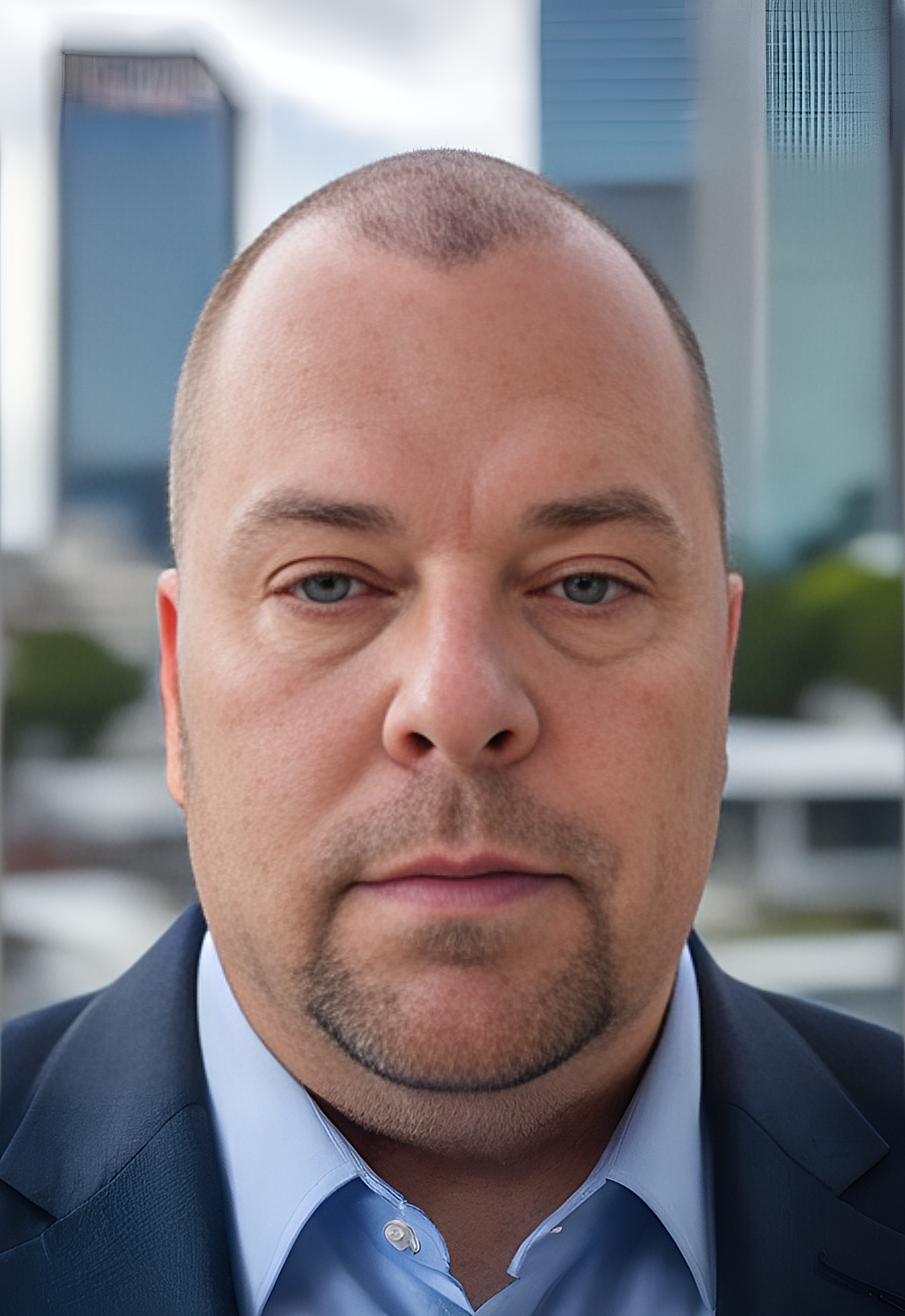
Oliver Schwank joined Maxion Wheels in 2018, and since that time, has led the strategic and operational execution of the Company’s sustainability, safety, and risk processes and procedures. Prior to joining Maxion Wheels, Schwank served as Global Head of Security, Environment, Health and Safety at Ledvance. His career also includes several positions within the Health, Safety and Environmental department at Johnson Controls. He earned his Master's Degree in Environmental, Hygiene and Safety Engineering from the University of Applied Sciences Mittelhessen in Gießen, Germany.