“We are ready”: Maxion Wheels and the future of the CV industry at IAA 2024
By Bradley Osborne - 5th November 2024
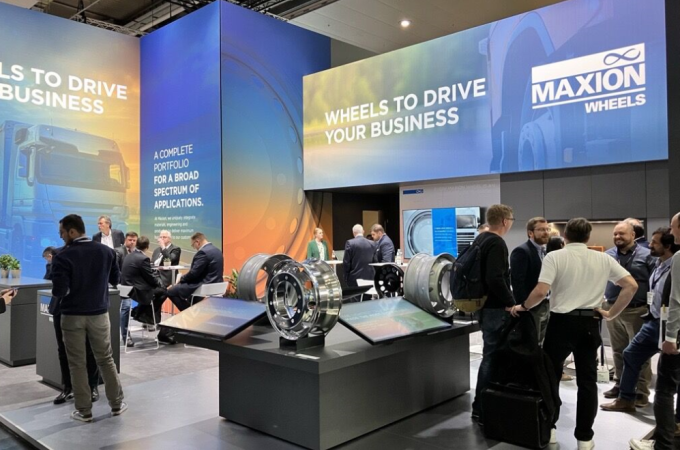
Maxion Wheels' stand at IAA Transportation 2024
Germany – At IAA Transportation 2024, held between 17-22 September in Hanover, Germany, the vehicle manufacturers said in unison to delegates: “We are ready for the transition to electric vehicles. Now we are waiting for the market to follow.” Maxion Wheels had a similar message for its OEM customers: “We are ready. Everything is developed. We know how to do it.” At its stand, the company showcased a range of different wheels, from sustainable steel to light electric urban to forged aluminium – this last type being shown to the public for the very first time since Maxion announced its intention to enter this market segment at IAA Transportation 2022. But Maxion’s execs were keen to stress that the company’s moves to support electric vehicles and sustainability are not disruptive; rather, these initiatives are in keeping with a longstanding “culture of innovation” at Maxion.
At the show, Truck & Bus Builder spoke at length with Mark Gerardts, Business Unit President EMEA and Ralf Duning, Vice President, Global Engineering. They agreed that uptake of electric vehicles will not pick up until they become affordable. While there was optimism about the electric transition at the 2022 show, at this year’s show, exhibitors are now vocal about the hard reality, that electric vehicles are not yet selling in volumes high enough to justify the massive investments made in them. Like so many others in the industry, Maxion has invested resources in anticipation of a market that has yet to fully develop. However, Gerardts and Duning both stressed that the company’s investments do not carry a huge risk. Much of the work Maxion has done to meet customer needs and enhance its competitiveness has led to real gains that can be enjoyed regardless of what the electric vehicle market ends up doing.
Take, for example, its “lightest sustainable truck wheel”, which was on display at the company stand. Maxion has brought the weight of its lightest series production steel wheels from 43 kilograms down to 32 kilograms, with the latest new development below 30 kilograms. The mission of Maxion’s engineers has been always to make wheels that are “lighter, lighter, lighter”, all while maintaining high levels of strength and robustness. For the electric truck manufacturer, who must accommodate the extra weight added by battery packs, any weight reduction that can be made in other areas, including the wheels, is very welcome. But the traditional combustion engine truck also benefits from the lower weight because it allows for reduced fuel consumption and higher payload. For Maxion, there is no dichotomy between conventional and electric drivelines: what benefits one can benefit all.
That is not to say that electric vehicle wheels are no different from those made for conventional vehicles. At its stand, Maxion also showcased the ‘eGen32’ steel wheel which is optimised for electric vehicles. Trucks carrying upwards of six battery packs can be as much as 10% heavier than their traditional counterparts, increasing the front axle load on each wheel by up to 500 kilograms. Maxion engineers were challenged to come up with a steel wheel design that would improve wheel performance and accommodate the extra load – without adding weight. The result was the eGen32, a wheel with a load capacity of 4,250 kilograms (compared to the “lightest sustainable truck wheel” which can take 4,000 kilograms).
Even this kind of ingenuity can take us only so far: to reduce the weight of a CV steel wheel to 25 kilograms would take a huge “technology leap”. Which is why Maxion is extending its CV wheel portfolio by offering for the first time a range of forged aluminium wheels for trucks, which are lighter by as much as 10 kilograms than today’s 32/34 kilograms steel equivalents. Again, the benefits of aluminium are manifold. A heavy battery electric truck will shed even more weight by using aluminium instead of steel, but equally, the conventional bulk storage truck-trailer will also enjoy the payload increase which would result from choosing aluminium.
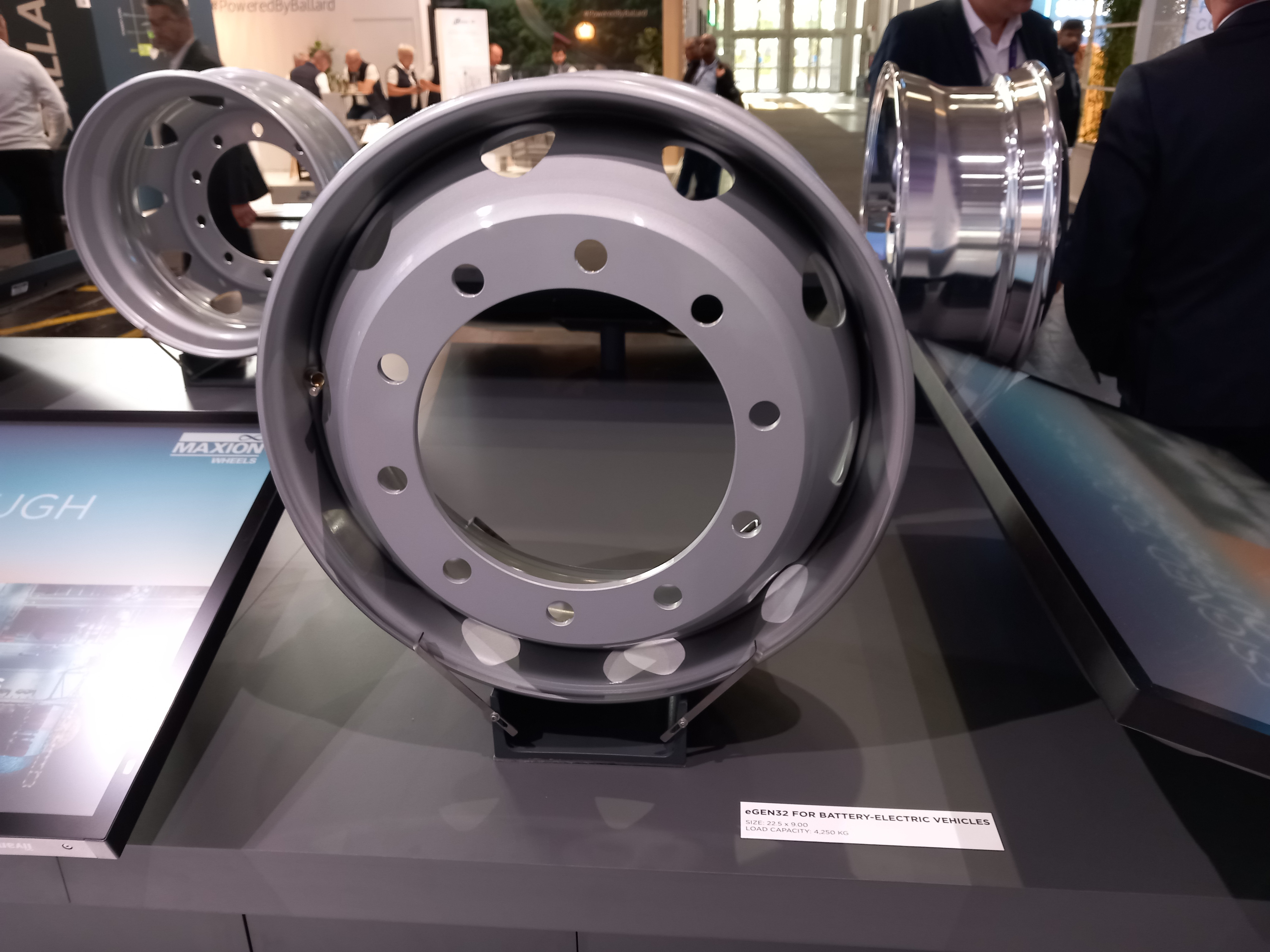
The 'eGen32' for battery electric vehicles
Though Gerardts and Duning admit there is a “question mark” over when the pace of electric vehicle sales will pick up, they are not discouraged. Maxion engineers continue to work as usual on making wheels that are as light and strong as possible. They are ready today to help operators increase their margins, and they are ready to do the same for electric vehicles as soon as the market matures. Gerardts and Duning were more concerned about the continuing ambiguity around the definition of a “green wheel”. Maxion is prepared to supply sustainably-made wheels as soon as there is demand, but given their higher cost, it will take a clear definition of “sustainable” and a push from the regulators to create a market for them, and Gerardts said that Maxion is keeping a close eye on the movement of government regulation and incentives in this area.
Markets – India and China
After taking a look at the wheels on display, we sat down to discuss two topics: market strategy and the future of wheel design. On the first topic, Gerardts explained that, now the company’s strategies for Europe and the Americas are in motion, its focus is shifting eastwards to India and China.
On the subject of India, the men rebutted the idea that the market values price above all else. “A wheel is a safety product. You cannot compromise on it.” Though it makes adaptations to suit local requirements, Maxion conducts its research and development globally and applies the same production and design standards across its wheel plants. As the Indian market continues to grow, Maxion expects to see an increase in demand for highly engineered products.
On China, Gerardts and Duning said that the pace of electrification has been “so quick” that wheel design “has not been able to keep up”. This applies to the passenger car segment even more than it does to the commercial vehicle segment, and Maxion expects to transfer many of the lessons from light vehicle wheel design to truck and trailer wheels. In China, Maxion has built up its business based on its “reputation for reliability”, and it will continue to maintain this as it focuses on keeping pace with the electric transformation.
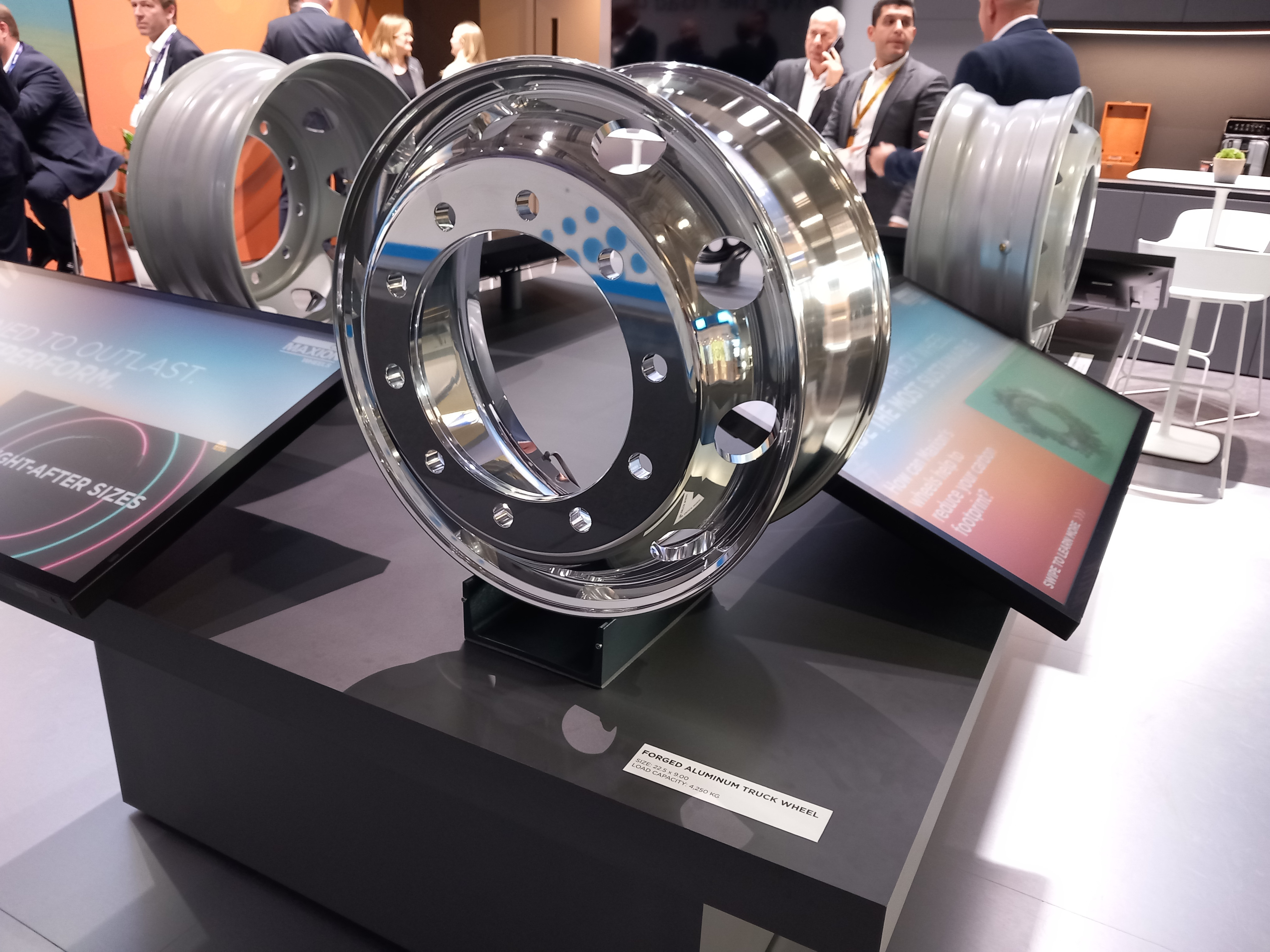
Maxion's forged aluminium truck wheel
Future of wheel design
On the future of wheel design, Gerardts and Duning named three topics: connectivity; aerodynamics; and expanded functionality. Expanding on the first and third points, we discussed the use of data in wheel development and maintenance. Wheel data is a boon to engineers: with more precise and wider ranging measurements, taken from customers’ wheels on the road in active duty, Maxion engineers are able to fine tune hundreds of parameters – leading ultimately to better products in the future. With real-time data analysis, Maxion aftermarket will increasingly be able to offer predictive maintenance and other services to customers.
Duning also raised the topic of system approaches to wheel design. Explaining what it would mean to treat a wheel as a “system” as well as a component, he said that further gains could be made, for example, in overall weight reduction. By optimising the “system”, one could shed weight from the tyre, add more weight to the wheel to compensate, and still end up with a lighter “wheel system” overall. Duning expects that the future of wheel development may increasingly take this “systems” approach to design.
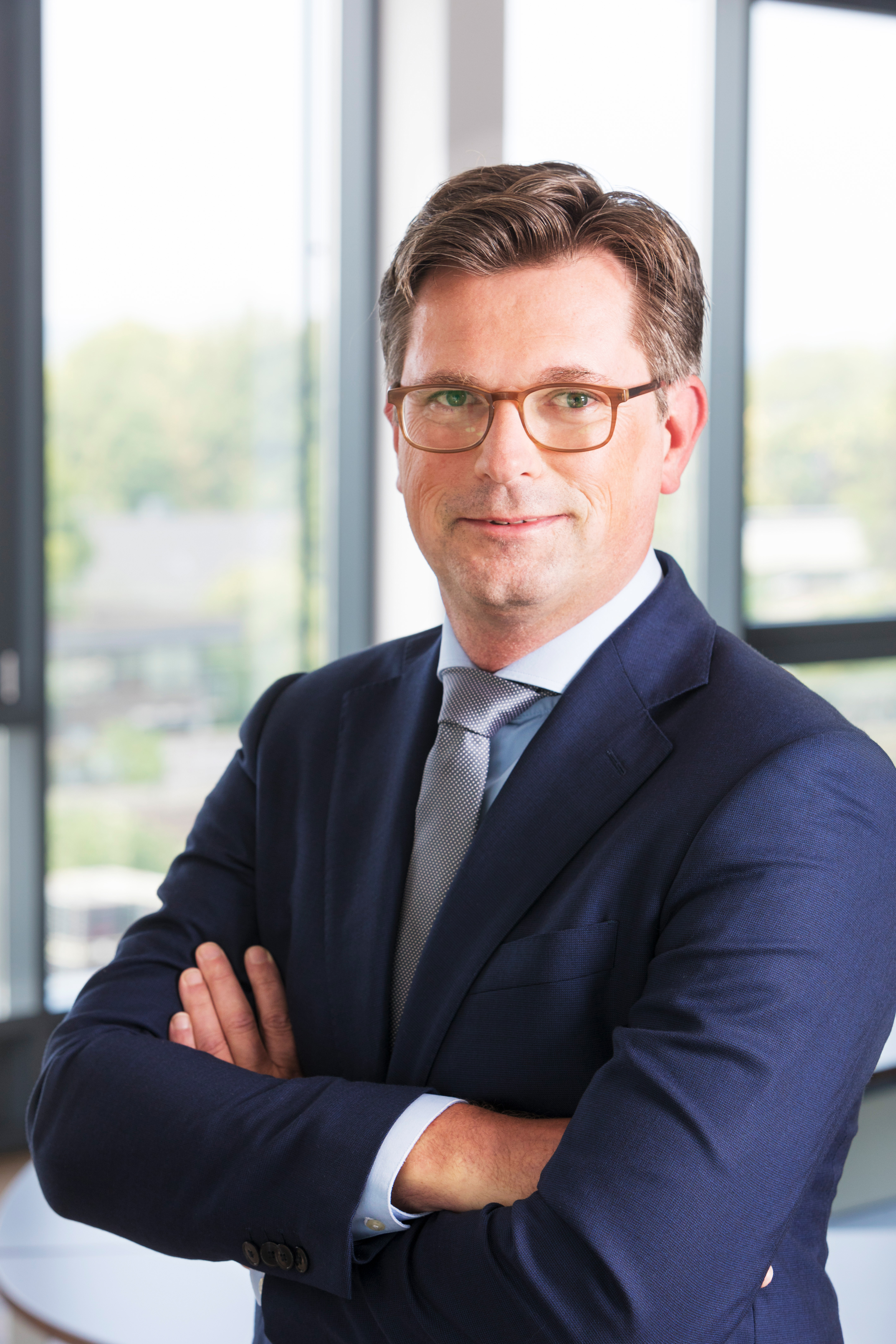
Mark Gerhardts serves as the Business Unit President of Europe, Middle East & Africa (EMEA) for Maxion Wheels, leading operations and strategic growth at ten wheel plants. He joined Maxion in 2015 and took on his current role in January 2024. Before Maxion, Gerhardts worked at Michelin, Mefro Wheels, and insulation firm Rockwool Rockpanel BV.
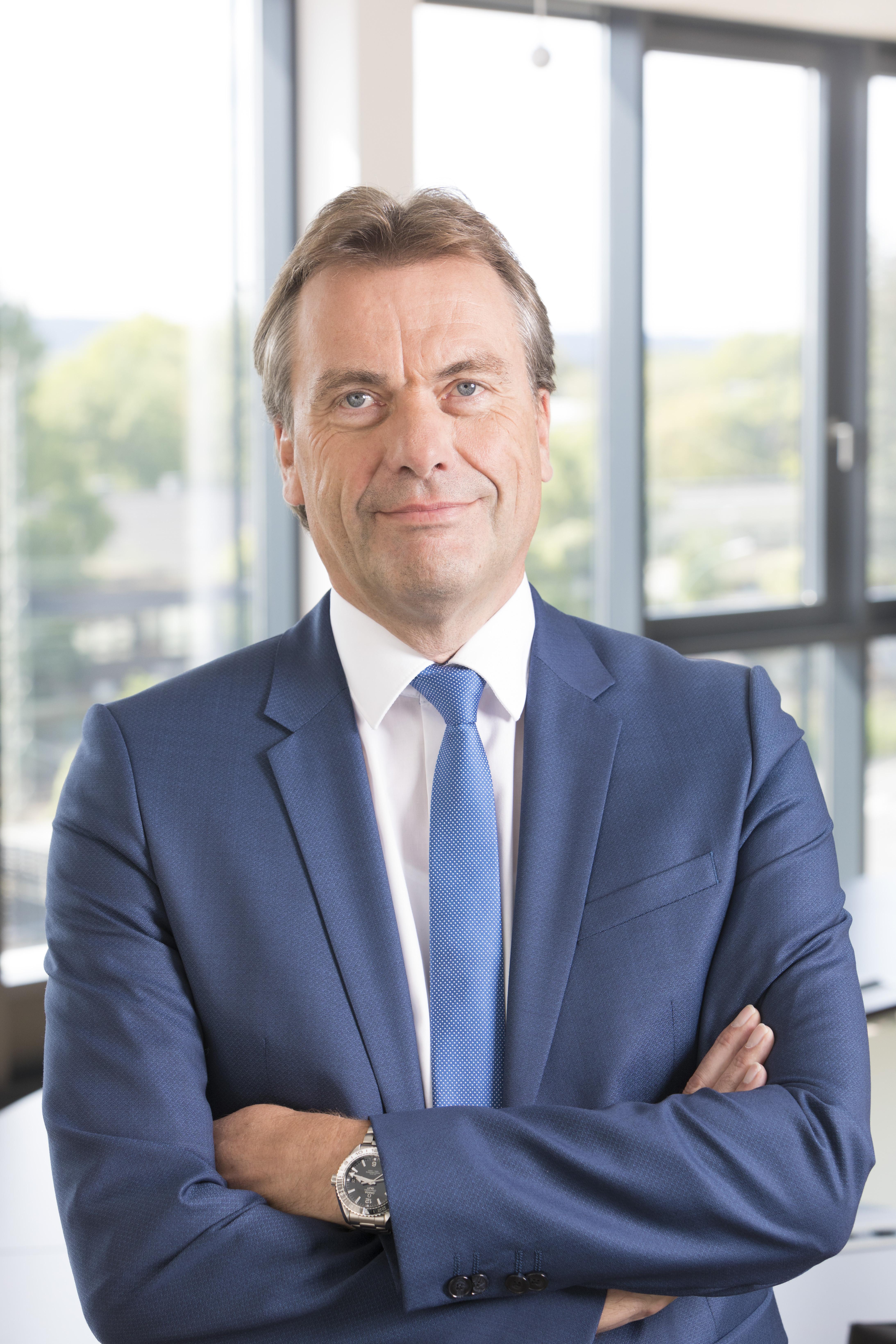
Ralf Duning is Vice President, Global Engineering for Maxion Wheels, a role to which he was promoted to this role in June of 2015. He is responsible for Maxion’s global R&D processes, including: customer-focused application engineering, program management, advanced engineering and new process development. Prior to joining Maxion in 2014, he worked at Michelin, steel engineering conglomerate Mannesmann, and bearings manufacturer NSK.