A Novel Approach to Platform Electrification: How BAE Systems Is Simplifying the Future of Heavy-Duty Mobility
By Luke Willetts - 6th May 2025
,-MPCS-(Middle),-Electric-Motor-and-EV-T.png?w=680&h=450&fit=crop)
BAE Systems’ ‘GEN 3’ components MAPS (Top), MPCS (Middle), Electric Motor and EV Transmission (Bottom)
USA - Electrification in the commercial vehicle sector isn’t just a technological shift, it’s a fundamental redesign of how vehicles are built, integrated, and maintained. While the benefits of zero-emission transport are clear, the route to full electrification is paved with complexity and cost, especially for OEMs under pressure to innovate faster, reduce prices, and minimise technical risks.
Yet, making the leap from diesel to electric isn’t a matter of simply swapping out one power source for another. For original equipment manufacturers (OEMs), electrification introduces new layers of technical and operational complexity.
As Derek Matthews, Global Partnerships Manager at BAE Systems, said:
Vehicle OEMs have a significant task on their hands when looking to electrify their vehicle offerings. Some perceive electric vehicles to be simpler than their predecessors – but in reality, the old design challenges have just been replaced with different, new ones. These range from redesigning vehicle architectures to meeting new regulatory standards. Despite the promise of clean transportation, the journey toward full-scale electrification is rife with hurdles. Hurdles that cost time and money!
Derek Matthews, Global Partnerships Manager at BAE Systems
BAE Systems has taken a fresh approach to power electronics, one that reduces complexity, enhances configurability, and offers integration support that empowers OEMs, not burdens them. The result? A simpler, more efficient path to electrified vehicles.
The electrification challenge
In his 2024 address at the IAA Transportation Event, Derek Matthews pointed out that electrifying heavy-duty vehicles is a complex balancing act. OEMs must now deliver reliable, high-performing zero-emission solutions without increasing vehicle development timelines or manufacturing costs. That’s a tall order when every element of the powertrain, from motors to cooling systems, must be reimagined.
Space and weight constraints
Adding batteries, electric motors, power electronics, and the accompanying cooling and HV infrastructure introduces new demands on already tight vehicle packaging. Every component has a space claim, every kilogram matters, and legacy designs were rarely made with electrification in mind.
Efficiency, compatibility and systems integration challenges
Beyond just power conversion, OEMs must consider the efficiency of charging systems, battery management, electric accessories, and more. These new subsystems introduce fresh metrics and trade-offs. Efficiency isn’t optional, it’s integral to range, TCO, and uptime.
Vehicle platforms are often cobbled together from systems and components sourced from different suppliers with varying levels of expertise and maturity. The integration risk is high, and when things don’t work together seamlessly, who takes responsibility?
Certification complexity
Gone are the emissions tests, but in their place are evolving electrical safety standards, cybersecurity protocols, and homologation hurdles. With regulations still maturing, OEMs need both technical know-how and regulatory insight to stay compliant.
This evolving landscape can overwhelm OEMs, particularly those newer to electrification or without dedicated in-house compliance teams. The cost of missteps is steep: failed certifications, production delays, and potential liability issues. What’s needed is a trusted partner who can deliver not only hardware but also a deep understanding of the regulatory terrain.
Enter BAE Systems: Integration by Design
Derek Matthews continued:
BAE Systems is answering that call. With nearly 30 years of experience in vehicle electrification, in both commercial and defence applications, the company has developed a platform-based approach that simplifies electrification for OEMs. At the core of this strategy are our third-generation power electronics: the Modular Power Control System (MPCS) and the Modular Accessory Power System (MAPS).
Unlike traditional component suppliers, BAE Systems doesn’t just offer parts; it provides scalable, ready-to-integrate electrification products that consolidate critical power functions and reduce engineering overhead. This architectural approach enables OEMs to accelerate product development, reduce risk, and easily tailor electric drivetrains to a broad range of vehicle classes and duty cycles.
MPCS: The electrification backbone
The Modular Power Control System acts as the central nervous system for high-voltage electrification. It manages the vehicle’s main propulsion and energy distribution functions, including traction motor control, battery pack combining, and charging interface coordination.
What sets the MPCS apart is its slice-based modularity. OEMs can scale the system up or down depending on the vehicle’s power requirements without needing a ground-up redesign. This commonality is a game-changer for manufacturers looking to build multiple electric vehicle models on a shared platform, from last-mile delivery vans to long-haul trucks.
BAE Systems’ MPCS
The Nova Bus LFSe+
One of the most compelling real-world applications of the MPCS is in the Nova Bus LFSe+, a zero-emission transit bus powered by BAE’s Gen3 electric drive system. This vehicle supports configurations from four to eight battery packs, with a total onboard energy capacity of up to 784 kWh.
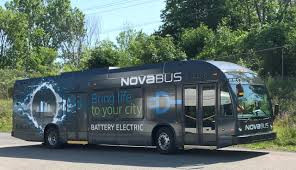
Nova Bus LFSe+
Thanks to the MPCS, Nova Bus can use the same chassis design across different route types, inner-city or suburban, simply by varying the number of battery modules. This flexibility eliminates the need for costly redesigns, shortens production timelines, and allows transit agencies to adapt to varying service demands using the same platform.
MAPS: Powering the essentials
While the MPCS handles propulsion, the Modular Accessory Power System provides clean, reliable power for lower-voltage systems such as HVAC, power steering, lighting, and vocational equipment like electric PTOs.
MAPS delivers both 24V DC and three-phase AC outputs, and, like its high-voltage counterpart, is modular and scalable. Whether it's a refuse truck that needs high accessory power for compaction systems or an airport shuttle with heavy climate control demands, MAPS can be configured accordingly, without requiring bespoke design changes.
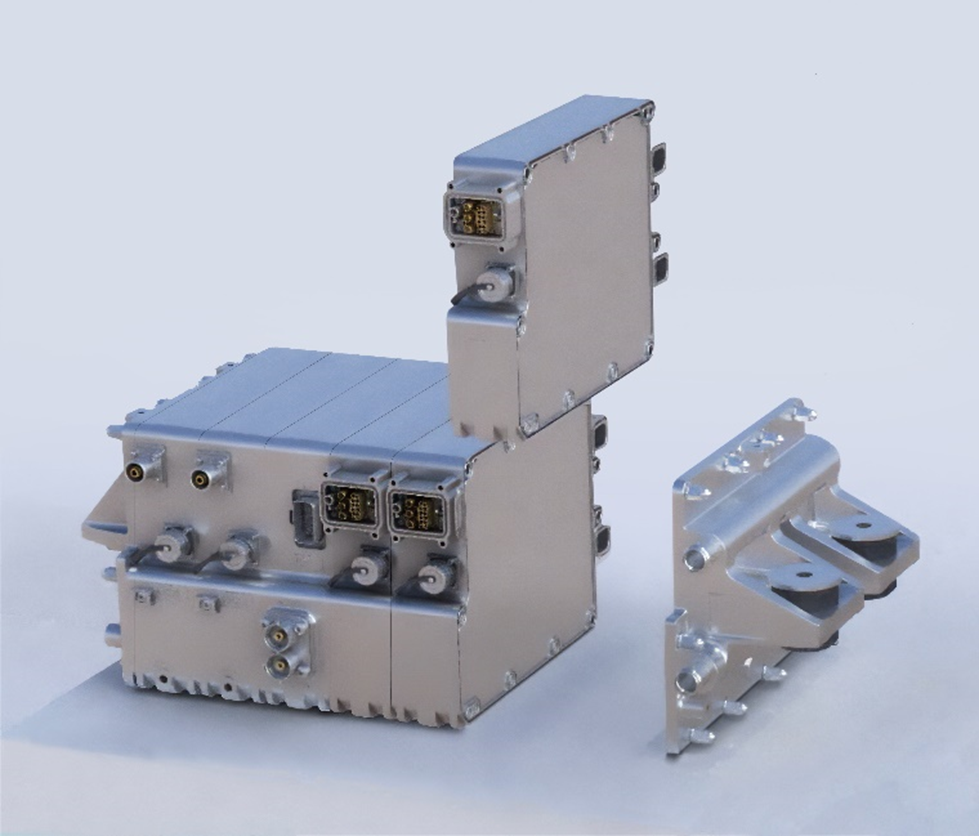
MAPS unit, highlighting the configurable ‘slice’ design
Streamlined integration and simpler manufacturing
What truly differentiates BAE Systems is its integration-first philosophy. By delivering pre-engineered, cohesive subs-systems, the company removes much of the guesswork and variability from vehicle integration. The result is fewer components to manage, fewer connection points to fail, and a cleaner overall design.
This streamlined architecture translates into faster production times, easier troubleshooting, and enhanced serviceability. For fleet operators, it also means increased reliability and reduced total cost of ownership. These are key metrics in any procurement decision.
Less complexity, more control
Through systems consolidation, BAE Systems reduces the total part count of electrified vehicles. That means fewer vendors to manage, simpler logistics, and fewer failure points. This all contributes to better uptime and lower maintenance costs.
OEMs benefit from a leaner bill of materials, while gaining flexibility to adapt the platform to a range of use cases. This balance of simplicity and scalability makes BAE’s approach especially attractive to manufacturers managing large, diverse fleets.
Proven on the road and built for the future
In April 2025, BAE Systems announced its Gen3 electric drive system would power 42 hybrid-electric buses for San Francisco’s transit fleet, built by New Flyer. These vehicles incorporate cutting-edge technologies such as silicon carbide (SiC) inverters and high-efficiency permanent magnet motors, which deliver lower weight, greater efficiency, and quieter operation compared to traditional induction motors.
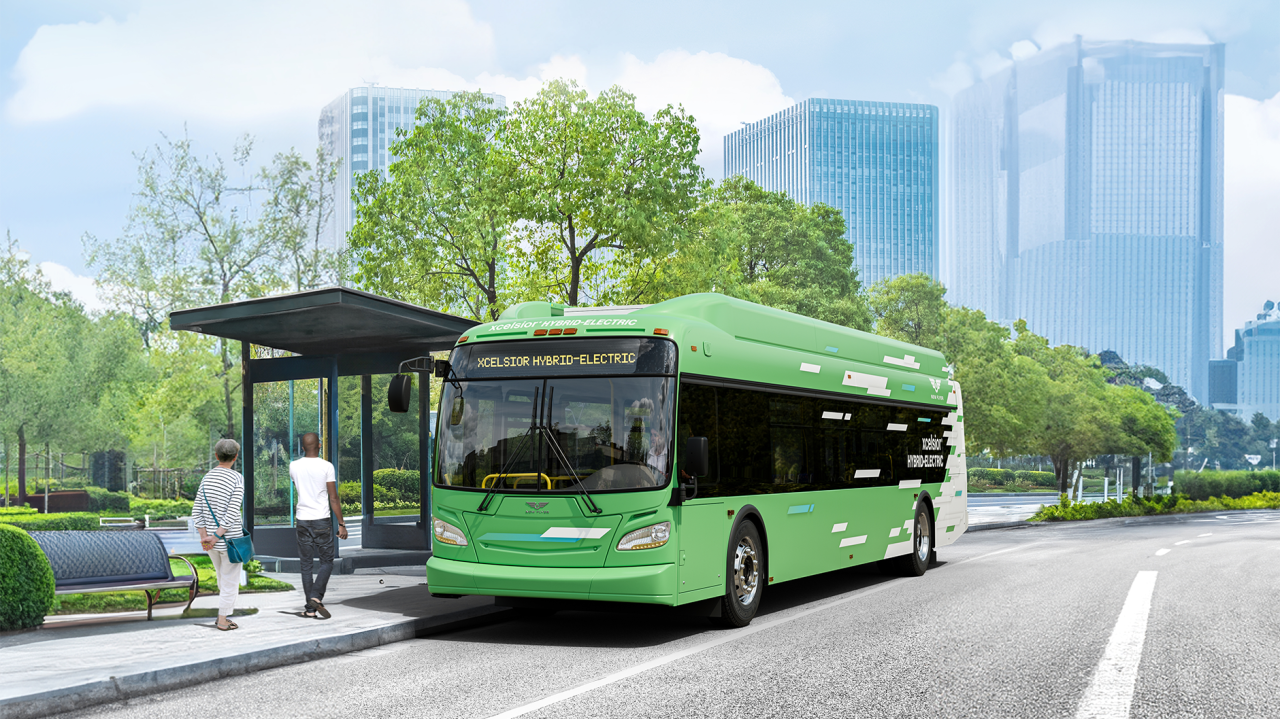
New Flyer Xcelsior hybrid-electric bus
This same electrification platform is already being used in battery-electric and hydrogen fuel-cell vehicles, showcasing its drivetrain-agnostic design. For OEMs, this means one platform investment can support multiple propulsion strategies, enhancing ROI and reducing engineering risk.
Tailored for today’s trucks and tomorrow’s innovations
The MPCS and MAPS architecture isn’t just for buses. It’s equally applicable to a wide variety of heavy-duty commercial applications, from terminal tractors and dump trucks to vocational vehicles that demand complex power profiles.
With the ability to scale and configure accessory loads and powertrain control, BAE’s product offering allows manufacturers to address niche use cases without having to create entirely new vehicle platforms. That level of adaptability is critical as fleets become more specialised and customer expectations evolve.
Support that goes beyond supply
Whether supporting legacy manufacturers or newcomers to the EV space, the company brings decades of domain knowledge and an unwavering focus on customer success.
As Derek pointed out:
We recognise that not all OEMs have deep electrification resources in-house. BAE Systems can provide robust engineering and integration support throughout the development process, on a case-by-case basis, dependant on an OEMs needs and wants. From initial system design to validation testing, certification guidance, and even on-site assistance, BAE is willing and able to act as a true collaborator, rather than just a vendor.
A strategy for scalable electrification
In an industry often defined by one-off solutions and piecemeal electrification attempts, BAE Systems is offering something more comprehensive: a repeatable, scalable strategy for success. Its configurable electrification architecture enables OEMs to build, adapt, and scale electric vehicles quickly, without the compromises or complexities of traditional development models.
By integrating critical systems from the outset and providing a clear path to compliance and scalability, BAE’s approach minimises risk while maximising performance.
Powering the possible
As the heavy-duty vehicle industry races toward a zero-emission future, the challenges of electrification remain real, but so do the opportunities. BAE Systems is here to help OEMs overcome complexity, reduce costs, and bring high-performance electric platforms to market faster and with greater confidence. This will be paramount in a future where uptime, reliability, and simplicity will define competitive advantage.
At the 2024 IAA Transportation Event, Derek Matthews spoke about the concept of Electrification Simplified. You can watch his full address here: https://vimeo.com/1085712884