Systems within systems: Voith’s new inverter platform for electric vehicles
By Bradley Osborne - 5th September 2023
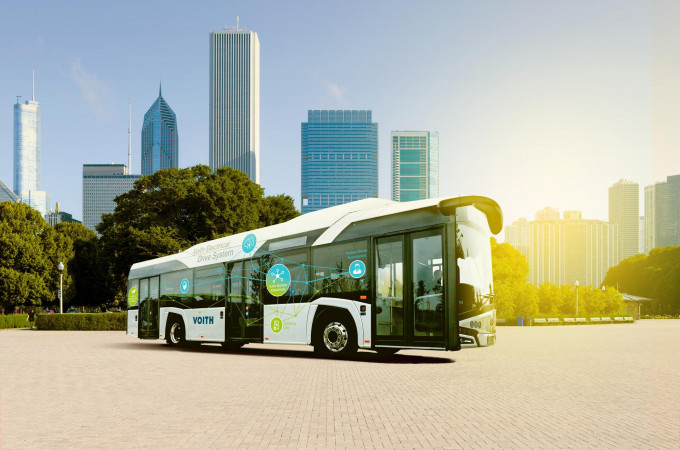
Solaris Urbino 12 powered by Voith Electrical Drive System
Germany – In January of this year, when T&BB interviewed Alexander Denk of Voith, we reported that the upcoming electric drive system for heavy duty vehicles will include a new inverter which will take the place of the former ‘Drive Inverter System’. At the time, we paid it little notice, but in fact the inverter is a crucial new development for the E-Mobility division of Voith Turbo. Calling it the ‘Future Inverter Platform’ (FIP), the German manufacturer plans to integrate it with prospective generations of the ‘Voith Electrical Drive System’ (VEDS). The new inverter is an overhaul of the old design, making it better suited to commercial vehicle uses and more compliant with the latest cybersecurity requirements; that is according to Manuel Calero, Voith’s new vice president for E-Mobility who came into his role in February 2023.
Lightness and compactness are key goals for the team working on the FIP. The new inverter platform, which will also comprise the drive management unit (previously separate), will weigh in at 25 kg, providing greater power density than before. In making such changes, Voith is responding to competitive pressures to cut costs and improve efficiency. In the passenger car segment, manufacturers are pushing their engineers to come up with drive systems with higher levels of integration, and this is influencing commercial vehicle design too, according to Calero.
Governments are the source of another kind of pressure. The European Commission will begin enforcing international security standards for cybersecurity, as set by the United Nations Economic Commission for Europe (namely, UNR 155 and 156), on the automotive industry from the middle of next year. In addition, road vehicles will need to meet standards for functional safety and cybersecurity engineering set by the ISO (i.e., 26262 and 21434). Every new vehicle platform introduced to the European market from mid-2024 will therefore need to be validated as “cyber secure”. Acting as both inverter and control unit, the FIP is vulnerable to hacking, and Voith therefore needs to prove that hackers will not have an open door into the electric drive’s control system. As such, the new inverter was designed from the start to be compliant with global cybersecurity standards.
Given that every VEDS application needs to meet these demands, it made sense for Voith to design the inverter as a modular component. The base inverter platform has to be integrated not only with the electric drive system, but also with the DCDC converter, charging control unit, power distribution box, and other electronics which Voith can offer to OEMs as part of a systems package. At the same time, each application requires an inverter and control unit which are optimised for the customer’s use case. It makes little business sense to design a separate inverter for every new application, and so Voith opted for a common platform which can be tweaked to suit different uses.
The VEDS is a system of systems, with each part often containing multiple subsystems. The FIP functions as a part within the electric drive system, but it is also a system in its own right, comprising inverter and control unit. Voith prides itself on its systems expertise: that is to say, its competency in integrating and harmonising separate parts so that they work together optimally. But the systems approach makes it all the more crucial that every software-controlled part measures up to the latest cybersecurity standards, given the interconnectedness and interdependence of the parts which make up the whole.
Calero told T&BB that OEMs are increasingly looking for strategic partnerships that reduce the complexities of procurement from different suppliers. The more integrated the vehicle software controls, the simpler the vehicle design and manufacturing process can be. Having a single control unit which manages all tasks at the vehicle level makes the whole more efficient, and to this end Voith is designing its future inverter platform to integrate with many different electric drive system components. “The keyword will be efficiency,” Calero said: “This can mean energy efficiency, but also efficiency in terms of vehicle software architecture, system architecture, and also implementation efficiency.”
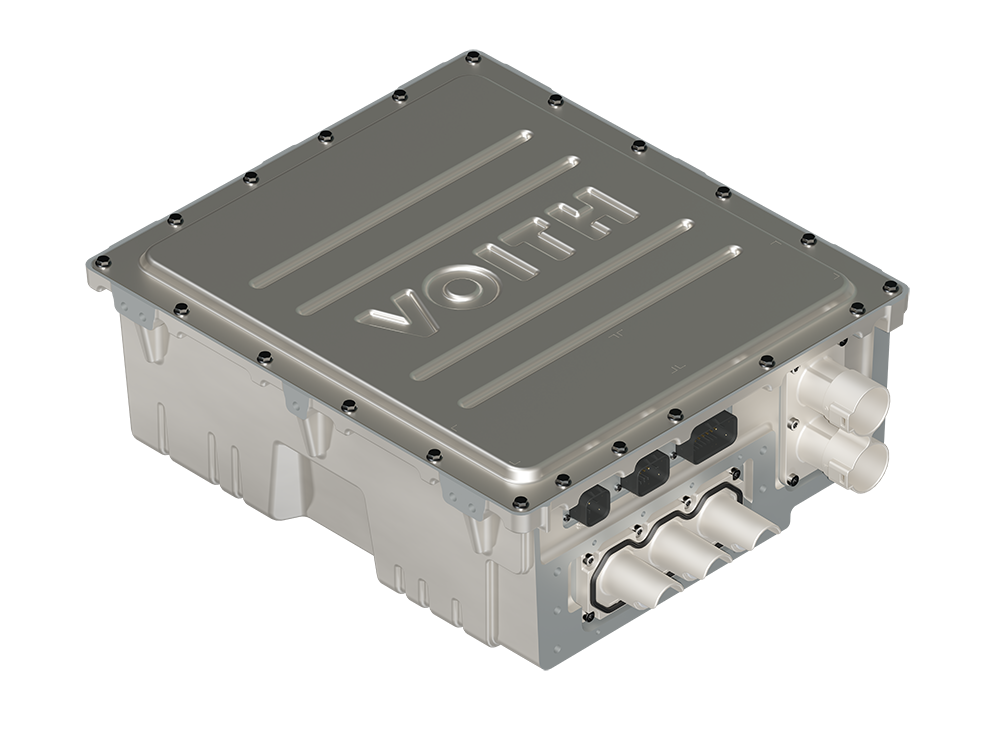
The Future Inverter Platform
Principles of the ‘Future Inverter Platform’ design
Voith’s new inverter platform is the successor to its Drive Inverter System, but the two are quite different from one another. The latter, which can be found in all current drive systems made by Voith for electric vehicles, is derived from similar products for locomotives. Voith Turbo’s involvement in rail is of long standing, whereas its electromobility business is just six years old, and so it was natural for the company to draw on its expertise in rail when it began designing electric drive systems for CVs. But the demands of rail are very different to those of the road. The components in a locomotive need to be far more robust: the warranties for rail vehicles far exceed those for commercial vehicle parts. On the other hand, size and weight are a greater consideration for commercial vehicles: “you cannot make [the component] big because you need to integrate it and you cannot make it heavy because every single kilo will have an impact on range.”
The differences between CV and rail extend beyond product design to manufacturing: “The rail business is very project-based. That means, even if you have a big project with 50 to 100 pieces, it is not comparable to the series project you will have in automotive with several thousands of units per year. That will have an impact on your industrialisation concept, which also needs to be supported by the hardware design.”
All of this meant there was considerable scope for designing a new inverter which would be specifically geared towards commercial vehicles. Development began in 2021 with the following aims: (1) make it modular and therefore capable of covering different power ranges; (2) achieve a high level of integration with the electric drive system; (3) incorporate automotive-grade software architecture.
Two design choices which aim at the second goal include making the inverter more lightweight and compact, and integrating the control unit in the same package. Calero said his team have successfully reduced the inverter system’s weight by over 50% when compared to its predecessor – from 54 kg down to 25 kg. Moreover, integrating the control unit with the inverter has reduced the design complexity of the electric drive system.
Compliance with cybersecurity standards
The third goal of the inverter development brings us to the issue of cybersecurity. The passenger car segment is several steps ahead in cybersecurity compliance, and commercial vehicles are only now catching up, Calero told T&BB. His team therefore decided it should use the very latest automotive-grade microcontrollers for the integrated circuits in its new inverter platform; a design choice which ensures that the required cybersecurity software can be easily implemented.
Before the introduction of standards for new vehicles only a couple of years ago, implementation of cybersecurity was haphazard, varying between manufacturers. This was in spite of the fact that road vehicles were incorporating more and more digital parts and systems which were connected to the internet. Thus it meant that people were driving vehicles which were potentially vulnerable to external security threats, according to Calero. A case reported in 2015 involved a Jeep Cherokee which was hijacked remotely by two men with a laptop and mobile phone. Hacking into the vehicle controls, the men gained limited control over the steering and were able to turn off the engine and activate the brakes, as well as manipulating the car radio and windscreen wipers. The Cherokee was directed into a ditch on the side of the road.
This was not a criminal case, but the result of a test carried out by Wired which was intended to highlight the potential risks faced by drivers of new vehicles with connected devices and digital control units. The eventual outcome of such concerns has been regulations which will come into effect in the EU next year, along with less robust efforts to strengthen cybersecurity in the UK and North America. In the EU, vehicle manufacturers will need to design its control systems with risk mitigation from cyberattacks built in from the start. Moreover, they will need to follow standard procedures for delivering software updates to vehicle systems over the air in order to reduce the danger of allowing unauthorised and/or malicious software from being installed inadvertently.
The risks do not come exclusively from hostile actors. Calero explained that the driver or operator of the vehicle must also be prevented from hacking into the system in order to make changes to performance. He asserted that drivers have already set a precedent for this in Germany, with cases of engine control units which have been hacked into and altered. Not only does this have negative implications for the warranty of the drive system, but it also presents a risk to the driver and to other road users where vehicle performance is made unsafe. As such, cybersecurity controls integrated into the drive system will prevent drivers from making alterations which breach regulations on functional safety.
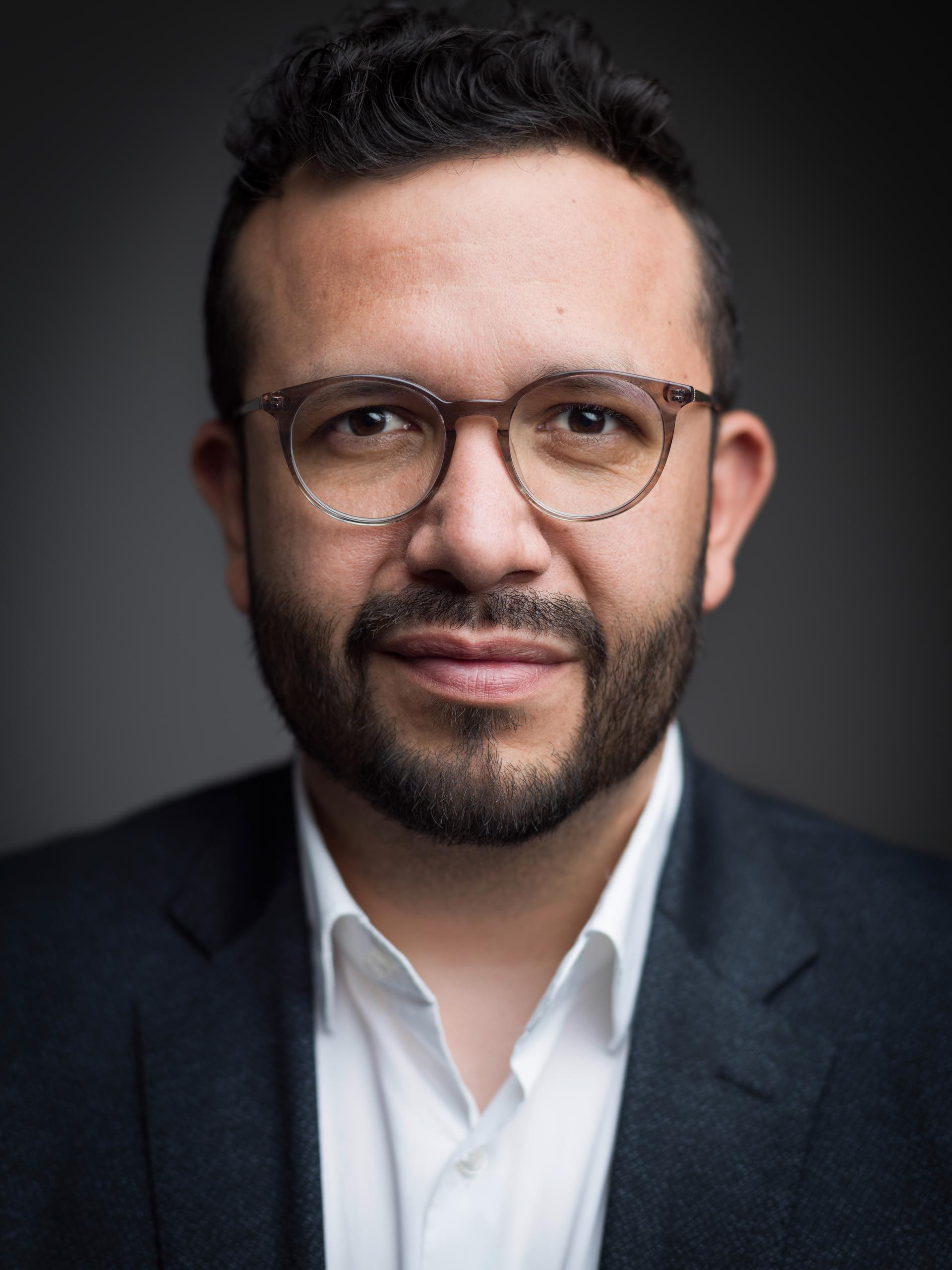
After his studies in mechatronics, Manuel Calero held various positions in system engineering and development in the field of e-mobility. Most recently, as R&D Director, he was responsible for defining the product and corporate strategy within the high-voltage inverter sector as well as the positioning on the e-mobility market. In February 2023, he joined Voith Turbo as Vice President E-Mobility.