Build it and they will come: a T&BB feature on the UTAC-FEV test centre and track in Morocco
By Bradley Osborne - 23rd January 2024
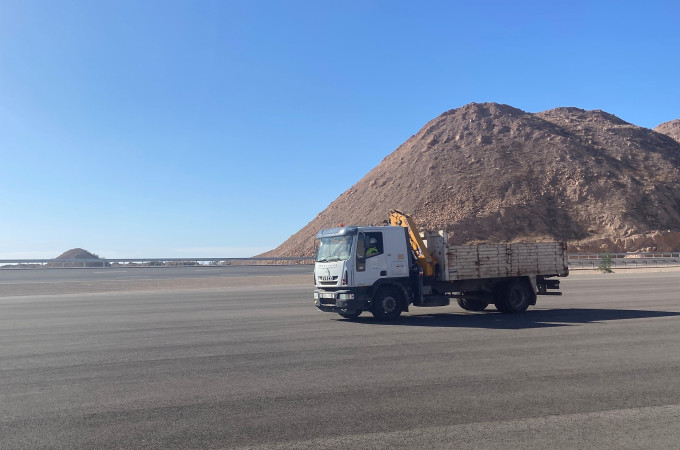
Test track at Morocco Mobility & Automotive Centre
Morocco – Build it and they will come. This is the approach being taken by the Moroccan government to grow its automotive industry, which is the largest in Africa but still modest by global standards. The kingdom already has major plants owned by Renault and Stellantis, alongside components production from European, American, and Japanese firms. Relying on foreign companies to do all the work can have variable outcomes, however: for example, a new EV plant which was proposed by Chinese automaker BYD in 2017 has failed to materialise. In that same year, the Moroccan government drew up plans for a new test track in the centre of the country, halfway between the coastal plain and the Atlas Mountains. The track, along with testing facilities and accommodation, was developed in partnership with French company UTAC Group, but the funding came from the government. At the new test centre, which was opened earlier this year and is now occupied by UTAC and German engineering firm FEV Group, Morocco hopes to build up a state-of-the-art facility capable of matching the very best in the developed world, but with the added benefit of being operable all year round at a competitive price.
The Morocco Mobility & Automotive Centre is a 500-hectare site comprising 30 kilometres of track (up to 16 configurations), two testing facilities (one leased by UTAC and the other by FEV), four workshops, and various other buildings including showrooms and onsite guest accommodation with a “hammam” or Turkish bath. It is located on the site of a former opencast or surface mine, owned by the state phosphate extraction and processing company, OCP. The mine was opened during the time of the French protectorate in 1921, and activity continued until very recently when the phosphate at the site was exhausted. Today, the test tracks weave their way between piled up mountains of earth and rubble, legacies of the site’s former use. These artificial heaps make for some picturesque scenes, and one feels both comfortably enclosed and yet infinitely remote while at the test centre, although the city of Oued Zem is very close by.
In the summer, the test centre recorded a maximum temperature of 47 degrees Celsius. At the peak of the hot weather, the asphalt can reach temperatures as high as 70 degrees. In the winter, the temperatures can fall as low as 4 degrees, but when T&BB visited in November, it was very hot and there was not a single cloud to be seen. In fact, the surrounding country, known as Khouribga, has had little to no rain for the past two years. These conditions not only make the Moroccan test centre the perfect place for hot weather testing, but they also make it suitable for outdoor vehicle testing all year round, with virtually no risk of interruption due to heavy rain or snowfall. The site is a 90-minute drive from the Casablanca airport primarily on modern and well-maintained motorways, making it easy to get to from abroad despite its remoteness.
The test centre was officially opened in January 2023, and since then, two out of the four onsite workshops have been occupied by clients (Stellantis and French engineering firm Segula Technologies) for prototype development. Swedish manufacturer Volvo has reportedly used the site already for testing its commercial vehicles. Potential customers have two options: either they can rent out a workshop and move in their own engineers and equipment, or they can employ the resources of UTAC and/or FEV. Though the test centre was described as a “joint venture” between UTAC and FEV, the current arrangement does not at all fit the legal definition of that term. Both companies lease their facilities and their access to the track and onsite accommodation from the government. On the whole, one’s impression from visiting the site is that the government is not at all involved in the day-to-day running of the test centre.
Onsite electricity is entirely sourced from a nearby dam. Surprisingly, there is little use of solar energy, although there are ongoing discussions to change this. There are 16 chargers at the centre, including two 180-kW stations, and there are plans to add 140-kW chargers. Further details on the track itself and the capabilities of the testing facilities are provided below; suffice to say, both UTAC and FEV have every intention of helping the Moroccan government to develop a test centre which can accommodate the latest innovations in electric and digital mobility.
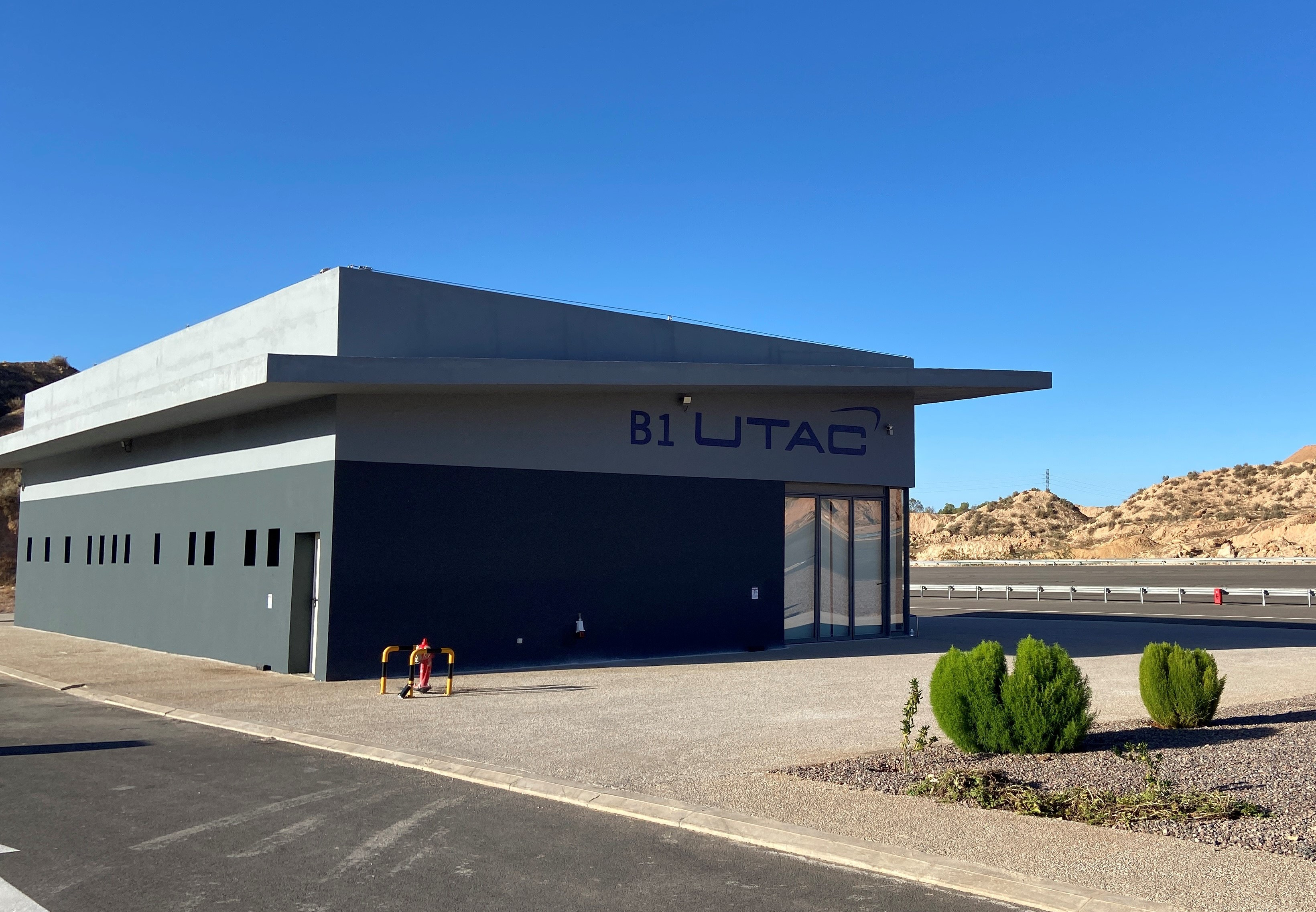
UTAC vehicle showroom
The UTAC Group was formed over twenty years ago and has become the custodian of two renowned test tracks, the Autodrome de Linas-Montlhéry in France and Millbrook Proving Ground in the UK. At these sites, UTAC can carry out electric machine, inverter, and battery tests as well as crash testing for EVs; it can test ADAS and autonomous driving through vehicle-in-the-loop and driver-in-the-loop simulation; it can test the latest electric/electronic architectures and cybersecurity at vehicle, system, and component level to ISO/SAE 21434; and it can carry out special vehicle modifications such as powertrain retrofits and conversions between left-hand and right-hand drive. It is authorised to carry out regulatory testing in accordance with EU rules, and its Linas-Montlhéry site is also the official Euro NCAP laboratory responsible for measuring vehicle safety performance. Laurent Benoit, Chairman of the UTAC Group, told press that the Moroccan centre offers “the same testing services for commercial vehicles as that of a passenger car and as that which we offer in facilities in France and the UK.” Eventually, UTAC aims to certify the Moroccan centre as an official NCAP testing site.
Alongside Millbrook and Linas-Montlhéry, UTAC owns two other sites in the UK and France: a test lab in Leyland and another test track in Mortefontaine. Cold weather testing is carried out at two sites in the vicinity of Ivalo in Finland. Moreover, UTAC has three sites dedicated to e-mobility testing, one near Frankfurt in Germany and the other two in Michigan and California in the USA. Benoit told the press that UTAC is working to offer European-like type approval and Euro NCAP certification in China, though in partnership with Chinese-owned labs. There are no plans to establish a proving ground in China in the foreseeable future.
Aachen-based firm FEV is concentrated on powertrain development and testing. With more than 300 test cells across the world, FEV can support manufacturers with hybrid systems, electric drives, fuel cell systems, and batteries in addition to conventional drivelines. The company has been present in Morocco since 2018; today, it has 150 people working in Casablanca, Oued Zem, and Tangier as well as at the test centre.
Oussama Hafsi, General Manager of FEV North Africa, told T&BB that the business in Morocco is initially focussed on those customers already with manufacturing and product development facilities in the country, which is predominantly passenger car makers like Stellantis. However, at some point in the future, it hopes to develop business in the CV segment. Commenting on FEV’s general role in the CV market, Hafsi said:
Regarding the CV segment, our core focus is on the design, prototyping and testing of IC engines and powertrain technologies, and providing engine calibrations to ensure compliance with current and next level emissions regulations. We also offer turnkey development services under our vehicle division; currently we are developing and designing a new electric truck (for a German OEM), not just the powertrain but also the total design of the truck itself.
Details of the track and testing facilities at the Morocco Mobility & Automotive Centre
As mentioned before, the Morocco test centre offers 30 kilometres of track in total and up to 16 different configurations. The longest track is the road circuit, covering 4.7 kilometres and offering multiple bends and dynamic curve zones. The road circuit is 7 metres wide and provides large side clearances. Next in length is the ovoid high speed track, measuring 4.2 kilometres and encircling eight other tracks (with a radius between 450 and 550 metres). With three lanes, the high speed track measures 12 metres in width. The maximum speed allowed on the track is 160 km/h, though exceptions may be allowed. The coast down track measures 4 kilometres and has a slope of 0.7%.
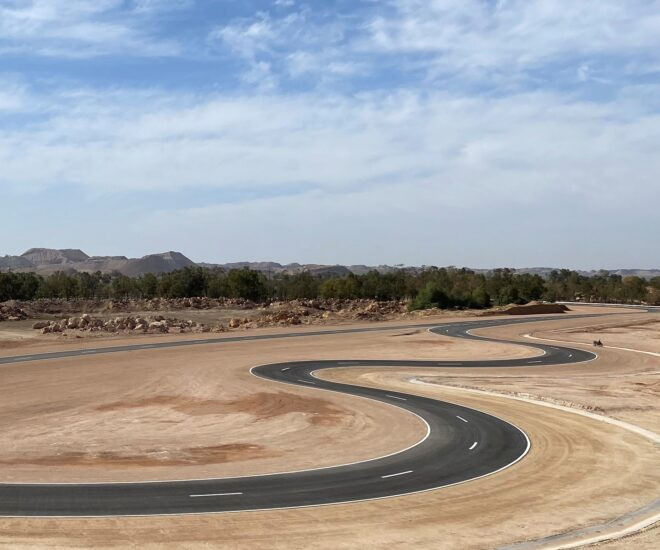
Dynamic curves on road circuit
Within the high speed track, a dynamic platform with a surface area of 70,000 square metres can be used to test active safety mechanisms, including anti-lock braking (ABS), emergency brake assist (EBS), electronic vehicle stability, steering, and other advanced driver assistance systems. Test drivers demonstrated for the press two braking tracks for testing handling on dry and wet surfaces. The dry track measures 350 metres long and 20 metres wide. The wet track is 200 metres long and 16 metres wide and offers three separate lanes: a wet grip ceramic track; a low grip track; and a track split between low grip and asphalt.
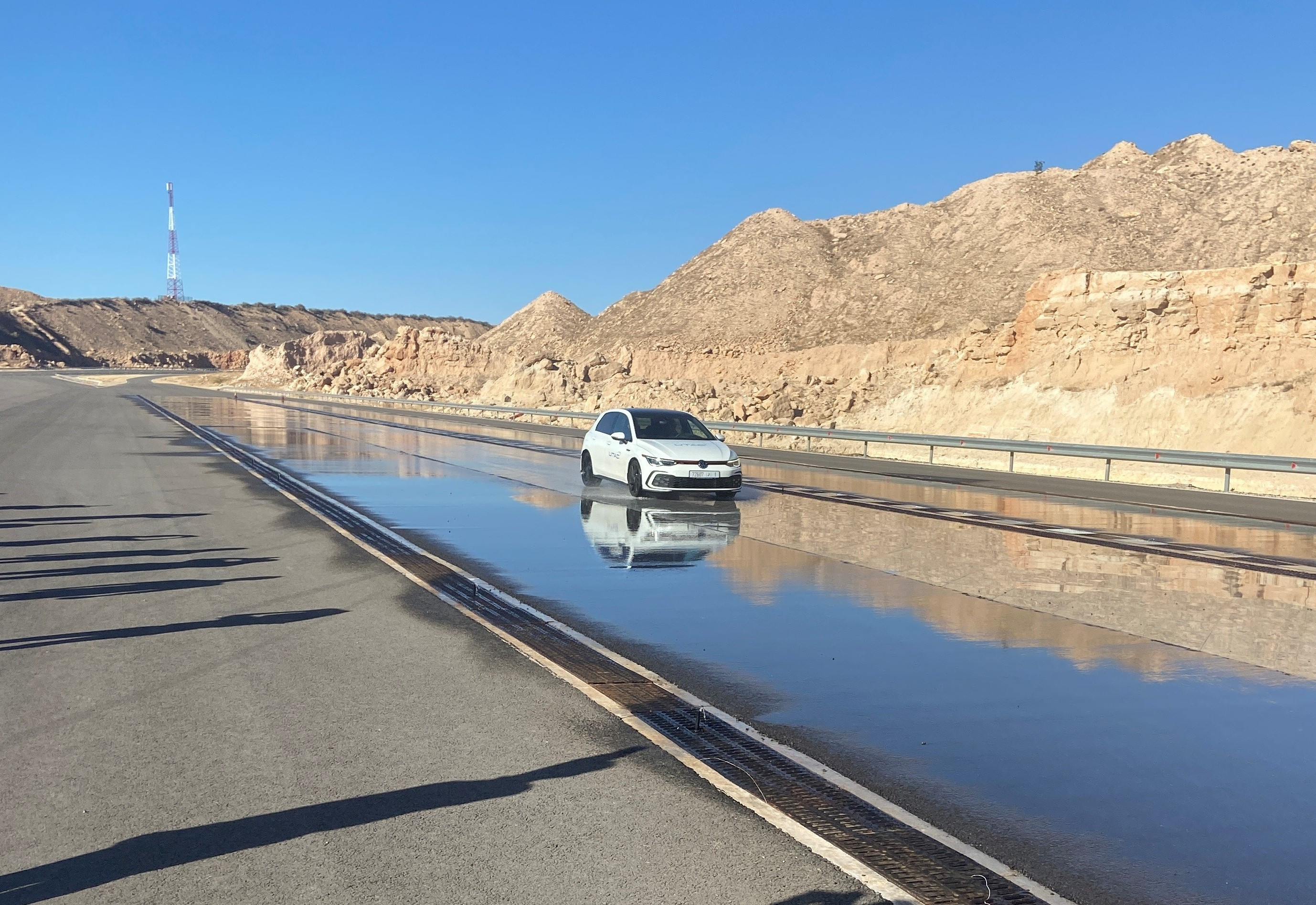
Car on wet grip track
Also within the high speed track, there is a dust track, sloped tracks, special surface tracks, and one of two acoustic test tracks at the site. The dust track is a 300-metre straight with a width of 8 metres. The sloped track section offers four slopes, three with low adhesion sections in the middle. These are (1) a 150-metre slope with 12% gradient; (2) a 120-metre slope with 16% gradient; (3) a 100-metre slope with 20% gradient; and (4) a 50-metre slope with 30% gradient (the only one without a low adhesion section). The special tracks include surfaces such as gravel, cobbles (three different patterns), humps, and corrugated sheets. There is also an acoustic tunnel and two fords, a shallow water ford and a deep water ford (as deep as 40 centimetres).
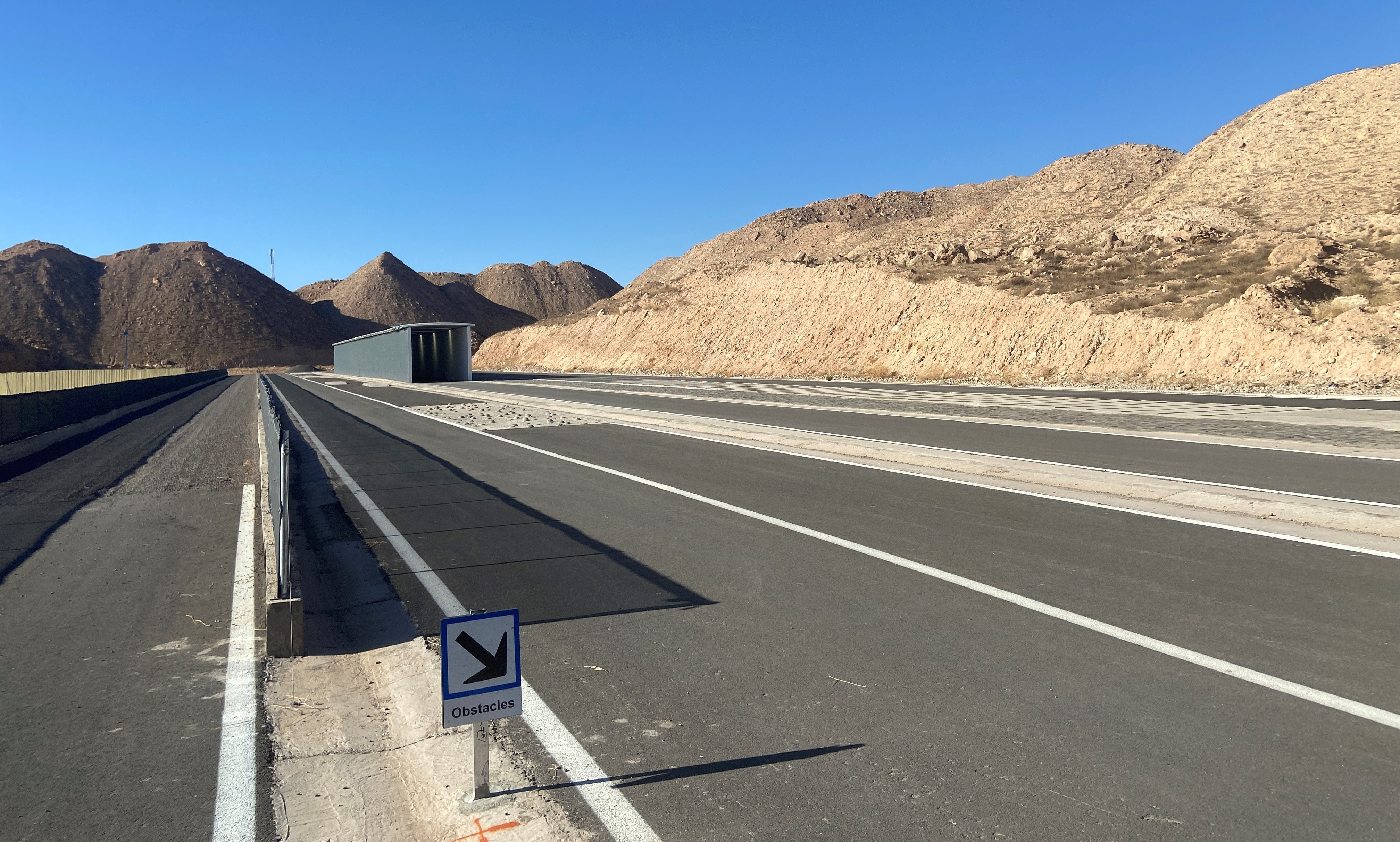
Special tracks including acoustic tunnel
The first acoustic test track is 200 metres in length and 2.4 metres wide. It is paved with five different surfaces, including Parisian paving stones, grooved concrete, and three types of asphalt concrete. This track is used for testing rolling noise, percussion, low speed vibration, and other variables. The second is an ISO 10844 acoustic approval track, measuring 500 metres in length and 5 metres in width. This track is used for homologation related to vehicle noise testing, minimum sound testing, and tyre noise testing.
There is an urban track which measures 2.8 kilometres in length and 5 metres in width, allowing for simulations of various city traffic scenarios. Finally, there are off-road tracks around the site providing rocky and hilly terrain.
Clients of UTAC can enlist the services of onsite engineers to carry out tests in two facilities. The main facility comprises offices and meeting rooms as well as workshops and car lifts, while the other incorporates three maceration boxes: one between -30 degrees and 60 degrees Celsius with controlled humidity, and two between -20 degrees and 40 degrees Celsius. Next year, UTAC’s facilities will include a rain chamber, a sunshine chamber, and a dust chamber. Alternatively, customers may rent one of four workshops for their own use, with private entrances and dedicated confidential car parks. These vary in size between 160 and 240 square metres and incorporate offices and kitchenettes as well as workshop spaces. Two of these are currently let.
Members of the press were shown around the FEV engine testing and vehicle emissions facility, including a chassis dyno for passenger cars and light duty trucks (5 tonne maximum, 3-metre height by 7-metre length). The facility is split into several chambers, including a soak room, a vehicle workshop, a cooling box, and a humid controlled zone. The cold boxes are used for cold start and warm-up calibration, going down to -20 degrees Celsius. The soak room is 23 degrees and incorporates temperature boxes between -20 and 50 degrees. Along with the chassis dyno, there are multiple engine test benches (250 kW dynos) for performance and emissions testing up to Euro 6d. The total value of all the equipment in the FEV building is EUR12m.