From passive to active: Martin Mayer talks to T&BB about ZF’s ADAS suite for General Safety Regulation II
By Bradley Osborne - 27th February 2024
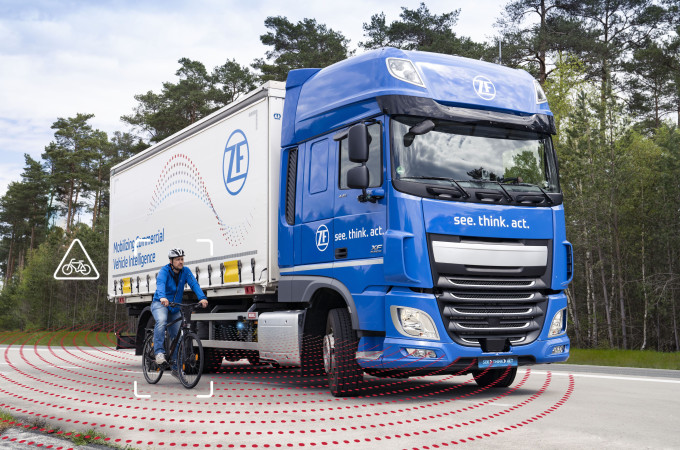
Visual of ZF's Blind Spot Information System
Germany - From 7 July this year, all newly registered vehicles in the European Union must comply with the second tranche of rules known as the ‘General Safety Regulation’ (“GSR II”). These regulations will require all new road vehicles to be installed with more advanced driver assistance systems (ADAS) which employ some of the latest innovations being made at the cutting edge of artificial intelligence. These include systems for intelligent speed assistance; reversing detection with cameras and/or sensors; attention warnings in case of driver drowsiness or distraction; event data recorders; and emergency stop signals. For buses and trucks, the regulations are more stringent: in addition to the aforementioned systems, they must also come with blind spot detection, collision mitigation, and tyre pressure monitoring.
Recently, Truck & Bus Builder spoke with Martin Mayer, who is Head of Global Product Segment ADAS & Electronics at ZF Group, about the upcoming safety regulations. Mayer made it clear, however, that there is more to ADAS at ZF than merely assisting OEMs with regulatory compliance. Far from being a box-ticking exercise, ADAS development is at the forefront of vehicle design: future products will not only make trucks and buses easier and safer to drive; they will also pave the way for semi- and even fully autonomous vehicles.
In Mayer’s opinion, widespread use of self-driving vehicles in complex urbanised areas is still years into the future. The development and deployment of autonomous vehicles is very expensive and complex and requires vast amounts of computing power per vehicle. On the other hand, ingenious safety and assistance systems which afford the vehicle a degree of autonomy are already available and can be integrated in existing vehicle models. The “robotaxi” hype of ten years ago has died down somewhat, as software engineers discover the magnitude of the task they have set for themselves in eliminating the driver altogether from the equation. In the meantime, ADAS is gradually taking more and more work out of the driver’s hands without making him entirely redundant.
When talking about vehicle autonomy, we normally refer to the scale of “levels” (0-5) formulated by the American Society of Automotive Engineers (SAE). Vehicles with cruise control, automated lane keeping, and/or automatic emergency braking are at Level 1 on the SAE scale. In the interview, Mayer spoke frequently about “Level 2+”: that is to say, vehicles which will allow the driver to take his hands off the steering wheel (Level 2) and his eyes off the road (Level 3) in certain situations. To allow for such scenarios, ADAS must be capable of monitoring the road and taking action to avoid accidents with minimal driver intervention. To elaborate on ZF’s current motto (“See. Think. Act.”): ADAS must enable the vehicle to perceive its environment and the other road users around it, to quickly make an appropriate decision, and to act immediately on that decision.
For Mayer, the purpose of ADAS development is absolutely clear: the ultimate aim is to eliminate road accidents altogether. By replacing or enhancing the driver’s ability to perceive and respond to hazards, ADAS could minimise the repercussions of human error. However, it is impossible to put a date on when technology will have evolved enough to remove human error entirely. In any given road scenario, there are so many unpredictable elements at play that even the most advanced self-driving vehicle conceivable would struggle to interpret and respond to accordingly. Nevertheless, the target of zero accidents remains “absolutely important” to Mayer.
When discussing different applications for ZF’s ADAS technology, Mayer described three types of OEM customer which he normally encounters: those seeking components only, those requiring subsystems or those needing complete systems. The components only customers produce most of their truck technology inhouse, and often develop their own systems. They approach ZF simply as a supplier of specific components, such as cameras and sensors. The subsystem customers need more help in developing their ADAS technologies and may contract ZF to develop specific systems which they cannot or do not wish to do for themselves. The complete system customers require entire ADAS systems from ZF for integration in their vehicles – these tend to be manufacturers of buses or specialty trucks. One of the unique points in ZF’s favour – thanks to its acquisitions of TRW and then WABCO in 2020 which enabled it to expand its portfolio – is that it is able to supply OEMs with a complete suite of ADAS products, from emergency braking systems and intelligent speed assist systems to turn assist, and it can even support the customer in homologating new vehicles.
Background to ADAS development at ZF
The first raft of regulations retrospectively known as “GSR I” came into effect over ten years ago. These required OEMs to incorporate automatic emergency braking and lane keeping systems in their commercial vehicles. In response to GSR I, ZF developed its AEBS and lane departure warning technologies, and it pioneered “data fusion” between the camera and the radar. It was one of the first companies to produce automated braking systems which could take and compare data from camera and radar, improving vehicle perception and thus making the system more reliable. Following the implementation of GSR I, ZF continued to work on the ADAS products developed for it. By 2018, Mayer says that the ZF system (which used brakes supplied by WABCO before it was acquired by ZF) ’was capable of decelerating from 80 kph on their own, exceeding the requirements of EU regulations at the time.
According to Mayer, the reason why ZF originally entered the ADAS market was to address the problem of heavy truck accidents. While collisions involving heavy trucks are rare, when they do happen, they can be acutely severe and more often lethal than those involving just cars. Judging that many of these accidents were due to human error, ZF began developing its first mitigation systems, including automatic emergency braking. These initial forays into ADAS took advantage of early vehicle perception technologies that had been developed for a different purpose: functions such as adaptive cruise control which were made to improve driveability.
By the time that rumours of GSR II were beginning to circulate, then, ZF was already iterating and innovating upon the ADAS products it had under its belt. Mayer told T&BB that ZF began working on ADAS technologies specifically for GSR II in 2020, though this was before the parameters of the new regulations had been finalised. In any case, ZF’s vision “towards zero accidents” meant that it continued developing its ADAS portfolio to improve its functionality and robustness. In 2022, newly homologated vehicles in the EU needed to comply with GSR II, and later this year newly registered vehicles will need to comply as well. Mayer said that, since 2020, ZF has invested “significantly” in ADAS development.
ZF’s product suite for GSR II
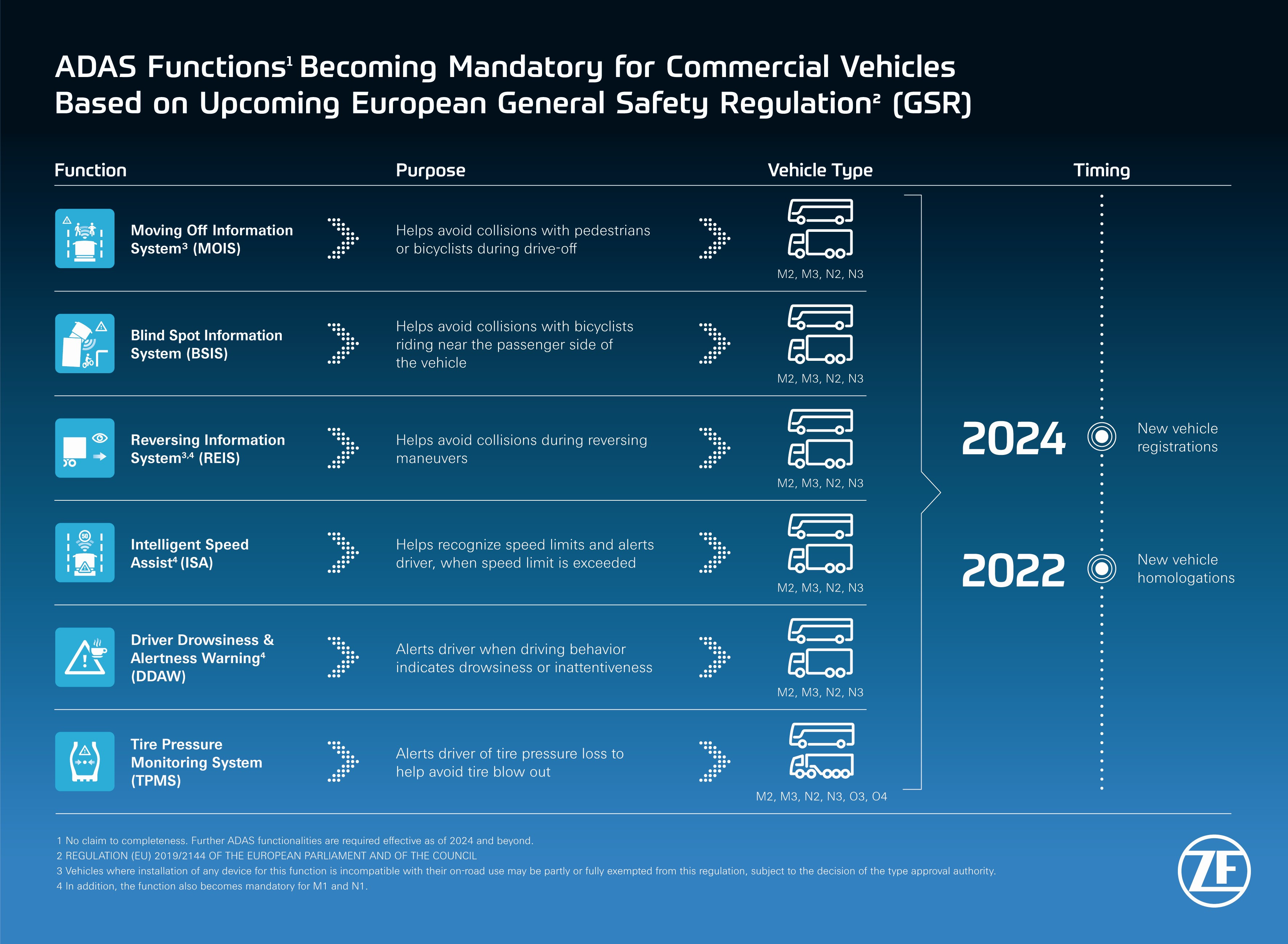
The image above shows six ADAS functions which will become mandatory for trucks and buses in the EU and for which ZF is able to supply components and systems to OEM customers. In our conversation, we focused on three functions: blind spot information systems, moving off information systems, and driver drowsiness and alertness warnings.
ZF’s ADAS technology for trucks is exemplified in the ADAS GSR II Suite which includes a combination of sensors, software, and automatic braking allowing it to meet, and in many ways, exceed many of the requirements of GSR II. The system is geared towards assisting the driver with “moving off”, or starting up the vehicle after pausing at, for instance, a pedestrian crossing. If the system detects a road user such as a cyclist in front of the vehicle or in close proximity to the vehicle sides which may be in the driver’s blind spot, it will alert the driver with a visual, acoustic or haptic warning.
The chipset in ZF’s cameras for blind spot and moving off systems are supplied by the Israeli tech company Mobileye. The chipset and perception software is married together with the functionalities of OnGuardMAX to make the ADAS work correctly and effectively. ZF opted for Mobileye’s technologies as its perception algorithms were not something that ZF was keen to replicate itself. “The investment to develop such an algorithm from scratch is huge,” Mayer said, requiring hundreds of people and thousands of manhours, to say nothing of cost, to develop to the level required for commercial use.
Such safety systems attempt to overcome the limitations of the driver’s perception, bringing his attention to hazards which he cannot see. The driver drowsiness and attention warning system, on the other hand, address the limitations of the driver himself. If it detects that the driver is distracted or inattentive, it gives a warning. The nature of the warning depends on the OEM’s preference, though Mayer argues that haptic feedback, such as vibrating the seat or the steering wheel, is the most effective at getting the driver’s attention. The system determines whether the driver is becoming less attentive to the road through data from two sources. The front-facing camera monitors the vehicle trajectory, while a sensor on the steering wheel monitors the turning angle. Using these two sources, the system continuously judges the behaviour of the driver and will activate the warning if, for instance, the vehicle is starting to veer off course in an unusual way.
ZF deliberately chose to monitor vehicle behaviour as a means of detecting drowsiness or inattentiveness instead of monitoring the driver himself. Mayer emphasised that this is not because ZF judged the latter approach to be inferior. In fact, the company is continuing to work on a system which does take the driver into account – for instance, by monitoring eye movement and facial expression. However, the system which it has developed based on monitoring the vehicle is sufficient to comply with the requirements of GSR II. ZF intends to implement a driver monitoring component into the system later in the decade. First of all, though, it must overcome a series of challenges which, though they appear simple, are in fact rather complicated. One is the placement of the camera which is to monitor the driver’s face. Truck cabins can vary widely in their configuration, with different dashboards, seating positions, and steering wheel mountings depending on the make or the application. “To find a common place for a camera which works for every variant is complicated,” said Mayer. “Some customers, for example, have more than 250 different truck and cabin variations!” The other difficulty is getting drivers accustomed to a camera trained constantly on their faces. “There’s always the quite natural concern that maybe the boss can record what they are doing,” Mayer explained.
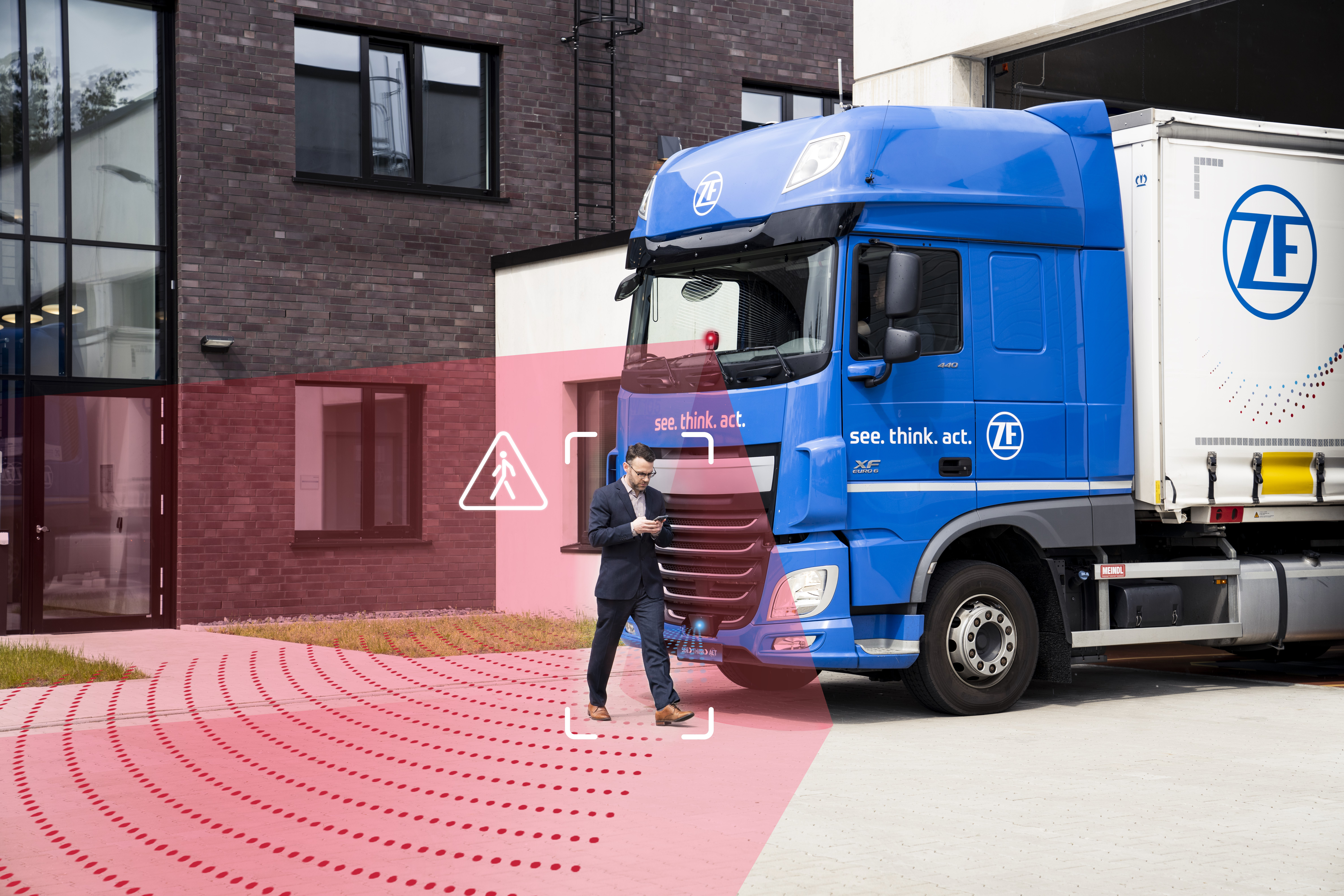
Visual of ZF's Moving Off Information System
Current and future applications of ZF ADAS
It is understandable why drivers would take umbrage with bosses potentially monitoring them in the truck cabin. But even less egregious ADAS systems can draw the ire of drivers. Mayer pointed out that a plethora of assistance systems can end up being a hindrance rather than a help. He recalled a conversation with one driver who said he wanted the aftermarket system fitted on his bus to be thrown away as it was causing him too many distractions. Drivers “don’t like to have 25 different kinds of system, 40 mirrors, 20 monitors, and so on,” said Mayer. Moreover, certain aftermarket systems can, in Mayer’s experience, be actively unhelpful, beeping and buzzing constantly while picking up non-existent hazards (or, conversely, not detecting real hazards). If ADAS technologies are to fulfil their purpose – making roads safer – it is crucial that drivers are able to understand how they work and rely on them without being overwhelmed by them.
In practice, this means fitting each safety system to suit its intended application. There is no one-size-fits-all approach to the problem of vehicle safety, with each vehicle segment and application presenting its own challenges. For example, the EU’s stipulation for advanced emergency braking in every new road vehicle does not apply to city buses: the reason being, a short, sharp brake automatically applied could throw passengers forwards and cause injuries. ZF’s ‘Collision Mitigation System’ (CMS)1 designed specifically for city buses avoids this with an adapted braking system. Instead of applying a hard brake, the system first gives a small “pulse” or “jerk” to warn the passengers, allowing them to grab a handrail or sit down before a second, harder brake is applied. The idea is that the system will brake enough to decelerate the vehicle and avoid or mitigate an accident without harming passengers.
As is often the case in the industry, the technological development is driven by the highest volume segment, that is to say the passenger car segment, where ZF, of course, has a strong presence. This has enabled ZF to achieve greater economies of scale when it comes to development costs as well other advantages such as reducing the time to market for new solutions.
That being said, there are some important differences between passenger cars and commercial vehicles with respect to ADAS technology. For one thing, ADAS in cars has been driven more by consumer demand than by regulation: for instance, the safety assessments of Euro NCAP are voluntary and differ from the mandatory type of approval process. ADAS in heavier vehicles is driven more by legislation. Automatic emergency braking, which has been required in new trucks for over a decade, have only just become mandatory in cars with the implementation of GSR II. Moreover, developing a system which is robust enough to withstand the rigours and demands of commercial vehicle applications – for example, a truck working on a construction site or travelling long distances all year round – requires a lot of extra work which is not required for developing a system which passes muster for the passenger car segment.
Nevertheless, ZF has the advantage of leveraging the higher volumes as well as the shorter development cycles for cars to advance the development of its ADAS systems for CVs. Many ADAS technologies begin as products for cars; however, the commercial vehicle division at ZF contributes its ideas and requirements at an early stage to ensure that such products can be redesigned later for heavier vehicles, Mayer told T&BB. Giving a rough estimate of how much crossover is possible between car and CV, Mayer said that about 50-60% of the technology developed for cars can be carried over to trucks and buses. The shortfall represents the tougher working conditions and the greater demand for robustness and safety which any product developed specifically for commercial vehicles must be able to address.
Mayer expects that, in the future, divergence of technologies and segments, rather than convergence, will be the name of the game. Companies such as ZF will continue to adapt their ADAS products to different applications, such as for trucks, city buses and coaches. But there is one trend which, in Mayer’s view, encompasses every segment. As safety systems become more sophisticated, they will also become more active. Systems which are passive today will be in control tomorrow; warnings will be accompanied or replaced by interventions. Certainly, this is the direction of travel for ZF’s ADAS division; and as the technology evolves, it will increasingly take over from the driver, making and enacting decisions which, Mayer hopes, will make our roads safer.
1 See the original announcement from 2022: https://truckandbusbuilder.com/article/2022/05/18/zf-developing-new-collison-mitigation-system-for-city-buses
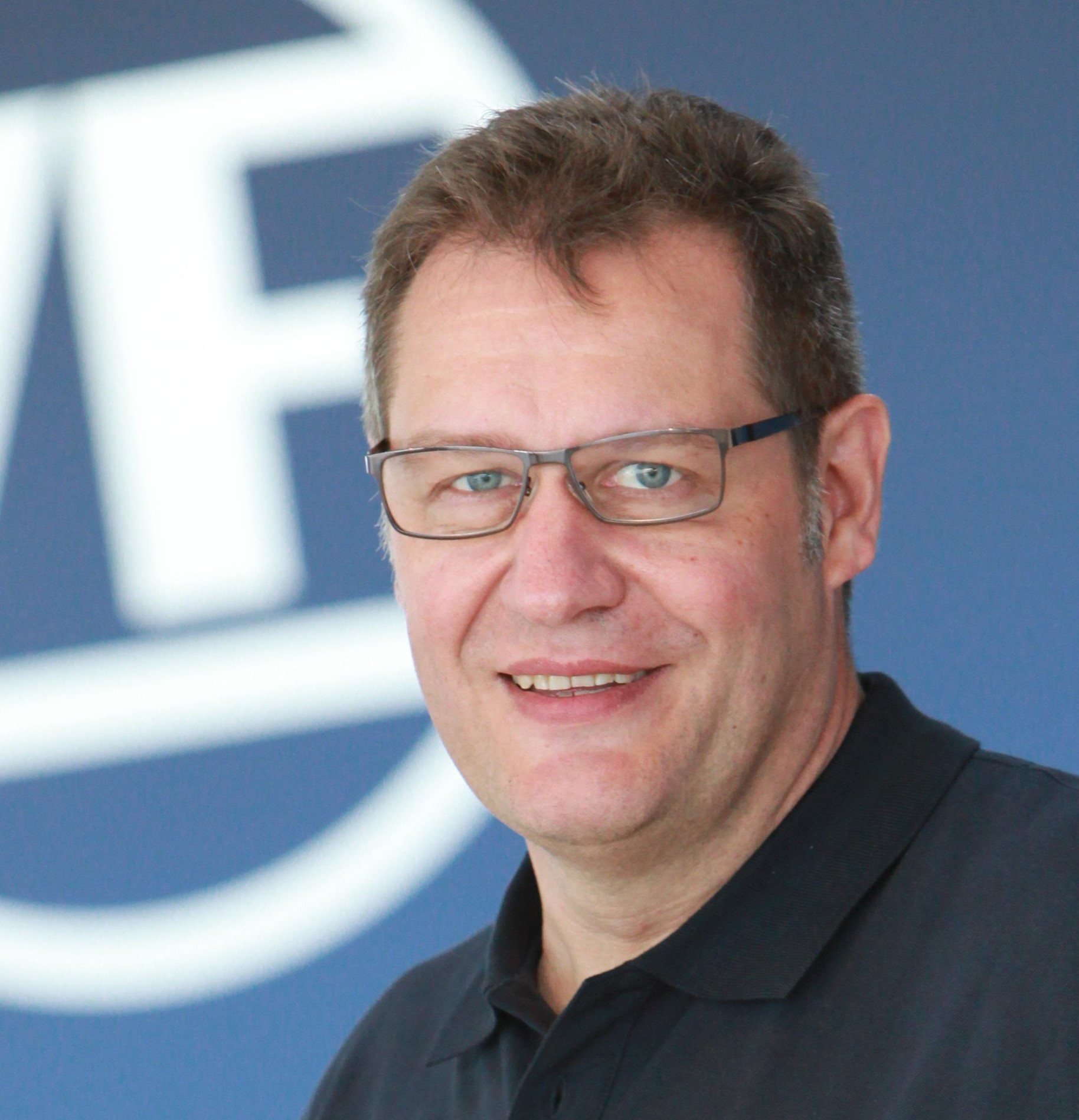
Martin Mayer has been Head of the Global Product Segment ADAS & Electronics for ZF’s Commercial Vehicle Solutions (CVS) Division since 2022. Prior to this, he managed the ADAS Sensors product portfolio within the company from 2019 to 2021, after working as a development engineer and development manager for passive safety electronics as well as technical sales director for ADAS Sensors at TRW Automotive. Mayer studied electrical engineering and electrical communications engineering (Dipl.-Eng.) at the University of Applied Sciences in Konstanz, Germany. Mayer has also chaired the Euro NCAP HDV (for heavy vehicles) working group at the European Association of Automotive Suppliers (CLEPA) since 2023.