From industrial to operational reality: T&BB report from Electromobility Days at Renault Trucks
By Bradley Osborne - 8th October 2024
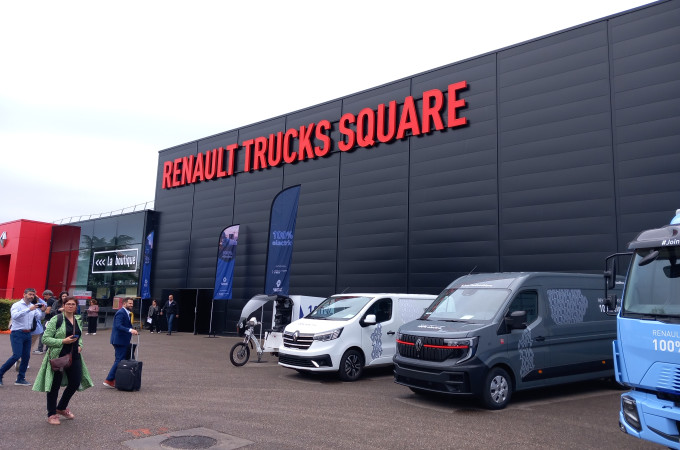
Renault Trucks Square in Vénissieux
France – In July, Renault Trucks SAS hosted journalists in Lyon, France for a media day packed with presentations, workshops, a factory tour, and a ride and drive. No substantial announcements were made; instead, the point of the event was to show how Renault Trucks’ efforts to switch to electric vehicle production have moved from an “industrial and commercial reality” to an “operational reality”.
What is meant by this is the following. In 2020, Renault Trucks began series production of its first battery electric truck ranges, the medium- to heavy-duty ‘D’ and ‘D Wide’. At the end of last year, serial production of the heavier ranges, the ‘C’ and ‘T’, was initiated. In the intervening period between the launches of the D and D Wide and of the C and T, Renault Trucks came up with a new brand – ‘E-Tech’ – to promote its battery electric vehicles. As of July, the French manufacturer had 1,317 electric vehicles1 in total on European roads, and it expects to reach a 2,000-unit production milestone at its Blainville-sur-Orne factory for the E-Tech D and D Wide ranges before the end of the summer. Production and sales of the battery electric truck ranges are thus well underway. Now, Renault Trucks is focused on supporting customers with the switch to electric, and to this end, it has embarked on a project to decarbonise its own logistics.
Every day, axles produced at the Renault Trucks plant in Vénissieux, situated in the Lyon metropolitan area, are transported ninety kilometres by truck to the assembly plant in Bourg-en-Bresse, where they are fitted on the C and T ranges. Renault Trucks’ ambition is to use electric trucks exclusively for its own logistics in Europe by 2030, but it is beginning with this relatively short route, which is nonetheless a significant contributor to the manufacturer’s carbon emissions in its Lyon operations.
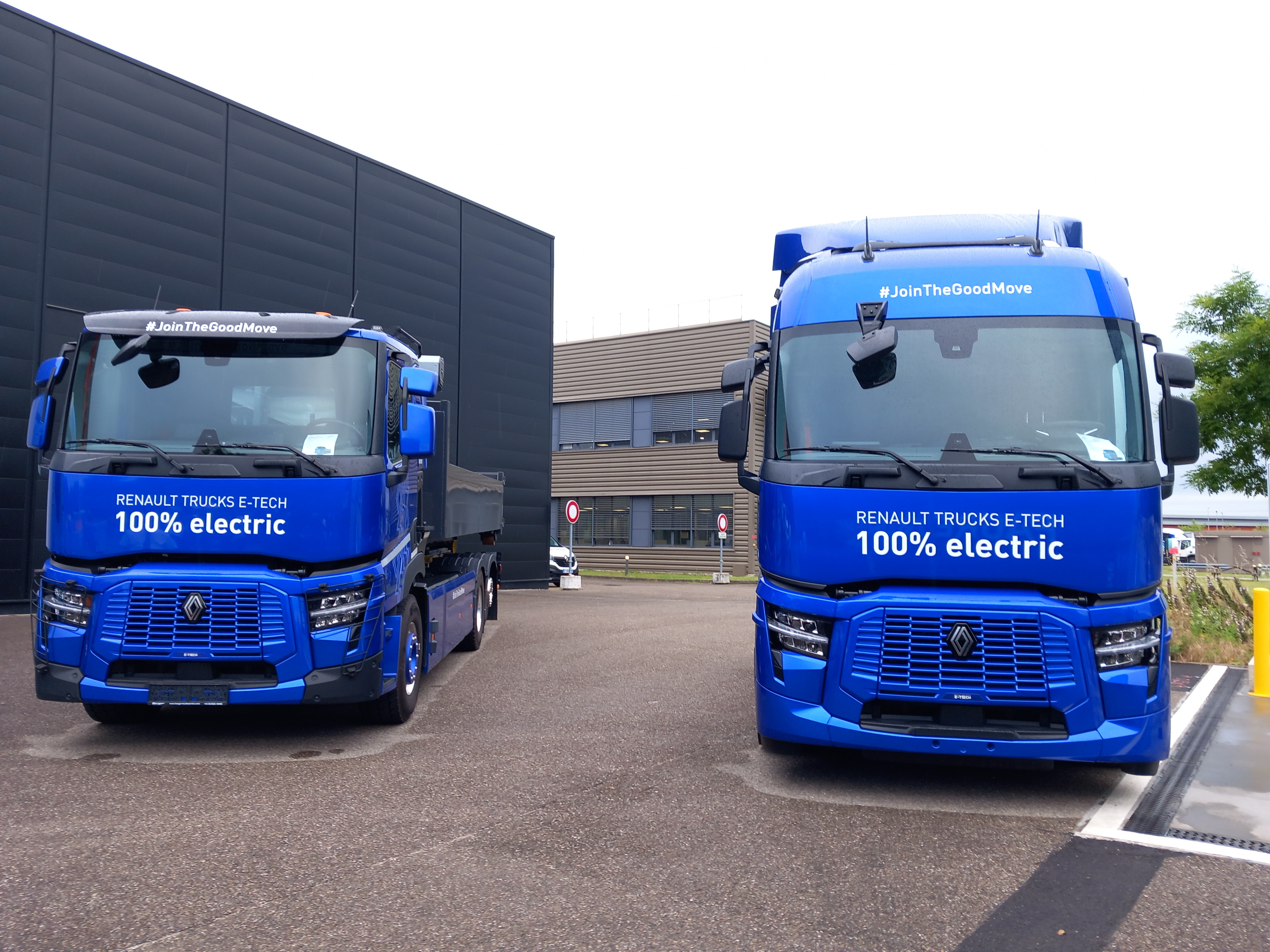
Renault E-Tech C, left, and E-Tech T
To fulfil its goal, Renault Trucks has deployed five 4x2 E-Tech T trucks, which each carry a 22-tonne load on two round trips (i.e., 2 x 180km) between Vénissieux and Bourg-en-Bresse every day. Using its own software to calculate the energy required to complete the mission – taking into account the topography of the route, the trucks’ energy consumption when laden, and the outside temperature – Renault Trucks worked out that each truck would use between 420 and 450 kilowatt hours to complete the two trips.
At the manufacturer’s headquarters in Saint-Priest, located nearby the axle plant in Vénissieux, we were shown two 360-kW charging stations installed by Power Electronics which can recharge up to four trucks at a time. Between the first and the second trip, the driver takes a break while the truck batteries are topped up with energy (45-50 minutes). Overnight, the trucks are charged to full at the operators’ depots.
The experiment of decarbonising the logistics flow between Vénissieux and Bourg-en-Bresse has only just begun. However, it comes at a cost: Renault Trucks estimates that the price of using electric trucks in the place of diesel ones on this route is as much as 40% higher. On the other hand, it expects to bring this down to around 12% by making adjustments to the trucks and to the operation over the next six years. The data and experience it will gain from this project will help it in decarbonising lengthier routes. At Bourg-en-Bresse, we witnessed trucks bringing in cabs built at Blainville-sur-Orne, having travelled many hundreds of kilometres from Normandy in the northwest to Lyon in the southeast of the country. Renault Trucks expects it would need a relay system of electric vehicles to transport goods over such a long distance. The experience also informs its customer service: pre-purchase, it devotes around nine months to helping customers decide what sort of electric truck they need to do the required job.
1 This apparently includes the ‘E-Tech Master’ and ‘E-Tech Trafic’ van ranges which are sold by Renault Trucks under the ‘Red Edition’ badge.
Project Oxygène
Parked alongside the charging stations in Vénissieux was a prototype truck with an unusual design. Based on the 16-tonne D model, the battery electric ‘Oxygène’ truck is one of three prototypes which Renault Trucks has made so far through its project partnership with logistics firm Geodis.2 The project brief was to develop an electric truck for use in urban deliveries. As such, the truck on display had an energy capacity of 200 kWh, providing a range of 150 kilometres – exemplifying Renault Trucks’ design principle, that the battery configuration should meet the requirements of the intended application. Indeed, the 150-km range, while modest, far exceeds the original target of 80 kilometres. With a rigid box van body, the truck offers a payload of six tonnes.
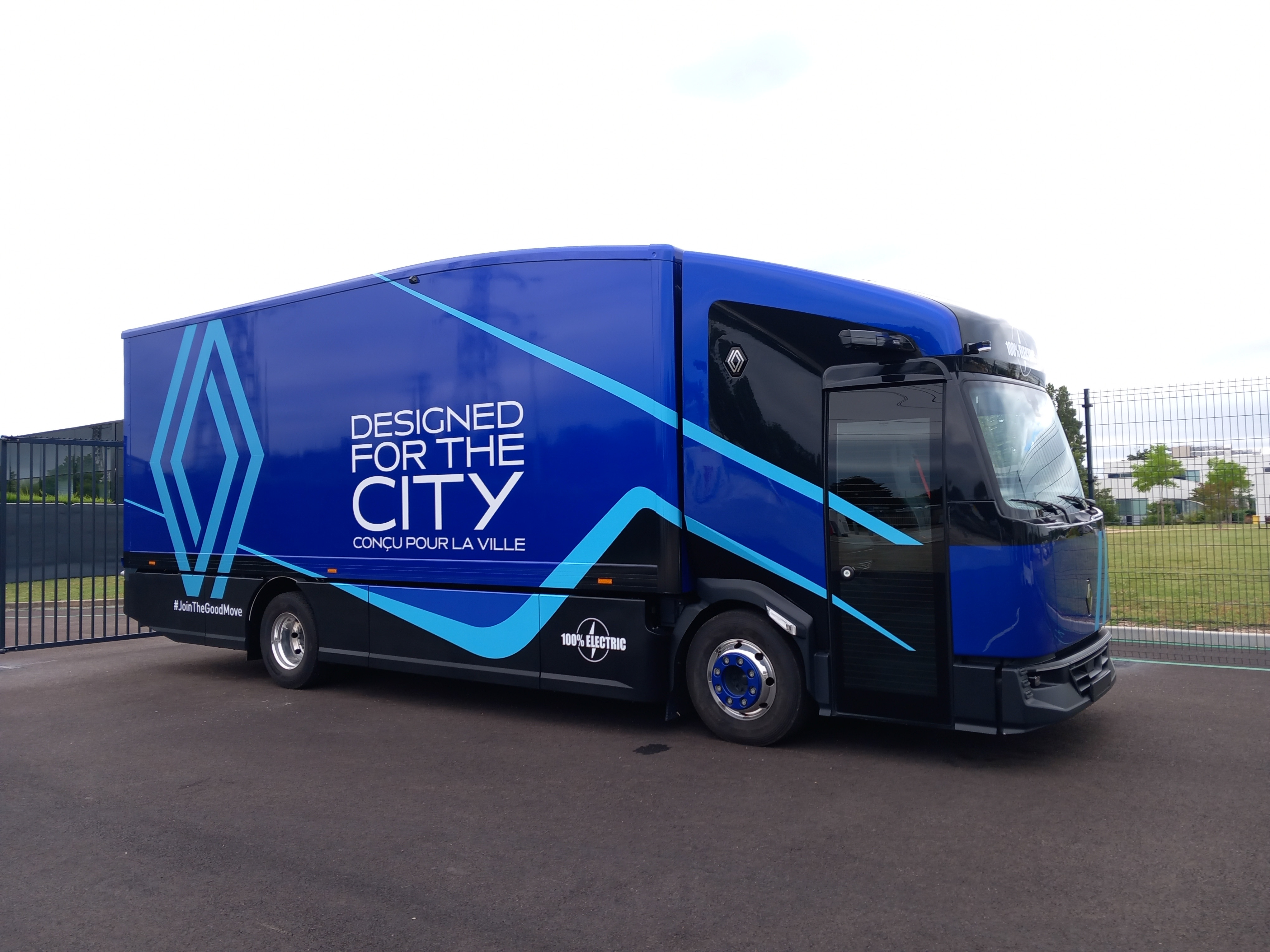
Oxygène prototype truck
The focus of our interest, however, was on the cab, which boasted some unusual design choices. The most apparent feature of the cab was its large windshield which offers, in combination with mirror-cameras, 360 degrees of visibility to the driver. One of the original design briefs was to achieve a five-star Direct Vision Standard (DVS), as defined by Transport for London. This measures how much the driver can see without the aid of mirrors or cameras; hence, the “glasshouse”-style cab offering an almost-wholly unobstructed 180-degree view from the driver’s seat. (From October, heavy goods vehicles operating in London will require at least a three-star DVS rating by law.) Another unusual aspect of the cab design was the passenger door which, instead of opening outwards, slides across the side of the vehicle. Renault Trucks wanted to not only eliminate the risk of hitting a passerby when opening the passenger door onto the pavement, but also to make entry and exit from either side as easy as possible. To this end, Renault Trucks also lowered the access height on both sides.
The Oxygéne truck was built with urban logistics in mind: hence, its cab was designed to make frequent delivery stops easier for the driver, and to enlarge his view of the street around him as far as possible. One 26-tonne and two 16-tonne prototype trucks have so far been built at Blainville-sur-Orne. The 26 tonner is a refrigerated truck with a greater energy capacity (282 kWh) to power the refrigeration unit while maintaining the 150-kilometre range. This variation on the Oxygène design is entering a customer trial in October: SVZ will drive it for supermarket chain Jumbo on the streets of Amsterdam.
2 The project was first announced in 2022; see our original report: https://truckandbusbuilder.com/article/2022/04/02/renault-trucks-and-geodis-to-develop-16-tonne-electric-truck-for-urban-use
Future plans at Bourg-en-Bresse
After looking around the Oxygène truck and going for a ride in a E-Tech T, we were whisked off to Bourg-en-Bresse, where the company assembles its heavy-duty truck ranges. Here, Renault Trucks is approaching the end of its project to adapt the plant to electric vehicle production. When it is finished, all trucks will be entirely assembled on the same production lines, regardless of driveline.
Established in 1964, the Bourg-en-Bresse site today covers 117 hectares and employs 1,428 permanent workers, with a pool of around five hundred temporary staff to draw from. Besides the truck assembly lines, Bourg-en-Bresse is also home to Renault Trucks’ “refactory” for the refurbishment of used trucks. Solar panels covering around 17 hectares of roof space are currently being installed.
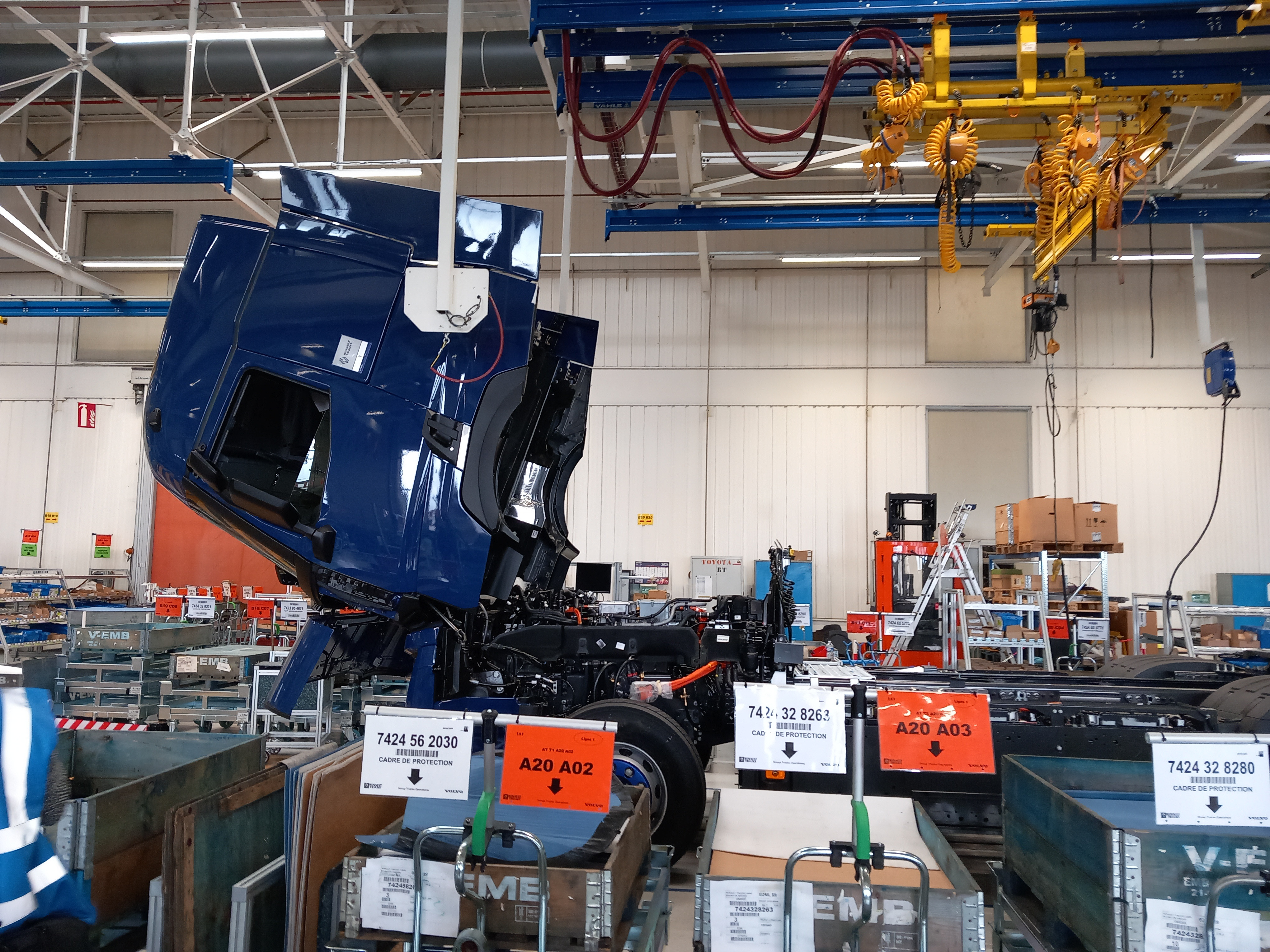
Renault E-Tech truck on 'finishing' line
On two parallel assembly lines – one of which is dedicated to 4x2 tractor units – Renault Trucks builds its T, C, and ‘K’ ranges. These have the capacity to produce around 115 trucks every day. The company is in the process of adapting these lines to accommodate battery electric models alongside the conventional diesel ones. As of July, this work was 95% complete. In another area of the facility, the battery electric trucks are “finished” separately from their diesel counterparts with the installation of certain components. However, Renault Trucks’ aim is to remove the need for this discrete “finishing room” entirely.
Series production of the E-Tech T and C ranges began at the end of last year. Renault Trucks has invested EUR70m so far in its Bourg-en-Bresse factory to adapt it to electric truck assembly. A further USD30m will be spent to finish the job, which includes a significant expansion of the parts warehouse to accommodate the new electric powertrain components required.
During the morning press conference, Emanuel Duperray (Senior Vice President, Electromobility), Marc Lejeune (Business Intelligence Director), and François Savoye (Vice President, Electromobility Solution Offer) discussed the company’s current electric truck portfolio. With the introduction of the E-Tech T and C, they are now confident that its electric vehicles can cover 75% of the applications for which heavy trucks are typically used. They admitted, however, that some heavy-duty and long-distance missions would not be feasible even with the E-Tech T or C trucks. Consequently, they announced that, in 2026, Renault Trucks would bring out vehicles which would be capable of covering 600 kilometres on a single charge, powered by 800-kWh batteries and a new electric axle (developed in-house).
The men stressed that a long-distance e-truck would complement, not replace, the models which are already available. In the meantime, Renault Trucks is squarely focused on squeezing as much out of its current products as it can, making clever use of digital tools to effectively plan and execute their delivery routes. The company’s electric trucks have moved from industrial to operational reality: Renault Trucks’ conviction is that each model will fulfil its potential, provided each one is smartly adapted to its intended application.