Cummins opens new R&D testing facility in Darlington: a T&BB feature
By Bradley Osborne - 15th October 2024
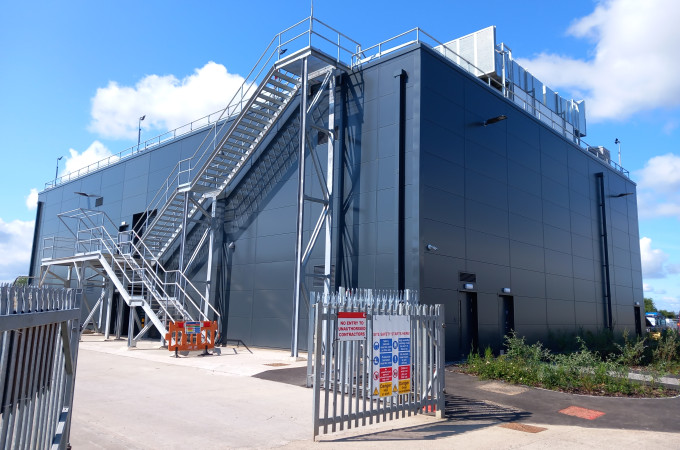
New R&D facility at Cummins site in Darlington, UK
UK – In July, American powertrain manufacturer, Cummins Inc, opened a new test facility at its engine plant in Darlington in the northeast of England, with the attendance of T&BB and other members of the trade press.1 The company has carried out engine testing at Darlington for many years, but the new facility represents a definitive change in approach to product development and evaluation. While the older test cells are solely designed to assess engines, the new facility can accommodate an entire truck or bus for whole vehicle testing. Moreover, the building which houses the new facility is specifically made to safely test gas and hydrogen combustion vehicles. These, along with other features, make the new Darlington test facility wholly unique in Europe, according to Cummins.
The second capability – safe testing with gas and hydrogen – is the easiest of the two to justify. At IAA Transportation 2022 in Hanover, Cummins launched a new fuel-agnostic engine platform, designed to run on natural gas and hydrogen as well as diesel, in order to target those niche applications which cannot be fulfilled by an electric vehicle. Hydrogen is a highly volatile and combustible element, and in the following section of the article, I describe the measures Cummins has taken to mitigate the repercussions of an explosion in the test chamber.
The first capability – whole vehicle instead of isolated engine testing – takes some further explanation. The decision to expand Darlington’s testing capability to the entire vehicle was driven by Euro 7, according to Tom Partridge, who is Director of Laboratory Operations. The new emission standards will be even more stringent than before, requiring engines that emit particulates with a diameter smaller than 10 nanometres, and stipulating lower exhaust emission limits on commercial vehicles. Furthermore, Euro 7 will require OEMs for the first time to restrict particle emissions from brakes and tyres.2 These new requirements throw up a number of different challenges for manufacturers, not the least of which is the problem of accurately measuring very small particulates. In particular, the question of how to test for brake emissions is one which Cummins does not have an answer for yet: simply encasing the braking system to capture emissions could lead to a change in performance and/or overheating.
Therefore, Cummins decided that, in order to switch from Euro 6/VI to Euro 7, “we needed to do our testing and development on a vehicle level, not just on an engine and component level,” Partridge told the press. With the opening of the new test facility, the company is now inviting OEMs to start making use of its expanded capabilities: they are welcome to take full advantage of the personnel and resources based at Darlington, or they can send their own engineers to carry out testing with Cummins’ equipment. As OEMs spend more and more of their R&D budgets on electric vehicles, Cummins expects they will outsource some (if not all) of their internal combustion development where they can in order to meet the Euro 7 standards, a trend that Darlington stands to benefit from. (In the latter part of this article, read my report of a talk on Euro 7 delivered by Cummins during the press visit.)
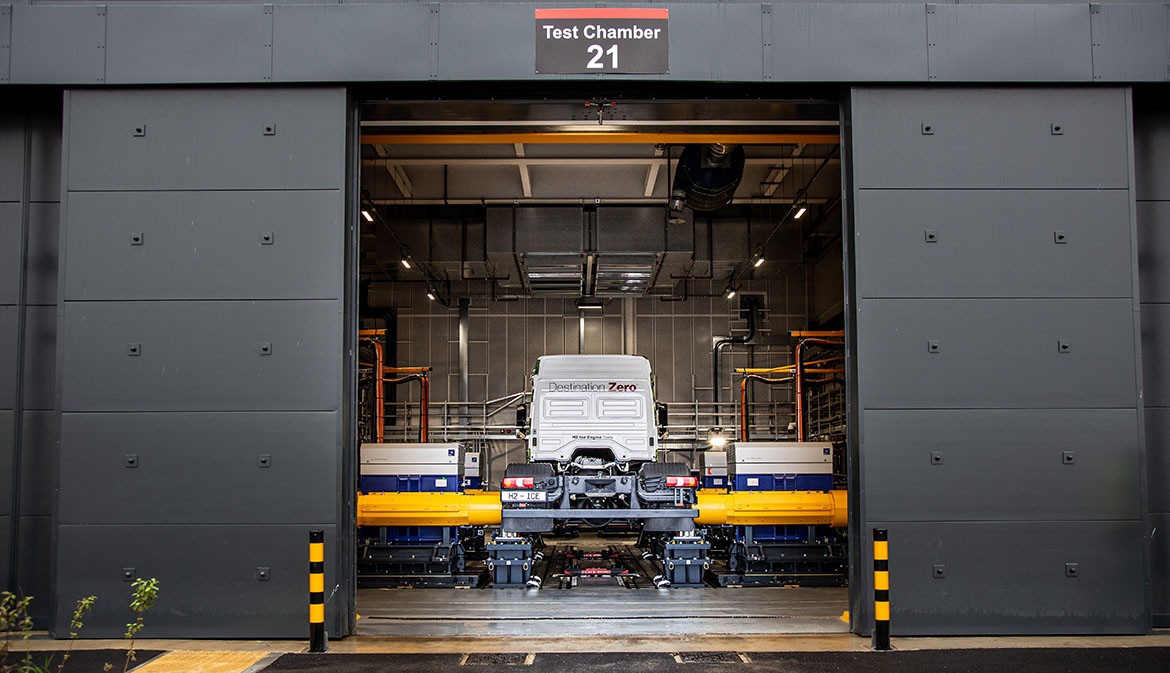
Test chamber front entrance with tethered panels on the doors
Cummins intends that the new test facility should serve the needs of OEMs through Euro 7 and beyond: it is “futureproof” for the next fifteen or so years, Partridge said. Following the expansion of its testing capability, the Darlington site will see further investments totalling USD30m in its production, establishing a new long block line for Euro 7 engines. Last year, Darlington shipped 72,325 engines and 41,785 aftertreatment systems (for all applications including CVs) to customers, and Cummins does not expect demand for its engines to abate any time soon. Indeed, the main takeaways from the press trip were these: so long as the majority of heavy vehicles continue to run on combustion engines, there will be a need for Cummins’ expertise and services; and, so long as electric vehicles eat up the lion’s share of R&D budgets, the greater the opportunity for Cummins to step in and take control of the development process for combustion engines on behalf of OEMs.
1 It was first announced over two years ago; see our report from April 2022: https://truckandbusbuilder.com/article/2022/04/07/cummins-to-open-fuel-agnostic-engine-rd-site-in-uk
2 Consult our series of Euro 7 articles for further details: (1) https://truckandbusbuilder.com/article/2023/10/02/european-council-adopts-its-position-on-euro-7vii-emission-limits ; (2) https://truckandbusbuilder.com/article/2024/03/05/an-update-on-euro-vii-the-future-regulation-of-the-european-commercial-vehicle-industry ; (3) https://truckandbusbuilder.com/article/2024/04/18/european-council-approves-euro-vii
Testing facilities at Darlington
Cummins’ vehicle testing facility at Darlington is located in an entirely new building, which is detached from the older engine testing facilities. Entrance to the building is from a central door which opens onto a T-shaped corridor. Flanking the middle of the ‘T’ are test chambers, one on each side. The one on the left is complete and fully operational and is accessible via two doors: one from the T-shaped corridor, and one on the front of the building which is made to allow vehicles to be driven in and out. The second chamber is incomplete: at an undetermined later date, this will be fitted out to mirror the first chamber and expand the testing capacity of the facility.
Inside the test chamber, the vehicle’s wheels are attached to four ‘AVL Dynoforce’ load units. These can be moved around to accommodate different wheelbases. The dynamometers have a maximum torque of 60,000 Nm at up to 5,000 rpm, and they can deliver up to 6,000 Nm directly to each wheel. By attaching each wheel and running the equipment, the action of driving can be simulated in a way which Cummins claims can provide more accurate measurements than would be possible on a rolling road.
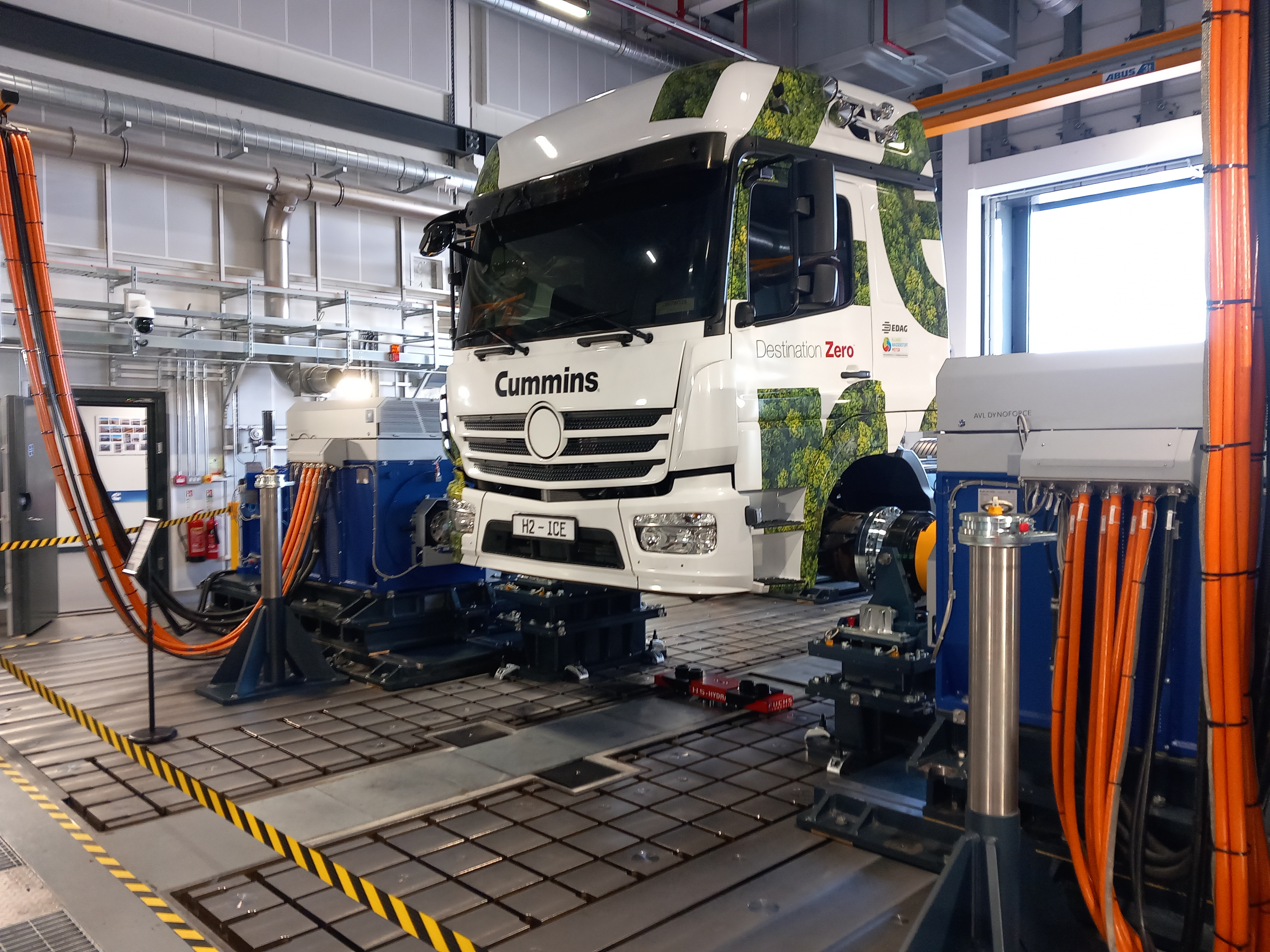
Truck mounted in dynamometer in test chamber
The testing chamber can accommodate vehicles with wheelbases between 2,300 and 6,700 millimetres and weighing no more than 28,000 kilograms. The maximum continuous power which can be delivered is 450 kilowatts. It is designed to test many kinds of vehicle, from sports utility vehicles and lorries to tractor units, agricultural tractors, and buses (up to a “Hong Kong-spec” double decker).
The most striking feature of the new test facility are the unusual panels on the exterior of the building. These are so-called “tethered” walls, which are “aircraft-grade” according to Cummins. In the event of a gas or (especially) hydrogen leakage leading to ignition, the test chamber is designed to contain the explosion and protect any personnel inside the building. The testers and their monitoring stations are located solely in the T-shaped corridor, which is safeguarded by a blast protection wall separating it from the test chamber. The function of the tethered walls is to relieve the pressure inside the chamber in the event of an explosion. The panels fly out from the external walls, dissipating some of the energy released by the blast inside the chamber.
In order to keep its test engineers safe, Cummins had to find a way to operate the vehicle during testing without using a human driver. It opted for a robotic driver, affectionately named “Vera” (by a pupil from a local school in Hartlepool), which sits inside the cab while the vehicle is being tested. This “virtual engineer robotic assistant” (VERA) was supplied by Stähle Robot Systems and can perform many of the basic functions which a human driver would do while operating the vehicle. (Of course, it cannot navigate the vehicle on an actual road, but it does not need to within the controlled conditions of the test chamber.)
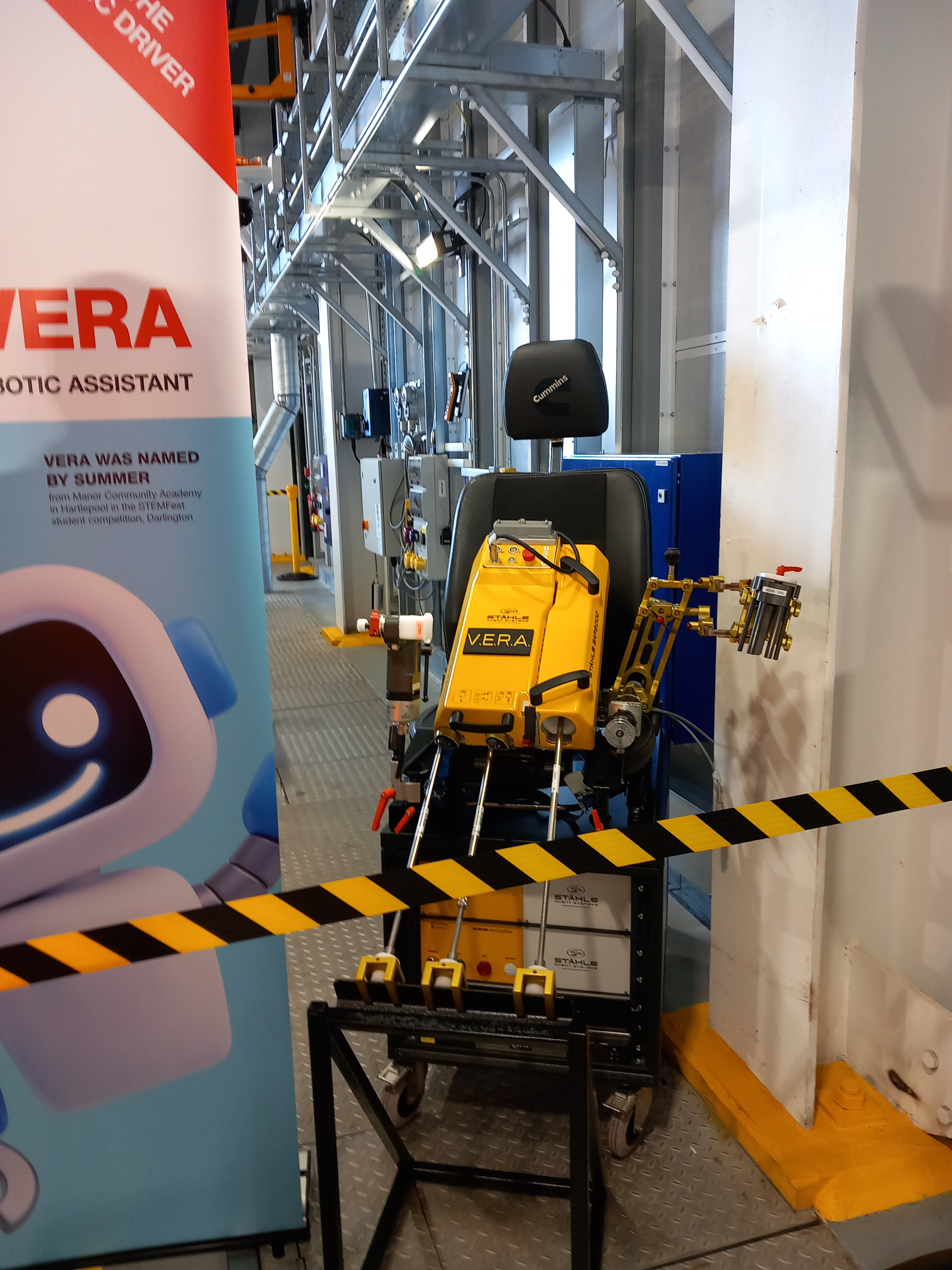
'Vera' the robotic driver
Construction of the building began in July 2022 and was finished two years later. Cummins aims to put fifteen to twenty-five vehicles through testing per year, and it expects the vast majority of these to be trucks. The company says it has invested around GBP13m in Darlington over the past four years, primarily in the new test facility.
The new vehicle test chamber is intended to complement, not replace, the existing facilities in Darlington. We were given a tour of the older buildings, which comprise ten test cells and a “pilot centre” for assessing vehicles on the road. Cells 1-7 are for CPE engine testing – i.e., combustion, performance, and emissions. Cells 8-10 are for machine development and allow for hot box testing, extreme testing, and water spray testing. The test cells we saw were apparently extended and refurbished nearly ten years ago to meet ISO/IEC 17025 testing and calibration standards; it was reportedly one of the first testing sites in Europe to be accredited. In the pilot centre, there is a workshop where Cummins will take in trucks and other vehicles at different points in their lifespan to test their engines and aftertreatment systems. These facilities will continue to have a use as Cummins transitions to Euro 7.
Euro 7 requirements and opportunities
During the afternoon, Felipe Rocha, who is On-Highway Europe General Manager, Peter Williams, Director of Technical Compliance and Certification (EMEA and APAC), and William Lamb, Director of Product Strategy, spoke to the press about Cummins’ approach to Euro 7, which will start coming into force for heavy-duty vehicles from 1 July 2027. Other key markets will be implementing similar standards by the end of the decade: India’s BS-VII, Brazil’s P9, and Japan’s P-PPNLT are expected to copy Euro 7, while China’s NS-VII could end up being more stringent. It is therefore imperative that Cummins prepare for Euro 7 now, futureproofing its business not only in Europe but in most of the rest of the world.
To get more technical: according to Cummins, in order to achieve Euro-7 compliance, combustion engines need to demonstrate the following.
(1) engine-out nitrogen oxide (NOx) suppression during cold start;
(2) reduction of exhaust flow during long coast;
(3) keeping aftertreatment warm in low power duty cycles.
In Cummins’ view, achieving these goals require whole vehicle testing capabilities and emissions measurement equipment which is more accurate than what we have currently. This means significant investments of time and money which many OEMs feel they cannot afford to spend.
During his presentation, Rocha cited figures from Daimler Truck, calculating the deployments necessary to achieve the European Union’s current target of 45% fleet CO2 reductions by 2030 (compared to the 2019 baseline):
400,000 new zero-emission vehicles on the road, starting from now;
60% cost reduction for total-cost-of-ownership parity between electric and diesel;
35,000 public charging stations (with megawatt capability);
2,000 hydrogen refilling stations for trucks.
Rather understatedly, Cummins and Daimler Truck are of the view that these targets “may be challenging given the technological, financial, and infrastructure constraints that exist, as well as the complexity of the regulatory framework.”
Given the background of costly and complicated investments in electric vehicles and infrastructure, driven mostly by regulation, it is easy to see why OEMs are baulking at the prospect of simultaneously putting in the work to ensure compliance with Euro 7. “Vehicle OEM R&D funds are not unlimited,” said Rocha, and he estimated that capital and R&D expenditure on conventional powertrain technologies has fallen by 12% between 2019 and 2022.
Cummins’ new powertrain test facility strikes two key targets with one stone. It provides OEMs with the testing capabilities required to develop Euro 7-compliant vehicles without taking too much time and money away from electric vehicle development; and it is also designed to accommodate alternative powertrains running on different energy sources. It is set up to deal with gas and hydrogen in addition to diesel, and at a later date it will be expanded to allow for battery testing as well.