ACT Expo 2025: What next for vehicle electrification in the USA?
By Bradley Osborne - 1st July 2025
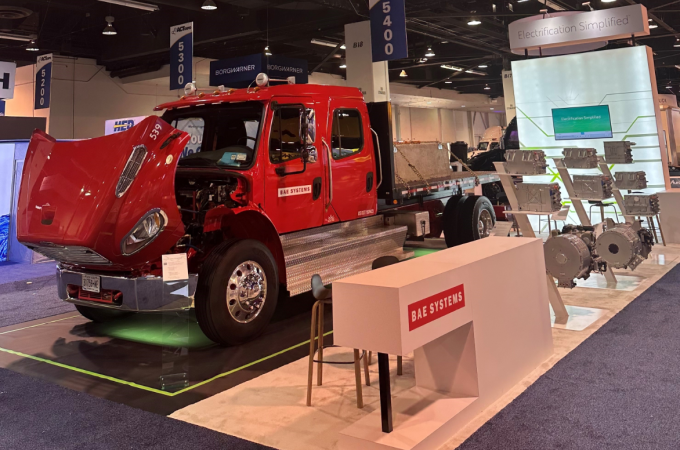
BAE Systems' stand at ACT Expo 2025
USA – The general mood of this year’s Advanced Clean Transportation Expo – held between 28 April and 1 May in Anaheim, California – was one of healthy confusion. There were questions about the direction of the commercial vehicle industry and how a more sustainable transport system might be achieved. But the confusion was coloured not by disillusion but by optimism, a feeling that the range of technological solutions available to the country’s fleets were opening up again. Now that the focus has expanded beyond fully-electric vehicles, interest in natural gas, propane, and other alternatives to a pure diesel vehicle, including hybrid solutions, has been rekindled.
One company, however, which exhibited absolutely no confusion about the future of the industry was BAE Systems, an established supplier of electric drivetrains and power electronics to bus manufacturers and increasingly to heavy-duty applications as well.
The company is confident that the industry will continue to move towards net zero; the only questions concern “how it will be done and how long it will take”, according to Robert Lamanna, vice president and general manager of BAE Systems’ Power and Propulsion Solutions division. Indeed, BAE Systems’ entire electrification portfolio is intended to clear away confusion, easing the integration of e-powertrain subsystems and thus simplifying the drivetrain layout. At the company’s stand in the expo hall, a medium-duty diesel truck converted to be an all-electric vehicle was used to demonstrate the design principles of the BAE Systems solution (more details below).
The company’s products are not exclusively geared towards battery electric vehicles. BAE Systems became a familiar name in the industry following its extensive work on diesel-electric hybrid buses, and it has worked with fuel-cell systems since 1998. Whether the industry pivots towards hydrogen or hybrid, BAE Systems can meet the electrification needs of customers in those use cases; and Lamanna is confident that the market will continue to request electric vehicles in applications such as school and urban transportation, terminal operations, and waste collection, where adoption is less complex and payback is turning favorable. Speaking with Truck & Bus Builder, Lamanna opined that the medium- to heavy-duty truck segment, particularly vocational trucks, is currently “underserved” by the industry.
The duty cycle [the frequency and duration of typical vehicle operations and resulting power demands] of a work truck is not dissimilar to that of an urban bus – short, predictable routes and a return to the depot at the end of the day. With the provision of appropriate charging infrastructure, we see the vocational sector as a promising next step for electrification,
Lamanna told T&BB.
In previous years, the expo hall was filled with all kinds of electric vehicles, some from familiar brands and many more from new entrants, not all of which have survived. While there were fewer electric vehicles at this year’s show, BAE Systems is not concerned by the tumult of the past twelve months. Many of the vehicles showcased in the past were immature efforts, assemblies of mismatched components and subsystems shoehorned into the diesel engine’s former home. “Customers have now learned from direct experience what good EVs look like and understand the trades that need to be considered,” said Lamanna. Now that this initial wave of electric vehicles is subsiding, Lamanna encounters customers who are asking for more sophisticated and optimised solutions from suppliers with longstanding reputations and proven products, and he expects BAE Systems will benefit from this maturation of the electric vehicle market.
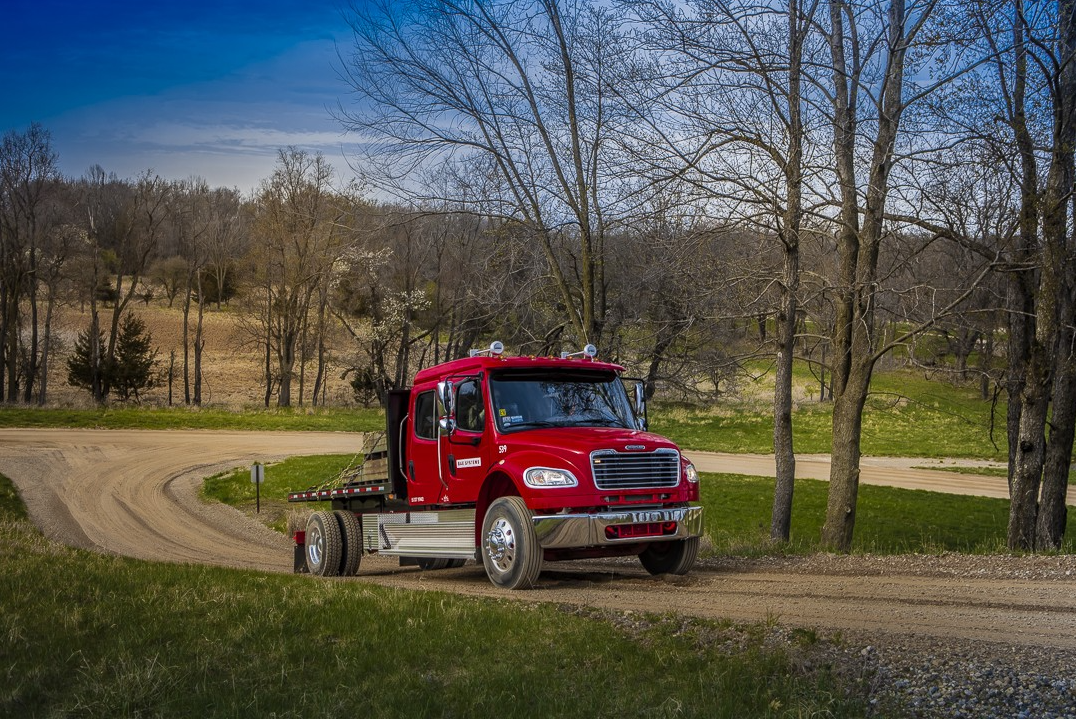
Electrified truck fitted with BAE Systems' electric driveline
The electrification portfolio on display at the company’s stand represents the third generation of development at BAE Systems, incorporating several innovations. One of these is the inclusion of semiconductors made of silicon carbide, providing superior electrical and thermal properties that deliver greater power density at a lower operating temperature, while also reducing size and weight. Moreover, the company has continued to develop its principle of “federated” design: rather than a “distributed” system, where electronic components and subsystems are dotted all over the vehicle chassis, the company’s system concentrates the power electronics in a combined “X-in-2” solution that can be configured to the customer’s required functionality.
BAE Systems believes that its latest generation of products will be foundational to the purpose-built electric vehicles of the (near) future; that is to say, vehicles which are built from the ground up to run on electrical energy. As electric vehicles mature, Lamanna expects manufacturers to ask more nuanced questions about powertrain design, including questions about how to optimise the interoperation of the electrical drive motor and its power electronics; how to handle electrical loads for auxiliary systems which power, for example, a heating system or a power take-off; and how to enable better charging performance. It is challenges such as these which BAE Systems addresses with its portfolio.
Electrification simplified: BAE Systems’ demonstrator truck at ACT Expo
BAE Systems supplies electric motors, power electronics, and system controllers to original equipment manufacturers in the medium- to heavy-duty bus and truck segments. The components it produces include traction motors paired with Eaton transmissions, and two types of modular system for power control: the “Modular Power Control System” (MPCS) and the “Modular Accessory Power System” (MAPS). The high-power MPCS delivers power from the batteries to the propulsion system, integrating subsystems such as inverters and charging in a single box. Inputs and outputs can be added or taken away to support multiple motors and battery packs, as well as fast and/or slow charging systems. The low-power MAPS powers auxiliary systems such as coolant pumps and air compressors, e.g., for cabin heating and air conditioning in a city bus.
At ACT Expo, BAE Systems arranged several motor/MPCS/MAPS combinations in a row to demonstrate its configurable “X-in-2” solution. These groupings covered several applications in the Class 6-8 segments; not on display was their most powerful motor for the heaviest of use-cases. Switching between applications can be as simple as adding or removing ‘functional slices’ from the modular power electronics or incorporating one of the two sizes of transmission to the driveline.
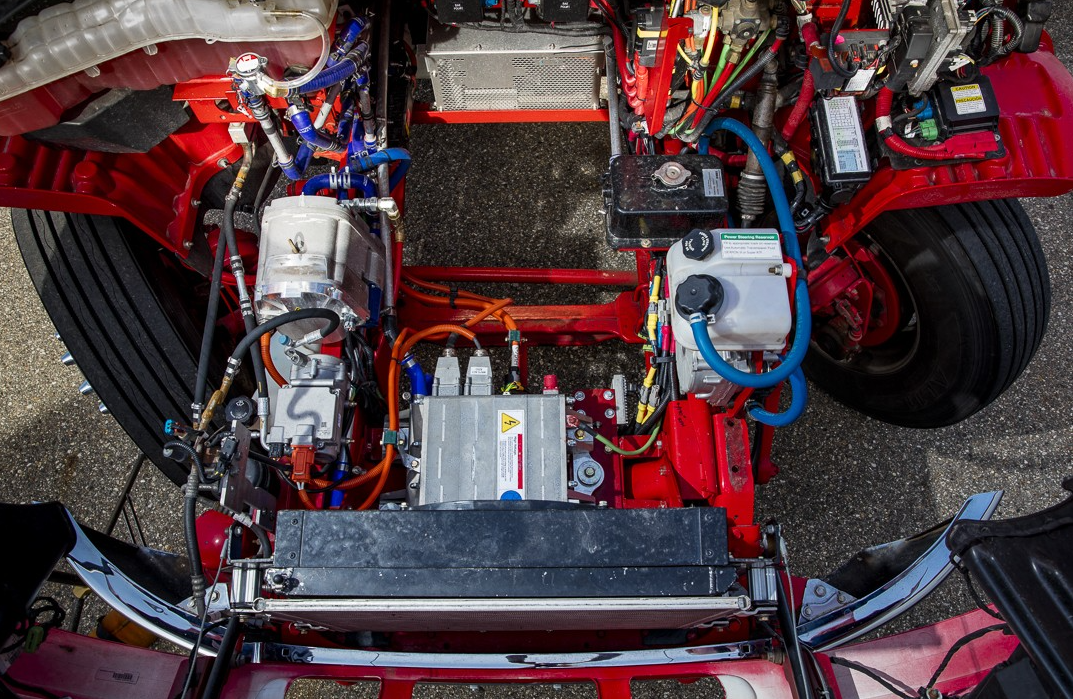
Space-efficient equipment fit under the hood of the truck
To give a flavour of how simple its system is, BAE Systems showcased a medium-duty truck installed with its e-powertrain. The company removed the truck’s diesel engine and associated components and replaced them with its e-powertrain, trying to make the best use of the space available. The resulting integration has a compact and efficient arrangement of units and wiring harnesses, making very good use of the space available and with large amounts of unused real estate remain under the bonnet. With a minimal unladen weight increase – even after adding 230kWh of battery storage – the truck has impressive performance, which BAE Systems has been actively demonstrating to interested customers.
In two informational videos shown at the stand, BAE Systems visually demonstrated the advantages of its solution. In the first, a conventional electric vehicle architecture is contrasted with the company’s modular system.1 In the second, a truck is assembled by selecting from several different options related to traction, energy storage and input, and accessories, showing how easy it is to configure the product portfolio to suit the needs of different customers.2
They show that there is more to be gained from BAE Systems’ solution than a neater arrangement of cables. The combined weight of all the parts in its solution can be as little as half of that of the typical competitor system. Furthermore, the number of parts can be significantly reduced: this makes the system easier to maintain by decreasing the potential points of failure and the number of subcomponents which may need to be replaced during the life of the vehicle.
1 https://www.youtube.com/watch?v=sYTqMBNV0dw
2 https://www.youtube.com/watch?v=uZQ3pPm_Ai4
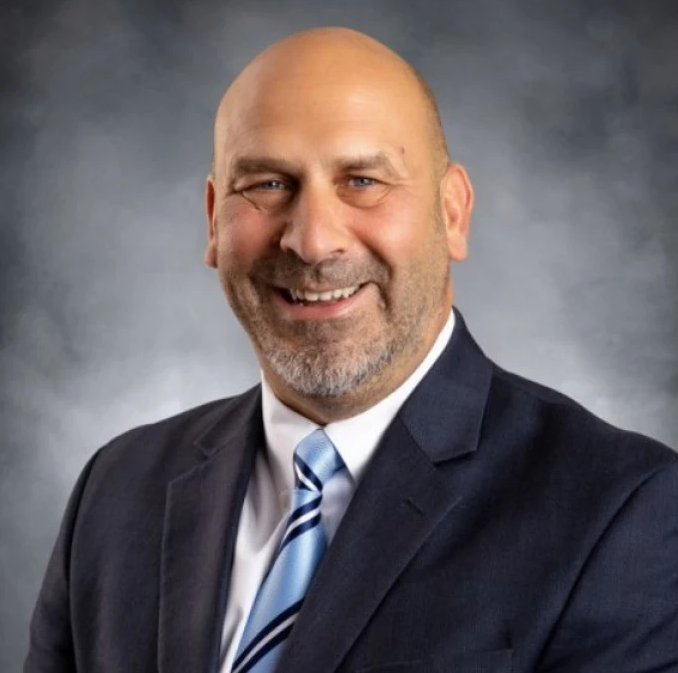
Bob Lamanna is the vice president and general manager responsible for the BAE Systems Power and Propulsion Solutions (PPS) business area and is a current member of the company’s Electronic Systems sector leadership team. Most recently, Bob served as the deputy vice president for BAE Systems PPS business area, where he was integral in executing and enabling efficient company operations, and increasing product capability. Previously, he was the director of global transit accounts within the PPS business, customer solutions director at Endicott Interconnect Technologies, Inc., and the global services director at Universal Instruments.