Hübner Chassis Technology – a new name in suspension and steering system technology for the truck, bus and trailer industries
By Jim Gibbins - 28th March 2023
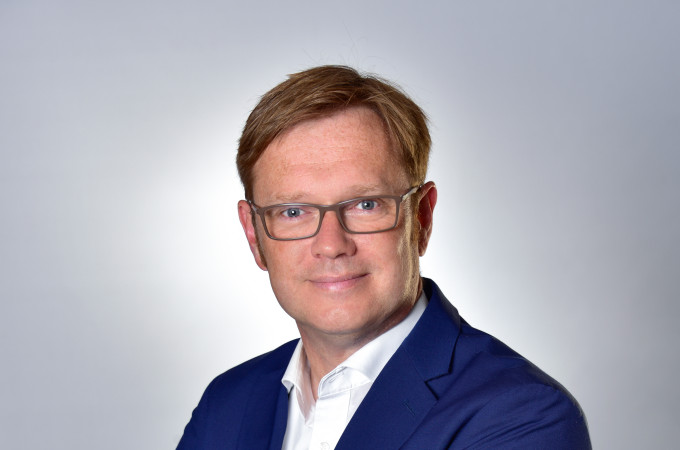
Dr. Mark Wöhrmann, Managing Director of Hemscheidt Fahrwerktechnik and head of HUBNER’s new business unit, Chassis Technology.
Germany - Hübner Chassis Technology is the name of a new suspension and steering system division of the Hübner Group. This new division is the working combination of two formerly independent companies, V.S.E. Vehicle Systems Engineering B.V. (VSE) of Veenendaal, near Utrecht, Netherlands and Hemscheidt Fahrwerktechnik GmbH & Co. KG of Haan, Germany.
Truck & Bus Builder was fortunate to meet the senior management representatives of both companies recently to discuss the background to the latest division within the Hübner Group and, its future plans.
Chassis Technology – a new business division
On hand, for interview, was Dr. Mark Wöhrmann, who has been at Hemscheidt Fahrwerktechnik since 2011; he is the manager of the Hemscheidt Fahrwerktechnik and is also responsible for the new business unit, Chassis Technology. Hemscheidt Fahrwerktechnik was bought in 2007 by the Hübner Group as a competitor manufacturer of articulation systems. Today, it produces hydro-pneumatic suspension systems and dampers for niche applications, such as the truck, off-road and defence markets. (For more information on Hemscheidt see below).
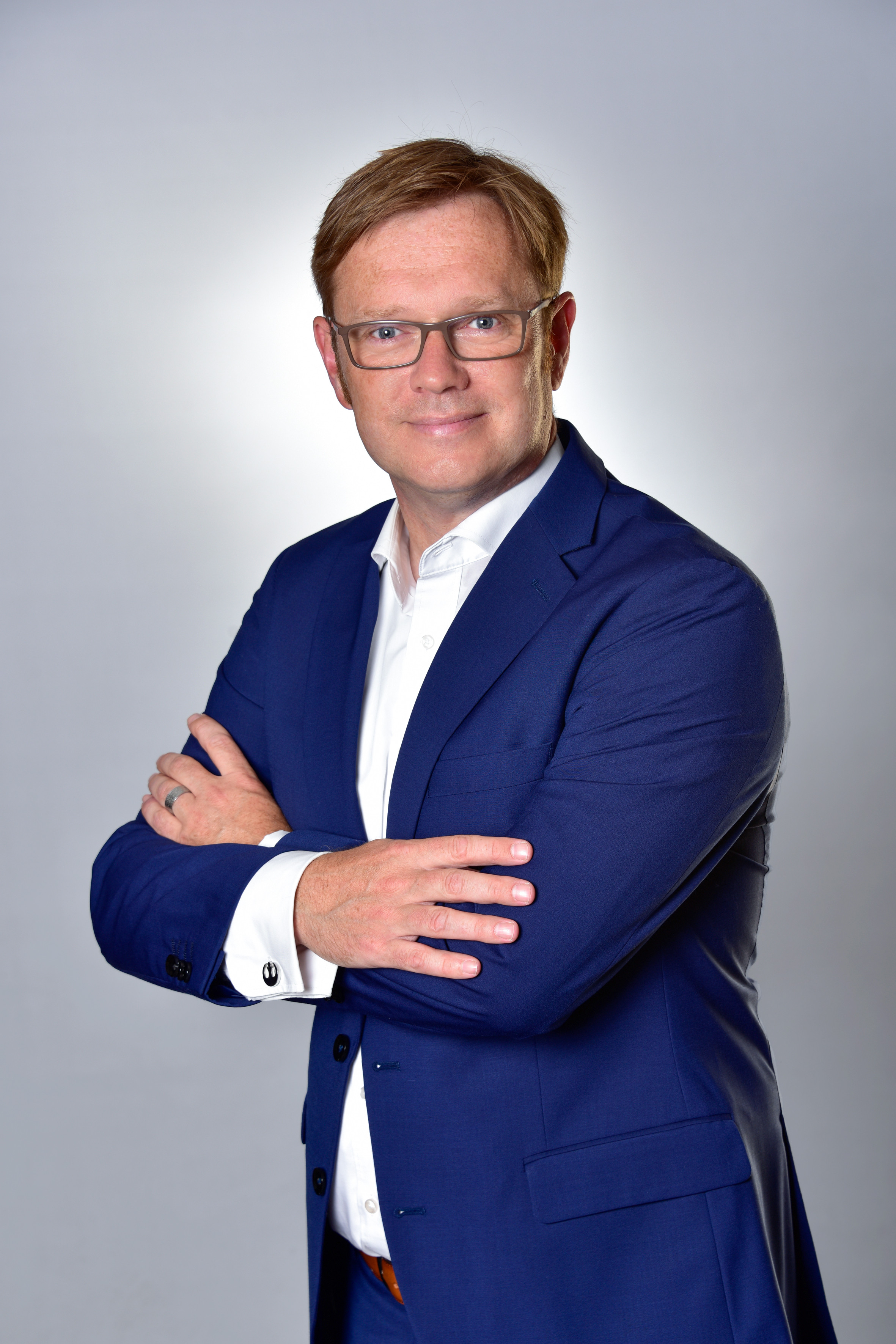
Dr. Mark Wöhrmann, Managing Director of Hemscheidt Fahrwerktechnik and head of HUBNER’s new business unit, Chassis Technology.
Dick Lodder, one of the founders and manager of V.S.E. Vehicle Systems Engineering B.V. since 2001, is focussed on advanced chassis steering and suspension system solutions, primarily in trucks and trailers, but now also in buses.

Dick Lodder, one of the founders and manager of V.S.E. Vehicle Systems Engineering B.V.
In the last few years, Wöhrmann said the Hübner Group had started to consider what would be the possible suspension solutions of the future and what would be the key markets in future years. He said Hemscheidt Fahrwerktechnik was good at designing mechanical components for suspension solutions, but that it did not have the software competencies in house, which, he said, the company saw as a major key competency to competing in the electrified truck and bus markets of the future.
“All future products,” he said, “would have to be smart, need to have sensors with the ability to control them.”
He said that as VSE had many of these competencies - it makes steering systems, electrical steering systems, as well as the necessary software for the controlling function and safety – it made sense to acquire the Dutch company, which was agreed and then concluded in May 2021.
Subsequently, Wöhrmann explained, it sees huge synergies and benefits for Hübner in combining the competencies of the two companies - the software and electronics competency from VSE and the mechanical know-how from Hemscheidt - under the new umbrella organisation of Hübner Business Unit Chassis Technology .
Today it has a joint product of hydro-pneumatics suspension systems, which both companies offer to the market; VSE in truck and defence applications and Hemscheidt in off-road and also, defence applications.
Hübner Chassis Technology has two engineering centres distanced by a one and half hour journey, one at VSE in Veenendaal, Netherlands, which makes all the software, electronics, and the controller hardware for the steering systems and the other, is in Haan-Gruiten, the headquarters of Hemscheidt Fahrwerktechnik GmbH & Co KG, which works on the mechanical components like cylinders and dampers.
Wöhrmann said Hübner Group’s strategy is now to merge the offerings of the two subsidiaries of VSE and Hemscheidt and to offer its steering and suspension systems solutions together to the market as Hübner Chassis Technology. The Business Unit is now in the process of putting the sales and engineering competences together.
Hübner sees great potential for hydro pneumatic suspension and steering systems in the electric bus and truck markets
Wöhrmann said:
The division’s core markets will still be suspension systems for the truck and trailer market and large off-road truck applications, rear axle steering systems for the trailer market, but we also see great potential for our steering and suspension systems in future electrified trucks and buses.
Why? Hübner sees hydro pneumatic suspension as a good solution for electric vehicles because of the advantages it offers of compact packaging, better driving comfort, improved vehicle dynamics and most importantly, better energy efficiency. In electrified applications, it is important to consider all the other auxiliary electrical consumptions needs of a bus or truck and Hübner believes that use of hydro pneumatic systems can make the vehicle more energy efficient and reduce the TCO (Total Cost of Ownership). The energy package can also be increased and thereby, overcome package limitations of today’s air springs, Wöhrmann stated. This suspension system competency, together with the software expertise of VSE, puts it in a strong position to provide active / adaptive suspension and steering solutions in the future.
So, the electrified bus is one of the company’s core focus areas, mainly because Hübner is already very strong in the bus market in articulation systems, but also because of its ability to bring intelligent systems to the segment through VSE. Wöhrmann said, it therefore made sense to develop and present its suspension and steering solutions, in the bus segment. It has supplied already a few OEMs, such as the Alstom Aptis, where it has integrated its suspension system. (The Aptis project has since been shelved https://truckandbusbuilder.com/article/2021/05/01/alstom-to-put-its-three-year-old-electric-bus-business-unit-aptis-up-for-sale, however, there are other electrified buses and new designs on the market, where it sees opportunities).
Working with Ziehl-Abegg on independent e-drive wheel with hydro pneumatic suspension system
In 2017, it started to look at how to provide solutions for the electrified bus market. The first cooperation was with Ziehl Abegg because it had an axle with wheel hub motors, and it asked Hemsheidt to look at developing an independent suspension system. Hemscheidt together with Ziehl Abegg combined an electric wheel drive with semi-trailing arm independent wheel suspension using a hydro pneumatic spring and damper system. Currently, this remains a prototype, with no customer at the present time. (Details of the semi-trailing arm independent wheel suspension can be found via this link: https://www.hemscheidt.de/produkte-services/fuehren.) However, Wöhrmann said, the company was still working together with Ziehl Abegg to find a customer with this kind of solution.
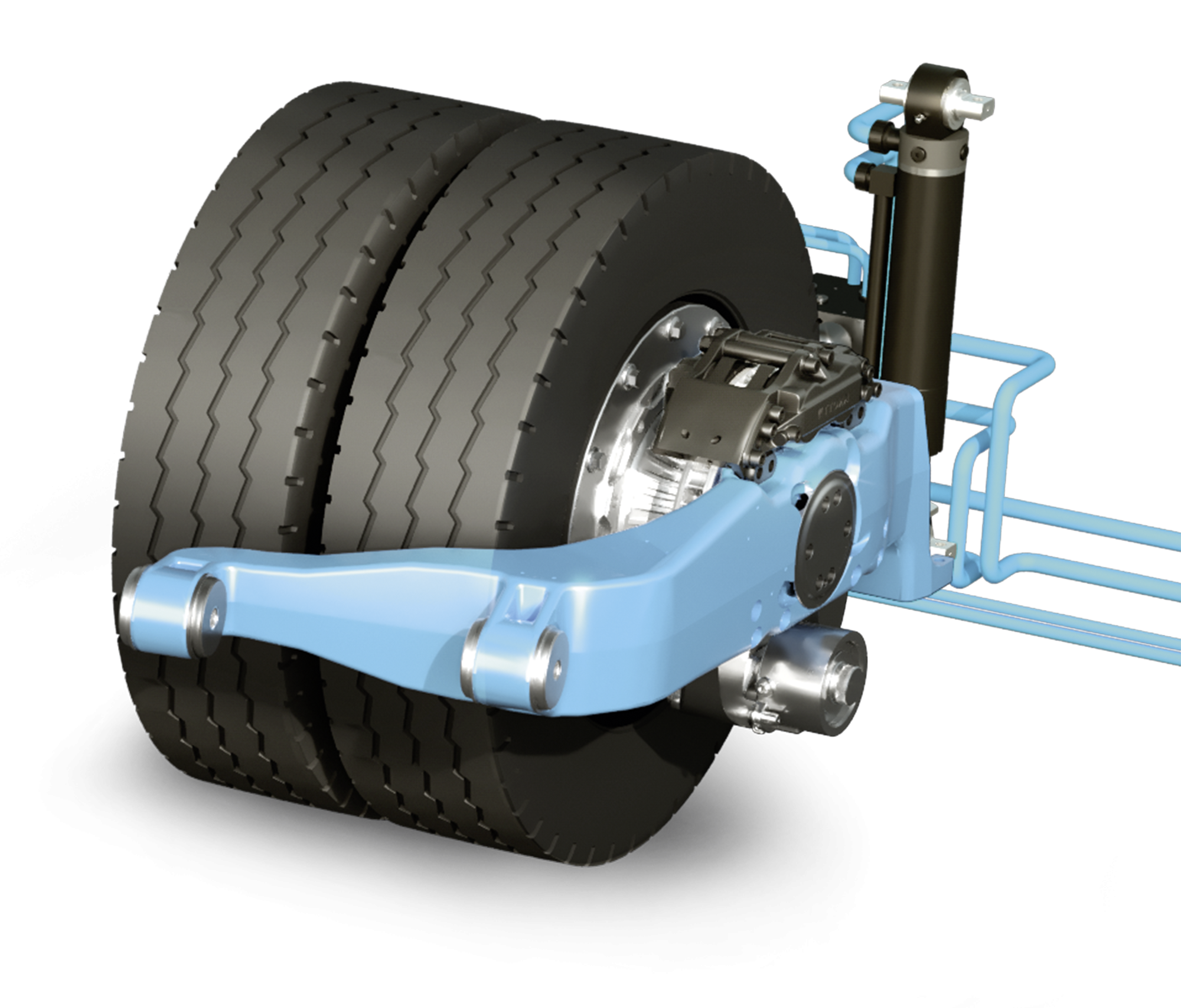
An electric wheel with semi-trailing arm independent wheel suspension using an hydro pneumatic spring developed by Hübner in collaboration with Ziehl Abegg
Possibly a reason why it does not yet have a customer for the independent suspension, Wöhrmann surmised, is because many of the bus builders today have been using the same platform for more than 30 years; adding that currently, most electrified buses are more or less the same design with an electric motor replacing the diesel engine and transmission. So, all the connections to the chassis and body frame remain the same, Wöhrmann continued, as this is because it is the easiest and quickest way to electrify a vehicle. However, if you were to design an electric bus from scratch, most likely, he said, you would build the bus in a different way to the way it has been built for the last 30 years. He added that there are several spin-off companies {start-ups} that now do that and this is where “we think all our ideas can be taken into account”. Another major advantage for start-ups is that they do not have the same challenges as the established truck and bus builders in terms of legacy production and architecture – they can design from scratch and build in a new bespoke plant with no legacy production and labour costs. Only time will tell if there is demand for its semi-trailing arm independent wheel suspension with hydro pneumatic spring and damper system Hübner has developed with Ziehl Abegg.
ISO 26262 functional safety software – an integral part of vehicle electrification
Another key area of focus for Hübner is functional safety. Since 2018, the ISO 26262 standard makes it necessary for electric vehicles over 3.5 tons to a have a functional safety system and VSE’s engineering department has invested heavily during this timeframe to develop functional safety software. This is an area where the Hübner Chassis Technology division sees an opportunity for expansion, as it is also necessary for the Hübner articulation system in electric buses. Everywhere there is a controller, Wöhrmann explained, a company needs to integrate functional safety software.
Wöhrmann pointed out that, whilst the ISO 26262 Standard is not a regulation, it is the state-of-the-art standard and one that is needed for electric vehicle technology development. Lodder added that VSE has a new control unit for its electrically controlled hydraulic steering and suspension systems. ISO 2626-2 requires that each step of the functional safety software process is documented. Whilst perhaps the customer is not aware of this safety process, Hübner sees it as an integral part of its future smart steering and suspension system. It is also confident that its hardware and software systems will prevent a critical safety incident from occurring in the future.
One-axle electrically controlled hydraulic steering with ISO 26262 functional safety now on the market
Lodder stated that it has started fitting its functional safety systems’ protocol with its one-axle steering system and that it is now moving to two axles and then three. He added that starting this quarter (February), Hübner Chassis Technology would be able to provide customers with one axle steering systems for electric trucks and buses fitted with the ISO 26262 functional safety software. This is a steering system for the rear axle of an electric truck or bus with a fully integrated functional safety system.
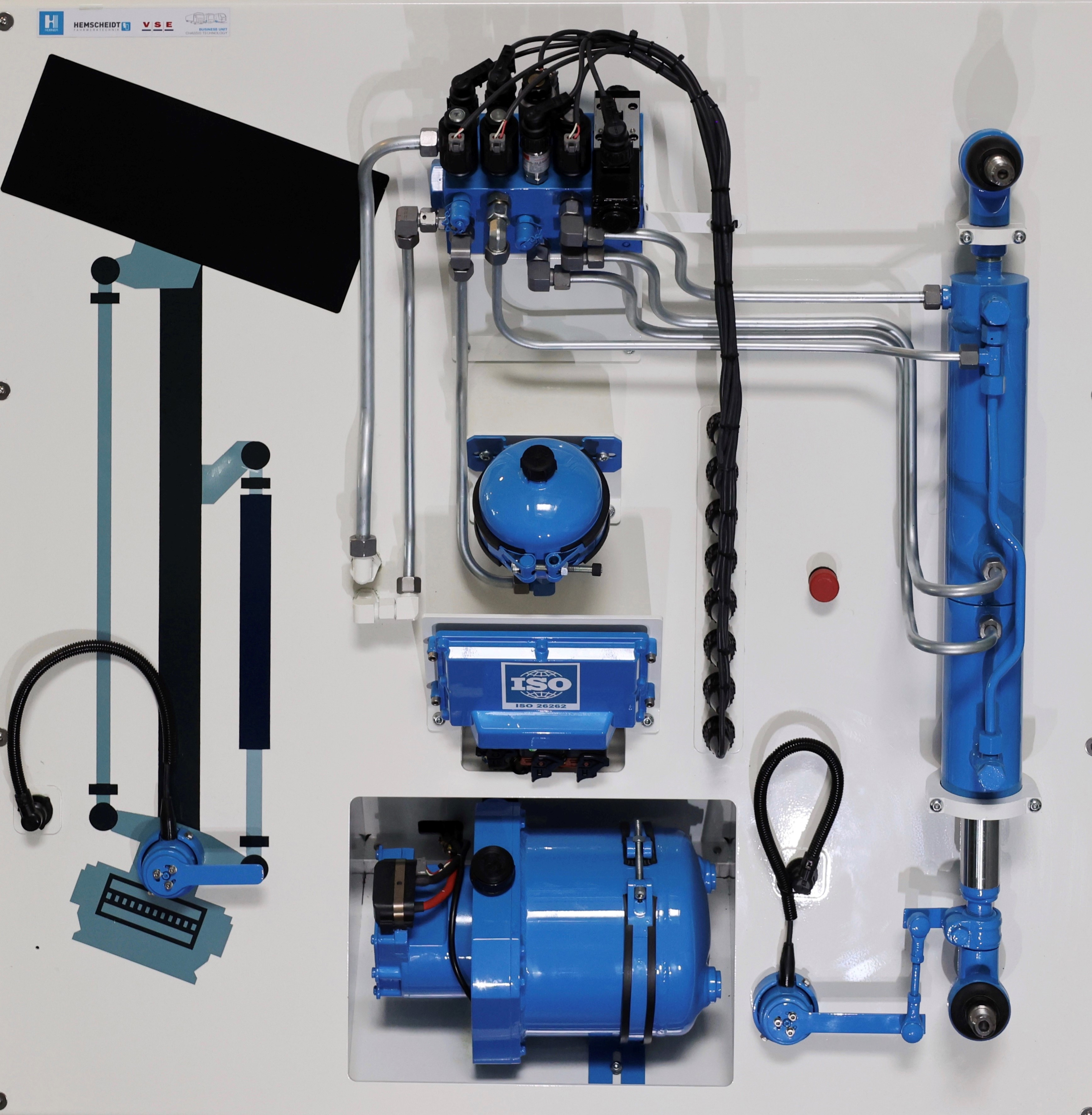
Steering System kit from Hübner - All components of the Electric Truck Steering System (ETS1) with control unit (certified according to ISO 26262) for controlling one axle. The system can also be expanded to control more axles.
In the lead up to the launch of the new steering system in the European CV marketplace, Lodder said the division had been testing its steering system in its own test trucks at VSE in Veenendaal, Netherlands. The next stage, Lodder stated, is to extend this to two- and three-axle steering systems in e-trucks and e-buses, and then thereafter, it will focus on trailer applications.
Wöhrmann continued by explaining that the steering system is axle agnostic. It is a case of application engineering of fitting the cylinder to the axle and then installing the software; the software is generic and can be used for the bus, truck and trailer industries.
In addition to the company’s traditional standard markets of coach and refuse trucks, Wöhrmann said that it was targeting two segments of the electric bus market with its electrically controlled hydraulic steering systems technology, long single and double articulated city buses and, small to mid-size buses. In the latter, the axles are at the very ends of the bus to allow for the maximum area for passengers, such as the Alstom Aptis (France) or the Letenda Electrip (Canada). This results in an extended wheelbase, and for compliance with turning circle regulations the rear axle needs to be steering. Another benefit of both axles steering is a reduction in tyre wear, Wöhrmann pointed out; certainly a future consideration when designing a vehicle to meet the new proposed EC Euro VII emissions standards, in reducing fine particulates (dust) from tyres. A third advantage of rear axle steering, Wöhrmann suggested, is reduced energy consumption compared with a fixed axle.
*Hemscheidt today is providing dampers for special applications as well as hydro-pneumatic suspension systems for heavy trucks especially for off road trucks and a lot of defence applications; Oshkosh Truck Corporation in the USA is a big customer, equipping a lot of their trucks in the last couple of years with its suspension system, as well as several other OEMs such as MAN and Rheinmetall. The third core area was the articulation system, which it had provided to MAN, which is no longer Hemscheidt business anymore because its Hübner Group’s sister company, ATG Autotechnik GmbH in Siek, Germany; ATG was acquired by Hübner in 2018.