Ever lighter and stronger: T&BB interview with Maxion on the past, present, and future of steel CV wheels
By Bradley Osborne - 16th April 2024
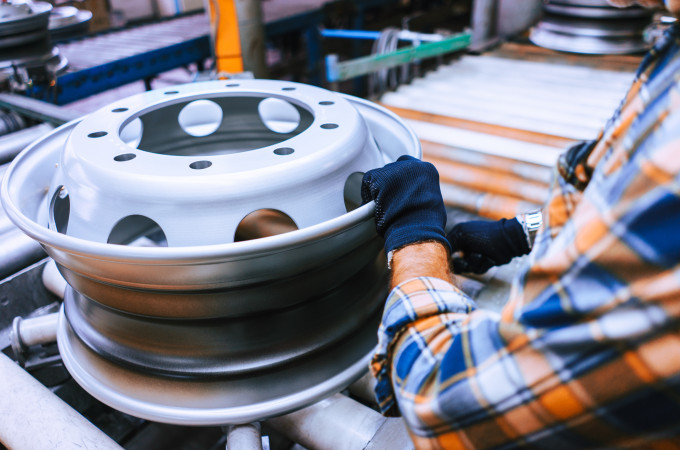
Maxion steel wheels for commercial vehicles
Germany – A truck wheel is easily taken for granted. Low to the ground and enrobed in a rubber casing, its steel face is hardly noticeable as the eye passes over the details of a typical truck cab. Indeed, the face or “disc” of the wheel is the only part which we see; the other part, the “rim”, attaches the tyre to the wheel and is mostly invisible. The disc and the rim are arc welded, or welded along the joint, to each other to form the wheel. While the passenger car wheel is given an identity by individual styling, the truck wheel is made in such a uniform way that it is treated almost like a commodity. This is misleading: in fact, its plain appearance and simple construction are the products of no less care and ingenuity than most any other part essential to the making of a truck. For Karl Rode, who is Director of Engineering for passenger car and commercial vehicle steel wheels at Maxion Wheels, the ingenuity emerges from the fine balance maintained between weight and strength. The wheel manufacturer’s eternal aim is to shed as much weight as possible without compromising on robustness.
In light of the company’s ambitious plans – announced at IAA 2022 in Hanover – to expand its portfolio of CV wheels to include forged aluminium for the first time, it seemed appropriate to take a fresh look at Maxion’s steel wheel business and to reiterate the unique merits of steel as a production material. Stan Mommers, who is Vice President of Sales for Europe, Middle East and Africa (EMEA), was keen to emphasise that steel wheels for trucks have a bright future – not least because of their smaller carbon footprint compared to aluminium. And it remains the case that steel, with its high yield strength and its good tensile strength, alongside its capacity for elongation, is an alloy which is easy to form to the desired shape at the same time as being remarkably robust. Rode described steel as “forgiving”: it can “forgive” the driver for passing over a particularly bad pothole, enduring considerable stress while remaining perfectly useable.
Maxion Wheels is a subsidiary of Iochpe-Maxion, a global corporation headquartered in Brazil which supplies structural components as well as wheels to the world’s truck makers. Maxion produces steel wheels for commercial vehicles in six countries: Germany, Brazil, Mexico, Turkey, India, and China. According to Iochpe-Maxion’s 2023 results, CV steel wheels accounted for 22% of the group’s net revenue, generating BRL3,209m in sales. Today, Maxion is truly a global supplier of wheels to the CV industry, but it was formed by several acquisitions and mergers of companies which began by serving local customers.
During our conversation, we touched on several topics of importance to the future of the wheel industry, including sustainability and e-mobility. In our discussions of these topics, we tackled various questions, asking how steel wheels will be made differently, how they will adapt to electric vehicles, and even how they may look in the near future.
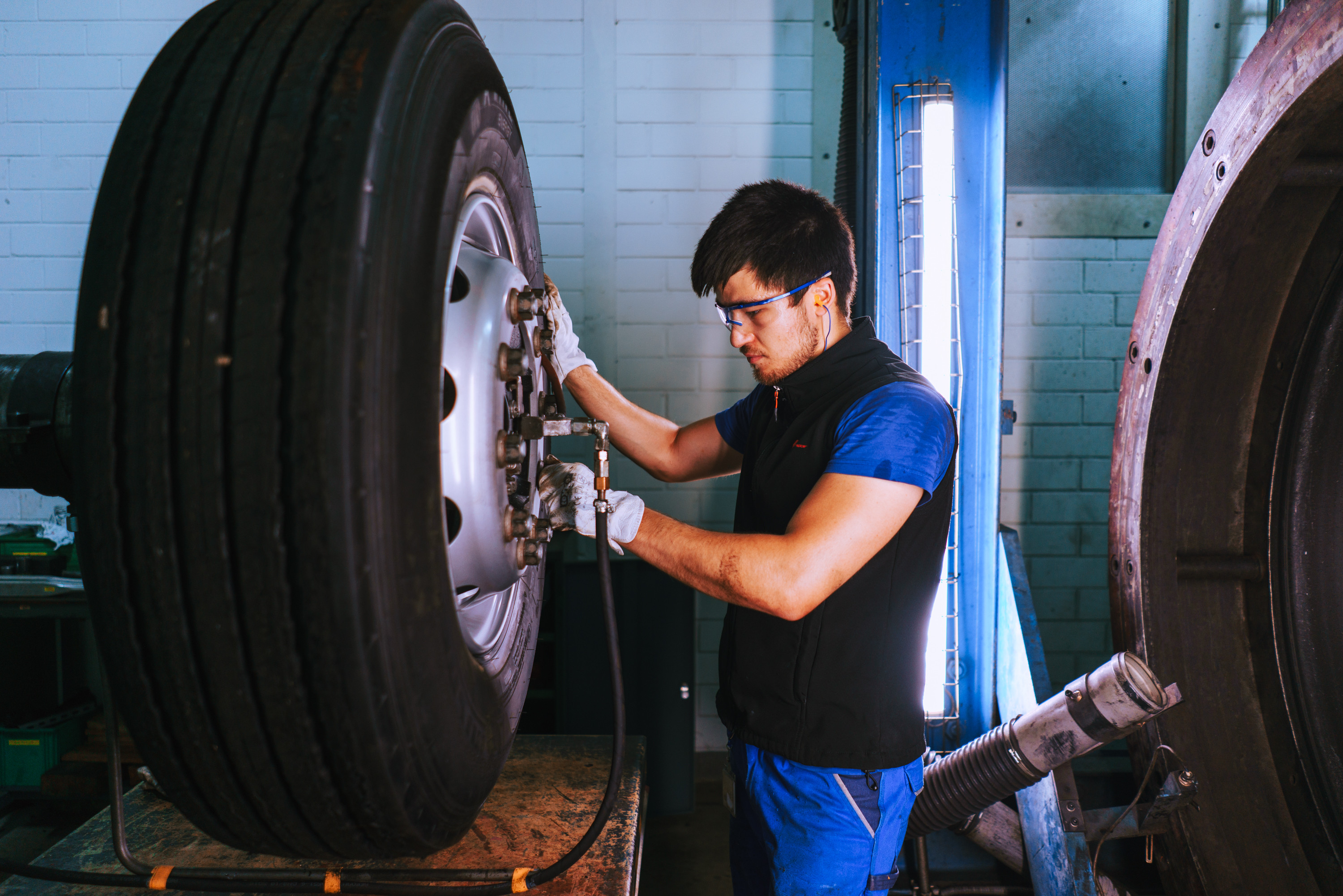
Technician working on a truck wheel
Background to steel wheel production at Maxion
The deceptively simple and utilitarian steel wheel which rolls off the production line at any one of Maxion’s several facilities today is in fact the result of many years of development under various entities which no longer exist. The first of these to begin operating was Hayes Wheels, founded in the United States in 1908 to produce wooden spoke steel wheels for the Ford Model T. The company quickly moved through producing wire spoke wheels before settling on steel disc wheels for the passenger car market. For trucks, it initially produced wheels with a cast iron disc before changing to wheels with discs made of pressed sheet steel.
The factory in Königswinter, where Maxion Wheels is based today, was opened in 1919 by the German company Lemmerz. The business was eclectic at first, involved in segments such as motorboats and motorcycles before it reduced its focus to wheels for the passenger car, commercial vehicle, and agricultural vehicle markets. In 1997, Lemmerz became part of Hayes, and the resulting firm was called Hayes Lemmerz International Inc. By this point, the company was already a worldwide concern, with facilities and joint ventures in Europe, Turkey, Brazil, India, and North America, and it was the desire to serve the global market which led to the truck wheel’s uniformity of design and production. Before that, truck wheels were more diverse, with production separated between different countries and regions and with designs reflecting local market conditions.
The Maxion name comes from Brazil. Starting as a logging company in 1918, Iochpe later made several acquisitions, including Indústria de Màquinas Agrícolas Ideal (“Ideal”) in 1978 and Massey Ferguson Perkins SA in 1983. Having licenses to build International Harvester and Massey Ferguson agricultural machinery in Brazil, Iochpe merged the two acquisitions, creating the ‘Maxion’ brand. Iochpe subsequently divested itself of the agricultural machinery business and restructured Maxion to focus on automotive parts. Further acquisitions in the 2000s – including assets belonging to the wheels businesses of Meritor and Nugar SAPI de CV – marked Maxion’s proper entry into the wheel industry. With the acquisition of Hayes Lemmerz in 2012, Maxion finally took on the form which is recognisable to us today – as one of the world’s foremost manufacturers of steel and aluminium wheels.
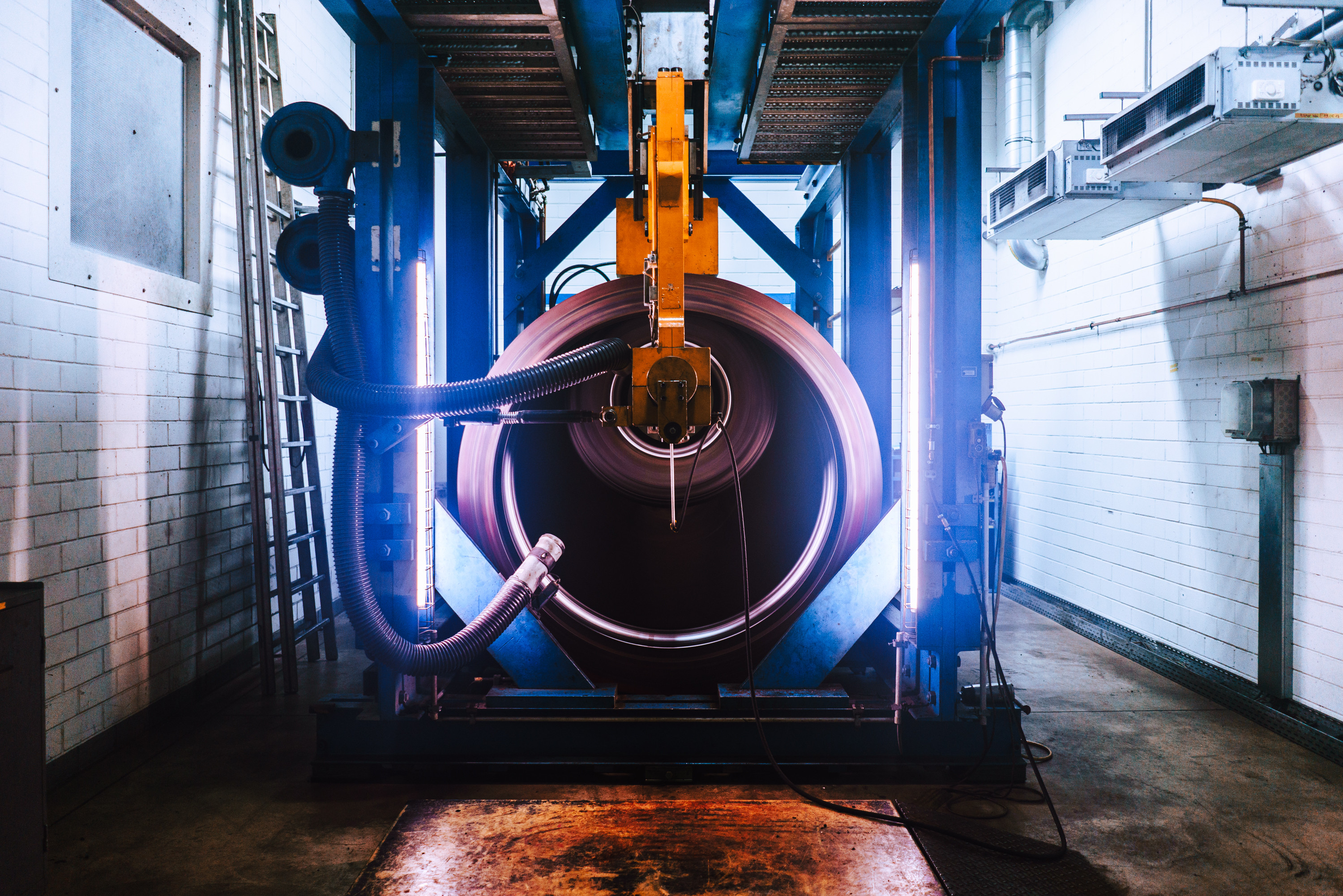
Biaxial wheel testing
Contemporary design and production of steel wheels
At the former Lemmerz factory in Königswinter, Maxion serves the European truck market, primarily with a wheel sized at 22.5x9.00. Steel wheels of this type have been produced in Königswinter since as far back as the late 1990s, when it weighed roughly 41 kilograms. At that point in time, Rode recalled, the manufacturer was shifting from a wheel design with an internal valve to one with an external valve. Wheels featuring an internal valve had a marked disadvantage: debris getting caught between the brake disc and the wheel, such as gravel, could end up damaging and even tearing off the valve. With an external valve, Rode said, that flaw could be avoided, but with the cost of adding extra weight to the wheel.
It was at that point that efforts at Hayes Lemmerz to reduce weight began in earnest, and this work has been continued by Maxion Wheels up to the present day. In generational leaps and bounds, the company successfully reduced the weight of its most common steel wheel for trucks down to 38 kilograms in 2010, to 36 kilograms in 2014, and 34 kilograms in 2017. Today, Maxion produces truck wheels as light as 32 kilograms, meaning that it has shed 9 kilos since 1997. What this means for the operator is a payload increase of 40 kilograms or more, as well as fuel efficiency gains from the reduction in wheel mass.
Shedding weight in the truck wheel is not as simple as putting it on a diet. It means treading a very fine balance between mass and strength. For every kilo lost, Rode and his engineers must carefully tune the design of the wheel and the grade of the steel in order to maintain its robustness. It involves a great deal of experimentation and testing, trying out different shapes and material grades to see what works best. Rode has even worked with different metallurgical processes to try and get the desired result. One such process is the hot forming of wheel discs; Rode told T&BB however that he was “unhappy” with the results of this experiment. His team found that not only would it require a “huge investment” to implement, but it also produces less than desirable results with regards to the wheel’s notch sensitivity (i.e., the relative strength of those locations on the wheel where the stress is significantly greater than the surrounding area). When it comes to playing around with different material grades, Maxion engineers must work closely with their suppliers to ensure the quality and suitability of the steel. “Everything that is in the material itself,” said Rode, the “ingredients that make the steel hard, that makes it deformable, that makes it robust, that makes it hardenable,” are determined before the steel is rolled and delivered to the Königswinter factory.
To make sure that a steel wheel concept is up to the job of moving a truck, it must undergo a thorough programme of testing. “The wheels are designed for the complete life of the truck, and in several cases, they last even longer than the truck itself,” Rode told T&BB, and so it is essential that every new wheel design is able to bear the rigorous demands of the truck.
The simplest determinant of a wheel’s suitability for the job is the maximum wheel load, i.e., the load capacity that the wheel has to bear over the lifetime of the vehicle. This is not enough on its own, however, to guarantee the quality of the wheel, and so it must pass a further series of assessments, which Rode broke down into three steps. The first step is the “cornering fatigue” test, which simulates the scenario of a vehicle going around a corner. The wheel is placed on a test rig and a rotating force is applied. The second step is the “rim rolling” test, which is carried out with a tyre fitted onto the wheel. This simulates the wheel rolling straight ahead without turning. The third step is the “biaxial wheel” test, a dynamic fatigue assessment which puts the wheel under combined variable radial and lateral loads. Maxion carries out its steel wheel research and development at its Global Engineering Centre in Königswinter, where it carries out tests according to the requirements of the Association of European Wheel Manufacturers (EUWA). These require the wheel to endure a minimum of 200,000/2million cycles in the first test, 500,000 cycles in the second test and up to the equivalent of 16,000 kilometres for the third test. In the first test, Maxion tests its wheels to the point of failure, which can be up to 2 million cycles on the test rig.
Research and development into new wheel designs has progressed significantly thanks to the use of computer-aided engineering (CAE). For example, by using the finite element method, engineers can analyse and assess the structure of a new wheel concept before producing a prototype, reducing the cost and time expended in bringing a product to market. Other tools are employed to push the design of the steel wheel to its limits, finding new shapes and thickness profiles to achieve the utmost weight reduction without compromising on strength. The 32-kilogram weight of the current Maxion truck wheel is a considerable accomplishment, but Rode says that “it’s not the end of the story.”
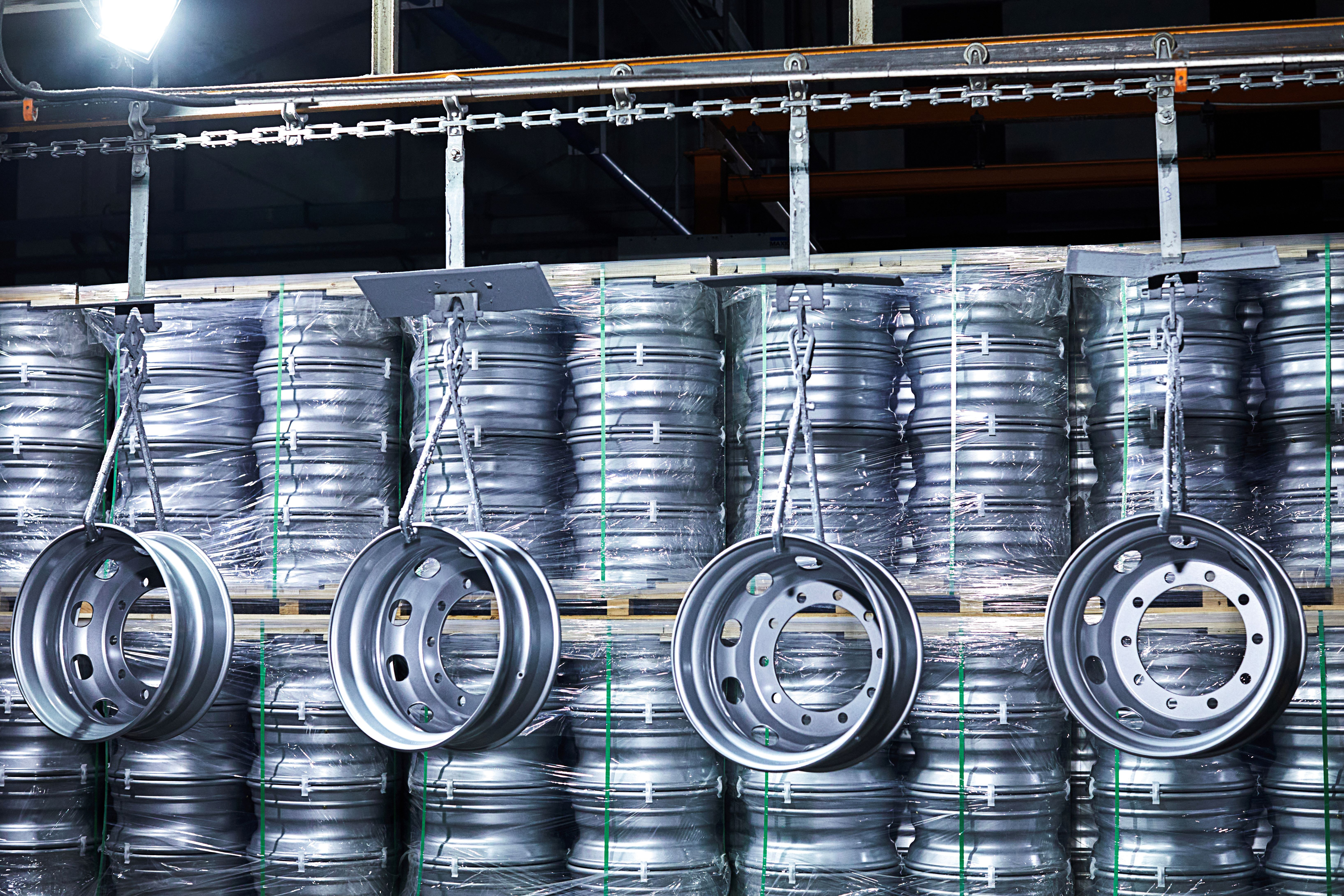
Stacks of finished steel wheels
The future of the steel truck wheel
When considering the future opportunities and challenges faced by its steel wheel business, Maxion must look at two topics: sustainability and e-mobility. While the first presents more opportunities than risks, the picture is still very mixed. The opportunities come from the smaller carbon footprint of a steel wheel relative to aluminium, a factor which could give steel wheels the edge in the market as sustainability increases in importance. The challenges come from the higher costs involved in sourcing renewable steel, resulting in higher prices for the final products.
With the 22.5x9.00 steel truck wheel, produced in the conventional way at Maxion’s Königswinter plant, the cradle-to-gate CO2 emissions per wheel are 133.45 kilograms. Using “green” or renewable steel, this figure can be brought down to 44.9 kilograms CO2 equivalent, a 66% reduction. Maxion is more than ready to supply “green” truck wheels to its customers, but Mommers told T&BB that its OEM customers are reluctant to switch to them just yet. This is because of the relative lack of renewably produced steel available on the market, which means that prices are obstructively high. “Green steel will definitely come”, Mommers said, and when it does, he expects it to replace conventionally produced steel as the standard. “From a specification point of view,” he added, “there is no difference between green steel and normal steel.” However, replacing their truck wheels with green steel ones is not yet a high priority for the OEMs, and Mommers was unable to put a date on when the transition would come; though we should expect the momentum to pick up as we get closer to the deadlines for the vehicle manufacturers’ sustainability targets.1
The growing number of electric vehicles presents more of a challenge for the world’s wheel manufacturers. “It’s a known fact,” said Rode, “that batteries will lead to additional weight,” and therefore additional strain, on the wheels. What this means is that for all chassis components, including the wheels, the engineer must assume an increase in load capacity of about 10%. In designing the first dedicated wheels for EVs, Maxion’s aim is to keep them at a similar low weight as current wheel generations while increasing their load capacity. However, the advent of electric vehicles has other and perhaps more surprising implications for wheel design. Assuming that much of the braking energy in an EV will be recuperated instead of wasted as heat, then there will be less need for the ventilation holes which are ubiquitous in vehicle wheels and which contribute a great deal to their appearance. The need to cool down the brakes will be reduced, and therefore wheel makers will be able to experiment with designs that would not be suitable for a conventional vehicle wheel. Indeed, there is the possibility to reduce the size of the holes – as far as will still allow some ventilation for emergency braking, for example – and therefore achieve gains in aerodynamics, which is something that Maxion has demonstrated through simulation.
The wheels fitted on the trucks of the future will probably be made from renewable or “green” steel. They will need to be made differently in order to accommodate the greater load of the lithium batteries. And they may even look different than before. But both Rode and Mommers were clear about one thing, that steel wheels will continue to dominate the heavy vehicle market and control much of the lighter CV market too. They will probably be made in much the same way as before, with many of the same properties as before. And, as always, the engineer will continue to maintain the tightrope balance between weight and strength, aiming for the lightest and strongest wheel possible.
1 For more information on the topic of sustainability at Maxion, see our previous feature: https://truckandbusbuilder.com/article/2024/02/20/green-transformation-oliver-schwank-talks-to-tbb-about-sustainability-at-maxion-wheels
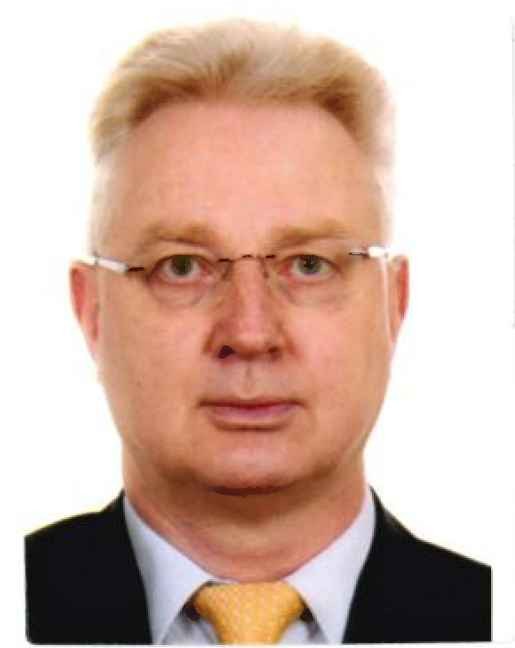
Karl Rode began his career with Lemmerz in 1989, when he was employed as a simulation specialist in finite element analysis. In 1997, he was made product engineering manager for all passenger car applications for the newly-formed Hayes Lemmerz company. He switched to steel wheels for passenger cars and commercial vehicles in 2011, before being appointed to his current role, as Director Engineering Steel EMEA&ASIA for Maxion Wheels, in 2018.
Stan Mommers became a key account manager at the Hayes Lemmerz concern in 2007 and swiftly moved up through multiple sales director positions for HL and later Maxion Wheels until becoming Executive Sales Director, with responsibility for the truck segment, in the EMEA market in 2018. In 2023, he took up his current role as Vice President Sales EMEA, with responsibility for all segments.