IAA Transportation 2024: T&BB talks to Matt Brest about Maxion Wheels’ new forged aluminium CV wheels ahead of Hanover show
By Bradley Osborne - 3rd September 2024
Latest drone shot of forged aluminium plant in Manisa, Turkey
Turkey – Last month, I wrote about the background of Maxion Wheels’ manufacturing activities in Turkey and the investments which have been made in its steel and aluminium wheel plants there. However, I made only brief mention of a very recent and significant development at the Manisa site: the construction of a new plant for forged aluminium wheels, designed not for light vehicles but for heavy trucks and other commercial vehicles. The decision to enter the CV aluminium wheel market was announced by Maxion Wheels at the last IAA Transportation in 2022; the news is important enough that it deserves an article to itself, and so I interviewed Matt Brest, Senior Product Manager for Commercial Vehicle Wheels, ahead of IAA Transportation 2024, where Maxion Wheels will show its forged aluminium wheels to the public for the first time.1
The slated production launch of 2025 at Manisa will mark the company’s first step into the CV aluminium wheel market. One is bound to ask why Maxion Wheels is taking the risk to move into this new market when it already has a strong reputation for CV steel wheels – and then the question of whether aluminium is really any better than steel naturally arises. Answers to these and other questions are presented below, but it would be convenient to raise two quick points at the outset. The first is that aluminium wheels are considerably lighter than steel ones. Over many years, Maxion engineers have worked to bring down the weight of steel truck wheel to 32 kilograms; an aluminium truck wheel of a comparable size (22.5/9) weighs 23 kilograms. Just by changing the material of the wheel, Maxion can immediately shed nearly 10kg, and further weight losses may be possible in the future. The second point is that the addition of the forged aluminium wheel significantly expands Maxion’s coverage of the market. Sweating assets and getting the most out of one’s fleet are crucial to any operator, but some are more than willing to pay a higher price for aluminium wheels in order to benefit from the lighter weight – and other advantages – compared to steel. If fleets become increasingly made up of vehicles carrying heavy battery packs, then shedding weight everywhere else – including the wheels – will become a top priority for fleet buyers.
One of the most important markets for CV aluminium wheels today is North America, which has seen widespread adoption by trucks especially over the past several years. This is a market which Brest believes has hit a “saturation point”; Maxion Wheels is therefore setting its sights on Europe, where the trend towards aluminium in CV wheels is somewhat behind North America. Brest is convinced that there is an opening for another supplier to enter the CV aluminium wheel market in Europe, and Maxion intends to struggle head-to-head with its competitors for a share of the sales.
Brest told T&BB that construction of the forged aluminium wheel plant in Turkey is now complete. The next steps are to install the manufacturing equipment, before kickstarting production of the first wheels by the middle of 2025. Following several months of qualification and approvals, Maxion Wheels hopes to begin serial production by the end of the year, with deliveries starting around the same time. Covering an area of 20,000 square metres, the plant will have an installed capacity of 300,000 forged aluminium wheels a year. When, in the future, the plant is extended by an extra 10,000 square metres, the annual production capacity could be doubled.
1 Thanks is also due to Adrienne Hattingen of Maxion Wheels, who provided some of the figures and information relating to sustainability presented in this article.
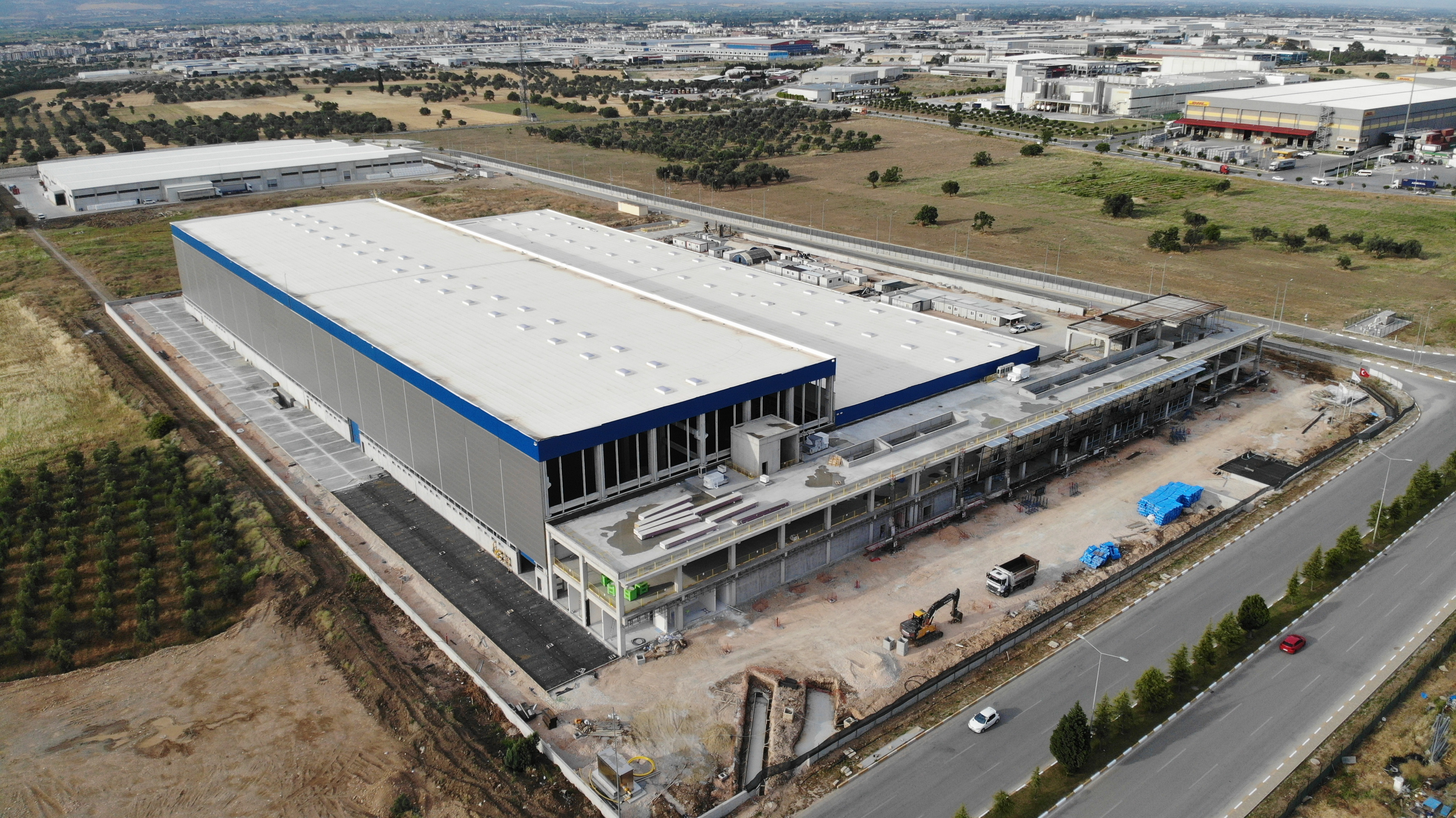
Another drone shot of the Manisa facility
Aluminium wheel forging process
The process which Maxion Wheels has selected for the production of truck aluminium wheels is essentially different from that which it uses to produce its light vehicle aluminium wheels. Whereas the light aluminium wheel is made in a casting process – that is to say, the alloy is poured into a mould and solidified in the desired shape – the truck aluminium wheels will be made in a forging process. The alloy is heated up, shaped with a machine tool called a ‘die’, and then allowed to cool.
The composition of the forged aluminium wheel is purer than the cast aluminium wheel. Cast aluminium is composed of roughly 7% silicon, which is added to the alloy in order to help it flow into the mould. In the forged wheel, the alloy1 is approximately 97% aluminium, providing it with greater strength than the cast wheel.
The forging process currently under development in Turkey combines aspects of cast aluminium wheel with CV steel wheel production, according to Brest. It begins with a cast bar which is shaped like a log, measuring seven metres in length. The aluminium ‘log’ is cut into pieces, and then the pieces are heated up. Once the pieces are hot enough to be shaped, they are fed through progressive dies that manipulate the molten alloy into the desired form – in this case, the round shape of the wheel hub. Using a force of up to 10,000 tonnes, a large press squeezes each piece into the wheel-like shape. A further “flow-form” process creates the wheel rim: this is done by flowing the rim portion of the wheel over a rotating mandrel. At the end, you have a complete aluminium wheel, forged using tools and methods which are not all that different from those used currently to make CV steel wheels.
However, the aluminium wheel is not yet finished at this point. First, the wheel must be heat treated, and then quenched and aged. Following treatment, the wheel is machined, meaning that the shape is refined by removing material with machine tools. This is when the bolt holes and ventilation holes are made. Finally, the wheel is polished and given a surface treatment (optional) and is then ready to go. While the aluminium forging bears similarities with the steel wheel manufacturing process, the subsequent treatment and machining resembles the process Maxion employs to finish its cast aluminium wheels.
1 To be specific: the alloy used by Maxion Wheels for its forged aluminium is ‘6061-T6 ALU’.
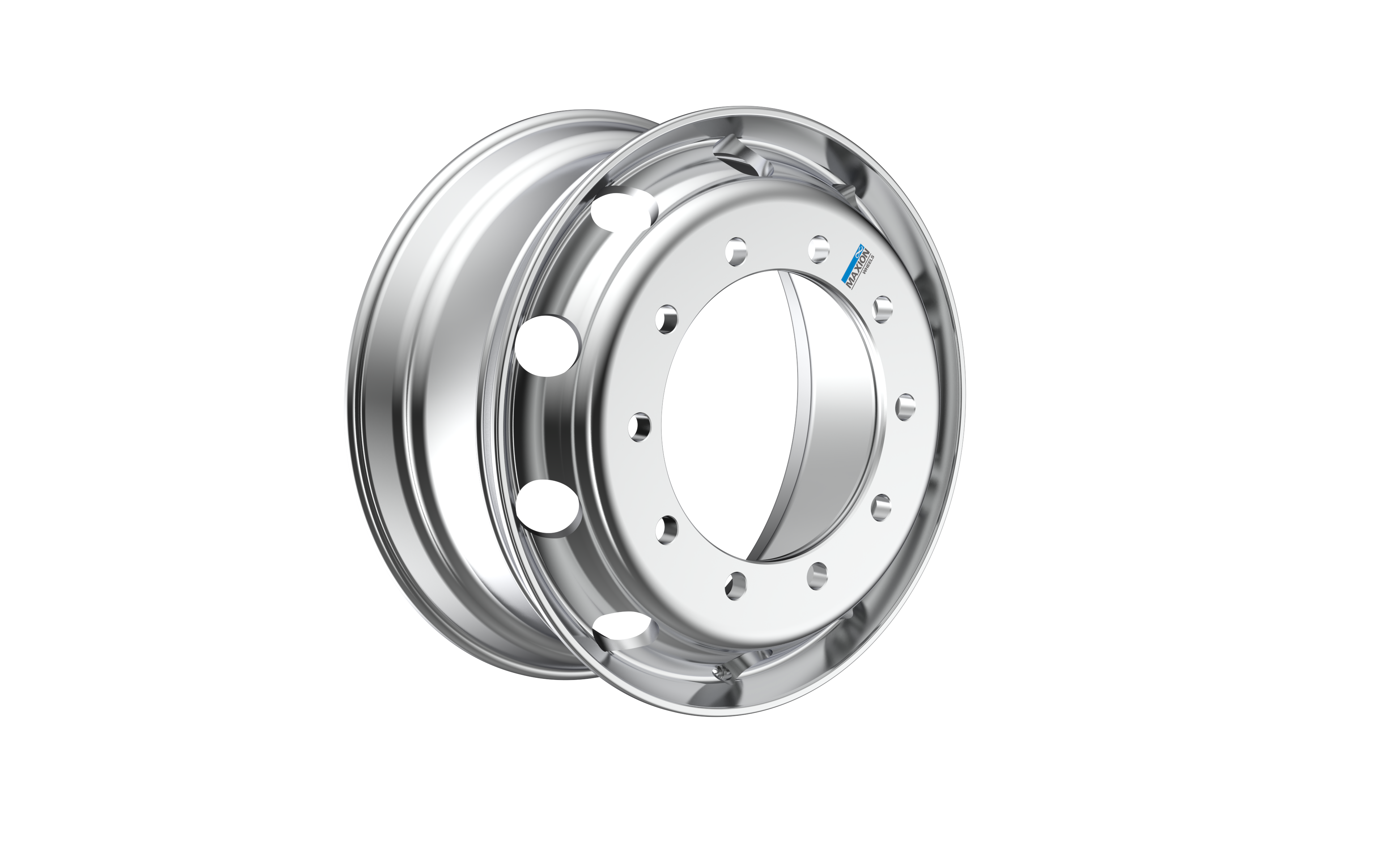
Render of Maxion forged aluminium wheel for CVs
Properties and applications of the forged aluminium wheel
In order to appreciate its unique qualities, the forged aluminium wheel must be compared against both the cast aluminium wheel and the CV steel wheel. Compared to the cast aluminium used in light vehicle wheels, forged aluminium is far stronger – as much as 50% stronger, according to Brest. It owes this extra strength not only to the higher proportion of aluminium in the alloy, but also to the forging process itself. For instance, when the alloy is pressed into a wheel-like shape, any porosity (i.e., empty spaces within the alloy) is removed; and when it is heat treated, its material properties are enhanced even further.
As mentioned at the beginning, the forged aluminium wheel is far lighter than an equivalent wheel made of steel, by approximately 30%. However, its lighter weight is not its only advantage over steel. When the wheel leaves the heat-treating process, it is “fully turned”, giving it a better “run out”. In other words, the forged aluminium wheel, while not “perfectly” round, is rounder than its steel counterpart, and this property gives it better balance and leads to less vibration when it is on the road. The driver may or may not notice any difference, “but the tyres and suspensions certainly will,” said Brest, meaning that they wear at a reduced rate. Another property which aluminium boasts is greater conductivity compared to steel: this means it can transfer heat as much as three times faster. Again, this means that connected parts will not wear out as quickly: the aluminium wheel will conduct heat away from the tyres and brakes at a faster rate, thus extending their service life.
One more advantage which may seem trivial – though it is very important to some customers – is improved aesthetics. “One reason people pay a lot of money for aluminium wheels is, they look great!” said Brest. “If you go to websites for heavy trucks, they’re probably going to have aluminium wheels – that’s the top of the line.” Though the styling options for a forged wheel are more constrained than those available for a cast wheel, they provide customers with greater flexibility than they would have with a steel wheel, and the end result is shinier and far more attractive.
Without a final surface treatment to maintain the clean and shiny surface, the forged aluminium wheel will quickly become a dull grey. However, unlike the cast aluminium or forged steel wheel, the forged aluminium wheel does not need to be coated, making it “a very durable product from a corrosion standpoint,” according to Brest. For customers who do not mind if their wheels lose their shine, the anti-corrosiveness of the uncoated wheel is a far more attractive quality. Brest gave the example of bulk haulers who look to shed as much weight from the vehicle as possible in order to maximise payload. With forged aluminium wheels, the bulk hauler “can easily take fifty kilograms of weight off – that’s fifty kilograms of extra load, every trip, that he’s able to carry and dispense.”
By shedding weight from the wheels, hauliers can carry more payload; by taking fewer trips to carry the same amount of goods, emissions will be reduced. From this standpoint, forged aluminium wheels are more sustainable than their steel counterparts. But this does not take into account the emissions produced in the manufacturing supply chains of aluminium and steel. While the environmental impact of the wheel forging process does not differ greatly between aluminium and steel, the production of the aluminium alloy is far more carbon intensive. Considerable amounts of energy are needed to convert the raw material (from bauxite to alumina to aluminium) into a form which is ready for forging. If the energy is sourced from renewables, the carbon footprint will be reduced; however, “green” aluminium still makes up a small percentage of the global production capacity.
A forged aluminium wheel will have a footprint of approximately 150kg CO2e greater than a steel equivalent, due to the energy needed to process the raw material. Replacing one steel wheel with an aluminium one yields a 0.05% weight improvement, which would lead to savings of around 18kg CO2e over 100,000 kilometres (supposing a payload of 13.5t). In this scenario, it would take over 800,000 kilometres of use to offset the carbon “debt” (compared w/ steel) incurred by its manufacture. Only from this point onwards would the aluminium wheel become the “greener” choice compared to the steel wheel.
Despite the weight and payload advantages, then, the aluminium wheel today is not really a sustainable alternative to the steel wheel. However, the forging process for the aluminium wheel does allow for significant reuse of material that would otherwise be wasted. Chips of aluminium alloy that come off during forging can be remelted and incorporated into a new wheel. Moreover, the aluminium suppliers increasingly use this “secondary” or recycled aluminium in their raw material production.
Groundbreaking ceremony at Manisa site in October 2022
The market for forged aluminium wheels
Maxion Wheels will initially focus on selling its forged aluminium wheels to customers in Europe. Compared to the North American market, the European market for CV aluminium wheels is far less developed. Maxion Wheels estimates that there are three steel wheels for every aluminium wheel in the European truck-trailer market. In North America, on the other hand, there is a far greater proportion of aluminium wheels sold. In the Class 8 tractor market in particular, the penetration rate of aluminium wheels is a staggering 80%. There is considerable variation, however: in the North American trailer fleet, around 20% are fitted with aluminium wheels. Across the whole truck-trailer market, the respective shares of aluminium and steel wheels are roughly equal.
Brest believes the European market could head in the same direction as North America. “It’s a question of how much, how quickly,” he said. However, he does not expect there will be a dramatic shift comparable to that which occurred in the car market over a decade ago. Brest envisages that the share of aluminium wheels versus steel wheels could reach 50/50 in Europe, but this is likely to be gradual. As in North America, he expects there to be more aluminium wheels on trucks and fewer of them on trailers.
Maxion’s current installed capacity for commercial vehicle steel wheels stands at around ten million globally. It therefore has little to gain from a wholesale replacement of steel wheels with aluminium ones. The point, Brest said, in offering forged aluminium wheels is to provide “complete flexibility” to the customer. Maxion Wheels will be able to offer the full range of options to its customers, ensuring that they pick they best option for each application. By looking at the customer’s needs, based on the use profiles of their vehicles, the lifecycle of their trucks, the region in which they operate, and so on, Maxion Wheels will be able to recommend either steel or aluminium as the superior choice for any given scenario.
Because Europe is an ideal target market for the forged aluminium wheel, and also because of the company’s successful joint venture in Turkey, the site at Manisa was chosen for the launch of production. While some of its competitors’ wheels are exported to Europe from Asia, Maxion Wheels will be able to supply products that are locally made, using resources and expertise that are established in Turkey and are proven to be reliable. Brest is hopeful therefore that Maxion Wheels can “jump straight into” the European market.
Finally, I asked Brest why Maxion Wheels had taken the decision to enter the forged aluminium market now; or, to put it another way, why the company had not done so earlier. He said:
We are one of the leading manufacturers for commercial vehicle steel, light vehicle steel, and light vehicle aluminium wheels in the world. It’s been a natural progression for us to eventually invest in forged aluminium wheels and extend our reach to those applications where aluminium is the preferred solution. The new wheels complement our existing market-leading steel wheel portfolio providing customers with a compelling, one-stop alternative in a market previously limited in choice.
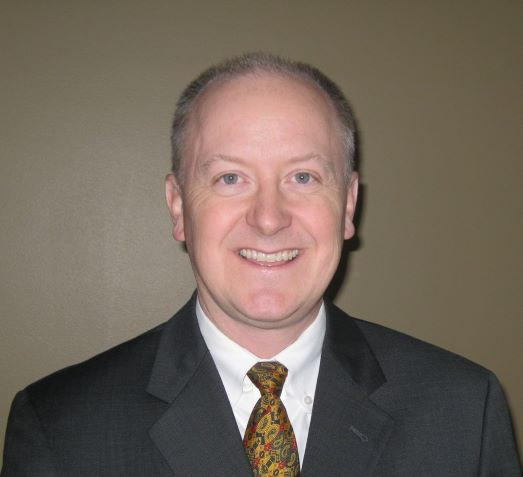
Matt Brest is Senior Product Manager for Commercial Vehicle Wheels at Maxion and has 35+ years of experience in the industry. He has held multiple leadership positions in both engineering and sales within Maxion Wheels’ North American operations, focusing on commercial vehicle and defence applications. Prior to joining Maxion Wheels in 2019, Brest worked in product design and engineering, R&D, and market strategy at Alcoa Wheels.