Bucking the trend: T&BB visit to British startup firm Sunswap
By Bradley Osborne - 22nd April 2025
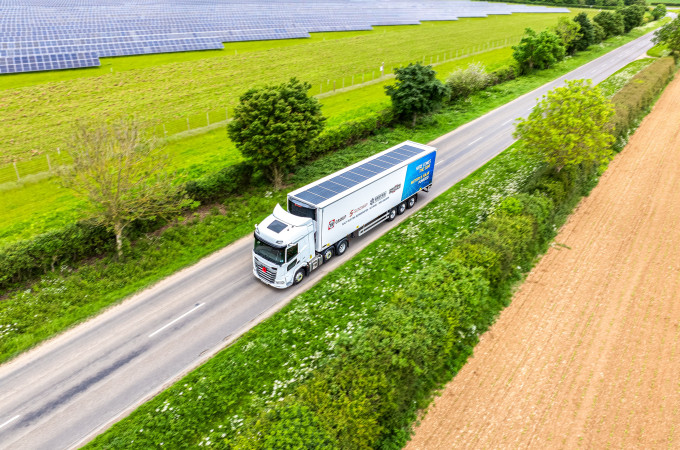
Sunswap's solar technology working on the road
UK – Readers of Truck & Bus Builder will be accustomed by now to news stories reporting the demise of yet another electric vehicle startup. Particularly in Britain and in the USA, several new companies in receipt of millions of dollars of investors’ money – either through venture capital funding rounds or the stock market – have faltered in the past year, reducing their business activities to a fraction of their original scope or ceasing to trade altogether. Yet, in late 2024, while all of this was going on, a small British firm successfully raised a sum of GBP17.3m from investors who could justifiably have refused to cough up a single penny towards yet another electric vehicle proposition. Bucking the trend, Sunswap Ltd is showing that a new entrant can bring out a product that is economically as well as environmentally sustainable.
One of the reasons behind Sunswap’s success is its relatively modest ambition. Rather than trying to build an entirely new vehicle and associated infrastructure from scratch, the British startup is addressing a niche market with a specific solution that demonstrates immediate benefits for its customers. Its sole product is a transport refrigeration unit called ‘Endurance’, an all-electric system which can be installed on any reefer or temperature-controlled truck on the road today. Endurance is powered by batteries installed inside the unit which can be conventionally recharged through shore power while the vehicle is parked at the depot or a truck stop. Its key selling point, however, is that the batteries can also be topped up by solar energy, generated by panels installed on the roof of the trailer or truck body. Depending on the weather conditions, a fully charged unit can achieve the following run times with the support of solar energy: twenty-four hours for frozen goods; two days for multi-temperature; and two months for chilled goods.
Of course, an Endurance unit which is married to a diesel truck or truck-trailer combination will not eliminate the vehicle’s emissions entirely. However, by reducing the refrigeration unit’s emissions to zero whilst the vehicle is running, Sunswap’s product provides the operator with an option that can not only decrease the carbon footprint of the overall fleet but also slash fuel costs. The solution is consequently being taken up by logistics firm DFDS and trailer rental group TIP; the former claims it could remove 895 tonnes in CO2 emissions from its fleet and save around 500,000 litres of diesel by operating 10 Endurance units over a ten-year period.
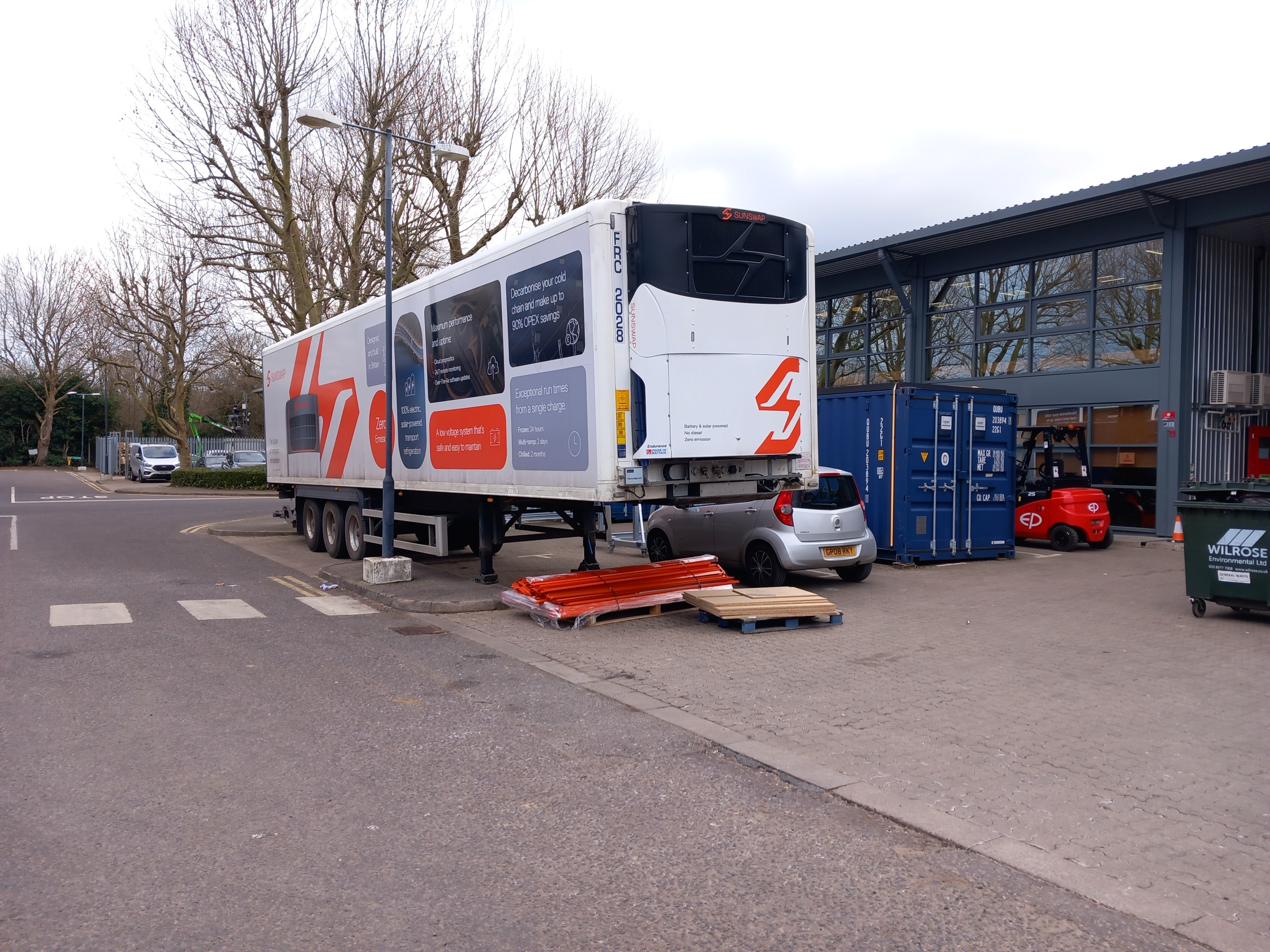
Sunswap's Endurance unit outside of its facility in Leatherhead, England
Last month, I visited the production facility in Leatherhead, England and spoke to the CEO, Michael Lowe, to find out more about the company, and I was struck by the smallness of its operation. Nowadays, the industry talks favourably of so-called “lean manufacturing”, but I do not believe I ever saw a truly “lean” operation before visiting Sunswap. The production facility is the smallest I have seen, packing product assembly, parts storage, and commissioning into a space no larger than the average vehicle workshop. I was informed that the layout of the production facility was still a work-in-progress and did not reflect its full capacity; nevertheless, what I saw was a diverse and functioning assembly line with a bespoke digital platform for tracking every part in the entire process. Many of the parts – including the batteries, the refrigeration components, and the solar panels – are not made by Sunswap but are supplied by other manufacturers. Sunswap’s core competencies are its software for energy management and its expertise in integrating different subsystems to create a high-quality product. According to Lowe, the majority of Sunswap’s engineers are generalists, with a broad systems-based knowledge of mechanical, electrical, and software engineering.
Lowe told T&BB that the company had to learn early on how to “pay its own way”:
Unlike many other startups, we began with very modest sums of money, and this restraint has informed our decision making – we have to always ask, do we actually need this or that product feature, facility expansion, and so on.
Although the company has grown swiftly since it was founded in 2020, sensible growth rather than rapid expansion has been the name of the game at Sunswap. The current plan is to scale up to a yearly production capacity of five hundred units at the Leatherhead facility in 2026; beyond that point, Lowe would not reveal any further details. “We will assess our expansion plans based on how the next year or so goes.”
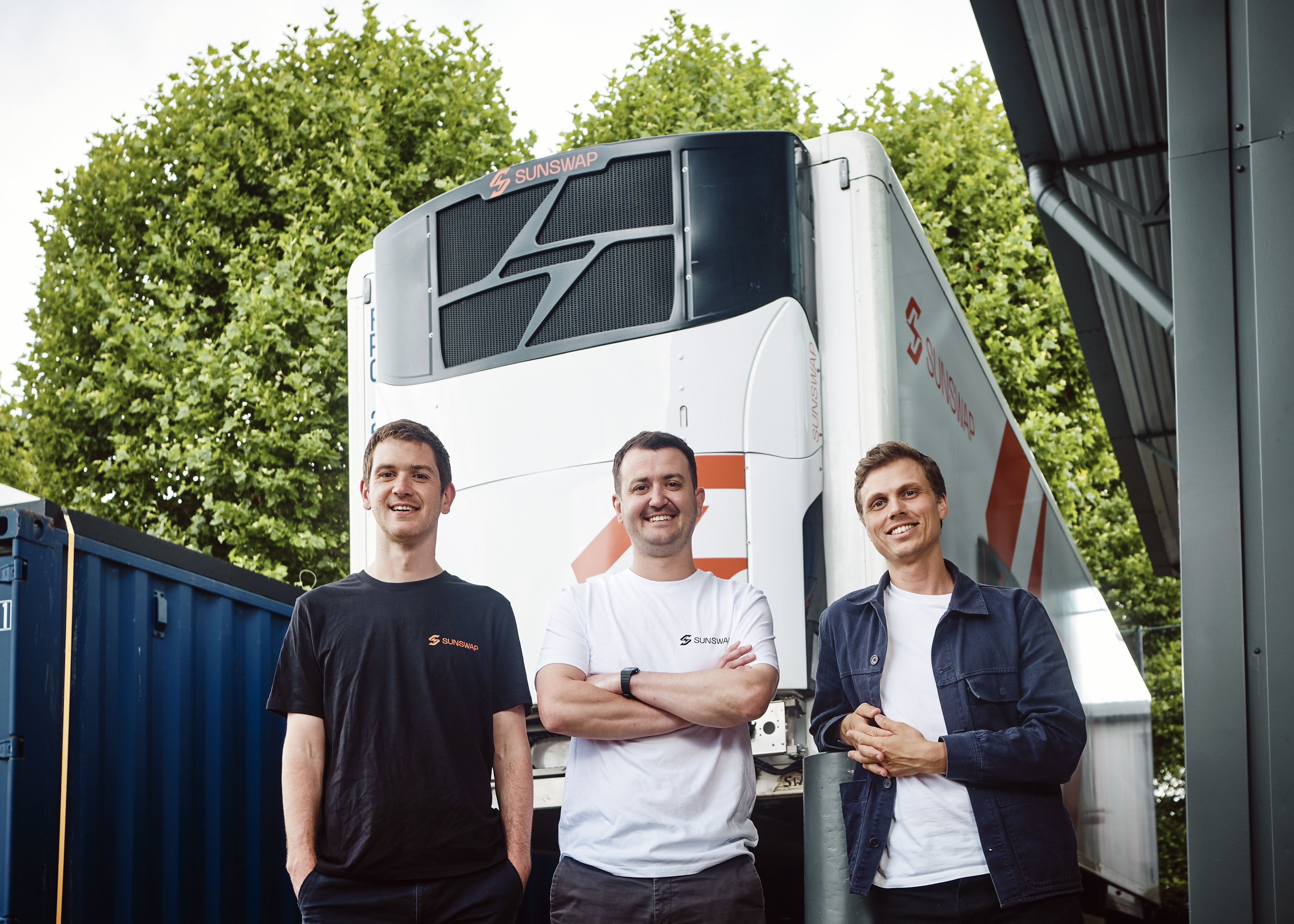
Sunswap founders, from the left - Andrew Sucis, Michael Lowe, and Nikolai Tauber
Background to Sunswap
Sunswap is the creation of three men: Lowe, Nikolai Tauber (now the Chief Technology Officer), and Andrew Sucis (now the Chief Operations Officer). Lowe was an automotive engineer at Ricardo, whereas Tauber and Sucis come from backgrounds in thermal systems and aerospace engineering, respectively. The three quit their jobs to found Sunswap in 2020, starting off with enough of their own private capital to sustain them for three months. The team successfully secured seed funding of £150,000 which enabled them to build their first solar-powered refrigeration unit. This prototype, called ‘NVD’, was not zero emission, as it was still powered by a diesel engine. The engine was dropped in the second generation, development of which was funded by money raised on crowdfunding platform Crowdcube. According to Lowe, Sunswap raised half a million pounds in the space of three days. With this injection of capital, the startup was not only able to continue technological development but also hire its first employees and launch its first customer trials.
The second-gen unit was the first to incorporate lithium battery packs, up to a capacity of 45 kilowatt hours. The first customer to test Sunswap’s technology was logistics firm Gist, which took on a single unit for its temperature-controlled fleet in 2022. In March of that year, Sunswap secured Barclays and the Clean Growth Fund as backers, enabling the company to move from demonstration to production. The Endurance units which I viewed at Sunswap’s facility in Leatherhead are production-ready models with energy capacities of up to 75 kilowatt hours. With the GBP17.5m investor funds raised in late 2024, Sunswap has now entered its scale-up phase. It tripled its workforce to more than one hundred people over the past twelve months and is currently expanding its production capacity from one to five hundred units per year.
When Sunswap’s founders started building their first unit, they set up shop in a carpark shed near London Bridge. After securing seed capital, the company moved to a site in Wimbledon which it occupied for two years before starting the transition in 2023 to the current location in Leatherhead. The company’s location in the county of Surrey has proven to bring the best of two worlds: home counties engineering heritage and proximity to London. The counties surrounding the capital city – especially those on the south coast – are home to several motorsports companies and engineering consultancies, including Lowe’s former employer, Ricardo. On the other hand, London itself is a major source of both investor capital and talent. In Lowe’s view, London is probably second only to the USA in the amount of capital available for innovative startups. The company takes pride in its “Made in Britain” designation and has no plans to move away from Leatherhead; in fact, it is looking at the local area for potential sites to expand its business in the near future.
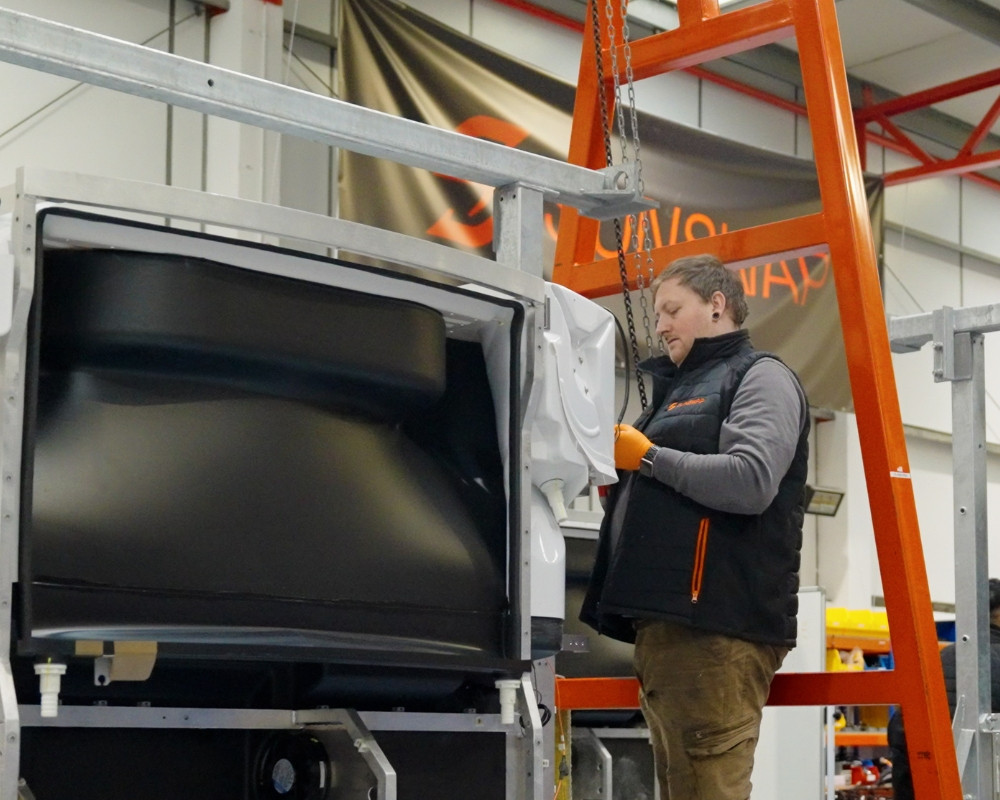
Inside Sunswap's production facility
The production facilities in Leatherhead
Sunswap works out of two buildings on Mole business park in Leatherhead. The first is the company’s main production facility where it assembles the Endurance refrigeration units, while the second is the home of Sunswap’s head office as well as a research and development space. When the company first moved to Leatherhead, it occupied only the first building and carried out all of its activities from there; more recently, it took over the second in order to free up more space for production in the former building.
The production facility is a 750-square-metre space, incorporating the assembly line, parts storage, and commissioning area. In the first phase of assembly, the line is split into two branches which are each responsible for building one half of the refrigeration unit. In the upper half of the unit, compressors and other refrigeration components are installed along with various sensors for data collection. Once these parts are in place, the upper half of the unit moves to an area which is cordoned off from the rest of the production floor. Here, the pipe joints are brazed before the unit is put through comprehensive strength and leakage tests, which are a legal requirement for refrigeration units produced for the European market.
Parallel to the upper half, the battery packs and associated electronics are installed on the bottom half of the refrigeration unit. These batteries are lithium iron phosphate systems which are sourced from suppliers (mainly Chinese, from what I could gather). They are low-voltage units – under 60 V – which are relatively safe to handle and do not require technicians to complete special high-voltage training in order to work with them. A single Endurance unit can carry up to six battery modules, with each module comprising four battery packs. The batteries are stacked on the lower half of the refrigeration unit and the control display unit is also installed during this phase of assembly. This half of the unit is designed to regulate the temperature of the batteries, with heating strips and extruded shelves for drawing air through unit.
Once subassembly of the two halves of the unit is completed, there comes the “marriage” or “mating” of the two, as the company calls it. A gantry system is employed to lift up the top half of the unit and install it on the bottom half. After the two parts are “mated”, the cable and exterior assembly takes place. In a separate part of the production space parallel to the exterior assembly, subassemblies of the power distribution unit and control systems are carried out before being installed on the main unit. At this point, the edge computing hardware is also fitted, serving as the cloud gateway for unit data.
Now the refrigeration unit is fully assembled, it moves on to the commissioning area where every actuator, sensor, and mode is tested. This review stage follows multiple quality checks that are performed throughout the assembly process. A final delivery inspection is conducted before the finished unit goes out of the door, normally to a trailer manufacturer or truck bodybuilder for installation. Next to the commissioning area is a small space for reworking or remanufacturing parts bought in from suppliers which need to be modified before installation on the main unit.
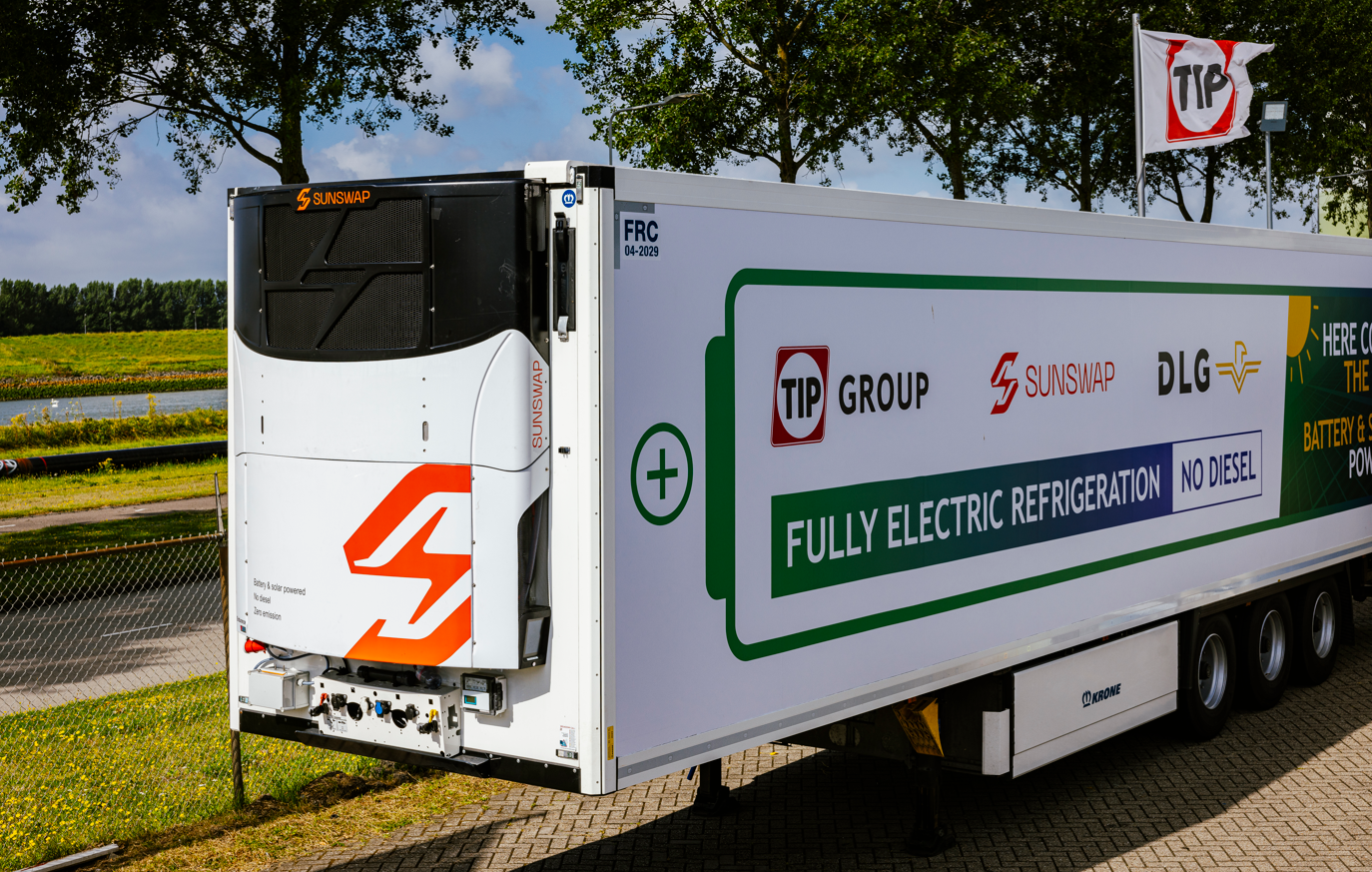
An Endurance unit on a TIP trailer
Some case studies and Sunswap’s future plans
According to Lowe, Sunswap has completed more than thirty customer trials, with several (including DFDS and TIP, mentioned above) placing orders for its Endurance unit. DFDS trialled the technology in 2022 and used it on delivery cycles which required a temperature setpoint of minus 22 degrees Celsius. During the longest duty cycle, involving two deliveries made over the course of two days, the Endurance unit provided twenty-two hours of frozen cooling time on a single charge, arriving at its delivery destination with around 30% of its charge left and recharging to full via onshore power in around eighty minutes. Of the total energy consumed during the trial, around 39% was derived from the solar panels on the roof of the trailer. Based on the trial data, DFDS projected it could reduce its tailpipe emissions by 895 tonnes over the lifetime of a single Endurance unit, reducing the total cost of ownership by 13%, or £10,696 per unit (£57 saved per tonne of CO2 reduced).
More recently, Sunswap conducted a two-week trial with Worcestershire distributor Bannister Transport, which put the Endurance unit on its most demanding duty cycle. Maintaining a setpoint of three degrees, the unit was in operation continuously over fourteen hours and twenty-three minutes, making six deliveries along the route. By the end of the cycle, the unit had used 70% of its energy capacity; 40% of the energy it used over the two-week trial was derived from solar. Bannister has since committed to replacing all of its refrigeration units with Sunswap’s Endurance, which it predicts will reduce its scope 3 emissions by 1,760 tonnes – equivalent to taking 419 cars off the road.1
The figures from Sunswap’s trials show that operators could reduce their fuel costs and carbon emissions by adopting its solar-powered units, but are they enough to make it competitive against established players in the transport refrigeration market? According to Lowe, although Sunswap cannot compete on scale against its major rivals, it can put up a good fight on the sustainability front. He argues that the Endurance provides an attractive alternative to fitting trailers with a regenerative e-axle plus battery system, which add weight and do not eliminate emissions entirely (provided the refrigeration unit they support is still powered by a diesel engine). He is confident that Sunswap’s technology has the potential to disrupt the sector – certainly in the UK, which is the company’s main focus for the time being.
At the last IAA in Hanover, I met with Sunswap who were exhibiting their technology on the continent for the first time. The Benelux region, and the Netherlands in particular, is a target for Sunswap’s commercial expansion, given its importance as a logistics hub and its closeness to the southeast of England. Moreover, Lowe told T&BB that he believes Dutch operators have a “positive, more advanced attitude to sustainability” than their British counterparts, and so he is confident that Sunswap’s technology will be taken up with enthusiasm. Beyond the Benelux, however, the company has no concrete plans which it is willing to share just yet.
1 More case studies can be found here on Sunswap’s website: https://sunswap.co.uk/case-studies/