Continental, maintaining dominance in a digital world
By Luke Willetts - 7th November 2023
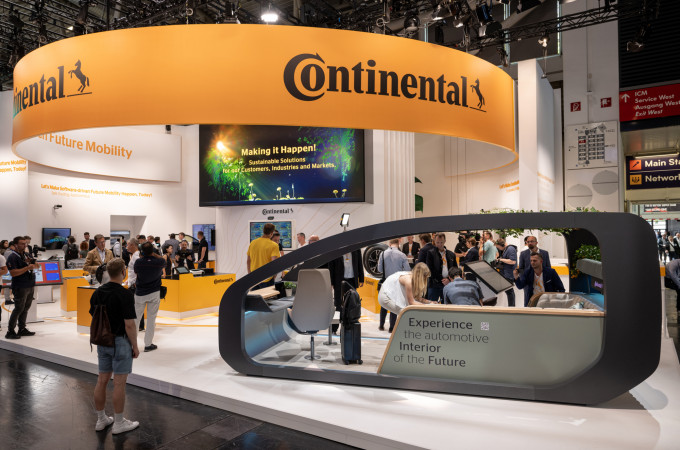
Continental stand at IAA 2023
Germany - Whilst Germany's biggest tyre manufacturer, Continental AG based in Hanover, celebrates the launch of its new Commercial Vehicle (CV) tyre range, we decided to have a closer look at the world’s 4th biggest tyre manufacturer as it looks to expand its global presence through fleet digitalisation, product range and aftermarket services in the context of the impending Euro VII regulation.
Continental’s Beginnings
Founded in 1871 as Germany's first rubber producer, the company morphed into an automotive tyre company, offering a complete range of premium tyres and services. Beyond the tyre group, the company has successfully branched out into other segments including infotainment products, automotive parts, brake systems and digital services. This is signified by the six divisions: Chassis and Safety, Powertrain, Interior, Tyres, ContiTech and ADAS (Advanced Driver Assistance Systems). Within the tyre division, Continental owns and operates multiple tyre subsidiaries including General Tire, Semperit, Barum and Uniroyal.
-in-Hanover.jpeg)
First-ever Continental factory (1874) in Hanover, Germany
With 22 international manufacturing plants in seventeen countries, 203,000 employees and a distribution market of over 160 countries, Continental’s 2022 revenue hit USD 42.4 billion. Currently the 4th largest tyre manufacturer (in terms of revenue), the company has global ambitions to be number one. The strategy to get there is to compete with other global tyre manufacturers in terms of innovative product design, quality, longevity and aftermarket services.
Developing new technologies and unique tyre compounds, altering production techniques and driving innovation remains at the core of the company’s business strategy. This is powered by its central research and development facility, the Hanover Development Centre which employs over 1000 researchers, designers, engineers and material scientists. This has strengthened its R&D performance and as a result, pushed innovation which has led to some long-term lucrative contracts with Commercial Vehicle OEMs.
A large part of what drives this R&D is the testing centre and proving ground in Hanover, known as the “Contidrom”. New products are tested on wet and dry road surface conditions before being independently tested offsite. Before new tyre models go to market, they cover a minimum of 25 million kilometres on roller drum test rigs and test tracks, strengthening the quality associated with this premium tyre brand.
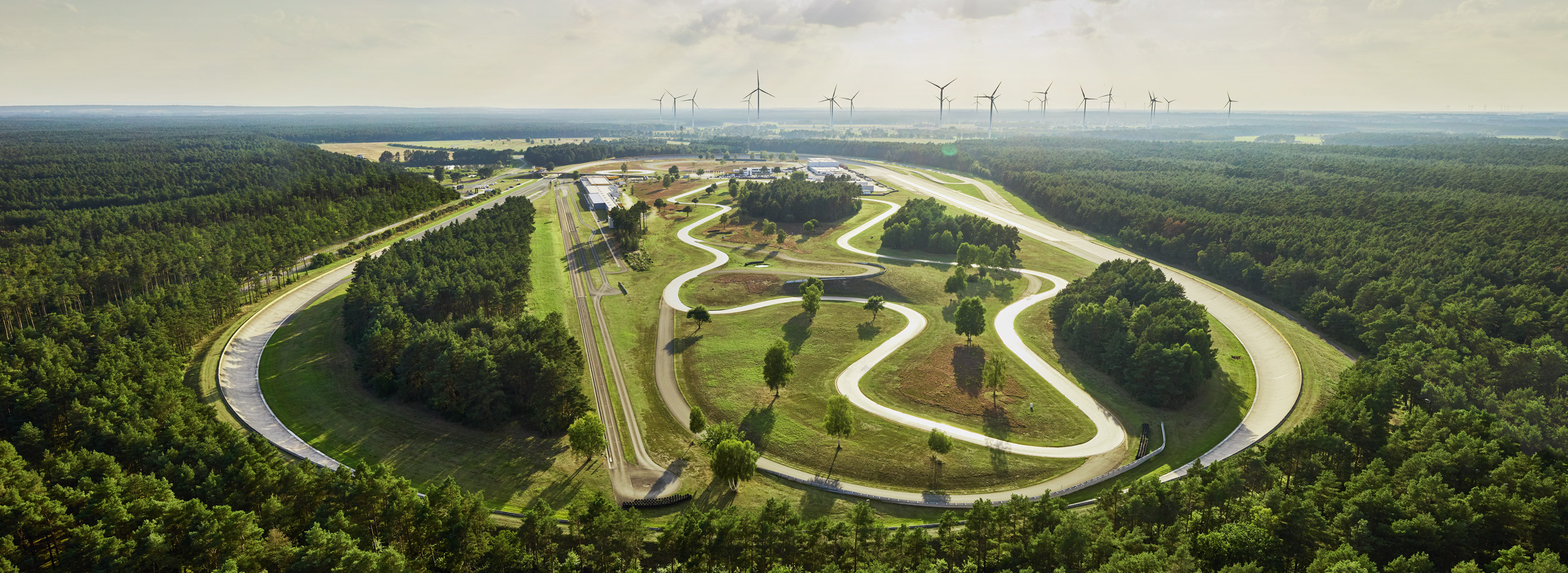
The Contidrom in Hanover, Germany
T&BB interviewed Steve Howat, General Manager of Technical Services at Continental to discuss the firm’s advancing product range, technical and digital expansion in the UK, sustainability and upcoming projects in the commercial vehicle sector. There was a lot to discuss considering the growing EV CV market within the EU.
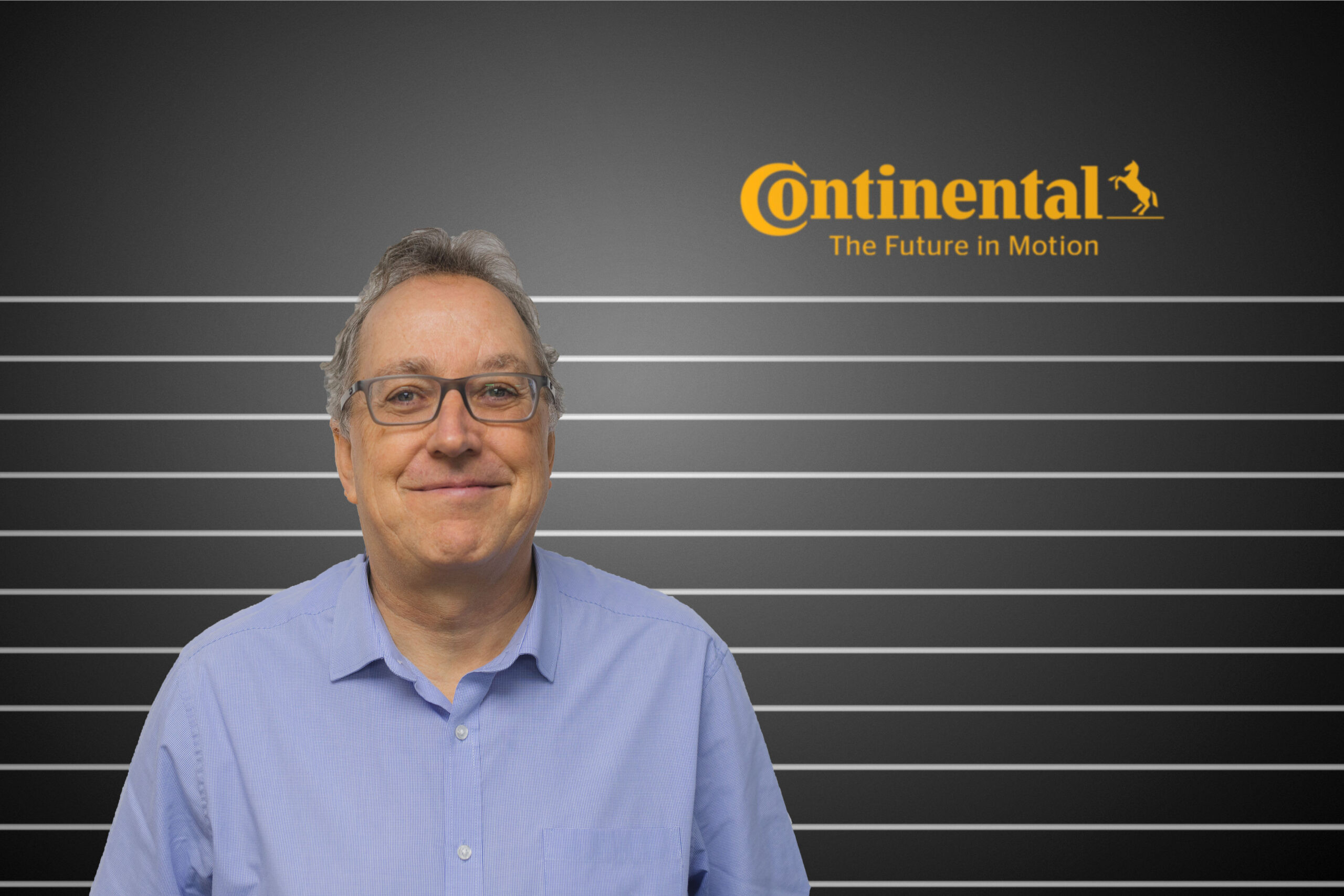
Steve Howat, General Manager of Technical Services at Continental
Production Facilities
Amongst the 22 factories (including the USA, Germany, South Africa, Brazil and China), most of the European CV tyre market is serviced by the Czech Republic (Otrokovice) and Slovakian (Puchov) facilities. Both of these facilities were upgraded in 2015 with the help of a EUR 200 million investment, boosting space and production capacity. Furthermore, Continental operates multiple technical and R&D centres globally, having recently spent EUR 115 million to extend and upgrade its Technical Centre at its campus in Bengaluru, India last year. These technical and R&D facilities are equipped with state-of-the-art technologies designed to develop tyres optimised for various road and climate conditions.
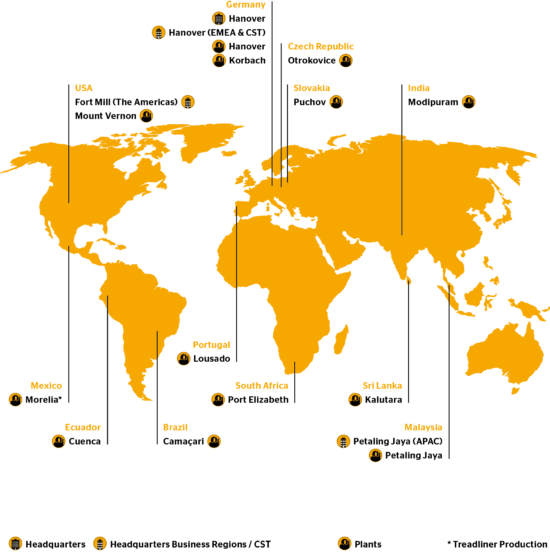
Continental tyre factories
Retreads: A Growing Market
Continental also operate two retread tyre brands under its ContiLifeCycle brand with key retread facilities in Stöcken, Germany and now in Ivybridge, UK. In 2016, the company purchased Bandvulc Tyres, a UK tyre retread company based in Ivybridge, Devon, which mainly focuses on hot-retreading for the UK market. This happens to be the biggest retread facility in the UK. Earlier this year Bandvulc installed several ABC (Automated Build Cell) robots to drive greater operational efficiencies at the plant. This is a part of the company’s three-year operational plan to introduce advanced and innovative tyre retreading technologies that drive quality and productivity. In March 2023, the facility was rebranded as a ContiLifeCycle production facility, but the Bandvulc branded hot-retread tyre range will continue to be offered under the same name.
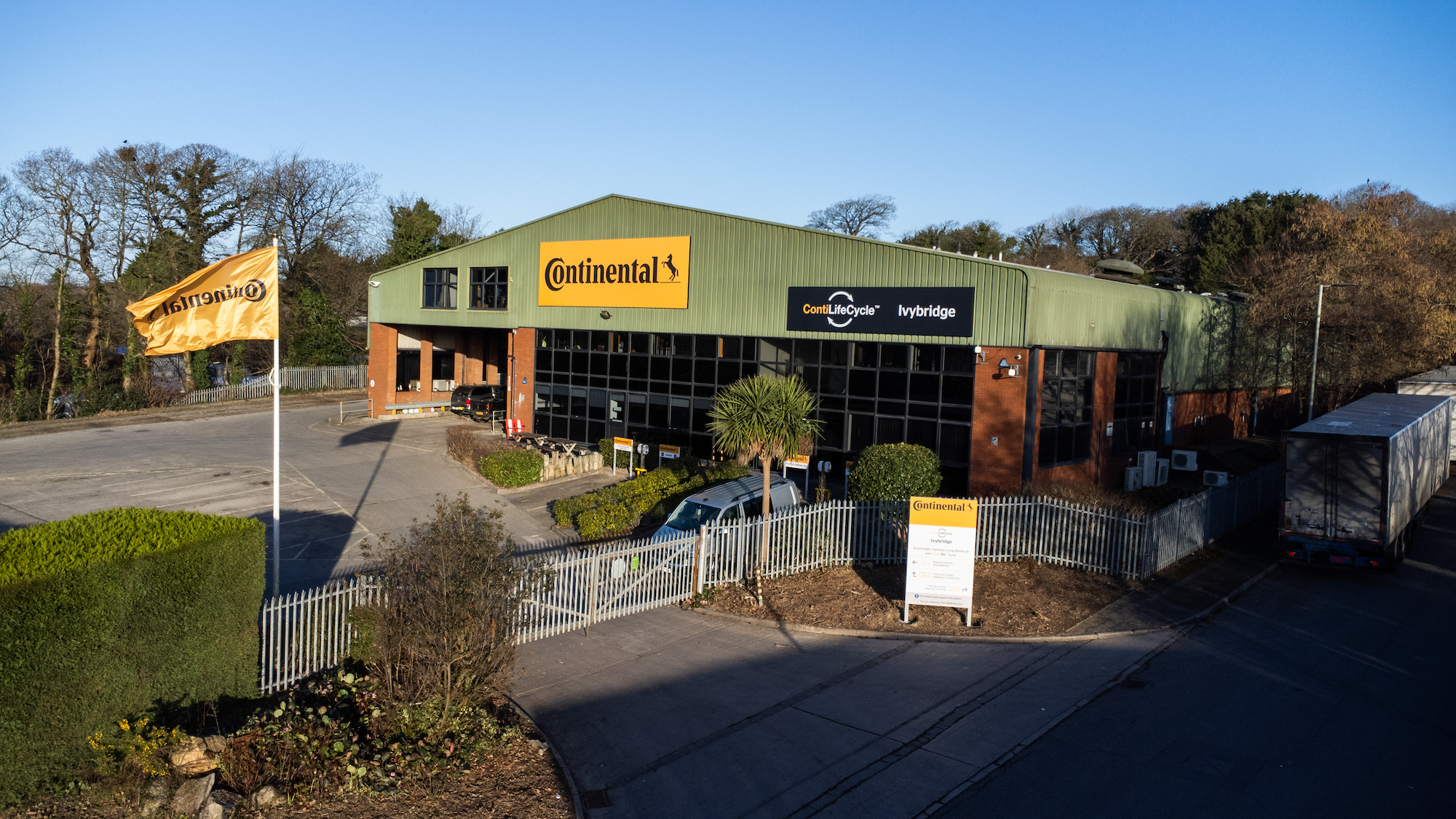
Bandvulc Ivybridge plant in Devon
All of these investments helped Continental launch new products for the CV sector at the 2023 Road Transport Expo (RTX), which took place from the 28th to the 30th of June at the NAEC Stoneleigh, in Warwickshire, UK. The company demonstrated the new Bandvulc BD5 retread drive tyre in the Fleetmaster range which has been engineered for mileage performance and longevity. The Bandvulc Wastemaster 5 tyre was also on display, demonstrating its sidewall protection features for urban waste collection vehicles. Finally, the Bandvulc Citymaster 5 tyre for the bus and coach sector was in attendance featuring a reinforced sidewall which adds an extra layer of rubber compound to the outer sidewall for enhanced protection against sidewall scrapes. Continental believes that the UK retread market and the larger European retread market will continue to grow. Continental’s objectives with its Bandvulc and ContiRe products are to offer lower costs for fleet operators, offering customers a similar performance at a cost of about 65% of the purchase price of a new Continental CV tyre.
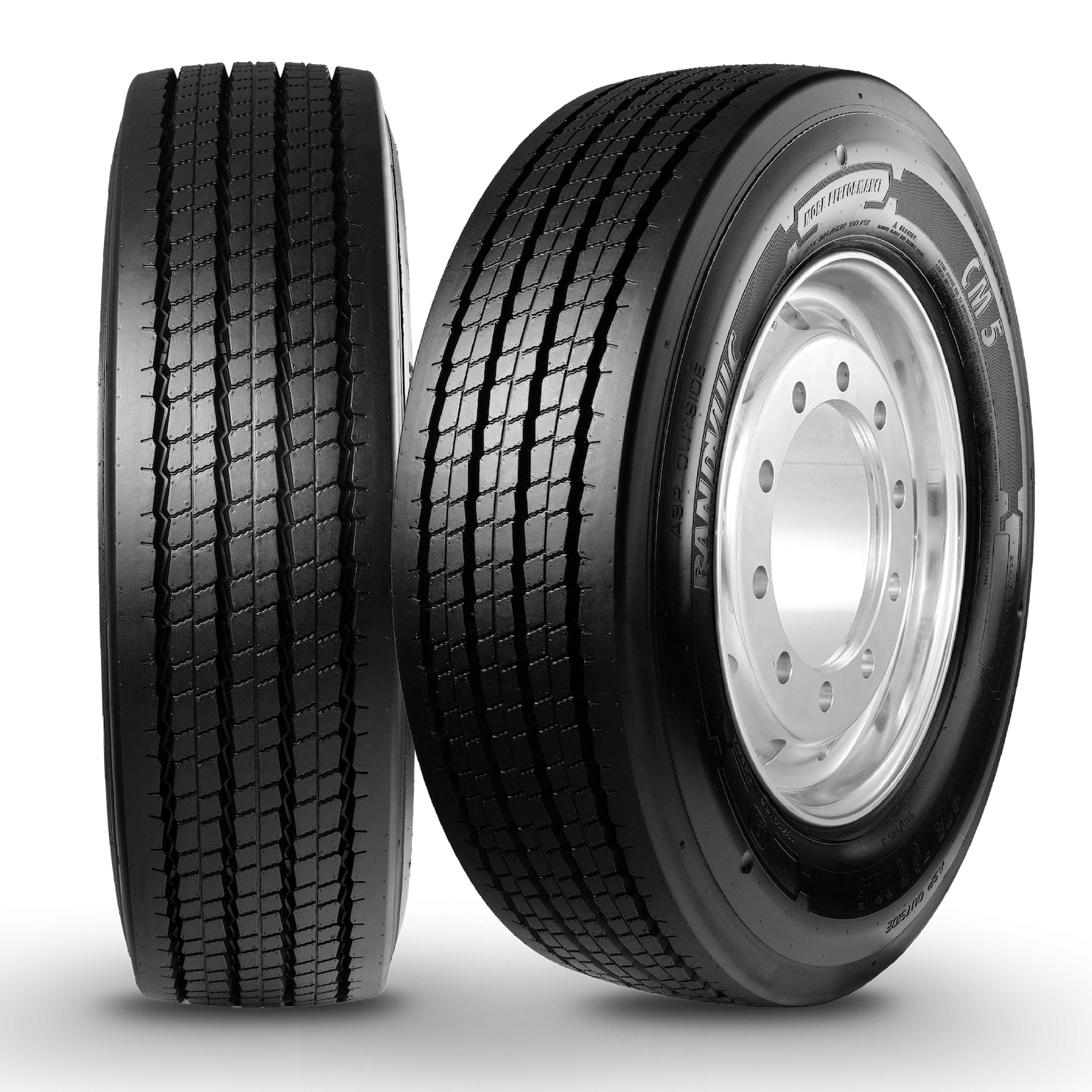
Bandvulc Citymaster 5
Expanding Product Range
Over the past few years, Continental has launched a premium bus and coach tyre range for intercity operation, the Conti CoachRegio. The new design claims to offer reliable and safe touring between cities and villages under variable speed conditions, with excellent handling and high mileage on hilly and winding regional roads. The CoachRegio range includes an all-axle fitment tyre ( HA3 295/80 R 22.5) as well as a dedicated (HD3) drive axle tyre. The HD3 drive axle tyre has a load capability of L1 154/149, which Continental says is the highest available in the coach and intercity segment. Both tyres carry EU Label C ratings for fuel efficiency and B for wet grip, with a rolling noise of 71 dB for the all-axle tyre and 73 dB for the drive axle tyre (both with one soundwave). The range meets the requirements for Three Peak Mountain Snowflake certification.
In the truck segment, 2022 saw the launch of its latest and fifth generation of Conti Hybrid truck tyres for regional transport. Continental claims that the new Conti Hybrid HS5 and HD5 offer increased mileage of up to 20 per cent compared with its previous generation. The new tyres incorporate innovative developments in tread design, rubber compounds and casing construction, which have been developed specifically to meet the gruelling demands of the booming online home delivery markets in Europe. To meet these regional transport demands, Continental highlighted the tread technology, which encompasses a two-layer construction (cap base) and innovative compounds which enable increased robustness and rolling resistance. Additionally, a newly enhanced tread structure of the Conti Hybrid HD5 protects the tread and casing very effectively against stone damage on the drive axle. Special stone ejectors prevent stones from becoming embedded in the tyre. The Conti Hybrid tyres are available in numerous sizes, starting with the following: Conti Hybrid HS5 315/70 R 22.5, Conti Hybrid HS5 385/55 R 22.5 and the Conti Hybrid HD5 315/70 R 22.5.
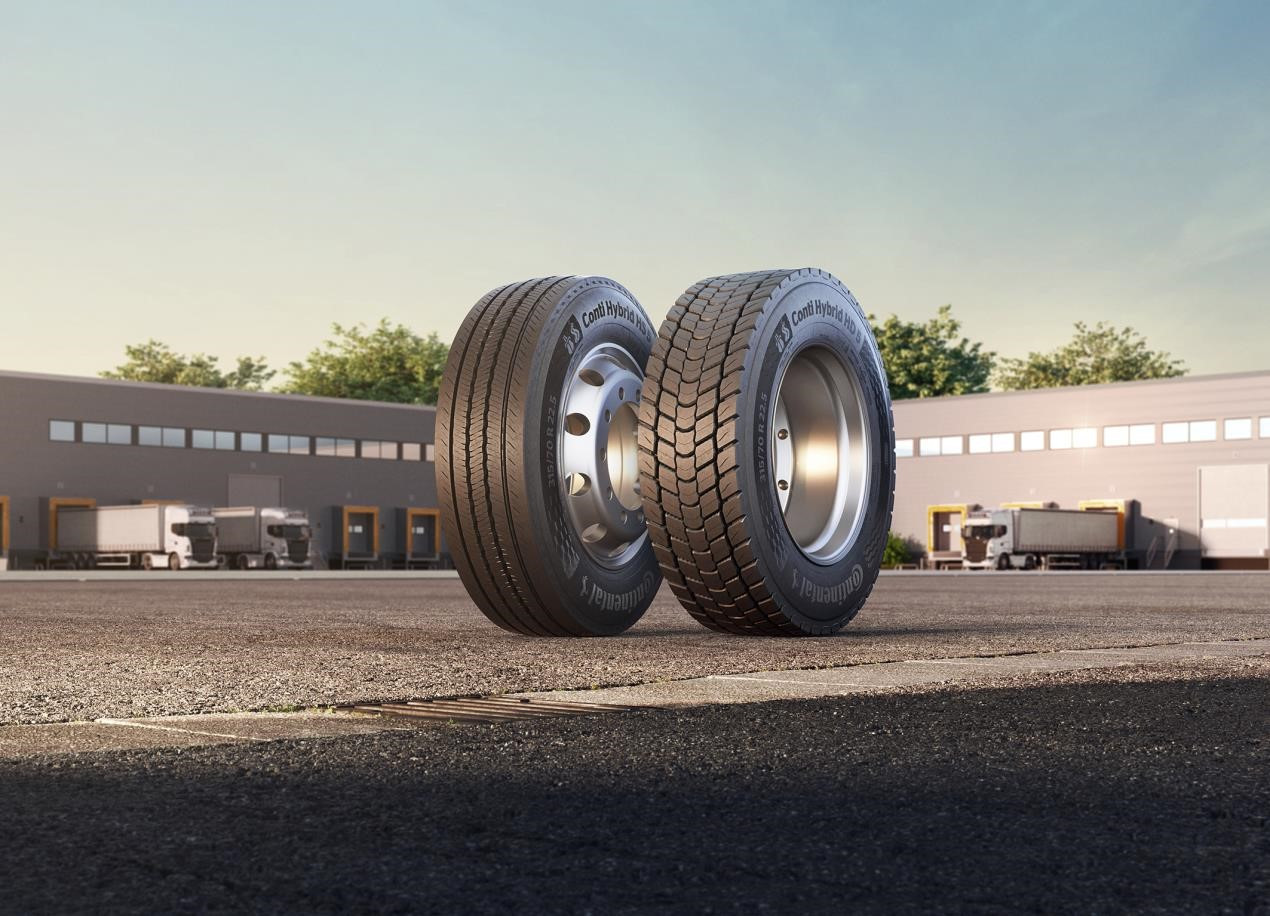
Continental Conti Hybrid HS5 steer and HD5 drive tyres
Continental produces a full range of sizes, helping customers extract the full value of the tyres. This is why these products are all originally made to be retreadable. This requires a much stronger casing and more tread rubber to allow for regrooving and multiple retreads. This is a central strategy to make it as easy as possible for customers to unlock 100% value of their tyres through a hot-cured retread offer.
Trailer Tyre Range
Last year the company added a new high-mileage trailer tyre aimed at reducing carbon dioxide emissions. The EcoPlus HT3+ offers a 10% higher mileage than previous generations due to a lower rolling resistance and improved retreadability. The HT3+ adds to the HS3+ and the HD3+ tyres that were recently added to the EcoPlus range. Continental states that the tread’s two-layer construction and the improved rubber compounds for both the tread and sidewall have made it possible to further reduce rolling resistance and increase mileage. This is mainly down to the refined production process featuring the firm’s Fuel Saving Edge technology and an optimised sipe pattern. The new groove geometry more effectively distributes pressure across the entire tread, resulting in uniform wear. In turn, this prevents the occurrence of one-sided wear or damage to the casing, preserving tyre retreadability.
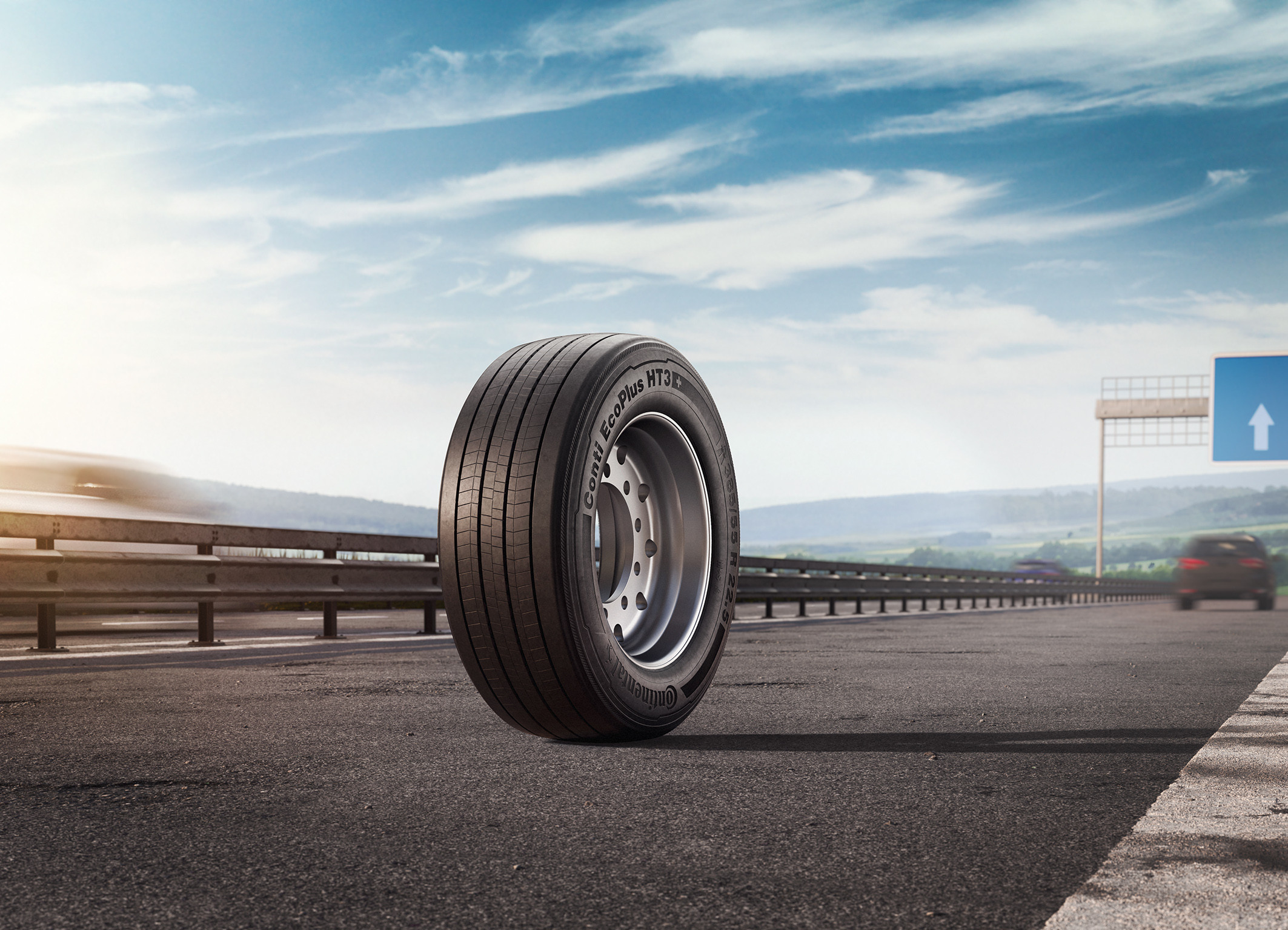
Continental's EcoPlus HT3+ trailer tyre
Continental has continued to add new trailer tyres to its Hybrid line for regional transport and recently announced that its EcoRegional Generation 3+ tyre is now offered with improved rolling resistance for mixed regional and long-distance applications. Continental states that all of the trailer tyres are designed for a wide range of road conditions and are built to offer impressive mileage with a focus on its wide tread and deep tread grooves.
Smart Tyres
A key update, from August 2023, has been that the new generation of e-bus Conti Urban Tyres has been equipped with smart sensors (Generation 2.0) embedded. This includes the entire new generation of the Conti Urban tyre range (The Conti Urban HA3, Conti UrbanScandinavia HA3+ and Conti UrbanScandinavia HD3) and has officially become the first smart tyres in the electric bus market to help drive fleet digitalisation and improve tyre and vehicle efficiency for operators by minimising downtime through predictive maintenance. The sensors count the amount of each tyre's revolution to identify how quickly it is wearing in relation to the distance travelled to provide a predicted pull point for replacement. These tyres will now be connected to the ContiConnect app, allowing operators and drivers to access real-time data including tyre pressure and temperature.

New Conti Urban tyre line
Speaking on the capabilities of the tyre sensors, Kalyan Yalamanchili, Head of Digital Solutions at Continental Tyres EMEA said:
The tyre sensors transmit live data on various parameters such as tyre pressure and tyre temperature via Bluetooth directly on the vehicle. Fleet management then accesses this data using a stationary Yard Reader station or telematics units. If any data anomalies are detected, immediate action can be taken. The intelligent Conti Urban tyres therefore help to reduce vehicle breakdowns and downtime, lower carbon emissions and cut costs. This creates the optimum conditions for carrying satisfied public transport users through cities aboard well-utilised buses in an environmentally sound manner and continuing to be a successful transport operator in future.
ContiConnect 2.0 driving Fleet Digitalisation
A major push into fleet digitalisation, AI and telematics software can be seen through the new and improved ContiConnect 2.0 software launched in April this year. This software goes beyond just monitoring tyre distance, condition, pressure and tread depth, as it now also features tyre history. This integrated platform allows every tyre to be tracked individually allowing operators to schedule tyre maintenance and manage tyre replacement more cost-effectively.
Commenting on ContiConnect 2.0, Dushyanth Rajagopal, Product Manager of Digital Solutions at Continental said:
ContiConnect 2.0 offers haulage companies the advantage of greater fleet efficiency through reduced costs and time savings, as maintenance and workshop appointments can be planned in advance. This paves the way for an even more efficient, straightforward, sustainable and forward-looking form of fleet management.
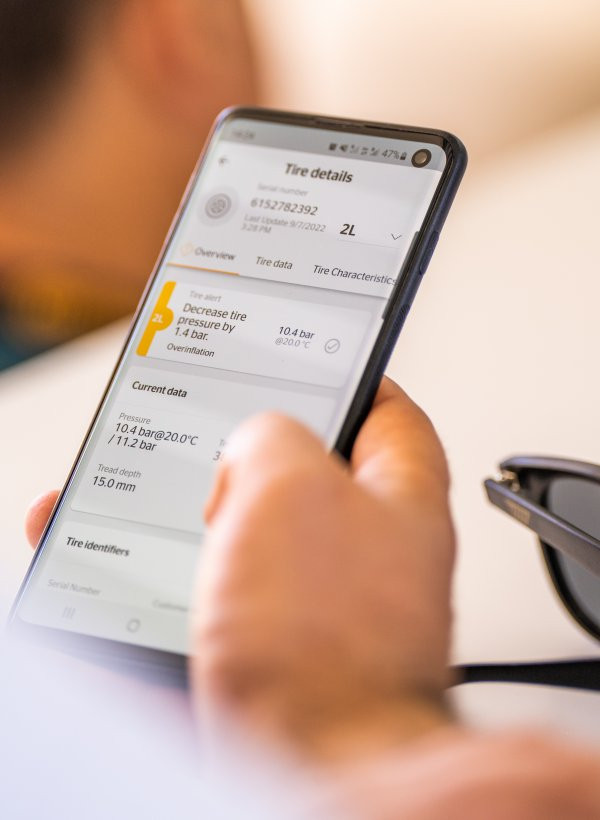
ContiConnect 2.0
Aftermarket Services
Howat spoke of the difficulties in the servicing side of the business, specifically related to the UK’s Conti360° network. Conti360° Solutions is Continental’s tyre management service for fleets, which aids in fleet monitoring, reporting and most importantly, swift response in the event of tyre breakdown. Whilst the company has massive fleet contracts in the UK, the problem has been servicing those contracts. Howat explained that they are facing a critical labour shortage of tyre technicians. That, according to Howat, is a challenge when managing fleet contracts. An apprenticeship programme was set up a couple of years ago to rectify this problem as Continental continues to work closely with its fleet partners.
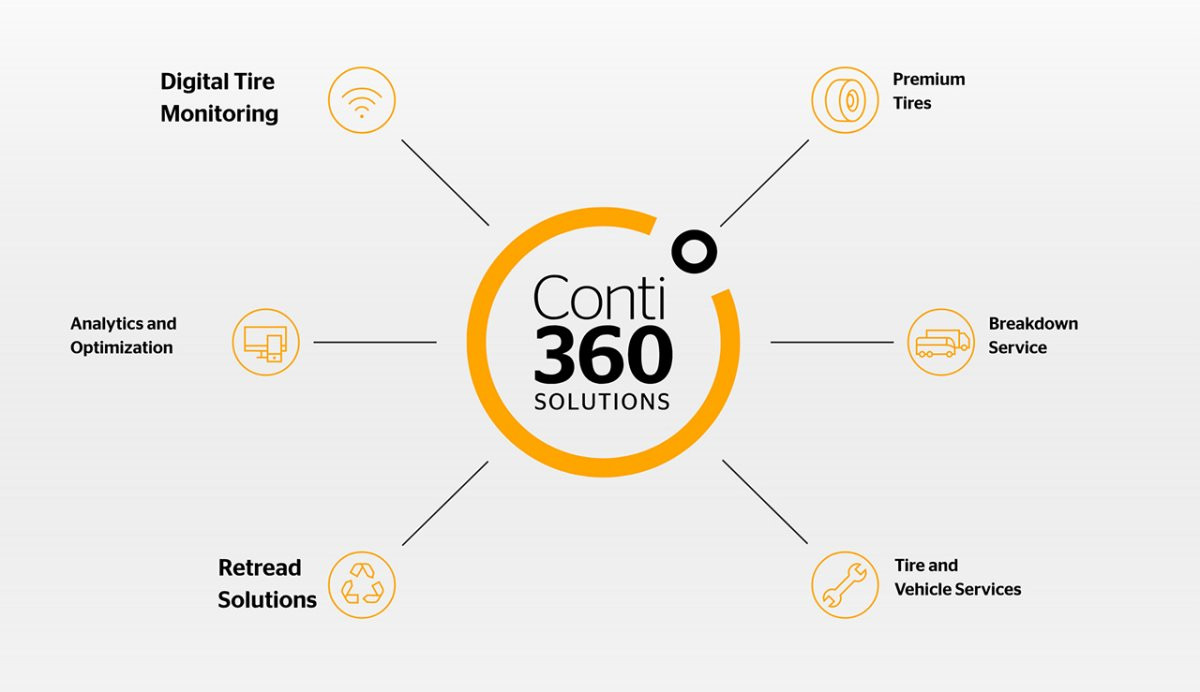
Conti360° Solutions
Euro VII
Sustainability has been on the lips of both regulators and manufacturers of late, with new measurements for emissions in Euro VII that take into consideration both the tyre abrasion and braking particles. This encompasses electric vehicles and means there will be constraints on the amount of wear particles that can be emitted from tyres. For Howat, it is an inconvenient truth that tyres will wear because they need friction, which is fundamental in providing tyre grip. Fleet operators and tyre manufacturers must therefore balance tyre performance (low rolling resistance and high mileage) with emissions targets. The challenge is to close that gap by rethinking tyre design and investing in R&D. Ultimately, the EU will give confirmation on the emissions constraints as well as the preferred testing method by the end of the year.
Sustainability
Howat spoke of Continental’s progress in sustainability and the various commitments to conservation, experimenting with synthetic latex rubber and pledging to protect the natural rubber supply chain through the digital traceability of natural rubber. The company also participates in ‘Project TREE’, a sustainable natural rubber project using a blockchain-based traceability system. A founding member of the Global Platform for Sustainable Natural Rubber (GPSNR), the organisation aims to bring more transparency to the entire tyre value chain. These organisations are a testament to the collaboration between multiple tyre manufacturers as they seek to decarbonise the industry writ-large.
In particular, Continental has declared to be carbon neutral across the entire group by 2040 which involves a holistic approach including producing renewable energy at its manufacturing plants as well as purchasing green energy when needed. Secondly, the implementation and use of energy-efficient technologies to reduce emissions in production processes is key, along with neutralising the remaining emissions. This falls on the shoulders of Jorge Almeida, who was recently appointed as the new Head of Sustainability. He is responsible for the global implementation of the company’s sustainability activities in its global tyre operations, with a focus on climate change mitigation, low-emission transportation, the circular economy and sustainable supply chains.
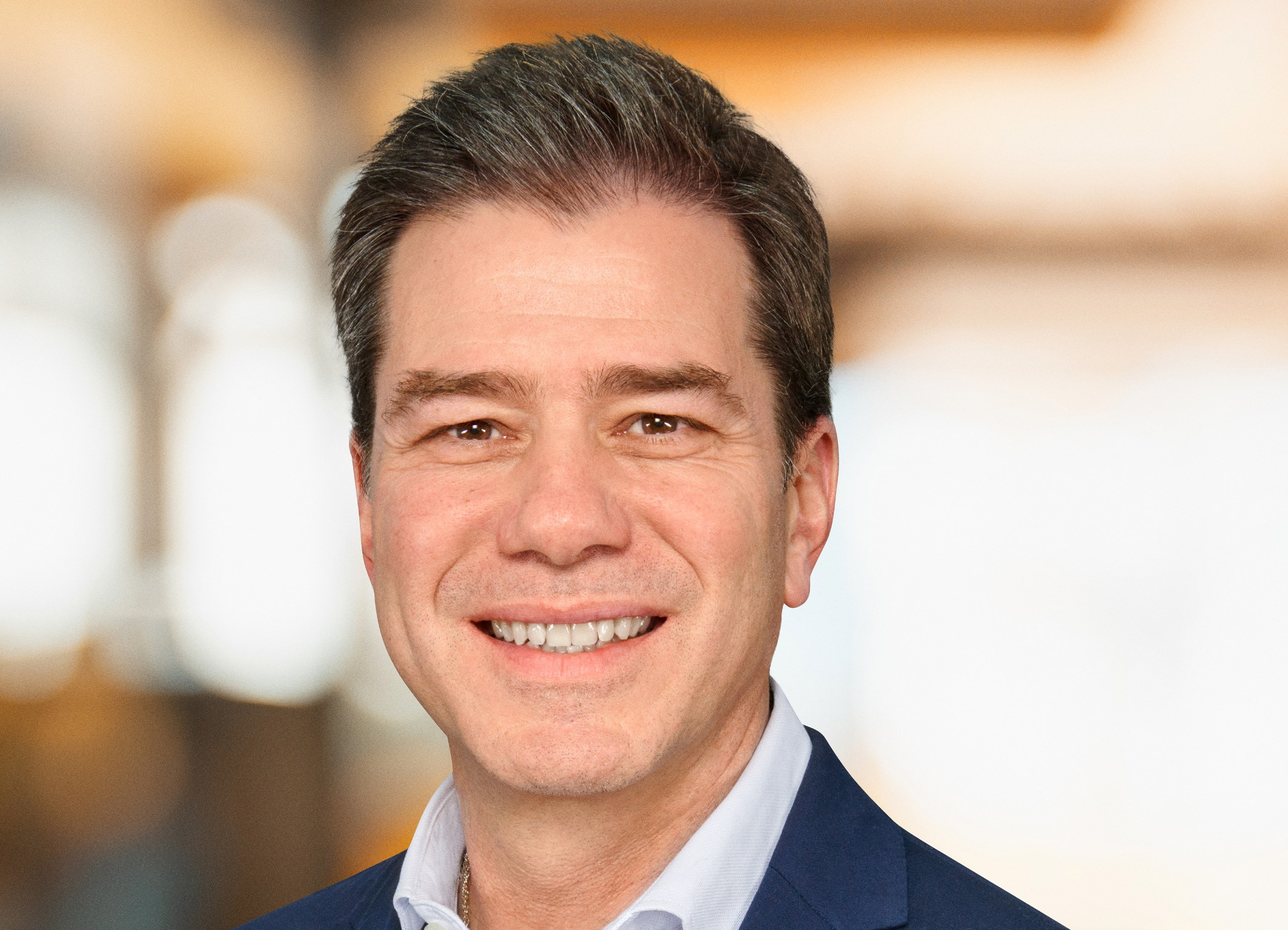
Jorge Almeida, Continental’s new Head of Sustainability
There is an arms race in the industry to look for renewable materials to replace traditional rubber. Therefore, a lot of R&D resources are going into materials science research. This is why a few years ago Continental invested EUR 35 million into a 30,000-square-metre dandelion rubber research facility in Anklam, Germany. This materials research laboratory is called 'Taraxagum Lab Anklam'. Taraxagum is the name given to a new alternative material to natural rubber, which can be extracted from a species of dandelion plant found in Russia. The goal is to develop commercial farming opportunities of the dandelion plant alongside methods and processes suitable for extraction. This dandelion was identified as an alternative raw material source to tropical rubber trees and its potential use in tyre manufacturing will ease demand for rubber, greatly improve sustainability and assist in protecting the environment. The material has already been used within the company’s Urban Taraxagum bicycle tyre.
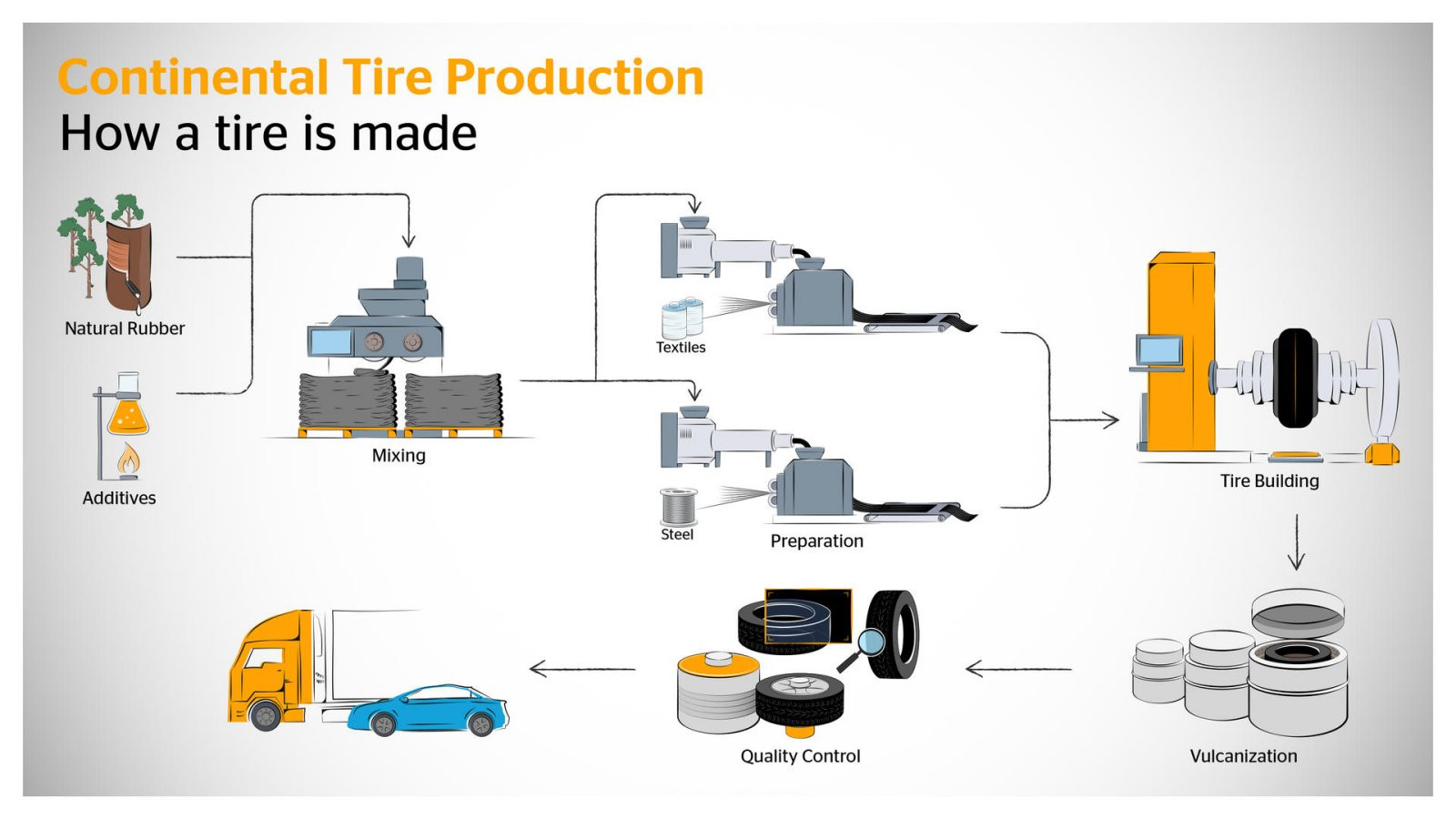
Continental’s tyre manufacturing process
3D-printing Technology
Continental is using AI and digital tools to optimise tyre design, new materials and production processes. 3D Printing Technology is being used in its tyre mould designs in order to help make a marked improvement in the performance of its products. 3D Printing Technology, which has been in use for five years, has been regarded as a breakthrough technology for the industry. The tread design incorporates features which are hidden from view when the tyre is new. These features add to the strengthening of the new tread block stiffness which in turn leads to increased fuel and mileage performance. Furthermore, as the tyre wears, hidden tread grooves are revealed to ensure continued wet grip, traction, and water evacuation. It is impossible to create these kinds of patterns without advanced tyre mould manufacturing technology. This allows Continental to continually make gains in terms of mileage performance, fuel efficiency and grip.