Hankook, the rise of an Eastern tyre manufacturing giant
By Luke Willetts - 19th September 2023
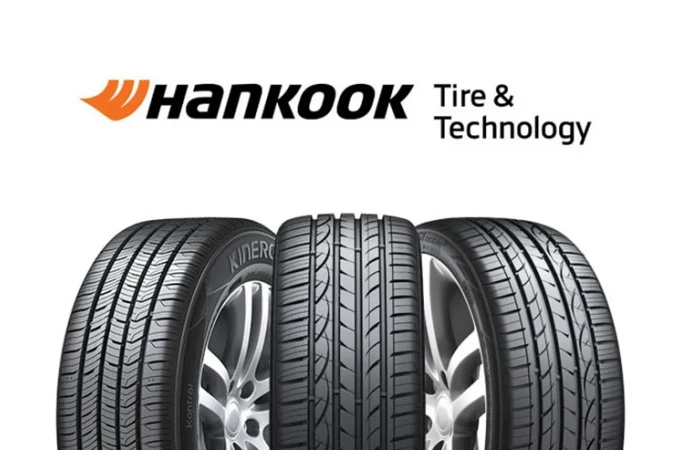
Hankook Tire & Technology
South Korea - Whilst South Korea’s biggest tyre manufacturer, Hankook Tire & Technology based in Seongnam-si, prepares for the launch of its new electric bus tyre range later this year, we decided to have a closer look at the rise of this tyre giant hailing from the East.
Hankook’s beginnings
Founded in 1941 as Korea’s first automotive tyre company, Hankook offers a complete range of tyres and services, with six international manufacturing plants, 20,000 employees and a distribution market of over 160 countries. Hankook is currently the 7th largest tyre manufacturer in the world in terms of revenue and is emerging as a global top-tier company through product quality and premium brand value. The strategy to get there is to compete with other global tyre manufacturers in product quality, longevity and therefore value/return on investment.
Developing original technologies, altering production techniques and driving innovation remains at the core of the business. This is driven by its central research and development facility, the Hankook Technodome at its primary tyre manufacturing plant in Daejeon, South Korea. This has strengthened its R&D performance and as a result, pushed innovation which has led to some long-term lucrative contracts with OEMs.
T&BB interviewed Guy Heywood, Vice President of TBR Sales, Marketing and Strategy at Hankook Tire Europe to discuss the firm's strategy, production expansion, new EV CV tyre range, sustainability and upcoming projects in the commercial vehicle sector. There was a lot to discuss considering the growing EV CV market within the EU.

Guy Heywood, Vice President of TBR Sales, Marketing and Strategy at Hankook Tire Europe
Production Facilities
Currently, Hankook operates 5 technical and R&D centres globally, including in the USA, Germany, South Korea, China and Japan equipped with state-of-the-art facilities designed to develop tyres optimised for various road and climate conditions. In 2017 the company opened the Technotrac in Ivalo, Finland, to test winter tyres and in 2022 they opened test centres in Idiada, Spain as well as Asia’s largest proving ground, Hankook Technoring in Taean South Korea. With 8 manufacturing plants across the USA, South Korea, China, Indonesia and Hungary, the factories in Jiangsu, Chongqing, Daejeon and Geumsan are responsible for producing the majority of the commercial vehicle tyres for the European markets. The new Hankook plant in Clarksville, Tennessee, has been steadily continuing to ramp up production of light commercial vehicle tyres, destined for the American market. The facility employs over 1000 staff and currently has an output of more than 10 million tyres per annum.
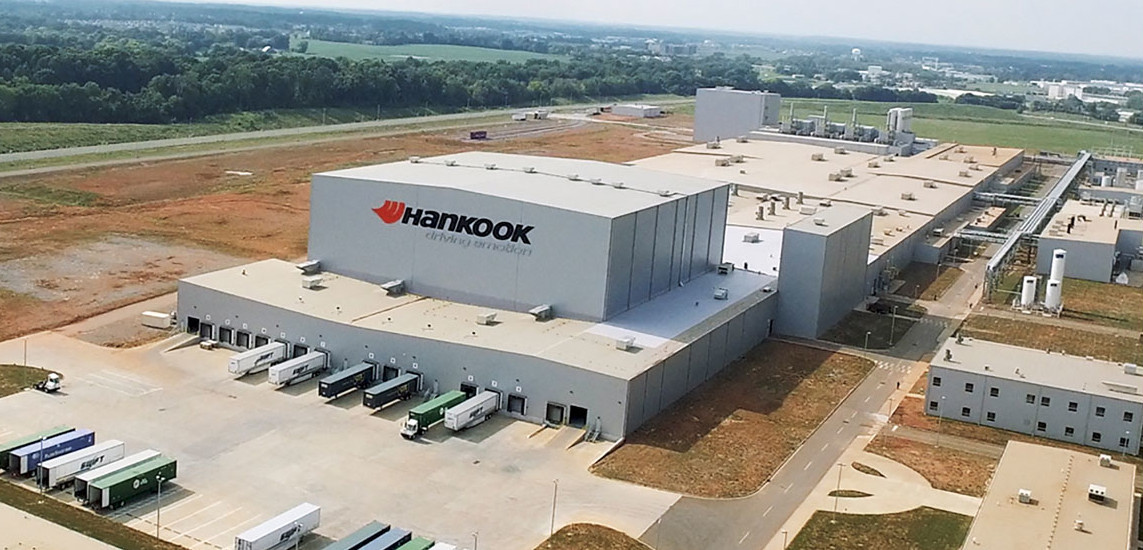
Hankook tyre facility in Clarksville, Tennessee
Whilst there are no Truck or Bus tyres being produced in Europe, there are 5 sites dedicated to the retread brand (Alphatread) in Italy, Spain, Germany, France and the UK. They produce a range of 13 sizes, helping customers extract the full value of the tyres, which is why they are made to be re-treadable and re-mouldable. This requires a much stronger casing and more tread rubber to allow for regrooving and multiple retreads. This is a central strategy to make it as easy as possible for customers to unlock 100% value of their tyres through a hot-cured retread offer.
According to Heywood, in order to meet the company’s global ambitions, a sizeable investment in increasing global production volumes has meant that the company is “currently trending at a 400% increase in sales in 2023 due to increased capacity.” At the same time, they are expanding their product range.
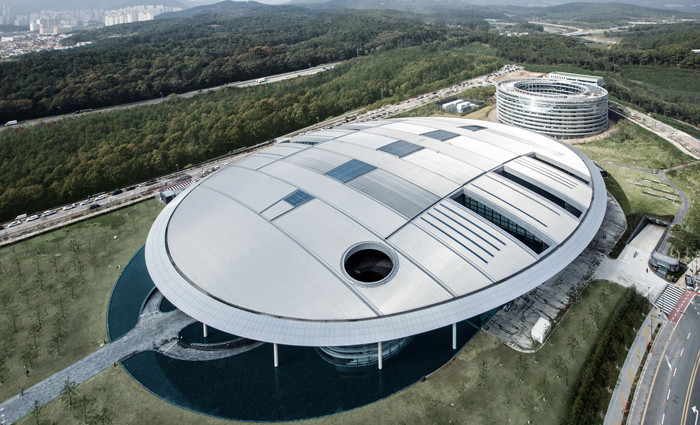
Hankook Technodome in Daejeon, South Korea
Expanding Product Range
This year Hankook launched its new range of hybrid tyres specifically designed for both regional and long-distance transport. At this past RTX expo, the Hankook SmartFlex AL51 for the steering axle, an all-position tyre, and the SmartFlex DL51 for the drive axle were both on display. Because the SmartFlex AL51 and SmartFlex DL51 tyres utilise 3D printing technology, the accurate tread pattern delivers good traction and water drainage under a wide variety of road and weather conditions. Because of this durability, the tyre carries the labels M+S and 3PMSF (snowflake pictogram), highlighting its ability to cope with cold conditions. The Stone Ejection technology in the tread grooves also prevents sharp objects from lodging into tyre grooves, which in turn reduces the likelihood of punctures and maximises the tyre’s life. The tyre also has low rolling resistance allowing it to be very fuel efficient. It is available in size 315/70 R22.5.
The company reported positive orders for these new tyres. The main Research & Development Centre assisted with both development and testing activities focusing on wear performance, low rolling resistance, durability and handling stability.
The company also unveiled the LF95 trailer tyre for regional haul applications from Laufenn, Hankook's second-line brand. The new all-season trailer tyre is designed for a wide range of road conditions and offers impressive mileage with a focus on its wide tread and deep tread grooves.
Heywood said:
The LF95 is addressing the needs of small and medium-sized companies, offering them a tyre with an excellent price-performance ratio which is designed for high fuel efficiency and durability. Our customers benefit from the brand’s many years of experience and get a product which meets the highest quality standards.
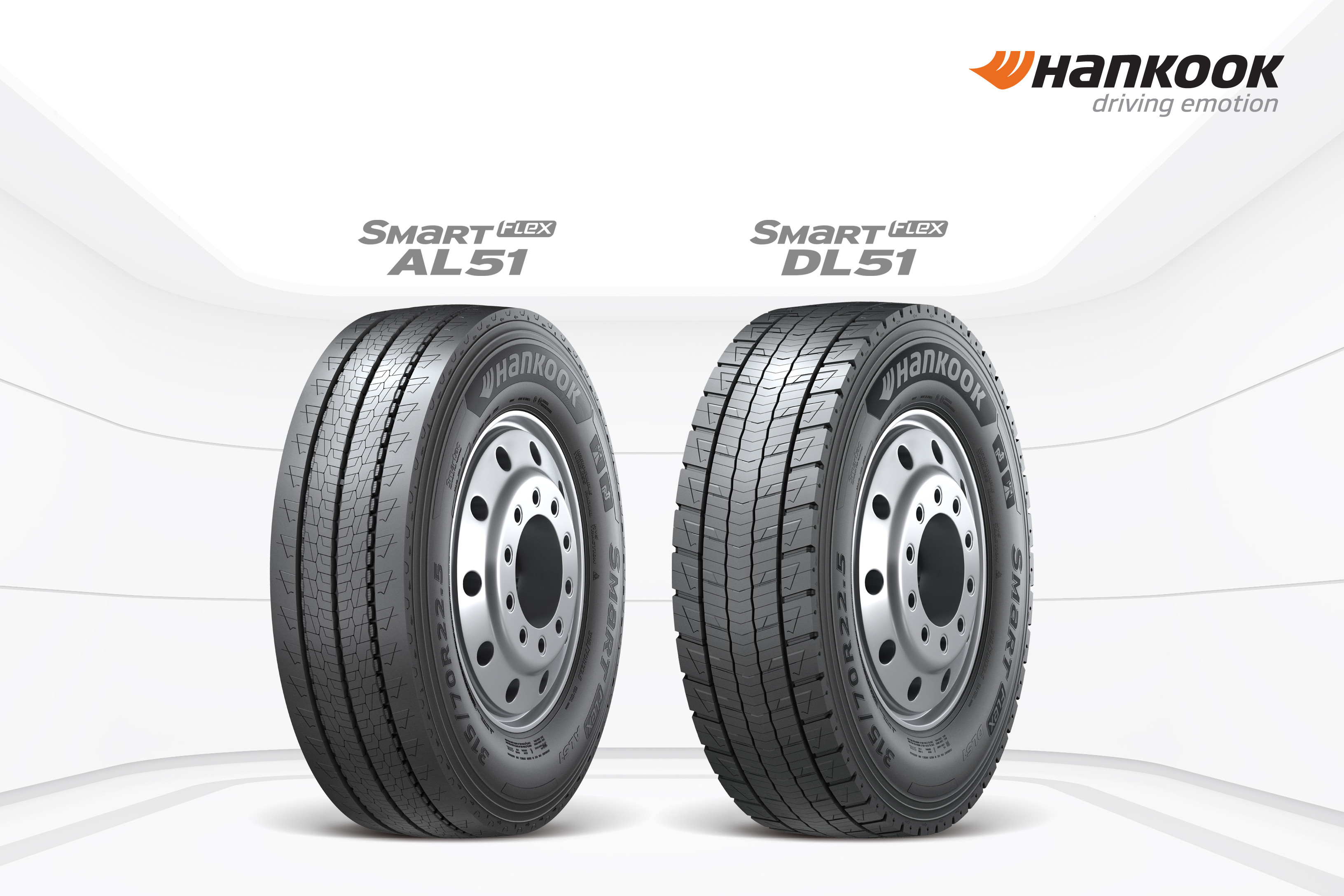
Hankook’s SmartFlex AL51 and the SmartFlex DL51
Electric bus tyre range
Hankook plans to launch a new range of EV tyres (275/70R22.5) for urban buses later this year at the Solutrans event from the 21st to the 25th of November 2023 in Lyon, France. Heywood sees a growing demand for electric buses in Europe because of the fixed routes and stable charging infrastructure. Increased vehicle weight means that the tyres require a different compound, and slightly different manufacturing construction to carry more weight (extra load capacity in the casing). The tyres aim to provide a high load capacity to accommodate heavy batteries, greater tread abrasion resistance to address the high torque of electric engines and deliver low energy consumption to maximise battery range.
Again, product development took place at the Technodome, with robust construction and compound technology developed into a four-groove pattern design for extreme stiffness, whilst wide shoulder ribs enhance cornering stability. Further developments include rubber-reinforced sidewalls to protect the tyre from curbing damage and abrasions. A wide and robust tread pattern and advanced siping further reduce noise and improves passenger comfort.
Growth Strategies
The philosophy for growth, according to Heywood, is to compete with other global tyre brands on both quality and price. This requires constant improvement by investing in R&D centres as well as continually increasing the automation of the manufacturing process.
The company is also looking to become partners with fleets. This requires moving away from a traditional business model that focuses on the number of tyres being bought and sold, to looking to identify opportunities in fleet operators' businesses to see how they can save money and improve operational efficiency. This can be regrooving, retreading, pressure management and using the correct size tyres on the right axles. This can bring down the costs of new tyre purchases whilst the correct pressure management can significantly decrease fuel consumption. The aim is to become partners with the fleet operators rather than just selling tyres as a commodity and the retread business (Hankook SmartLife) is a big part of that strategy.
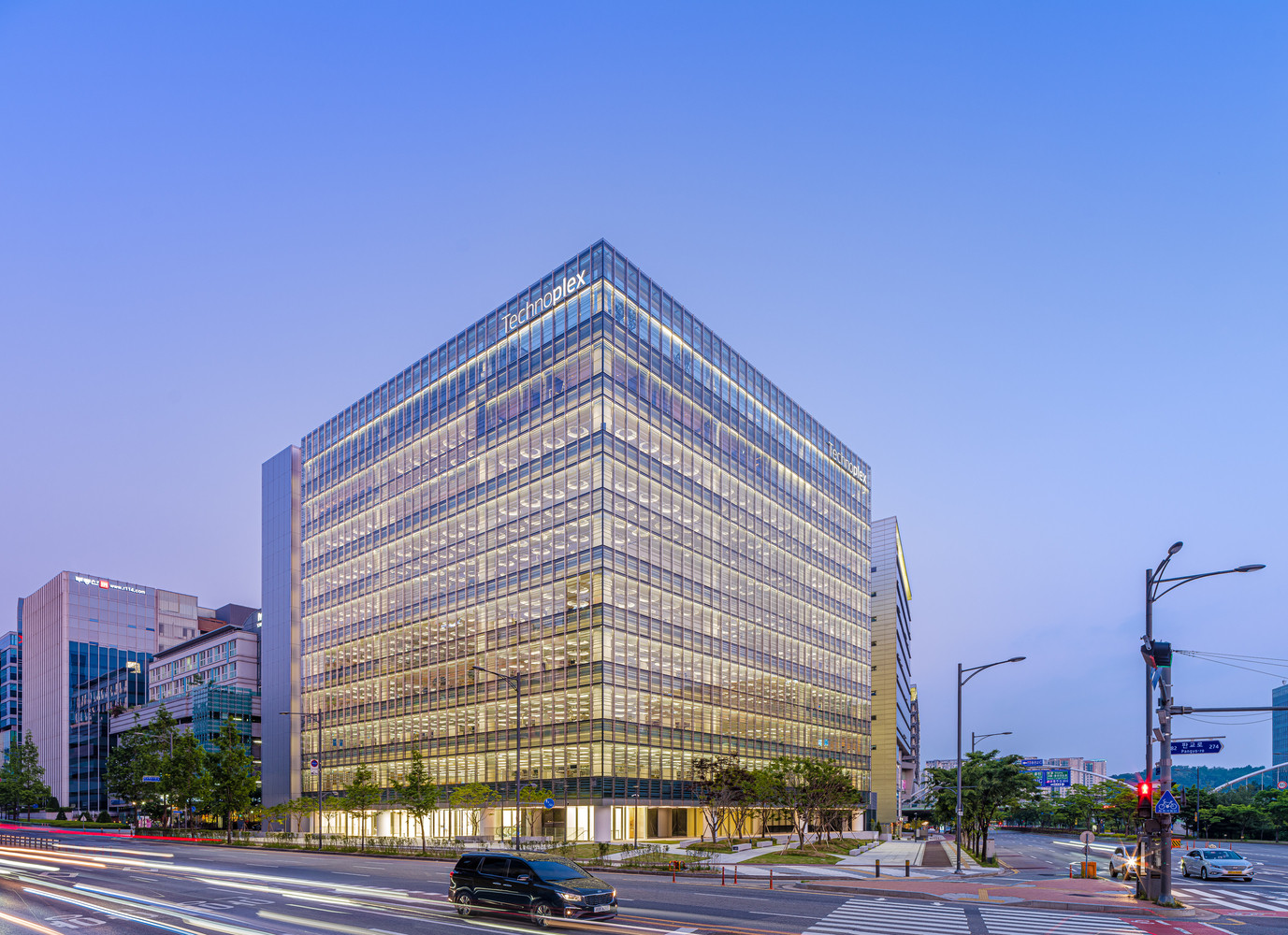
Hankook Technoplex in South Korea
Aftermarket
Heywood spoke of the added emphasis the company has placed on their aftermarket business over the past few years. The Hankook SmartLife retread solution aims to demonstrate the quality and sustainability of Hankook’s TBR casings, by offering “up to 250% tyre life from 1 new tyre.”
Today the SmartLife programme serves as an added-value service for optimal fleet cost reduction and sustainability. In 2022, Hankook also partnered with English company Vaculug, announcing that they would be producing Hankook’s Alphatread line for the UK market in Daventry. All of these tyres are hot-cure bead-to-bead retreads manufactured using certified Hankook casings. The manufacturer’s objectives with this range is to offer lower costs for fleet operators and reduce the environmental impact of its tyre programme. According to Heywood, these retreads save 70% material, 29% land use, 19% water, and 70% CO2 when compared to producing a new tyre. The key for customers is that they get almost the same performance from an Alphatread as they would from a new Hankook tyre at a cost of about 70% of the purchase price.
AI, Machine Learning and Big Data
Continuing in the aftermarket segment, the company has invested heavily in leveraging AI, big data and cloud-based services to improve efficiency and customer experience. The company has contracted Amazon Web Services Inc and Snowflake Inc to build an integrated AI data platform to improve the performance and quality of its tyre business. With the development of this cloud-based data ecosystem, the company hopes to make more informed decisions based on more reliable data sets aiding product development and increasing manufacturing efficiency, thus enhancing global competitiveness. The project will leverage artificial intelligence and machine learning technologies to integrate and analyse data from Hankook as well as its various subsidiaries. This has come in the form of a Virtual Compound Design (VCD) system, which predicts the characteristics of tyre compounds and finds an optimal combination through artificial intelligence analysis. This is built on digital technologies such as artificial intelligence and big data. The AWS cloud platform will enable Hankook to store, process and analyse huge swaths of data such as that gathered from the VCD system.
Hankook’s Chief Digital Officer (CDO) and Chief Information Officer (CIO), Seongjin Kim, said:
With the development of generative AI, AI is passing through an inflection point, there is a need for a platform that can collect and freely use internal and external data to apply it to businesses. By utilising the excellent technology and solutions of Amazon Web Services and Snowflake, we will maximise our AI capabilities and accelerate our journey to enhance product competitiveness in areas such as electric vehicles and smart tyres.

Seongjin Kim, Hankook’s Chief Digital Officer (CDO) and Chief Information Officer (CIO)
3D-printing Technology
Hankook is using AI and digital tools to optimise tyre design, new materials and production processes and 3D printing to help make a marked improvement in the performance of its products. The metal additive manufacturing technology known as 3D Printing Technology, has been developed at the Technodome. Over the past decade, Hankook has played a leading role in the R&D of this technology, as manufacturing metallic components using metal 3D printing is regarded as a breakthrough technology for the industry. Hankook designed the components, developed materials and processes suitable for the application and developed standards for product quality. Their mould-making company, Hankook Precision Works (HPW), then proceeded with the mass production of the moulds with regenerative 3D sipes, grooves and features.
The 3D tread design incorporates features that are hidden from view when the tyre is new. These features add to the strengthening of the new tread block stiffness which in turn leads to increased fuel and mileage performance. Furthermore, as the tyre wears, hidden tread grooves are revealed to ensure continued wet grip, traction, and water evacuation. The tyre maintains grip and traction performance even when it is 70% or more worn.

SmartFlex AL51 tread pattern
It is impossible to create these kinds of patterns without advanced tyre mould manufacturing technology. Hankook began to research additive manufacturing technology (3D Printing) and how to integrate this into the tyre mould industry as far back as 2013, and now has the capability to manufacture the tyre mould for these patterns by applying the '3D printed sipe’ and achieving long-lasting performance without any trade-off effects. This experience encouraged Hankook to develop the '3D sipe integrated tyre mould' and invest in 3D metal additive manufacturing as they foresaw the potential this innovation has to significantly improve tyre tread designs. Today all of the new generation of TBR premium tyres in Europe are using the mould adopting 3D metal.
Heywood states that the latest generation of Hankook TBR products is showing 20% or more improvement in mileage performance, fuel efficiency and wet grip versus the previous generation of products. In addition to this, 3D printed tread patterns mean tread features are revealed as the tread wears ensuring the grip and traction performance is maintained even as the tyre wears, so this benchmark performance is available from the first to last millimetre of tread wear.
Sustainability
Heywood spoke of Hankook’s progress in sustainability and the various commitments to conservation, experimenting with natural rubber and joining the organisation, the Global Platform for Sustainable Natural Rubber (GPSNR) which pledges to protect the natural rubber supply chain. Hankook also endorses the United Nations Sustainable Development Goals (SDGs) and is a member of the UNGC (United Nations Global Compact). The company works alongside the Conservation International organisation and participates in ‘Project TREE’, a sustainable natural rubber project using a blockchain-based traceability system.
In particular, the company has declared net-zero target by 2050 through its Carbon Neutrality Roadmap. This includes materials used in production. Hankook Tire’s approval by the SBTi for these targets is a significant move and is the first time in the Korean mobility industry that a company has set itself the challenge of reaching net zero by 2050 based on the SBTi Net Zero standard. They are currently sitting at around 30% sustainability this year. Heywood admitted that there is an arms race in the industry to look for renewable materials to replace traditional rubber. Therefore, a lot of R&D resources are going into material sciences.
Sustainability has been on the lips of both regulators and manufacturers of late, with new measurements for emissions in Euro VII that take into consideration both the tyre abrasion and braking particles being accounted for in the proposed emissions policy. Heywood mentioned that many of the companies in the tyre industry have been working together on a new standard to measure these various particles. This has translated into having better carbon accounting practices throughout the business, including in the manufacturing processes, in order to track and then subsequently reduce Hankook's carbon footprint. As a result, the company has been listed in the Dow Jones Sustainability Index (DJSI) World for seven years, proving its position as a global top-tier sustainable management company.